The South West of France is well known for its culinary delicacies and fine wines. But it’s also home to a company with an interesting ethos and a very French reverence for their raw ingredients. CPM visits the home and factories of De Sangosse.
The bait is every bit as important as the active ingredient it contains.
By Lucy de la Pasture
A few miles outside Agen in South West France lies the small town, Pont du Casse. It’s the home of a French company where the employees own 78% of its shares, with 14% held by the founding De Sangosse family and just 8% in the hands of investors.
Nicolas Fillon, De Sangosse directeur géneral and CEO, believes there are some unique advantages to an employee-owned company. “With no shareholder dividends to pay, all the profit goes back into the company enabling innovation and a strong entrepreneurial spirit. It gives the staff, who are our key asset, a commitment towards the aims of the company.”
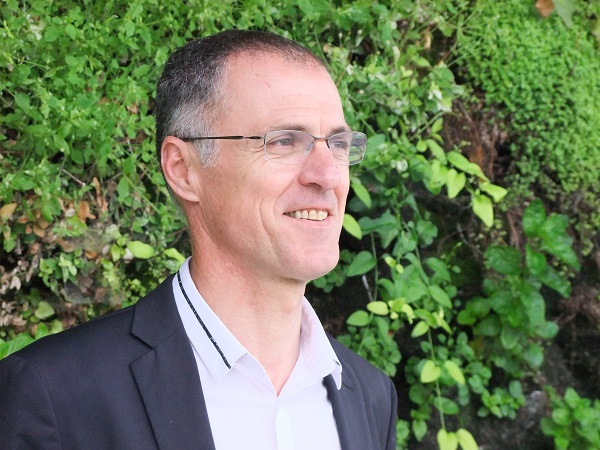
Nicolas Fillon explains because the staff are the major share-holders, all the profit goes back into the company enabling innovation.
He believes the business model of De Sangosse makes them ideally suited to niche markets with speciality products, where they have an international presence.
“De Sangosse have launched 31 speciality products in the past three years, have a further 44 in development and have 1200 registrations in 50 countries,” he says.
One of the markets Nicolas sees as having a huge growth potential is in biostimulants, an area which De Sangosse have been involved in since 2008. The emphasis on biocontrols in French agricultural policy is also driving the growth trend in Europe.
“Even though some biocontrols only have 35-40% efficacy, they can form a useful part of the solution, allowing a decrease in the use of conventional chemistry,” he says.
The focus on producing food in a more sustainable way is being driven by societal, regulatory and stewardship pressures, says François Benne, global marketing and project manager for baits. In France, where government policies in agriculture are increasingly green, ferric phosphate is registered as a biocontrol product rather than a pesticide, he comments.
“Baits are the only pesticide used in agriculture that involves being first found by the pest and then ingested in sufficient quantities to cause its death. To achieve this the bait is every bit as important as the active ingredient it contains,” he says.
De Sangosse have two laboratories dedicated to R&D in bait technology, looking at more effective product formulations, screening for new active ingredients and specific quality control. The company’s trials capability extends beyond the lab with cage trials and field trials used to evaluate new developments.
In true French tradition, the company pays the same respect to the ingredients that go in to their bait products as the they do to the champagne and foie gras the region is famous for. It’s all about quality and creating a product to be proud of.
Close by the living walls which envelop the modern building which is De Sangosse HQ lies Borie Industries, the manufacturing heart of the company’s bait business. Stepping inside one of the factories, its gleaming stainless steel, spotless surrounding and the slightly sweet smell of durum wheat flour mixing with warm water gives the distinct impression of a food factory, that is until closer inspection reveals the pasta dough is bright blue in colour.
On the day of our visit, the factory was in full-flow, producing slug pellets containing metaldehyde. Manufacturing director Arnaud Hot explains the factory runs 24 hours a day, seven days a week, and has a production capacity of 100t/day.
“There are 10-12 different raw materials that go in to making a metaldehyde slug pellet and quality of ingredients is really important,” he says.
Durum wheat is grown on contract and must meet the De Sangosse spec, with every load tested on intake. “It’s very important that we are able to produce a uniform pellet which is why we’re so fussy about the spec of the flour,” explains Arnaud.
Once the ingredients are mixed into a uniform dough, it’s passed through an extruder to produce a pellet. The pellet is still plastic when formed and has to be gradually dried by passing through a series of six driers.
“Drying must be a slow process because if the moisture content is reduced too quickly, the pellet could crack and would be less consistent,” he says.
At the moment the slug bait facility produces 80% metaldehyde and 20% ferric phosphate pellets, with the UK very much leading the way where the newer active is concerned, says Simon McMunn, commercial manager for the UK and Ireland.
Predicting the product requirements for a pest whose pressure is influenced so much by the weather is difficult at best, says Simon, but De Sangosse is in a unique position to respond to demand because all their slug pellets are manufactured ‘in-house’.
Arnaud explains that in order to switch the factory from metaldehyde pellet manufacture to ferric phosphate involves a two-day clean down procedure. To provide more manufacturing flexibility De Sangosse are in the process of building a new state-of-the-art factory, which will be up and running this autumn.
“It’s a strategic investment costing €10M and will enable us to respond more quickly to variations in the market because we can produce slug pellets containing different active ingredients at the same time,” explains Simon.
One of the things that makes slug pressure so difficult to forecast is their biology. “Slugs are hermaphrodite and a single slug can lay 100-500 eggs in 10-50 clusters. The time the eggs need to incubate depends on temperature, with hatch in 2-3 weeks at 20⁰ or it can take 5 months at 5⁰C.
“Slug activity depends on light and temperature, with 18⁰C the optimum. Humidity is necessary for movement, with slugs able to travel 2-7m/day under favourable conditions,” he says.
Simon believes slugs are an important part of the ecosystem as one of nature’s recyclers, so agriculture needs to be able to live alongside them but not to the detriment of the crop. That means an integrated approach to slug control is needed that employs cultural controls, takes the tillage systems used on a farm into account, identifies the risks and monitors slug populations in an effort to reduce the need to treat.
“Treatment decisions should always be based on likely economic damage to the crop and take into account unintended consequences of actions on the farm on slug numbers. For example, the loss of neonicotinoid seed treatments will probably result in more pyrethroids being sprayed, which will affect natural slug predators such as carabid and ground beetles,” he points out.
Simon believes the industry has been fooled into considering the number of baiting points as crucial for good slug control. “Around 6-10 slugs are killed per pellet, depending on their size and species. If the number of baiting points is 30/m2 and each pellet kills 10 slugs, then that’s 300 slugs/m2. If slugs were present at this population, the ground would be moving,” he says, explaining why more baiting points aren’t necessary.
But there’re also further consequence of making product choices by the number of baiting points they provide, believes Simon. “A smaller pellet won’t demonstrate consistent ballistic properties, resulting in poor application. It also represents a higher surface to volume ratio, which potentially can lead to increased leaching of the active ingredient and degradation of the pellet. All of which will result in reduced levels of slug control.”
There’s an old French proverb which says ‘long after the price is forgotten, quality remains’ which seems to hold true for champagne, foie gras and slug pellets!
Good control is all in the application
In a summer reminiscent of 1976, it’s hard to imagine slugs are able to survive the drought. But when wet weather returns, slug populations have an uncanny ability to recover.
Where slug pellets become necessary, application is as important as the choice of pellet, explains Charlotte Foxall of SCS Spreader & Sprayer Testing. She advises some simple measures to make sure growers get the best out of the pellets they’re applying.
“Monitoring comes first and foremost when it comes to slug control and can help establish real-time populations to base application decisions on. Once slug population levels have been established, inspect your machinery to ensure the spreader is fastened correctly, the electrics are functioning, and the discs, vanes and agitation mechanism are in good condition and turning correctly.”
Pellet quality also has a big impact on spreading accuracy, explains Charlotte. “There are four main characteristics that combine to make a good quality slug pellet. This includes size, which is best between 2-3mm, a uniform shape, a strong pellet that has a crush strength over 3kg, and a density over 0.7kg/l.”
Once a robust pellet is selected, Charlotte advises carrying out a full-width tray test to establish an accurate spread of the pellets, aiming for a balanced number of pellets per tray.
“This is vital to ensure maximum impact at minimum cost, and reduced wastage which is all better for the environment,” she says. “When switching between products it’s also important to recalibrate between, or after, each use.”
With ongoing pressure on metaldehyde usage and the introduction of 10m buffer zone guidelines from the Metaldehyde Stewardship Group (MSG), growers are increasingly using ferric phosphate as well as metaldehyde, with some switching entirely to ferric phosphate due to its efficacy and environmental benefits, explains Chris Charnock, Certis’ arable product manager.
“As Sluxx (ferric phosphate) isn’t soluble in water, it has an extremely good environmental profile and fits particularly well in high-risk situations, such as vulnerable drinking water catchment areas. It’s a high quality, uniform, wet process pellet so is a good choice this season as it spreads well, is rainfast and has anti-moulding properties.
“If all the tips above are followed then an accurate, cost effective and environmentally aligned slug pellet application can be achieved,” he concludes.
No change yet for metaldehyde
The future of metaldehyde and any statutory requirements that may accompany it’s reapproval are still in the hands of the regulators. With the slug pellet application season fast approaching, it’s business as usual as far as metaldehyde is concerned and all the enhanced stewardship measures remain in place.
Alison Hall, spokesperson for the MSG, explains that while it was hoped that metaldehyde product re-registrations would come through ahead of the 2018 slug pelleting season, the process is still ongoing.
“There’s still no decision, but we’ve been making a strong case to the authorities, particularly as to how stewardship is delivering environmental benefits,” she says.
Of the key stewardship measures, the larger buffer zone introduced last season is important to ensure no pellets fall within a minimum of 10m of any field boundary or watercourse, reminds Alison.
“The buffer was historically six metres and it only applied to watercourses. But increasing it and applying the zone to all field boundaries helps protect birds and small mammals, as well as providing additional protection to water,” she adds.
“With the view to helping minimise slug infestations and reduce the need for treatment, metaldehyde slug pellets should be used as part of a wider Integrated Pest Management (IPM) programme.
“Factors such as soil and stubble management, planting methods, weather, trapping and monitoring should all be considered as part of slug control programmes. And if treatment is necessary, remember to refer to the full set of MSG guidelines,” she says.