Though predominantly favoured by those with livestock to feed, forage harvesters are becoming increasingly important for the arable sector — particularly for those involved with growing for AD. CPM takes a look under the hood of Claas’ latest update.
The flagship model will be the first time Claas has launched a machine with over 900hp.
By Charlotte Cunningham
Much like a jaguar in the wild would tentatively move through the jungle and stalk its prey, a brand-new Claas Jaguar 970 forage harvester lines up ready to make its way through a ripened crop of maize.
It’s a stunning September morning in Suffolk and as product manager, Dean Cottey, waits for the trailer to arrive, he talks through some of the driving forces behind the newest additions to Claas’ fleet of forage harvesters. “The 900 series has been around for some time, but as of next year, Claas will be phasing out its existing models and replacing them with the new series,” he explains. “The range encompasses all of our farmer feedback, so we hope that this will tick all the boxes for a lot of growers.”
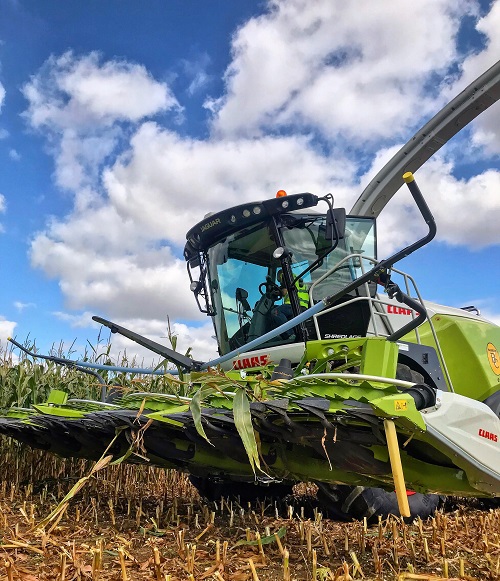
Claas has introduced a 42-blade option, and the main reason for this is for biogas throughput.
Of course, for the majority of arable farmers, a forage harvester has not traditionally been a must-have when it comes to purchasing kit. However, with an increasing number of producers now growing maize — particularly for AD plants — and more and more people including grass as part of their rotation, the forage harvester is rapidly cementing its place in the sector.
So how exactly does the new range differ from its predecessor and how could an arable farmer make use of the latest launch?
For those supplying AD plants, chop quality is an incredibly important variable to manage.
When asked what single feature would make an arable farmer part with hard-earned cash and invest in the new Jaguar, Dean’s answer is instantly — without hesitation — the chop quality. “A new option on the 990, 980 and 970 models is the 42-blade V-Max chopping cylinder, which can provide farmers with a cutting frequency of 25,200 cuts per minute.
“Previously we had 20, 24, 28 and 38 blade offers, now we’ve moved to a 42-blade option, and the main reason for this is for biogas throughput,” he explains. “When you want to cut maize or rye incredibly short, the feed rollers on the forager have to run very slowly to achieve that.”
However, the new system enables users to work through a chop length range of between 3.5mm and 14.5mm at a consistent quality, without compromising crop flow, adds Dean. “By putting more blades on the cylinder, the cutting frequency is considerably higher, so it picks the feed roller speed up.
“Where a longer chop length is required in grass, the chopping cylinder can be run with just 14 blades fitted, so it really is an all-rounder.”
Updates have also been made to the feed-roller housing. “We’ve redesigned things and put a more heavy-duty spin on the 900-series by reinforcing the feed roller, with the aim of providing maximum operation reliability,” explains Dean.
As well as a new roller, the housing also now features larger wear plates on the sides of the pre-compression rollers to reduce dirt and noise, while maintenance has been made easier by the use of clamps to secure the rollers, he adds.
A new hydraulic pre-compression system will now also come as standard across the range. “It has a major advantage over springs. With a spring system, the pre-compression load increases with the volume of crop that passes through the feed rollers. But a hydraulic system applies a uniform load, regardless of feed volume,” explains Dean.
“In terms of the advantage to the farmer, it means a thin crop receives the same compression as a very heavy crop. For biogas growers, the big advantage of this is chop consistency.”
With extreme weather patterns becoming the norm — putting increased pressure on growers to harvest a crop in a potentially very tight window — having a powerful machine on hand for when you do get going can make a huge difference, he adds. “At the top of the range is the 990, powered by a 925hp MAN engine, while the lower end of the series sits at 462hp.
“The flagship model will be the first time Claas has launched a machine with over 900hp.”
For 2020, all Jaguar 900 machines will make the move to the Tier 5 engines, developing more power and providing an increase in torque, says Dean. “Across most of the range, we’re sticking with our Mercedes engine that we’ve used for many years, but what we have done is change the exhaust system in line with Tier 5 emission requirements.”
However, the 970,980 and 990 models have had more of a change. In the past, the previous 970 used a Tier 2 MAN V8 engine — now it’s Tier 5 — so it’s made quite a big jump in terms of emission standard, but also benefits from a new engine, he explains. “Instead of using the old-style V configuration, the 970 model now has a new straight 6 big block engine.
“The engine itself comprises six cylinders — at almost the same capacity as we had in the past — but uses common rail injectors, something that we didn’t really have before, and also now use AdBlue to try and get them to Stage 5.”
So how does the customer benefit from the engine’s configuration change? “The big advantages for a customer going from a V8 to a straight 6 is that it is a lot lighter, so you’re not having to pull around as much deadweight,” explains Dean. “It’s also much more efficient. The former engine was very old — relying on new exhaust technology to bring it up to standard — but this is a nice, clean design. This makes it very efficient in terms of how much horsepower it can generate with very little fuel going into it.”
While the new pistons and valve technology have a role to play in this, Dean also attributes the improved efficiency to the displacement per cylinder, which gives very high torque at low engine speed. “This particular forager — the 970 — is fitted with a new MAN D4276 Straight 6, which develops 790hp from its displacement of 16 litres,” he explains. “With a displacement of three litres per cylinder, this means the 970 boasts a stable power curve with sustained torque, putting it at the top of its class in regards to fuel consumption per tonne of harvested material.”
And what about usable torque? “With the older machine — the V8 – the max torque was 1500 Nm, and only at that one point. So it used to build up on a dynograph to a point and then tail off,” explains Dean. “The new machine has more torque (3400 Nm) but a much wider operating range — between 1600 and 1350rpm.
“So typically where you want the machine to be running is ever so slightly higher than that — you probably want to run at about 1700rpm — then when you hit a lump or tough conditions, it then has that very flat, long torque curve to hang on to and keep itself going until it gets out of those conditions.”
While today’s harvesting has run smoothly, without any glitches, a machine is only profitable when it’s running, so minimising downtime has been a key part of the design process within the new 900-series, explains Dean. “A lot of customers now are running big machines and trying to do more work, but are obviously putting more hours on the clock. On the new Jaguars, the service interval is 1000hrs, enabling farmers to make it right the way through the season without experiencing a drop in oils.”
As we work our way down the field, Dean points out the new touch screen CEBIS terminal which now comes as standard across the 900-series range, designed to improve accessibility to machine functions. “Depending on individual preference, the forager operator has four options for setting up and adjusting the Jaguar,” explains Dean. “These include using the touch screen and new CEBIS terminal, the CMotion control lever, which is now standard on all machines, the CEBIS rotary switch and push button, or via direct adjustment via the switches in the armrest.”
The CMotion control lever has been introduced directly on the back of farmer feedback, explains Dean. “A big benefit for operators when using the new armrest and CMotion control lever is that it will be possible to adjust the machine on the move from the joystick using the new ‘favourite’ settings options.
“One of the most requested things we had from our drivers was a function to easily move the spout up and down from the joystick,” he adds. “With the new favourites setting on the lever, the driver will input his most popular tasks, for example roller crop press or in this case, spout up and down.
“If the driver is making their way across the field and spots a powerline coming up, they can simply press the arrow to scroll to the favourite setting and then the toggle switch on the joystick will then move the spout up and down.”
Steering solutions
A neat feature on the 900-series is the availability of Dynamic Steering which means operators can reduce the number of turns to go from lock to lock. “At the moment, without the option, to go from hard left to hard right requires five revolutions,” explains Dean. “With Dynamic Steering the operator only needs one and a quarter turns of the wheel. This means that when manoeuvring from a corner of a field, it’s extremely easy and quick for the driver.”
The feature that gives it its name, ‘Dynamic Steering’, is the fact that the function changes with speed, adds Dean. “Imagine that you’re working within a field at less than 10km/h. One and a quarter turns are required to go from hard left to hard right, so you can turn easily on the headland, for example. Once the header’s down in the row and you’re getting faster, you don’t want to have that incredibly short turning of the steering wheel, purely for stability.”
So as you pick up speed, that ratio starts to increase from one and a quarter to five turns of the wheel from left to right. “If you’re working at 20km/h, turning at that kind of speed could give you a bit of a fright,” he laughs.
Additive advantages
With additives playing an incredibly important role in forage quality, Claas has introduced the new Actisiler 37 additive tank. “Capable of applying a precise dosage from 0.2-20 l/ha, the Actisiler 37 features a double-wall tank to protect the silage additive concentrate from high outside temperatures, keeping the additive cool to ensure it works effectively,” explains Dean.
“The new system also has a built-in flushing feature to clean the additive out once finished to reduce contamination of different types of material.”
As an option, dry matter content value can also be determined using a near infrared sensor (NIR), which can then be used as a reference for setting the chop length and the amount of additive required, he adds.
The spec – The 2020 Jaguar 900-series