When it entered the round baler market 20 years ago, McHale’s initial focus was on fixed chamber models best suited to silage, but in 2009 it introduced variable chamber machines also capable of high outputs in straw. CPM visits an early customer of the V6 760.
“Being close to the coast means sea mists can limit our baling days and daily hours.”
By Martin Rickatson
Contractors or larger mixed farms with beef or dairy herds often require a machine that will produce 4ft/1.2m silage bales in spring and then be easily adaptable to making full-size 6ft/1.8m straw bales in summer. A variable chamber round baler is an important machine in these cases.
On the Lincolnshire Wolds, near the village of Skidbrooke, beef and arable business J & JR Appleby is in exactly that situation – requiring the universal capabilities of a belt-type machine that is reckoned to be as capable of baling (and chopping) high-moisture grass as it is packaging long, dry straw.
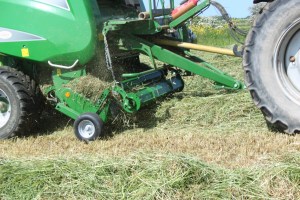
The farm’s V6 760 features McHale’s 2.1m five-bar pick-up, which feeds the 15-knife chopping unit for the 1500 silage bales made annually.
The 400ha family farm comprises combinable cropping, including wheat, barley, oilseed rape and beans, and 160ha of owned and rented grassland to support an autumn/spring-calving beef breeding herd of 200 head plus followers.
When the livestock enterprise’s straw and silage requirements are added to regular contract haylage baling, that means in some years as many as 6000 round bales are made, supplemented by further square-baled straw. And with the farm very close to the North Sea coast, baling hours per day can be limited, even when working on straw during the height of summer.
“We also operate a large square baler for part of our straw requirements, but round bales work best for silage, for feeding straw and for bedding straw in some harder-to-access buildings where we over-winter cattle,” explains Andrew Haith, who carries out many of the main tractor operations on his family’s unit, alongside his uncle, cousin and mother.
“Before we moved to McHale, we ran a Lely Welger RP520. That served us well, but when it came due for replacement in 2012, Lely had sold its baler line, so we looked wider at what was on the market. JPM Agricultural, which is based nearby, had become a McHale dealer, and offered us the opportunity to try a variable chamber McHale V660 baler on demo. Its output and bale formation impressed us, and we decided to buy the demo machine.”
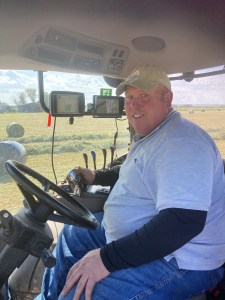
For silage, feeding straw and for bedding straw in some harder-to-access buildings, round bales work best, says Andrew Haith.
Capable of making bales from 0.70-1.68m diameter, and with a 15-knife chopping unit, three-belt variable chamber and drop-floor system to tackle any blockages, the V660 proved capable in both silage and straw, as well as contract hay/haylage work, and produced around 15,000 bales over the next decade without complaint. At this point, McHale introduced an updated V6 series of variable chamber balers, and JPM again offered the family the opportunity to try a unit, the flagship V6 760, on demonstration.
The highest specification machine in the maker’s current three-model V6 range (there is also a non-chopper V6 740 and a V6 750 which mirrors the V6 760), the key difference between the V6 760 and the V6 750 that sits alongside it – offering the same bale diameter capabilities and 15-knife chopper unit – is the complete automation of the baling process.
“McHale balers were an unknown quantity to us when we first tried one, but after the experiences we had with reliability, ease of use and bale quality with the V660, it was an automatic choice to look to McHale again when it came to upgrading,” says Andrew.
“While the V660 coped well in silage and straw, the level of automation integrated into the new V6 760 made a big difference to output when I tried it during early 2020, and although I didn’t really doubt that I wanted another McHale, it was this which really sold the idea of the updated model to me, so we purchased the demo unit.
“Being close to the coast means sea mists can limit our baling days and daily hours and with straw especially, the crop might only be dry enough to bale in the middle of the day. Added to the fact we are on quite heavy ground that holds moisture, we need a high-output baler capable of 50-60 bales an hour to clear as much crop as possible in the short windows we have.”
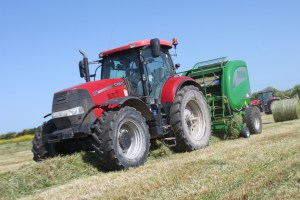
Bale netwrapping and ejection is automated once the tractor comes to a halt, with the tailgate opening only as wide as required.
With plastic costs having almost doubled in the past two years, the ability to pack in as much silage as possible into each bale is welcomed for financial reasons as for practical and feeding ones, he adds.
“Of the 4000-6000 bales the machine turns out annually, about 1500 are silage bales for our cattle. That starts the baler’s season in May, when we make full use of the chopping unit, although we don’t use the outer blades, as we find this helps the bales retain their shape, yet they still process well in our vertical auger Shelbourne Reynolds diet feeder.
“With most of the remaining baling workload being haylage and hay – some of which is contract work – plus some wheat straw for bedding and barley for feeding and bedding, we don’t use the chopping unit. We do most of the bedding straw with our Massey Ferguson 2170 big square baler, but we have some buildings where bedding has to be done by rolling out round bales, so the McHale also bales quite a bit of straw for us and for some contract customers.”
The full automation system on the V6 760 has made a big difference to ease of operation and hourly outputs, says Andrew.
“As soon as the chamber-full alarm sounds, I just have to bring the tractor to a halt and the netting and ejection process starts automatically. It makes a long day much less tiring.
“Prior to this season, we also benefited from a set of upgrades McHale has installed to bring our machine up to the current spec, introduced to V760 models since they were launched. That included new valve blocks, wiring looms, sensors, a redesigned bale kicker, a rear camera and control updates.
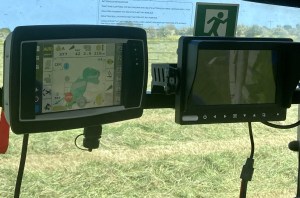
While the farm’s Case IH Puma 185 is a non-ISOBUS tractor, operating the baler via McHale’s own ISOBUS terminal (left, alongside the camera monitor) is simple.
“It’s early to judge what they do for the machine as a whole, but it’s good to see a manufacturer ensuring customers’ machines are kept up to date. JPM Agricultural, our dealer, has also fully supported us right from the day they delivered and helped set up the baler, with advice and guidance on how to get the best from it.”
Operated behind the farm’s non-ISOBUS Case IH Puma 185 powershift tractor, which produces a maximum 224hp during PTO operation, outputs have been well above expectations, says Andrew, while features such as the Intelli-Chamber control are especially welcome.
“The ISOBUS display is simple to understand and operate, and because the Intelli-Chamber system raises the tailgate by only the amount required for the bale size, it’s noticeably faster to get back to work.
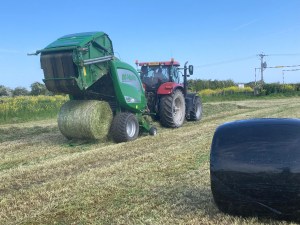
Via the ISOBUS controller or compatible tractor terminal, the V6 760’s three-belt variable chamber can be adjusted to produce bales from 0.70-1.68m diameter.
“The baler has the five-bar pick-up, and will swallow straw as fast as the crop will allow you to push the tractor. It coped pretty well with last summer’s straw given how dry it was, although I often had to make a 9pm start to avoid smashing the straw through no fault of the baler. The twin crop rollers do a good job of smoothing out the swath and the feed into the baler. I can press on, only looking round occasionally to check all is ok, and only getting out to replace netwrap rolls – the baler holds one roll on top and one at the front, so can cover some bales, especially with the improved tension/stretch. From the ISOBUS screen, I can adjust the net tension and the amount applied, as well as the bale density and knife pressure,” he adds.
“Even when I’ve had a smaller tractor on the front, I’ve produced 60 1.5m straw bales in an hour on a long field. Admittedly, that was pushing the machine to test what it could manage, but it will comfortably do 40-50 bales an hour all day long in straw from the 7.5m swaths produced by our Massey Ferguson 7382 Centora combine. That’s being changed this harvest for a 6.6m MF 7360 Beta, so it will be interesting to see if we get along even quicker this harvest, given that we’ll be taking in a metre less straw.”
Tech behind the bale
The ISOBUS-compatible machine can be fully controlled via an ISOBUS tractor terminal, or through McHale’s own ISO-Play 7 or 12 terminals on a non-ISOBUS tractor. It can also be set to fully automate the sequence of key functions – from net application to tailgate opening and closing, with the operator able to fully customise the baler’s operation according to preference.
Standard pick-up on the V6 760 is a five tine-bar cam-track unit, with the option of a six-bar cam-less pick-up plus double crop roller. Regardless of pick-up spec, McHale set out to boost crop intake capability by incorporating newly-designed lateral feed augers that direct material into the large-diameter rotor. An ‘Adaptive Intake’ feature allows intake area to automatically adjust to changes in material flow. This, claims McHale, allows machine capacity to be maximised regardless of swath density or the presence of swath lumps. By evening the crop intake, it’s also said to reduce the chances of blockages occurring.
Recognising that many farms seeking this size of baler will have high-hp tractors more suited to operating PTO-driven equipment at 1000rpm rather than 540rpm, the V6 760 is optionally available in 1000rpm format. This, points out McHale, allows an increase in PTO speed with a substantially reduced torque, reducing the load on the driveline, providing the clutch with 10% more capacity, reducing the risk of blockages and raising output. It also provides the option to select a lower tractor PTO speed (if available) for easier restarts in the event of a blockage. In addition, in lighter crops the 1000rpm gearbox can be operated at an optimal speed range of 900-1000rpm to maximise fuel efficiency, reduce noise and ease the load on the tractor and the baler.
The V6 760 also introduced McHale’s Intelli-Chamber control. By increasing tailgate opening and closing speed, this is said to contribute significantly to workrates and daily productivity. The system also adjusts the tailgate opening height according to the set bale diameter, to minimise component wear and the time taken to return to work.
Other features on the new baler included electronic variable density pressure regulation, reckoned to increase bale density due to the higher loads exerted on the bale at key bale formation stages. Load cell bale shape indicators, fitted on each door lock, measure the bale load on each side, displaying accurate bale shape feedback to the operator.
A new net system incorporates a larger brake, allowing for 25% more net stretch to improve performance when baling at high densities. A hydraulic bale kicker is raised/lower automatically with the closing/opening of the tailgate, which is reckoned to put more momentum behind bale ejection to ensure the bale does not impede tailgate closure.
Automatic drop floor reset is integral to ISOBUS operation, meaning that should a blockage occur, the operator can press one button on the control console to lower the floor. After the PTO is re-engaged and the blockage is fed through, the drop floor raises automatically and the knives reset to their original position. An automatic knife drop option can be enabled via the control terminal, which allows the operator to chop the crop until the bale is almost complete, at which point the machine will automatically drop out the knives. This is said to offer advantages in certain feeding systems and applications, keeping the bale neater when the net is removed. And for farms baling both silage and straw – as with the Applebys – chopping efficiency and consistency can be protected via the ability to set a knife cleaning cycle to run at desired intervals, ensuring the knives don’t become gummed up when not used for prolonged periods.
Farm facts
J & JR Appleby, Skidbrooke, Lincolnshire
Area farmed: 400ha
Cropping: 240ha winter wheat, winter barley, winter oilseed rape, winter beans; 160ha grass
Livestock: 200 head beef breeding herd
Soil type: Silty clay
Tractors: Massey Ferguson 7726; Case IH Puma 185, Maxxum 155/140/115, JCB Fastrac 2155
Combine: 6.6m Massey Ferguson Beta 7360
Round baler: McHale V6 760
Square baler: Massey Ferguson 2170
Telehandler: Kramer KT407
Drill: 4m Väderstad Rapid
This article was taken from the latest issue of CPM. For more articles like this, subscribe here.
Sign up for Crop Production Magazine’s FREE e-newsletter here.