Whether you prefer liquid or solid, dribbled or spread, there are many options out there for growers when it comes to investing in muck and slurry kit. CPM takes a look at some of the latest innovations.
By optimising digestate, you can reduce the requirement for other fertilisers and apply it right up to flag leaf.
By Charlotte Cunningham
Long gone are the days of clunky muck spreaders inefficiently placing clods of muck around the field. Instead, replaced by high-tech precision kit that can help farmers accelerate crop growth while keeping operations as cost-effective and precise as possible.
So what exactly is out there? And, how can growers make use of the latest innovation to maximise their muck and slurry spreading?
Vogelsang
Drawing its name from is beak-like shape, the new BlackBird trailing shoe linkage is set to be officially launched by Vogelsand GmbH at this year’s Agritechnica. “When it came to developing this new technology, we took into account the findings from our flow simulations as well as the flow rates of the liquid manure and tested a number of different shapes. The result is an ideal combination of a flow-optimized discharge that deposits the liquid manure even more precisely and a new skid geometry that separates the crops even better,” explains Henning Ahlers, head of sales, Vogelsang.
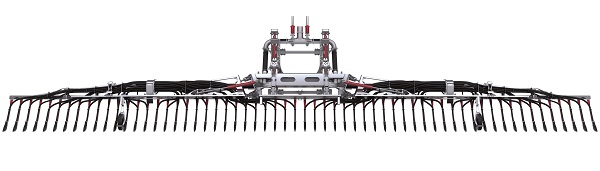
Available in working widths of 12m and 15m, the BlackBird trailing shoe linkage can be folded up to a transport width of 3m.
The new, long, beak-like shape helps to ensure a controlled and even flow of liquid manure through every discharge, preventing the crops from getting contaminated during manure spreading. By actively applying pressure, the BlackBird’s pointed skid is better able to penetrate the soil, ploughing a small furrow for directly depositing the liquid manure under the crops, adds Henning.
The new BlackBird incorporates the next generation of Vogelsang’s precision distributor – ExaCut ECQ.
The distributor is located in the center of the boom to ensure liquid manure is distributed precisely and evenly while large diameters and flow distribution plates keep the flow under control and ensure a high distribution accuracy, says Vogelsang.
With time often of the essence, the firm has added a large maintenance port to allow direct access to all the system’s internal components to make ‘tinkering under the hood’ quicker and easier, according to Henning. “As such, this means service work can now be carried out without dismantling the precision distributor or dismounting the cover and the outlet hoses and feed lines connected to it.”
The power requirements have also been reduced by up to 50%, thanks to a fresh rotor design and lower speeds, causing less strain on the cutter blades, he adds.
Hose layout has also been modified to prevent the unit from creating a V-shaped imprint at the start of its furrows and are installed for the first time in the new trailing shoe linkage.
As is standard procedure at Vogelsang, the BlackBird’s supporting structures are FEM calculated, adds Henning. “This ensures that the supporting structures can withstand the daily strains they are subjected to, guaranteeing a long service life of the linkage.”
Available in working widths of 12m and 15m, the trailing shoe linkage can be folded up to a transport width of 3m.
As well as the BlackBird, the German company is also set to launch its VX186GL gearless rotary lobe later this year – the first pump for the agricultural sector that has no synchroniser gearbox.
The company claims that the absence of a gearbox will make it run exceptionally smoothly, due to the four-wing lobes which are designed to work in conjunction with the two parallel connected hydraulic motors to deliver constant torques on both pump shafts.
“When used in today’s standard 30 m3 tank sizes, the gearless pump type in the VX Series offers a weight saving of around 100kg to 150kg – up to 55%,” explains Henning. “This allows the transport capacities of the vehicle to be increased or the vehicles to be driven with reduced ground pressure.
The compact construction of the rotary lobe pump makes installation on the vehicle easier and is straightforward to maintain, while the lighter lobes can also be installed individually as no fitting keys are required, he adds. “As there is no need for a gear oil change, this makes the rotary lobe pump low-maintenance, while also causing less wear to the lobes due to the lower shaft deflection.”
Vredo
With power and capacity entwined throughout its design process, the VT7028 from Vredo claims to be the new generation of Trac’s – setting a new standard in manure spreading. According to the firm, this comes largely down to the guts of the spreader – the Deutz 16-litre V8 engine with 687hp.
As well as this, the latest addition works in combination with Vredo’s own CVT and boasts a tank capacity of up to 32,000l.
Available in either dual or three-axle models, the VT7028 has load capacity at the front, back and on the chassis behind the cab.
The pump-slicer unit is positioned at the front of the machine, making for easy viewing from the cab. While the 12 l/min slurry pump – in combination with the 10 inch reloading arm – enables maximum capacity and flexibility under all circumstances, according to the manufacturer.
A slicing filter has been added in front of the pump to ensure all larger particulates in the slurry are chopped or separated from the liquid slurry in order to minimise damage to the pump and prevent the slurry injector hoses clogging up.
SlurryKat
Over in Ireland, demand has been increasing for dribble bar equipment – largely due to the looming threat of an all-out ban on splash plates. To satisfy this need, Irish firm – SlurryKat – have introduced an all-new 12m vertical folding dribble bar which can be tanker-mounted. Alternatively, it can be used on an existing umbilical system, coupled to the Bak Pak reeler, and capable of carrying up to 1000m of 12.7cm hose.
Sodimac
Launched earlier this year at SIMA, French firm Sodimac have added a new spreader its existing Rafal range.
Available in four single axle models and three dual axle versions, The Rafal Performer is a narrow body muck spreader, equipped with two horizontal beaters which work by teasing muck apart before spreading it with a pair of 1.1m discs.
The manufacturer claims good spread quality on widths up to 24m and boasts dose rates as low as 1t/ha can be applied.
Samsons Agro
Danish firm, Samsons Agro, is adding a completely new type of injector to its implement range ahead of the coming season.
The Samson Strip-Till has been designed with precision in mind, and is set to help growers ensure the efficient placing of slurry in row crops – reducing the amount of starter fertiliser needed and ensuring compliance with new phosphate rules in Denmark and Germany which set limits on P applications.
Available in two models, the Strip-Till 6 can be used on Samson’s PGII 18 and 20 tankers and has a 4.5m working width, while the 6m Strip-Till 8 is compatible with the tri-axle Samson tankers.
The Strip-Till is equipped with an integrated disc on a “soil to soil” front drum, cleaning wheel and a parabolic disc stand, which lifts up the soil and creates a V-shaped opening in the ground where the slurry nozzles place the slurry in two lines at a depth of 20-30 cm. The disc then closes the soil surface again.
“With our latest development, we can offer professional users an injector that ensures high capacity while maintaining high yields without mineral starter fertiliser,” explains Niels Haubjerg, product manager for slurry technology at Samson Agro.
Suitable for use in a variety of ground conditions – including ploughed soil or stubble field – the firm claims that the placing of slurry is always precise. “The injector itself has several different setting options and the parallelogram hitch ensures precise depth control for each row.
“This means the slurry is always placed at the preset height, the specially developed slurry nozzles can be adjusted easily and the placing of slurry lines can be adapted.”
The ability to carry out several operations in one injection will also no doubt have an environmental benefit and help to reduce associated emissions – something which is of particular interest at the moment as the IPCC report and Net Zero gathers traction in the media.
On-farm application – Charlie Baker
While a traditional fertiliser may be the product of choice for most farmers when it comes to applying nitrogen, Oxon farmer and contractor – Charlie Baker – has been making use of an alternative option.
Using a Vredo and Kaweco tanker combination, Charlie applies around 150,000m³ of digestate from anaerobic digester (AD) plants every year, varying between 25-30m³/ha. “By optimising digestate, you can reduce the requirement for other fertilisers and apply it right up to flag leaf,” he explains. “Digestate can be applied to stubble after combining, prior to seedbed preparation, for autumn and spring crops.
“As well as this, digestate can also be applied as a fertiliser for grass before and after silage cuts with a disc injector, or via a trailing shoe boom spreader onto the growing crops.”
The Vredo carries around 30t of digestate and spreads at a width of 36m through a dribble bar, while the Kaweco holds 24m³, spreading at 32m, explains Charlie. “Both work in the same way, just varying in capacity. All crops need feeding when they’re hungry, so it’s important you have the capacity to get the volumes on.”
As well as the increased precision aspect from applying digestate via a dribble bar, it also has an environmental impact. “Dribble bars are a low emission option to spreading,” he notes.
The boom applies digestate directly to the ground which is then readily absorbed by the roots of the crop. This not only ensures that the crop gets the nutrients it needs directly, but it also reduces the risk of run-off and leaching of nitrogen to the atmosphere..
Compared with other contracting work, liquid waste management is a job in itself, adds Charlie. “Logistics are probably the biggest headache, as transport can be a bit of an issue – a tanker is only efficient if you can get the product quickly enough to it.”
So what about cost? As a rough, ball-park figure, Charlie estimates a value of £3/m3 to spread the digestate and £3/m3 to transport to the tanker – totalling an overall cost of £6/m3 (dependent on the haulage distance). “We get a tremendous response from digestate,” he notes. “It’s a very available source of fertiliser and crops seem to respond well. I think there is still a lot of research to be done in terms of its value to crops, but from what I’ve seen – and the benefits we get – the response can be quicker than using granular fertiliser.”
Award-winning precision
Though not a brand-new piece of kit, the John Deere Manure Sensing HarvestLab 3000 could be worth another look after being officially recognised this year by the European Land and Soil Management Award jury as a major breakthrough in soil technology.
According to the firm, the Manure Sensing – which uses the HarvestLab 3000 sensor’s near-infrared (NIR) system to measure nutrient values during slurry application – provides farmers and contractors with the technology to enable more sustainable management of the nutrient cycle and to improve the efficiency of using manure as a fertiliser. The system prevents over or under-fertilisation by constantly measuring nutrient values during slurry application.
John Deere Manure Sensing allows users to apply N, P and K more precisely, based on a nutrient target and/or maximum application rate in kg/ha. These ingredients and the total volume applied are automatically and accurately documented, with the system also able to utilise site-specific prescription maps.
Speaking at the award ceremony earlier this year, Daniel Calleja Crespo, EC director for environment remarked: “It is exactly the kind of technology that the European Union wishes to promote and will inspire our policies for more sustainable agriculture.”