A ground-breaking project with the potential to transform how you feed your crops and dramatically cut food waste has just got underway. CPM reports on the mindset change that’s driving the circular economy.
Climate change and soil erosion have moved up the agenda and that’s led to a seed change in how waste materials are viewed.
By Tom Allen-Stevens
A much-quoted statistic, and one over which Society beats itself up, is that around a third of all food produced by the world’s farms is wasted. So wouldn’t it make sense if that food waste was recycled back into agriculture?
It seems a logical and simple equation, but in reality it’s not – food waste is a bulky material with a high water content and a fair degree of inconsistency. That’s before you’ve even addressed regulatory issues. So this apparently simple solution is a far cry from a potential replacement to the bagged nutrients you currently rely on to feed your crops.
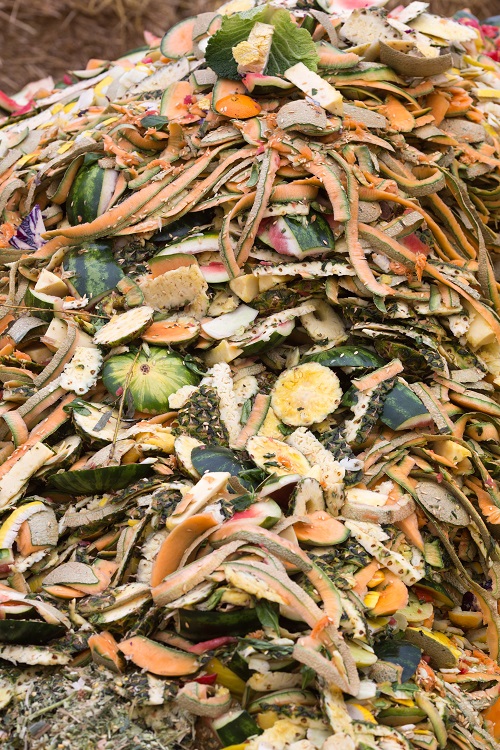
London has an estimated 2M tonnes of food waste that could be turned into a novel green fertiliser.
That could all be set to change, however. In 2019, the transnational waste management group Veolia joined forces with global fertiliser leader Yara in an initiative aimed at closing the loop in the circular economy. The Nutrient Upcycling Alliance (NUA) is a worldwide undertaking that will see the companies recycling nutrients from urban, agricultural and industrial waste into high quality fertilisers. This’ll be done through existing production processes, and locally through recovery, processing and distribution.
Since then, the alliance has gathered pace, with backing from the influential Ellen MacArthur Foundation. In three flagship cities, London, New York, and São Paulo, the foundation is leading major food system projects to demonstrate how a circular economy vision for food can be achieved at scale.
This has resulted in a ground-breaking pilot project that got off the ground in December last year and also involves Waitrose, Nestlé, Linking Environment and Farming (LEAF) and Waste and Resources Action Programme (WRAP). London has been chosen as the city that will address the technical challenges and explore the opportunities for turning its estimated 2M tonnes of food waste into this novel green fertiliser. And UK farmers will be the first to try it out.
“It’s very early days,” notes Yara’s Mark Tucker. “The aim this year is that we’ll have just 250kg of product to do some work with. That’ll build into bigger volumes as we go into 2022 and 2023. There are clear benefits in terms of organic matter it can bring, but for us the challenge is its nutrient value – there’s a fine balance to be struck between a straight organic matter addition and a classic mineral fertiliser.”
With Yara providing the nutritional expertise in this circular economy alliance, the technical challenge for providing the product itself falls on Veolia. The group already processes large quantities of food waste primarily into animal feed. Around 0.5M tonnes/yr of green waste processed in the UK by Veolia, including garden waste, goes into composting, around half of which is spread on farm.
The larger share of these organic additions to agricultural land comes from other organic waste streams – Veolia supplies around 160,000-180,000t/yr of biosolids, sourced from water companies, a similar amount of paper sludge and smaller amounts of digestate from anaerobic digesters.
“A major aspect of this is rigorous compliance with regulations,” notes Andrew Weeks who manages Veolia’s organic waste recycling to agriculture. “Each waste stream is judged on its own merits and has particular qualities in terms of organic matter content. Biosolids also contain phosphate, sulphur, potash, a bit of readily available N and then a fair amount of N that’s released over time.”
But the proposed product is quite different from the wastes currently spread on farm. Referred to as organomineral fertilisers (OMF), these have a high dry matter – around 80-90%. This also concentrates any nutrient content, but relative to mineral fertiliser, it remains a relatively small fraction of the material that’s in a pelleted or granular form.
OMF can be enriched or coated with mineral fertiliser to boost its nutrient content. It’s designed to be delivered in bags and applied using a conventional, solid fertiliser spreader at rates of 100s of kg/ha, rather than a contractor operation spreading t/ha using specialised equipment.
“The technology and the capacity to produce this material exists – our sister company in France produces OMF for various outlets, for example. We need to look at how the material can be processed, handled and stored more efficiently. There’s work needed to understand the nutrient content and guaranteeing the consistency of this,” notes Andrew.
“But there’s a different mindset now for how we as a society view the circular economy. Climate change and soil erosion have moved up the agenda and that’s led to a seed change in how waste materials are viewed.”
The reluctance to spread them doesn’t sit with farmers, he notes. “Those we already deal with know the benefits for soil structure of putting waste to land– that’s well understood. The resistance has come from regulatory authorities and that’s where there’s now a more positive mindset. So I can see this project may start small, but it’ll grow arms and legs as we all gain confidence in the potential for the product.”
So what exactly is the potential, specifically for agriculture? Dr Ruben Sakrabani is senior lecturer in soil chemistry at Cranfield University and has spent many years researching OMF and its value for agriculture.
“The research started in 2006 and initially we worked with United Utilities. Based in the North West, they were looking to spread biosolids produced at their plant on land outside the area closest to it – mainly grassland agriculture where phosphate loading was in danger of exceeding advised limits. It makes sense to turn the biosolids into a product that can be economically transported to combinable crop areas currently relying on mined sources of P which are less sustainable.”
United Utilities produced an OMF by drying sewage sludge cake in a tumble dryer from 25% dry solids to 80-85%. The resulting granules were coated in melted urea and ground potash to boost their nutrient value from around 3% N, 4.35% P₂O₅ and 0.15% K₂O to form two new products: OMF10 (10:4:4) and OMF15 (15:4:4). The aim was for a product that did no more in terms of phosphate loading than replenish crop offtake, Ruben explains. “Narrow N:P₂O₅ ratios in the product are suitable for lower P-index soils, while the OMF15 would suit situations where the aim is just to maintain soil P index.”
Spreading studies showed the OMF gave a gave a reasonably uniform result through a standard twin-disc applicator to 24m. Field studies were carried out at Silsoe, Bedfordshire, over four crop seasons (harvest 2007-10) in which the performance of straight biosolids was compared with OMF and urea. Grain yields were highest where urea was applied – 10.35t/ha at the most economic rate of N (MERN) of 225kg/ha – and lowest with the biosolids (7.9t/ha at 245kg/ha MERN). OMF came midway between the two, with OMF10 yielding 9.1t/ha at 257kg/ha MERN and OMF15 producing 9.5t/ha at 249kg/ha MERN.
Differences in grain yield and yield-to-N responses between treatments were due to relative patterns of N release from fertiliser applied to the soil influencing N uptake, biomass accumulation, and partitioning, notes Ruben. “You could improve performance of winter wheat treated with OMF by applying a straight N fertiliser source as the first dressing and OMF as the second,” he suggests.
Importantly P levels were found to rise where biosolids were applied, dropped back slightly where just urea was applied, but OMF P replaced crop offtake, supporting the product as a sustainable source of the nutrient. “We’ve also found OMF brings discernible differences in soil quality – it increases moisture retention and soil organic matter (SOM) content, confirming the hypothesis,” he adds.
“The difficulty with the material is in its production. To bring it from 25% dry matter up to the 85-90% needed for efficient transport and effective spreading requires a lot of heat. There may be opportunities to use waste heat, depending on the nature of the plant processing it, but clearly if you need to use fossil fuels to produce OMF, that would cancel out its green credentials.”
Ruben believes this is the main barrier that’s kept the technology from commercial adoption, despite the obvious benefits for soil health and the circular economy. However, there could be even greater benefits in terms of carbon capture that may reignite interest.
“There’s a lot of talk at present of carbon capture technologies, with industries responsible for high CO₂ emissions looking at technology that traps it into the sea or underground. But this is static carbon – what may be of more interest is to influence the active carbon in soils with OMF.”
He’s currently working on a project funded through UKRI’s £90 million Transforming Food Production programme, part of its Industrial Strategy Challenge Fund. The 18-month project started in Oct last year and is led by CCm Technologies, based in Swindon. The company’s developed a method of producing fertiliser and soil conditioner through the use of captured CO₂ from industrial power generators.
“We’re carrying out trials at the Luton Hoo Estate to evaluate the efficacy of this product, looking in some detail at the top 80cm, using scanners to study root architecture.”
Ruben’s hypothesis is that adding carbon to the soil affects the dynamics of the active carbon cycling within it. Get the balance right, and you can significantly increase the capacity of the soil to sequester carbon. Not only that, but you increase soil health and the productivity of your crops. “It’s a work in progress, but carbon capture, blended with the organic material in the soil, is the way forward,” he says.
So what does the farmer get from this? The immediate benefits are potential increase in soil health and, as a market develops for it, carbon credits. Neither will necessarily add to the bottom line nor tempt you away from mineral fertiliser, however.
“The cost of OMF on a nutrient basis is around a third less than conventional fertilisers. A key part of this is it then stimulates the organic, inherent residue nutrients in the soil to work harder for you,” adds Ruben.
For Mark there remain a lot of unanswered questions and barriers that have yet to be overcome. “Hopefully what we’ll produce through the NUA will be suitable for organic farmers as an addition that will help build soil health. The challenge is to get the N bit right for conventional farming systems. There may also be problems of ammonia release when using food digestate.
“But fertiliser is and always will be the big component of sustainability in any farming system and the progressive farmer will always be questioning whether a different approach will reduce its use or build fertility or both. The single best way to set your path on this route is to take steps to build soil organic matter,” he notes.
“There’s a change of mindset taking place – it’s not just about crop performance any longer but what you can do for your soil to optimise its performance. I think the solutions lie in a combination of organic additions and carefully selected nutrients, but there’s a lot of knowledge to acquire before we can strike the right balance.”
Grow the future
Climate change, societal demands, changing consumer trends and not least the weather – one thing that’s certain about farming is that it’s anything but predictable. So the best farms must be efficient enough to grow crops both sustainably and profitably now and in the future.
Few aspects of crop production are more critical in this than a plant’s nutrition, which is why CPM has teamed up with Yara. This series of articles looks at some of the innovations coming into this area and the practical steps needed to ensure your farming system is set to grow the future.
With decades of evidence-based knowledge, Yara continues to be at the forefront of crop macro and micronutrient advice. Investment in technology has resulted in world-leading products that support in-field decision-making and precision nitrogen application.