Whereas in the past mechanical weed control’s popularity may have been mostly restricted to the organic sector, the technology is fast becoming a part of everyday farm management including in conventional systems, believes Lemken’s Paul Creasy.
And in adopting the technology, growers are starting to realise the added benefits that hoeing machines and harrows can offer – from promoting root growth to improving crop establishment.
“There are many advantages when it comes to mechanical weed control,” says Paul. “The list includes saving water, breaking up compaction, interrupting capillarity, releasing nitrogen, promoting mineralisation and of course, reducing the use of chemical plant protection products.”
Furthermore, as rotations widen to accommodate alternative break crops and address new market opportunities, Paul adds that having a customisable machine is often top of the list when it comes to grower requirements. This is where Lemken’s Thulit weed harrow comes in.
Thulit weed harrow
“The challenges for successful mechanical weed control are constantly evolving – however, it must start with small and sensitive plants, and be feasible in all crops and at as many development stages of the crop as possible,” explains Paul.
“For the Thulit harrow, we’ve developed a unique combination of tine shape and hydraulic tine adjustment. This ensures a constant contact pressure over the entire process path with every adjustment.”
The tines
The Thulit’s tines are 575mm long diagonally, with a bend of 118o. Paul says these dimensions are to ensure a constant pressure regardless of the tine position, and with an 8mm diameter, they’re very stable.
“This ensures good power transmission to the ground and prevents lateral deflection. Therefore, they work evenly without overlaps or misses across the entire working width of the machine to reliably remove weeds. The large wear area of 120mm guarantees a long service life of the tines.”
If necessary, the tines can be easily replaced using the quick-change system, highlights Paul.
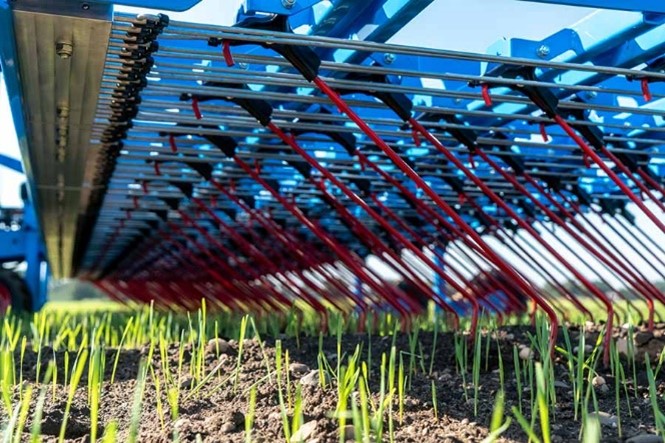
OptiTine hydraulic pressure adjustment
Tine pressure can be continuously adjusted from the tractor cab even while driving, with adjustment options ranging from 100g to a maximum contact force of 5000g/tine.
“The indirect loading of the harrow tines ensures constant pressure with every tine position or angle, both on flat surfaces and when working in ridge crops,” explains Paul.
“The tine pressure is infinitely adjustable via a hydraulic system; to ensure each tine can be controlled separately the tines are connected to a ram and combined in cylinder bars with 5-16 rams.”
These form a completely closed, sealed and double-acting system meaning pressure is the same everywhere and the rams can work in both directions, he adds.
Support wheels
Paul says the Thulit is available with a wide range of support wheel options for perfect results. “Their working height can be adjusted in eight steps on the profile toolbar, allowing the aggressiveness of the tines and the clearance height to be adjusted.
“The profile toolbar also makes it easy to adjust the track width of the support wheels to match the row spacing of the crops,” he comments.
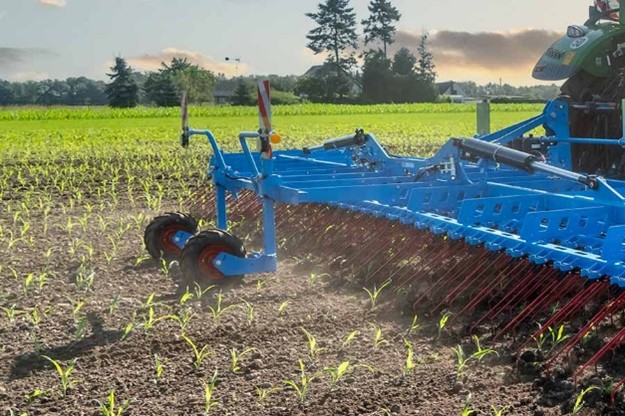
Improved visibility
According to Paul, an important feature of the Thulit is that it always provides sufficient visibility at work – it’s based on a four-beam frame concept in contrast to the eight beams commonly found on the market.
“With a reduced number of bars, the beam profiles can be designed for superior stability, while also keeping the total weight low.”
He adds that thanks to the OptiTine hydraulic tine pressure adjustment, the driver’s field of vision isn’t obstructed by springs. “With fewer bars and moving parts in the harrow frame, the tines are clearly visible, and work results can be checked earlier and better.”
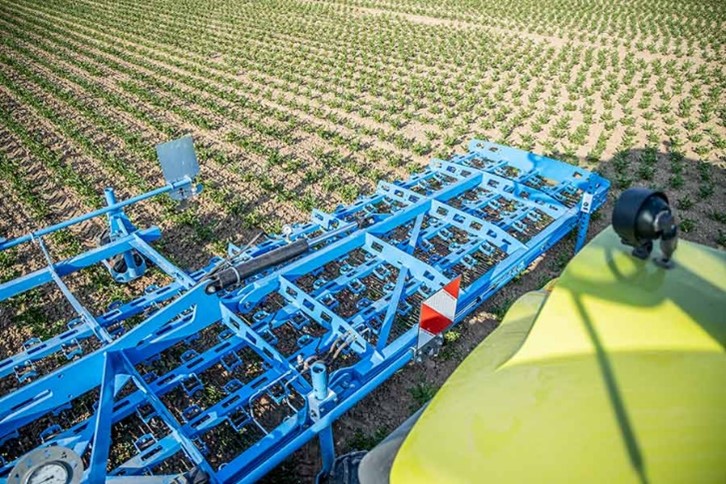
Optimum results
The 31.25mm line spacing of the Thulit weed harrow is adapted to the frequently used row spacing of 12.5cm for drilling. With an asymmetric tine arrangement, the Thulit provides up to 15% greater clearance between the tines than conventional harrows, points out Paul.
Whereas its well thought-out design and wide tine spacing means the Thulit requires only 32 tines per metre of working width, making it as light as possible. “At the same time, it’s heavy enough to make the most of its tine pressure of up to 5000g to produce outstanding results,” suggests Paul.
High ground clearance
He believes the Thulit is particularly impressive due to its high ground clearance. “There are no springs or sharp components under the 450mm high frame in which plants could get caught. This also simplifies harrowing in ridge crops or late growth stages, as blockages are reduced to a minimum.”
For a smaller working width and to avoid obstacles, the weed harrow can be folded on one side only. The nine and 12-metre versions additionally offer the option of raising the implement into a V-position for turning.
“To do this, the outer folding segments are angled in slightly which protects the crop from damage caused by the tines,” says Paul. “The process for V-folding or single-sided folding is triggered via the optional control box. If this option is used, one spool valve is required on the tractor instead of three,” concludes Paul.
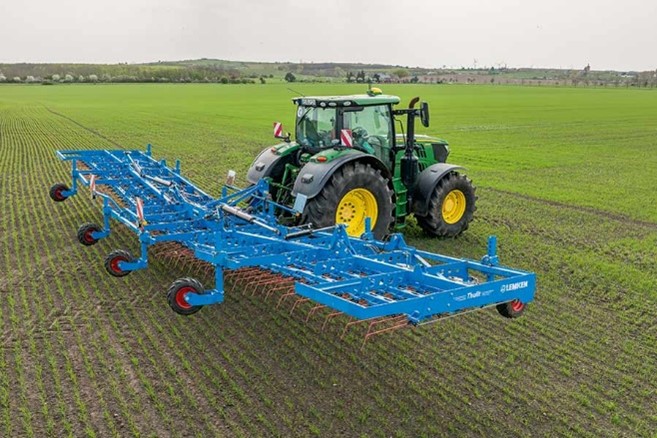