One North-East farmer has set his stall by consistently producing high-quality milling wheat. CPM looks at one of the drills he believes makes it possible.
It’s a real acre-eater.
By Emily Padfield
The key with any business is to identify and supply what the market wants. That seems a logical statement, but sometimes with farming you have to take a step back and reacquaint yourself with that concept, rather than keep your head down and carry on regardless.
Stephen Craggs, based in County Durham, has made a name for the 800ha East Close Farm,
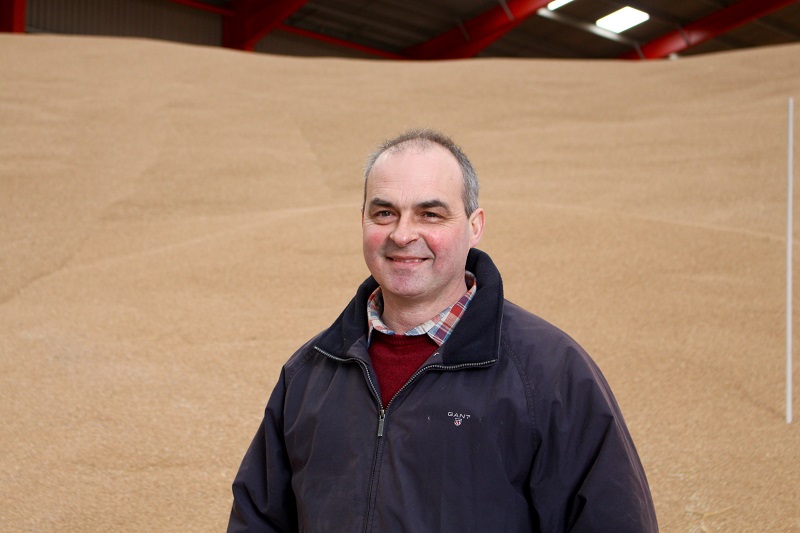
Stephen Craggs, based in County Durham, has made a name for the 800ha East Close Farm, Sedgefield by consistently producing high-quality milling wheat for the likes of ADM, Warburtons, Hovis and Jacobs through Bradshaws of Driffield.
Sedgefield by consistently producing high-quality milling wheat for the likes of ADM, Warburtons, Hovis and Jacobs through Bradshaws of Driffield.
He farms alongside father Ray and brother Ian, took first prize in the nabim Milling Challenge in 2013 – the first and only time he has entered the competition.
“I decided to enter the competition in 2013 as it had been a particularly difficult year but despite that, our wheat had stood up as well as always.” Growing wheat to such a high quality year-after-year isn’t easy, he notes, particularly in an area like County Durham where you get cold winds and sea fog, while being in the shadow of the Pennines make for hardly the most temperate of growing conditions.
Continuous wheat
The farm, before the three-crop rule, had been under continuous milling wheat for the past 15 or so years, explains Stephen Craggs. “Now, we’ve adapted to include spring wheat and HEAR oilseed rape,” he says.
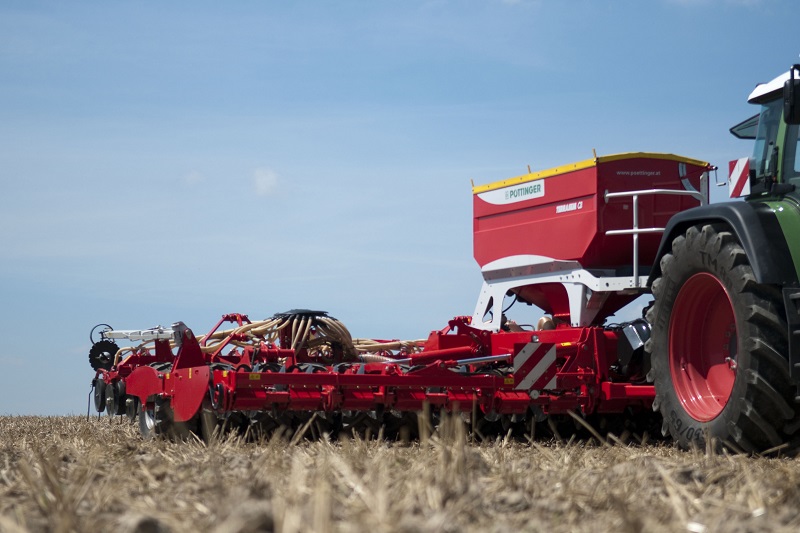
Although Stephen Craggs uses his C8 on ploughed ground, the drill can operate on worked stubbles, with the discs designed to handle a lot of trash.
Traditionally, milling wheat varieties grown include Solstice and Crusoe, however new variety Skyfall is also grown. “First signs look promising and bakers have been testing samples to see how it performs during processing.”
Land destined for spring wheat production is ploughed after combining and left for the frosts to weather it over the winter before drilling in the spring. For the past few years, the variety of choice has been Tybalt.
Yields regularly exceed 10t/ha, which is a pretty average base yield to aim for, believes Stephen Craggs. “With the three-crop rule bringing break crops back into our rotation we’ve now lost our take-all advantage. With our damper climate there can sometimes be root problems and we’ve had to readjust accordingly,” he adds.
All ground is ploughed behind the combine (a New Holland T1090 on tracks with 10.6m header), while nearly all the straw is chopped to return the nutrients to the ground. “Up here, it never dries out too much so we never worry about turning all the soil over we can.”
Although soil type varies across the farm, it’s mostly heavy clay loam, and because of its high magnesium content, ground can solidify if left untouched, explains Stephen Craggs. “Ploughing opens up the ground and lets the air get at it. We also apply a lot of calcium lime, usually in the form of Limex from the sugar beet factory in Newark. When it used to be at York it was a lot nearer,” he adds.
Sometimes quarried lime is used, but Stephen Craggs believes Limex is a good all-round product. This is done roughly once every five years, and with OSR now included in the rotation it’s done before to result in the spike in pH that OSR craves. SGS soil samples are taken every three years.
With everything being ploughed after the combine, the farm runs two ploughs: a 10f Naud and a 12f Gregoire Besson.
Two Challengers, a 765 and 865, deal with ploughing while two Fendts, a 930 and 936 are tasked with power-harrowing, carried out straight after ploughing in the autumn. Three 6m Kuhns mean land can be covered quickly and efficiently when required. “Even when ground gets sticky, power-harrows still work on our ground,” he explains. Whether the land gets a second pass with the power-harrow largely depends on the sort of year it’s been, but most goes after a single pass.”
The crop is then established with an 8m Pöttinger Terrasem. “The plan is always to start with the Pöttinger and carry on as far as we can manage,” maintains Stephen Craggs.
“It’s a real acre-eater and you soon blitz 1000 acres. As long as you have a fair bit covered it takes some of the pressure off,” he adds. “I like a lot of land ploughed going into winter, as then I know it’ll take a lot of rain.” If land does get too wet, a Kuhn combination drill comes into play.
After looking at a lot of other drills, what Stephen Craggs liked initially about the Pöttinger Terrasem disc drill was its clean lines. “You try getting your foot into one of the other makes and you just can’t. With the C8 it’s less-complicated, free flowing and you can get your whole boot in easily. It’s also a strong, no-nonsense piece of equipment and is extremely well-made.”
The Terrasem range of trailed seed drills comes in 3m to 9m working widths, and the Craggs opted for an 8m version three years ago to fit with their existing system. These larger folding models have the same components as the fixed models, but have been designed to move vertically to adapt to ground contours over the width of the machine, maintaining equal contact and ground pressure across the working width. Folding sections are pre-loaded with nitrogen accumulators to provide equal pressure in any working position.
Instead of a separate chassis, the Terrasem adopts a combined packing and chassis concept, meaning not only the weight can be used effectively but also the length of the machine can be kept at a minimum for manoeuvrability and stability on undulating terrain.
When on the road, the side sections are folded up to give a transport width of 3m and the two wheels in the middle are raised to improve stability.
“Weight is carried on four wheels – two behind each wheel track – putting more weight onto these tyres and making it ultimately far safer when moving on the road, which I think is really clever.”
Stephen Craggs’ model is specced with hydraulic brakes allowing transport on the road at 40km/h legally.
The combined packer and wheel unit is located between the disc harrow and seed drill sections of the machine. The tyre packer itself is made up of 425/55 R17 tyres, each of which has its own individual suspension system and packs four seed rows at a time. The cleat design and flexing properties of the tyres means they’re largely self-cleaning, something Stephen Craggs is really pleased with.
Offset configuration
“The staggered, large diameter wheels keep turning even when it’s sticky,” he reckons. “And the offset configuration also makes the packer easier to pull with the cleats on the tyres running with the tractor rather than fighting against it. You do have to keep the wheels turning, after all it’s in excess of 10t and you would get in a pickle fast if you were to stop when it’s too wet.”
The drill is supported by all 16 wheels at the headland, as the chassis always remains in the same position – only the disc harrow and coulter rails are lifted.
Ultimately, as with any ideal drilling scenario, the aim is to create a level seedbed with fine soil at seed level. Although all ground is ploughed and power-harrowed at East Close Farm, the two-gang disc harrow still has its work cut out on what can sometimes be heavy soil with tough, bouldery areas.
The 510mm discs are mounted on a heavy-duty square cross-section tube with four rubber grommets allowing the discs to avoid stones and rocks and there are two discs per arm. The bearing is permanently lubricated while a metal cover encases the labyrinth seal to protect it from damage and dust.
Each gang has infinitely variable hydraulic depth adjustment and can be controlled independently of each other. Spring mounted edging plates are standard so as to prevent any soil moving outside the working width. If necessary, a levelling board can be fitted between the disc harrow and the tyre packer, says the company.
The C8 has an easy-to-fill oblong 5100-litre seed tank with roller tarpaulin cover to make it dust and watertight. A loading platform makes it easy to open the tank cover and check filling process, however Stephen Craggs does say that there could be another platform to make access easier to the metering unit as at the moment it means clambering over the discs.
The Terrasem’s metering system can handle seed rates of from 0.6-350kg/ha and the hopper has a clever built-in level monitoring system.
“The feature I really like is the laser tank-level monitor system, which gives you an accurate count down of exactly how much seed you have in the tank. It’s like having a digital sight glass and takes away the need to guess whether you can get to the end of the bout or not, or even how many bouts you can manage exactly.”
Dual disc coulters, each mounted on an independent parallelogram meaning they follow ground contours, are guided by a pressure wheel to ensure uniform seed-placement depth. This depth is adjusted mechanically from a central point, but coulter pressure is applied hydraulically from the cab and can be anything from 40kg to 120kg, depending on the conditions.
“The on-the-move pressure control is a really good feature which allows us to alter the pressure within a field. For example, you can drill a whole field at one pressure, and then on the headland where it might be sticky you can ease the pressure off so you can scoot across the troublesome areas without bulldozing the soil.”
This also stands for the tougher, cloddier areas with really big boulders he adds. “If you take the pressure off it just flows through but still drills uniformly, and the weight is really well spread across the tyres. I’m happy with the coulter pressure range, it’s been more than enough for our conditions.”
Because the folding C8 has a three-frame design, which allows for vertical freedom of movement of up to 5°, ground tracking is provided across the whole working width, according to Pöttinger. Added to this, by mounting the coulter units to the back of the press-wheel frame by three-point linkage, each is free to follow the ground contours.
The C8 has two electrically driven metering systems controlled by radar sensor and seed rate can be controlled from the cab. The blower is driven hydraulically producing a large volume of air at low velocity, meaning seed is protected against damage and seed dressing is preserved and there’s less noise than some other drills, adds Stephen Craggs.
Two distributer heads are fed by riser tubes that feed seed uniformly via the air stream to each of the separate seed outlets. Standard row spacings are 125mm while there are distributer inserts available for those wanting larger row spacings. “For a disc drill, these spacings are quite close but at the moment we’ve found them to be fine. We can get blanking plates should we wish in the future.”
The tramline system closes either three or five seed-lines per track with any excess seed being returned to the riser tube and seed rate being reduced accordingly.
“The tramline indicators could be a bit bigger to make them easier to see from the cab and an annoying feature is the tramline marker control. I would prefer it on a separate spool as there’s no way of stopping the sequence, for example if the next row had a telegraph pole to deal with you need to start the whole sequence again. It would only need to be on a separate spool and this would solve it.”
According to Pöttinger, it’s now possible to work them independently whilst in work, which overcomes this issue.
When it comes to starting the next season, it only takes about half an hour to reacquaint yourself with the settings and features, says Stephen Craggs.
He opted for a separate screen rather than using the ISOBUS on the tractor, partly because of second-hand value when he comes to sell the drill and also he finds the push-button screen simple and easy to use. He also opted for the Artis screen rather than Artis+, meaning functions are controlled via tractor hydraulic spools rather than electro-hydraulically using one remote.