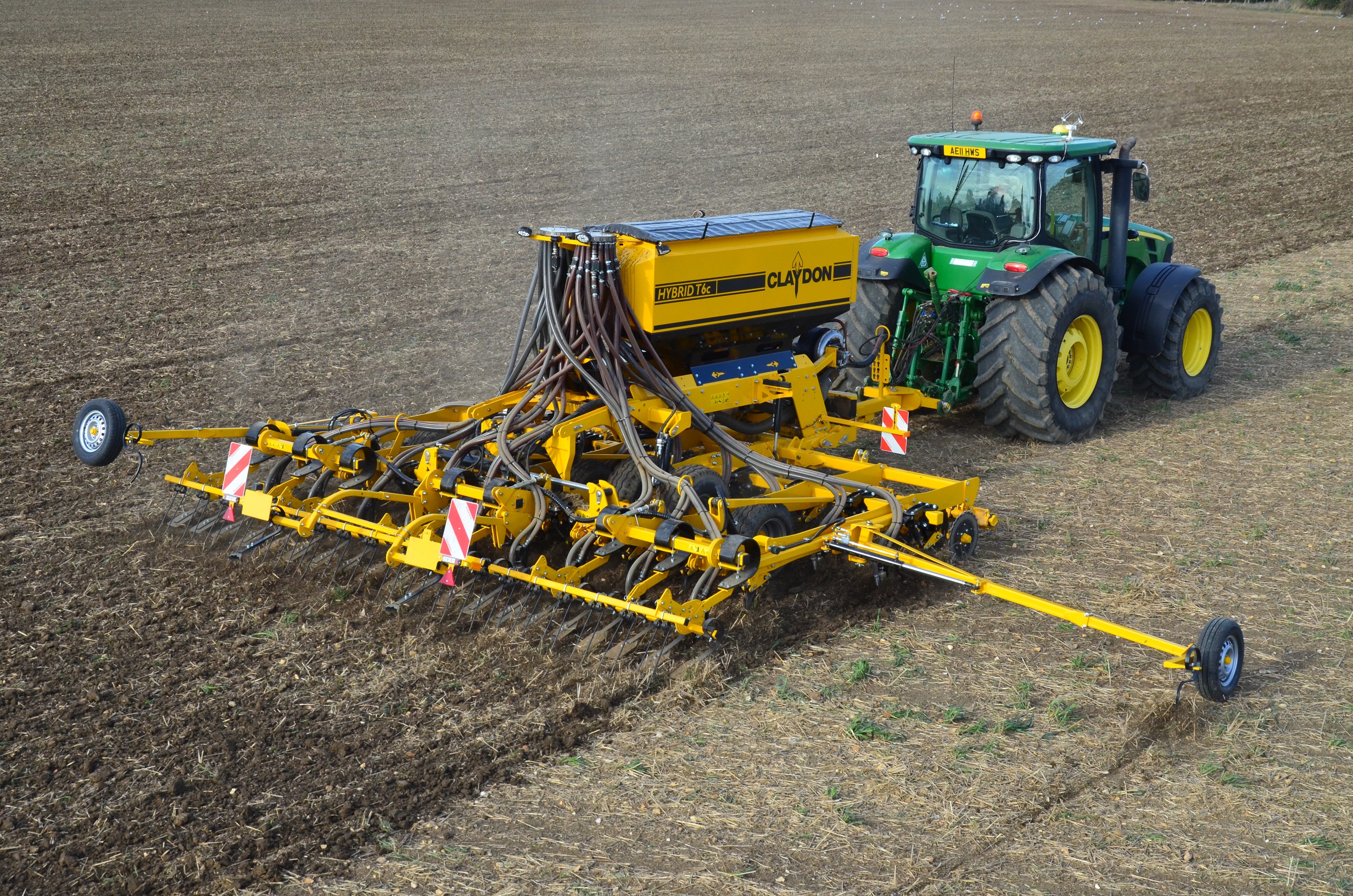
Claydon Drills, one of the European market leaders in direct strip seeding technology, will exhibit its new 6m OptiTill T6c compact trailed drill at LAMMA 2019 (Hall 6, Stand No. 6.600).
The T6c is the latest development of the pioneering Claydon OptiTill system which the company has perfected over the last 16 years to optimise crop establishment, development, performance and profitability; this latest model builds on the success of the existing 6m T6 drill, one of six trailed models from 3m to 8m.
“The new T6c is over 20% lighter and more compact than our standard T6, which was designed for larger farms and contractors who can make full use of its 5500-litre hopper capacity to maximise the area covered between fills and daily output,” Jeff Claydon, founder and CEO of Claydon Drills, states.
“The T6c combines the high output of a 6m seeding platform with the nimble handling characteristics and manoeuvrability of our 4m T4 trailed drill, on which it is based. We believe that the new model will prove very popular with farmers in the UK and other countries who value the combination of lower cost and greater manoeuvrability over ultimate hopper capacity and output.”
Capable of drilling typically 45ha per day behind a 300hp (223kW) tractor, the T6c is carried on the lower link arms and features a fully-floating seeding chassis which follows field contours exactly, ensuring accurate seeding depth under all conditions. It does this regardless of the weight in the hopper, which is carried on a separate frame supported on centrally-mounted depth wheels that run on clean, dry, uncultivated ground to avoid capping and compaction.
Providing a hopper capacity of 3500-litres, double that of Claydon’s 6m mounted drill, the T6c weighs approximately 7000kg unladen, compared with 9000kg for the T6. The hopper can be used for seed only or divided 60:40 between seed and fertiliser for combination drilling, a technique which is becoming increasingly popular with farmers and agricultural contractors throughout Europe and Scandinavia to get crops off to a fast start. The diameter of the pipes which transport seed and fertiliser from the hopper to the tines is 38mm.
Versatile, flexible, simple, strong, easy to use and with low operating costs, the T6c will sow directly into stubble, in min-till situations or on ploughed/cultivated land, across the widest range of soils, conditions and crops. This enables one drill to handle any crop establishment situation and minimises capital investment.
The 19 individually-adjustable tungsten carbide leading tines reduce compaction and aerate the soil. Theyoptimise drainage, form tilth for the seeding zone and create a uniform seeding depth. The following seeding tines create additional tilth and place the seed at the ideal depth, above the drainage channel. This highly effective system encourages very deep, complex rooting structures to develop quickly, which minimises soil erosion and produces stronger, healthier crops with optimum yield potential.
The new drill can be adapted to whatever the customer requires to suit different crops and conditions. They can have the standard tine set-upwith a variety of coulter and seeding boot options, choose to have fertiliser placed down the front or rear tine, andcan specify front shouldered cutting discs or press wheels. At the rear, the double toolbar can be equipped with a range of press wheel, boardand harrow configurations to fully cover the seed and leave the soil smooth and level.
Providing unparalleled versatility, the T6c folds to 2.97m for transport and is equipped with a wide range of standard features, including single-point depth control, a stainless-steel Kverneland metering system and an ISOBUS compatible RDS Artemis control system which provides tramlining and variable seed rate capability. The specification also includes a hydraulically-driven fan, Claydon-designed distributionheads for improved flow and seeding accuracy, together with a tramline kit and hopper cover. Amongst the options are a vision kit which incorporates work lights and cameras so that the operator can monitor the drill from the tractor cab, GPS variable-rate seeding, blockage sensors, pre-emergence markers and brakes.

Developed by Suffolk farmer Jeff Claydon, the Claydon OptiTill system is up to five times faster, one-third the cost and more reliable than a plough-based approach and typically 50% cheaper than min-till. Itsignificantly improves timeliness, enabling crops to be established at the optimum time, under the best conditions, resulting in significantly higher yields and profitability.
Claydon’s extensive product range includes mounted and trailed drills from 3m to 8m, Straw Harrows from 3m to 15m, the 6m TerraStar light rotary cultivator, TerraBlade inter-row hoes from 3m to 6m, heavy rolls from 6.3m to 12.3m and an injector system which allows farmers to strip inject and cover sewage/digestate directly into stubble fields. Claydon products are sold in over 30 countries by the company’s commercial team through an ever-developing distribution network and operate across the widest range of climatic conditions and soil types.