An even application over a bout width up to 40m is an essential part of optimising crop performance. CPM reviews recent advances that put the prill in its place.
The machine can also compensate for adverse wind effects on the spread patterns.
By David Jones
Accuracy of application and the optimum quantity of product have, between them, been the focus of much of the research effort for makers of fertiliser spreaders in recent years. Their engineers have been tasked with developing spread patterns that promote high crop yields while minimising the impact on the environment. So, how far have we come to date and what can growers do to help achieve this balance?
Almost 20 years ago, Rob Foxall took over Spreader & Sprayer Testing, a company which was then testing around 300 machines annually. Operating as Spreadcheck today, customer numbers have now grown to more than 4000 a year and over that time Rob has witnessed major advances in spreader technology.
“As always, things move on,” he observes. “Today, Amazone have their Argus system and Kuhn their Axmat. Both of these systems watch the fertiliser flying off the discs and compare it with known ‘good’ spread patterns. If the pattern changes as a result of fertiliser variation, the system will alter the spread pattern to ensure a ‘good’ pattern is maintained, so avoiding stripes.”
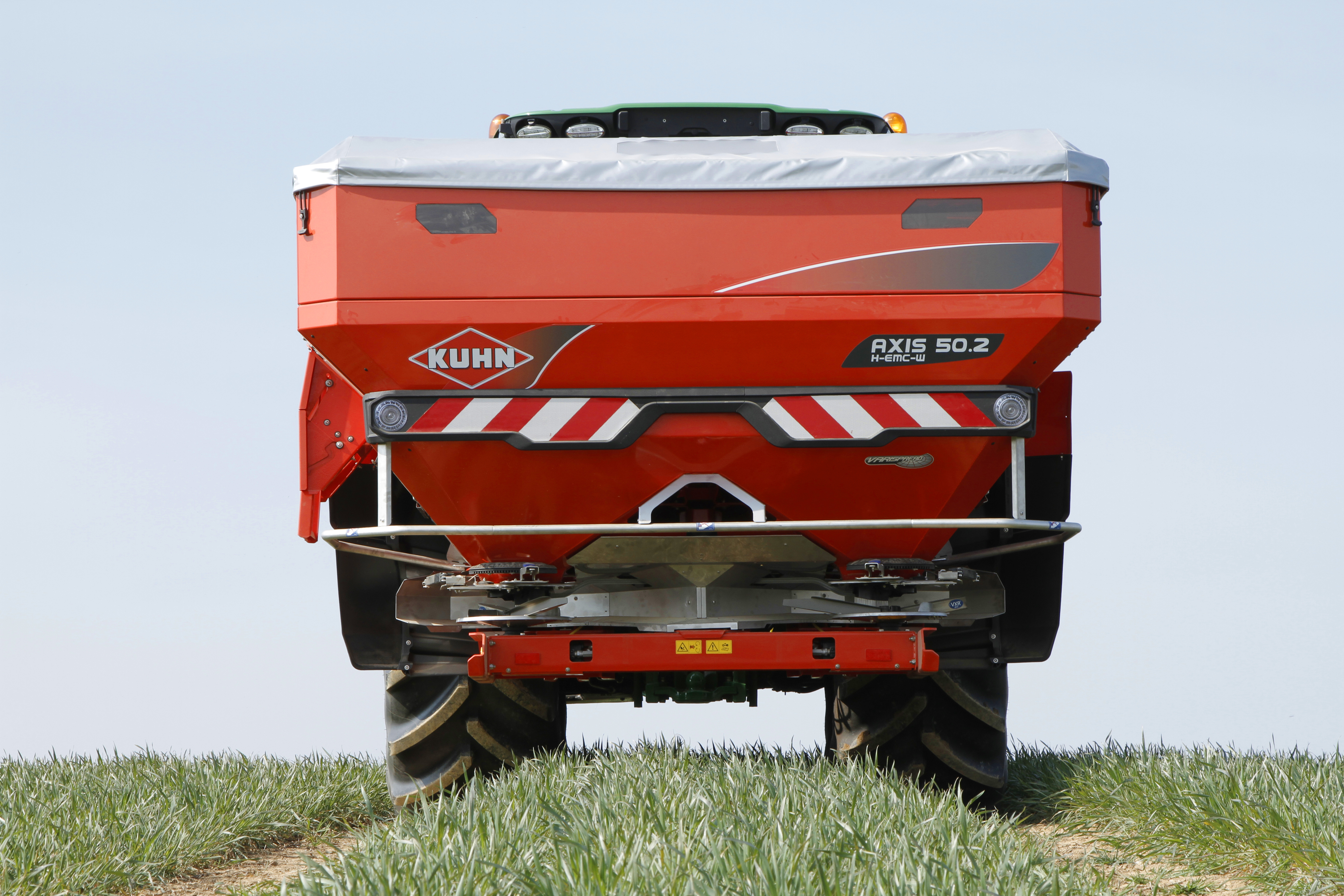
Electronic Mass .Control is a core element of Kuhn’s Axis spreaders
The starting point with these systems, Rob explains, is to use a ‘good’ pattern as the base – an initial tray test is still required so that the spreader knows what the ‘good’ base line is. “Personally, I think this is good for growers – if expensive – but the manufacturers need to ensure that growers are aware that a tray test to ensure even spreading is still the initial job: if the machine doesn’t know what it’s supposed to be aiming for, then it can only guess.”
The impact or benefit of this, Rob states, is the ability to set up spreaders correctly so that they have the ability to cope with fertiliser variations on the move. “In the case of Amazone, using their wind meter in conjunction with the Argos system, the machine can also compensate for adverse wind effects on the spread patterns. The machine should become more accurate in windy conditions, or if you are using variable quality fertiliser.”
The speed at which a machine is able to react to changes in rate, forward speed and spread width – in relation to sectional control – is critical when it comes to accuracy. This is the area of spreader technology that’s been the focus of work for engineers at Kuhn/Rauch in recent times. Kuhn area sales manager for the eastern counties, Paul Gregory, explains the latest milestone in this area.
“We’ve concentrated our efforts on developing faster and more efficient components in order to successfully achieve this objective,” he says. “The introduction of SpeedServo is the result of this focussed development.
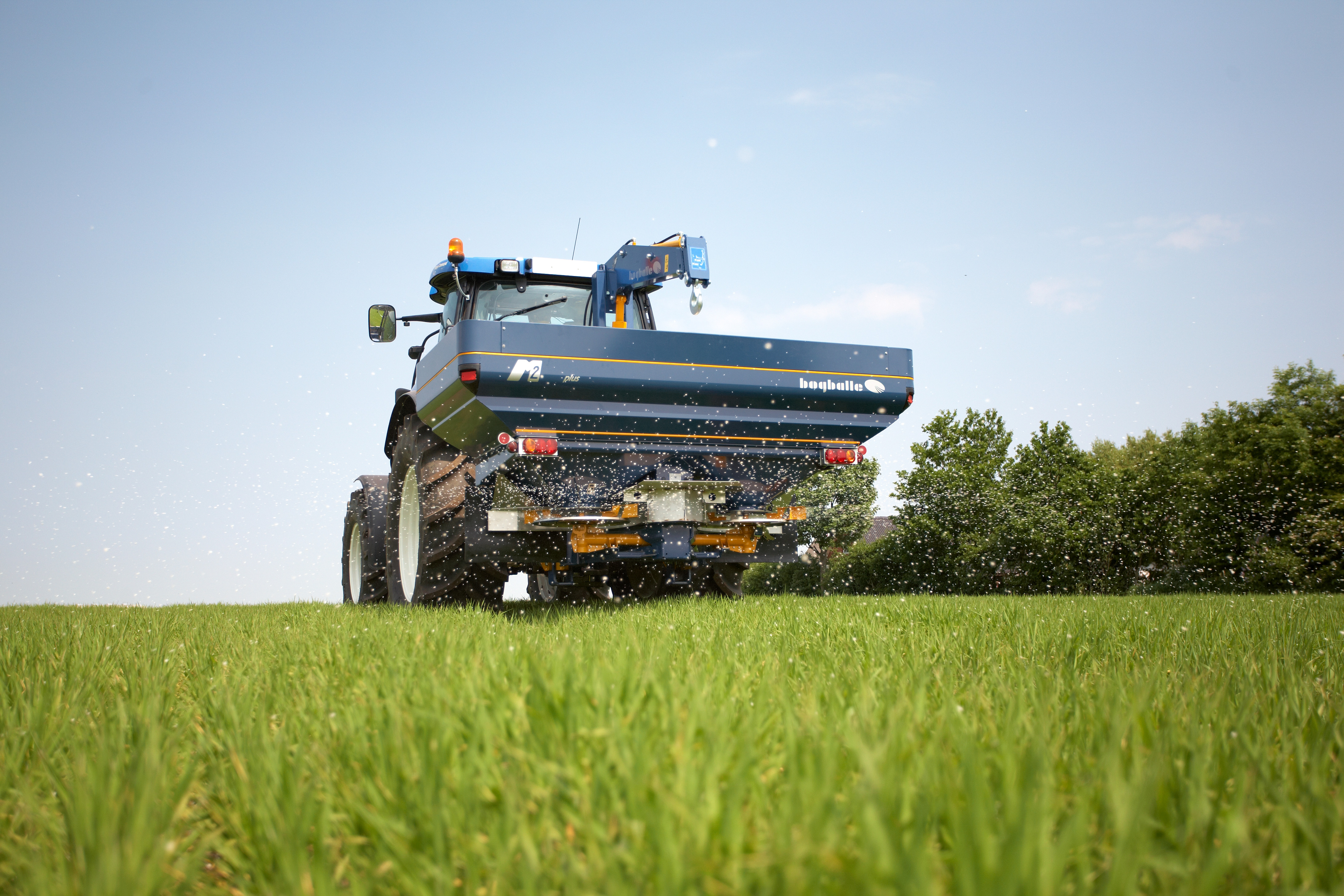
On KRM (Bogballe) spreaders, the two shutters operate away from each other to ensure that the drop-on point is unaffected by outlet size.
“Looking at the new elements of the three Axis models that have it, there are now no external moving parts, such as the original actuators – they’re now sealed units, and 2.5 times faster than the Axis .2. The OptiPoint is more accurate, as is the process when changing forward speed and when carrying out variable rate applications.”
Other changes include faster Varispread and Varispread Pro. “Varispread Pro,” Paul explains, “now allows the sectional control to operate in 1m sections. This means that if you’re working to a 24m tramline width, you will have 24 x 1m section shut-off – and so on, with the 30m (30 x 1m section shut-off) and 36m (36 x 1m shut off). The ability to separate 1m sections, he adds, comes from the components being able to accurately and quickly adjust as the machine moves around the headland areas of fields.
Having mentioned OptiPoint, Paul goes on to describe its function: “It’s a system that automatically controls aperture opening and closing at the headlands, minimising over- or under-application – whatever the shape, size, density or air resistance of the fertiliser.
“How it works is by pre-programming all the relevant information into whichever control box is being used – Kuhn CCI, Quantron or third party – to calculate the optimum aperture opening and closing point, in conjunction with GPS guidance,” he states.
Although not the most recent development from Kuhn, Electronic Mass Control (EMC) is still a central element of the spreading function in its Axis range. This provides constant measurement of material passing through each individual disc, in kg/min, at the point of application. This allows the machine to adjust the aperture size, on the move, so that the target application rate is maintained.
“EMC avoids the need for conventional static calibration testing,” Paul says, “as the machine makes the adjustments from simple pre-programmed data. What this means is that 100% of all the machine settings can be set without the operator having to leave the cab.”
Over at KRM, the degree of innovation the company has introduced to the task of spreading fertiliser is also evident. “Smarter, Faster, Stronger” is the slogan the company modestly applies to its Bogballe-based spreader range, so how does that manifest itself in the current line-up?
A detailed look at some of its innovations provides an impression of KRM’s determination to set new benchmarks within the sector. Simplicity with accuracy has been the company’s driver and nowhere is this more apparent than in the weigh cell set-up.
It revolves around a new generation Zurf electronic controller which incorporates ‘intelligent control’ hardware and software. The system assesses and sifts the information from the weigh cell in order to utilise data that’s only valid for maintaining accuracy of spreading on level ground and up, down and across slopes.
This data is validated automatically while the machine is on the move, but isolates the effects of bounce when the soil is hard, the degree of slope and the amount of product in the hopper. This process, KRM states, makes it the most accurate spreader on the market.
However, it’s made clear that when spreading fertiliser at a variable rate, the machine being used must have the ability to apply different rates on the move without having to physically make adjustments. KRM uses the same patented outlet design on all its spreaders, which involves two shutters that operate away from each other to ensure that the drop-on point is unaffected by outlet size.
Extensive testing by KRM revealed the need to advance the drop-on point slightly as the rate being applied increases, the outcome being that one outlet opens marginally ahead of the other and the advance is automatic. To find out how this translates on farm, turn to pxx.
Sulky Burel used last month’s LAMMA event to reveal the latest updates to its X40+ and X50+ fertiliser spreaders and the DX30+ range. Two new pieces of equipment – a hydraulic drive solution for the spreading discs and two low level sensors – have been added to the X40/50+ models.
The hydraulic drive element means that the spreading discs now work independently of engine speed, with the effect of maintaining the spreading disc rotation speed constant. This addition, Sulky’s Richard German says, gives a boost to performance and usability by making coupling simpler, so promoting an even spread and reducing fuel consumption when spreading at a lower engine speed.
“What’s more,” Richard says, “we also have the hydraulic half-width deflector controlling the spread. This is particularly suitable for vegetable growers and for working close to watercourses, using one disc to spread in-field and the full rate applied on the border spread.”
In the case of the DX30+, this machine is now ISOBUS compatible, giving it the same connectivity functions as the X40/50+ models.
Amazone, too, has been hyperactive in pushing forward the frontiers of spreading technology recently. While its WindControl facility has, deservedly, attracted a great deal of interest, progress is clearly being made in other areas, too.
Not least of these is the company’s new generation ZG-TS 01 trailed spreader, which incorporates the latest ProfisPro weighing technology and TS spreading unit. An interesting aspect of this model is the hybrid drive system in which the floor belt and steering are powered and controlled hydraulically.
So as to allow the machine to be drawn by smaller tractors, a choice of two drive systems is offered – the conventional tractor-based load-sensing hydraulic system or the new hybrid. In the latter, around two-thirds of the of the oil capacity of the tractor’s load-sensing system is used in conjunction with a twin-pump pressure balancing set-up. The remaining third is generated via the on-board hydraulic system on the spreader.
The outcome is completed by the presence of a hydraulic pump on the spreader which is driven directly by the tractor’s PTO shaft. This hybrid composition – as well as allowing smaller tractors to do the job – is, Amazone says, considerably cheaper than conventional on-board hydraulic systems.
Turning to the ProfisPro weighing system, the ZG-TS is the first trailed spreader model to have the ability to utilise this technology enabling on-line calibration and fill level management, together with regulation of the combination’s braking force. Under the fill level heading, the system calculates the refill quantity required to complete the remaining field area and the optimum load distribution – not a secondary consideration when a 10,000-litre hopper and often heavy fertiliser types are involved.
A few months ago, at Agritechnica, Amazone introduced the FlowCheck system for monitoring the spreading apertures on its ZA-TS mounted spreader and alert the occurrence of blockages which may have been caused by foreign objects or encrusted lumps of fertiliser, before they can cause a stoppage of the operation.
FlowCheck is a constant monitor of each aperture for blockages and also signals if the spreading unit is running empty. The flow pressure within the spreading disc motors is measured constantly by sensors located within the hydraulic system and if this changes – due to a blockage – and the rate of application is affected, an alarm signal is sent to the operator via the cab terminal.
To end this look at the latest technology being developed for fertiliser spreaders, the last words come from Natalie Wood, who works as a crop nutrition agronomist with Yara UK. Recognising that application machinery and software has improved significantly in recent years – in terms of wider bout widths and greater accuracy, in particular – she stresses that the quality of the product being applied is paramount.
“Progress has certainly been made, but as the hardware continues to improve there are still issues with software compatibility and data transfer with real-time precision technology systems,” she states. “All we urge is that when farmers are looking at purchasing new equipment they bear in mind variable nitrogen applications and precision technology to optimise the return on their investment.”