Pre-production models of the Claas Lexion 8000 series hybrid combines, due to go on sale for 2020, have been working in a number of countries this harvest. CPM visited the owner and operator of one of the two flagship 8900 machines here in the UK.
It’s the internal upgrades that aren’t so visible that have made the biggest difference.
By Martin Rickatson
There’s a relaxed look on Andrew Tetlow’s face as he watches the new, thinly-disguised Lexion 8900 open up a new field of oats. This is in spite of the fact that summer 2019 has been giving him a particularly catchy harvest, and he and his business partners have chosen this harvest to commit to a machine as yet unproven in the marketplace.
But the potential for risks as well as rewards in taking on a manufacturer’s pre-series machine, built for final testing and tweaking before production commences, doesn’t seem to faze Essex multi-farm partnership AWT Farm Services.
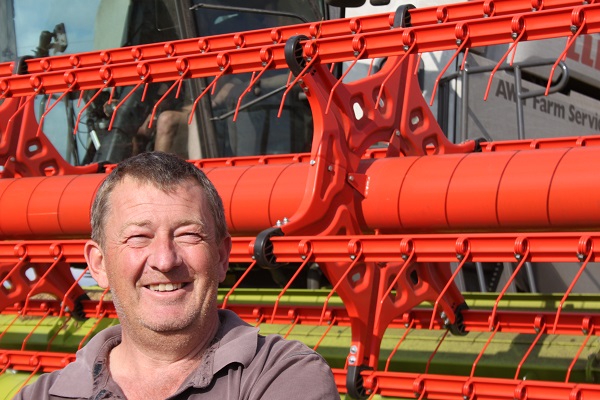
The reward outweighs the risk when agreeing to take on a pre-production combine offering greater performance, reckons Andrew Tetlow.
That’s perhaps because this isn’t the first time Andrew and his co-directors have agreed to help Claas with the final pre-production tests before a new combine range is launched. Since the development of the 500 series Lexions and the 580+ range-topper back in the early 2000s, AWT has, every few years, worked with the manufacturer, taking on a pre-series flagship each time new or updated models have been in their final phase of development.
“Being one of the first to take on a new machine does involve some risk,” acknowledges Andrew, who with his business partners uses a pair of combines to cut 2040ha of combinable crops grown across four partner and two associate farms and further contract-farmed land in the west Essex/Cambs/Suffolk area.
“But we’re at the end of the development chain of the maker’s own prototyping and product development, so we’re not working with untried components. And the rewards, in terms of enabling us to see where we can go next, particularly with greater capacity and the benefits that brings, are significant.”
Beyond the desire to make the most of each good weather window and minimise the need for drying, one of the key reasons greater capacity is so important to the business is its key cropping types. Wheats are predominantly Group 1, meaning a race to cut before rainfall can hit Hagbergs. Meanwhile, although AWT’s land lies in one of the most high-pressure UK regions for flea beetle, oilseed rape remains the primary favoured break crop, meaning sufficient cereal ground must be cleared quickly enough to allow OSR establishment to get underway as early as possible.
“While we’ve had to broaden our cropping mix, its potential margins and agronomic advantages mean OSR is still our favoured key break crop, but the pressure here means it must be established early for the best chance against flea beetle. For some time now we’ve been beginning OSR drilling in early Aug, with the aim of finishing by the middle of the month, so we need wheat land cleared promptly.”
This is the fifth time in a decade the business has worked with Claas to help with final pre-series testing of a new combine. Every three years AWT replaces one of the two machines it operates, tending to run one of each of the largest narrow-body and the largest wide-body of the two Lexion hybrid sub-ranges offered by Claas. With the maker and its UK arm prepared to provide enhanced service to assure reliability of and support for pre-production machines, in exchange for access to them and feedback on their performance, the risks of taking on a pre-production machine are minimal, believes Andrew, while the rewards of early access to a combine with greater potential are considerable.
“It doesn’t look that different externally to the Lexion 780 it replaced, save for its bigger grain tank extensions and new 13.8m Vario cutterbar instead of the 12m version we had. But it’s the internal upgrades that aren’t so visible, to areas like the engine and the threshing and separation systems, that have made probably the biggest difference to the 8900’s capacity. In wheat, you definitely need to run rather than walk to follow it on foot.
“Normally we’d replace one of our two combines every three years, but we knew the Lexion 8000 series was coming, so held on to our 780 for a couple more seasons until it was launched. Claas kept us informed and we agreed to again take on a pre-production model of the top-of-the-range machine when it was ready, which ultimately was in time for harvest 2019.
“Once it arrived, we knew we would all be learning – the Claas service staff plus us and our operators. But with the extra capacity it offers, and our Lexion 760 remaining with the business, we weren’t pushed, and 60% of our wheat was cut by mid-Aug. When we were running Lexion 580 and 600 models on this acreage 10-15 years ago, and oil prices – and hence drying costs – were lower, we were cutting cereals at up to 25% moisture. Now we tend not to cut at above 20%, and greater capacity gives us more flexibility to wait.”
Most of the business’ 2019 wheat lies on lighter, lower-yielding ground, so by mid-Aug when land destined for OSR had been cleared, there had been relatively few opportunities to really test the limits of the 790hp, 13.8m cut, 16,000-litre tank capacity Lexion 8900 in a thick crop. And with a high proportion of straw being left for baling by a local power station-supplying contractor, there had barely been a chance to push the combine while cutting and chopping.
“Heavy wheat crops will be the real test, but even in thinner ones its performance has been remarkable,” says Andrew.
“But where we haven’t been swathing it has produced a brilliant chop and spread, much improved over that from the 780, especially in unripe, brackled winter barley straw. The new chopper distribution design, which produces a much smoother, more positive side-to-side action than the jerkier fishtailing movement of the old type, is brilliant at dusting the material really evenly across the whole cut, and should be more robust. And the chaff spreader is also much improved in the way it distributes material through the chopper units across the whole cutting width.
“Depending on the field and the crop, it’s giving us an extra 15-20% hourly output, and our trailer drivers – we don’t see any advantage in a chaser bin, given the cost of it and associated lorries – have to be swift to keep up. We run three HM 16t models, and often the combines are running separately, so on land close to one of our farm bases we may be using one combine supported by one tractor and trailer.
“The new unloading system, which can empty the 16,000-litre tank in under two minutes, really makes a difference here, although there have been some pre-production teething troubles with it. Even at the half-speed setting for topping off a load, it really chucks the grain out,” continues Andrew.
“We give students harvest opportunities, and it’s tested this year’s combine and tractor/trailer operators quite a bit, particularly in oats if the wind has been strong. The trailers also need to be quick to get back to the combine, and we have been waiting at times, but safety is our priority, and with this capacity we aren’t pushed.”
Andrew ensures all grain trailers, which are new every year, are fully safety-compliant regarding air-brakes and equipped with ABS. Grain is stored at the local Camgrain store, where AWT members have over 13,000t of committed storage space. “At harvest we’re simply trying to get crops off the land as quickly as possible and either straight to the store or temporarily into on-farm storage.”
On a long day he reckons refuelling is necessary a little sooner than previously, but this is more than compensated for by considerably higher outputs. “There’s a new stepped power-output system, inherited from the Claas Jaguar forage harvesters, which adjusts fuelling to workload. This makes a positive difference to the way the machine uses fuel depending on what’s going through it.”
Day to day management of the business is conducted by Andrew and business partner Anthony Wiseman and just two full-time staff, but two further workers are recruited for harvest. This year one of those, Ben Latham, was entrusted with piloting the new pre-production Lexion 8900. Having spent his first combining season last year on the AWT’s 780, he has been in a good position alongside Andrew Tetlow to compare the two machines.
“It looks pretty similar from outside – and it carried 780 stickers this year to hide the fact that underneath it was a new 8900,” says Ben. “The day’s operator course I went on at Claas UK made it easier to understand what’s different inside the machine. This includes the bigger drum that runs at lower speed, the APS Synflow threshing changes and, in the cab, the new CEBIS terminal.
“I’ve only been combine-driving for a year, and at first I was a bit apprehensive, but it didn’t take long to get used to the 8900 after last year’s 780. Many controls, such as the joystick, are the same, but the new CEBIS screen makes it easy to find the best settings for a crop – just tapping on the screen brings up everything needed,” he explains.
“I use the standard stored settings and then fine tune them if I can, but generally don’t need to do much. The CEMOS Automatic system, as I had on the 780, then automatically adjusts them to what I ask it to do, in terms of throughput and losses. With the grain quality camera constantly taking images and updating settings accordingly, the sample is notably cleaner on the new combine.
“The new CEBIS touchscreen is a bit slower to boot up than the old one, but the screen and its settings are more accessible and easier to work with, and the new dial and touchscreen combination means I can use either depending on what’s most convenient.
“The other key thing noticeable in the cab is how quiet it is. That’s not just in terms of the engine, but also when engaging the threshing and separation elements – the new engagement system makes much less noise.”
He also rates the improvements to the new Lexion’s engine cleaning system, designed to prevent dust and chaff build-up.
“The engine seems to stay a lot cleaner on top than the one on the old machine, while the engine air filter improvements are also handy, in that it requires cleaning only when a message appears on the CEBIS terminal. The idea of not cleaning it daily was odd at first, but it seems to work well – it saves time and we’ve not had any problems. We needed to clean it probably only once a week during the early part of wheat harvest.”
In capacity terms, Ben believes the 8900’s additional power – from a 790hp MAN engine versus a 626hp Mercedes – and extra grain tank capacity – 16,000 litres versus 13,500 litres – have made a big difference to efficiency.
“I have more power to push the combine in heavier crops, and obviously I’m emptying less often, although I can still be waiting for trailers at times. The capacity difference has been really noticeable when working the 8900 and our other combine, the 10.5m Lexion 760, together. I’ve been able to push on slightly faster even with the additional 3.3m cut, or 1.5m extra compared to our old 780‘s 12.3m unit. That 15% greater header width makes a noticeable difference in reducing field passes.”
Beyond the machine’s controls and capabilities, Ben rates features such as the new fan installed on the top of the feeder house/elevator.
“It’s especially good in barley, where it stops awns collecting on top of the elevator, although the downside is there can be more dust in the air in front of the windscreen.
“Although we’ve had some teething troubles with the high unloading speed, the trailer drivers and I have found it OK to work with when it has been operating OK. It can need shutting off quickly with an inexperienced trailer driver, though. A 16t trailer takes a full tank and a top-up, and the fact the auger comes further forward does make viewing easier.”
While prices for the new model and its siblings are to be confirmed, Andrew Tetlow reckons combine capacity is a worthwhile investment when compared with the alternative cost of additional combines, drying costs and extra labour, as well as potential loss of milling premiums and late OSR establishment.
“Good labour is becoming harder to find and more expensive. Considering what a machine like this can do for us, I reckon the investment, and the risk, are worth the reward.”
Farm Facts
AWT Farm Services, Saffron Walden, Essex
- Area farmed: 2040ha
- Soil type: Heavy clay to lighter clay loam
- Cropping: Winter milling and ‘clean’ food-grade wheat, winter barley, spring malting barley, winter oilseed rape, spring oats
- Tractors: AGCO Challenger MT875C and MT875E, 2x JCB Fastrac 4220
- Cultivation equipment: 12m Farmet Fantom cultivator, 7m Great Plains SL700, 6m Keeble Brothers subsoiler, 6m Horsch Terrano12.25m Väderstad Carrier
- Drill: 12m Horsch Sprinter 12SW seed/fertiliser, 6m Horsch Sprinter
- Sprayer: 36m Challenger RG655D plus Homberg Handler IV mixer tank/bowser
- Fertiliser spreader: Trailed 36m KRM Bredal F10
- Combines: 13.8m Claas Lexion 8900 and 10.5m Claas Lexion 760
- Handlers: 2x Claas Scorpion 9055
- Trailers: 3x HM 16t capacity (hired)