The purchase of two new combines has helped a Lincolnshire estate increase capacity and speed up harvesting in tight working windows. CPM finds out more.
There has been a significant jump in output over the competition.
By Charlotte Cunningham
Jaws dropped when John Deere announced the launch of its new X9 combine back in 2020. Not only because of the claim that the 1100 model had the capacity to achieve throughputs of 100t/hour, but also because of its hefty nine-figure price tag leaving many to wonder – is it really worth it?
Lincolnshire farm manager Matthew Wallace believes the answer is yes – having recently invested in two of the 1000 models from the X9 range.
Matthew is manager of the Buckminster Estate, based near Grantham, a business which has a simple goal: to produce food profitably while managing the land in a way which lends itself to benefit and enhance wildlife and the wider environment.
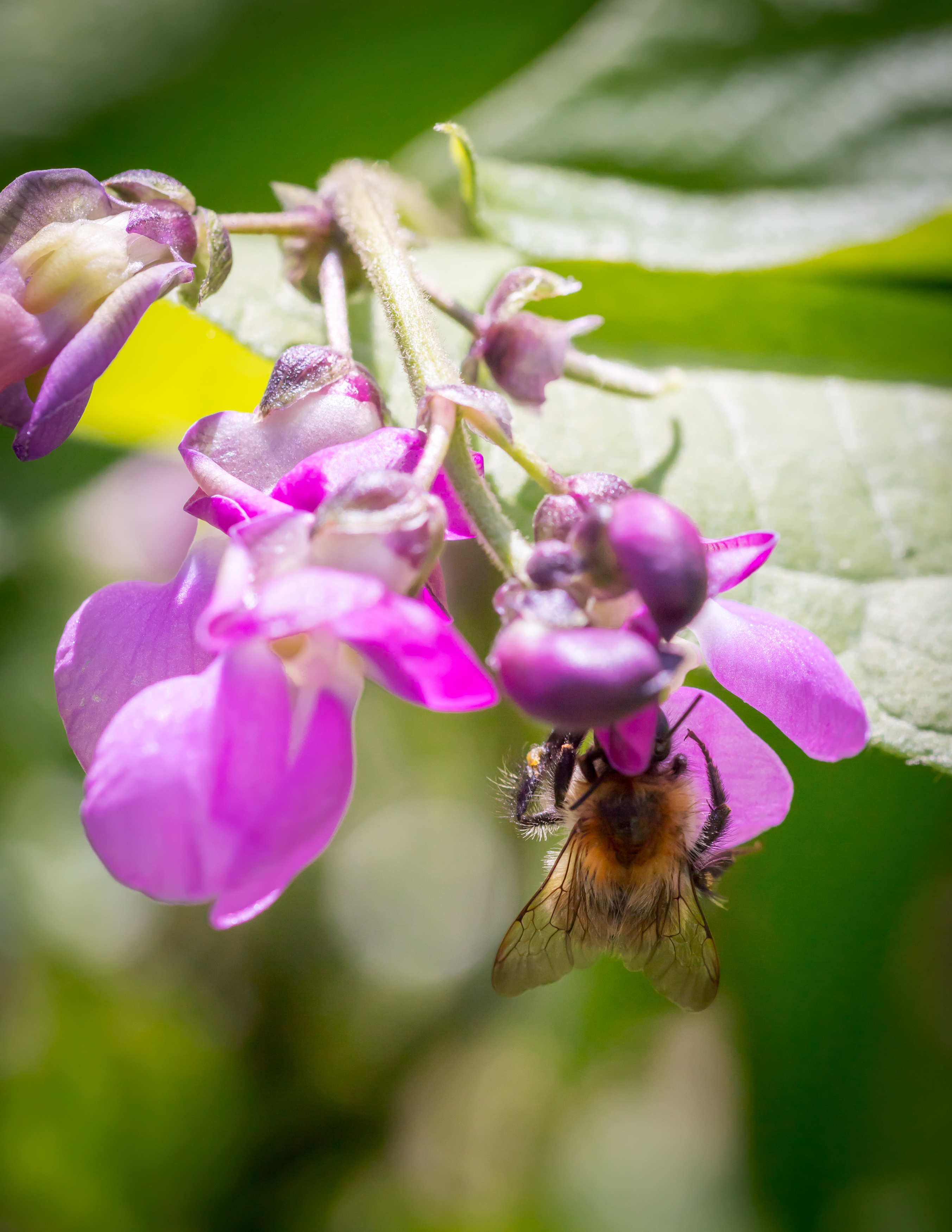
Buckminster’s goal is to produce food profitably while managing the land in a way which lends itself to benefit and enhance wildlife and the wider environment.
From a food production perspective, the land is largely put to arable cropping and incorporates a wide range of crops across a varied rotation. “We try to widen the rotation as much as possible and include a mixture of both winter and spring crops,” explains Matthew. “This includes winter wheat, winter barley, winter linseed, winter beans and winter rye as well as spring oats, barley and wheat.
“On some of the lighter land we’re also growing sugar beet and we’ve now brought grassland into the rotation. We try to maximise our acreage of first wheat as much as possible, so having variety helps us to set ourselves up a bit for that.”
A focus on improving soil structure means crops are now established via minimum tillage, and cover crops are also grown for their soil structuring benefits. Grass and wildflower margins have been planted to provide habitats and a food source for wildlife.
Environmental stewardship is also a new avenue the estate is pursuing. “We’ve embraced Mid-Tier stewardship and are in our first year of running that,” explains Matthew. “This will allow us to make better use of some of the less productive areas, rather than cropping them. In turn, this means we grow better crops in the areas that are more likely to bring a return on investment.”
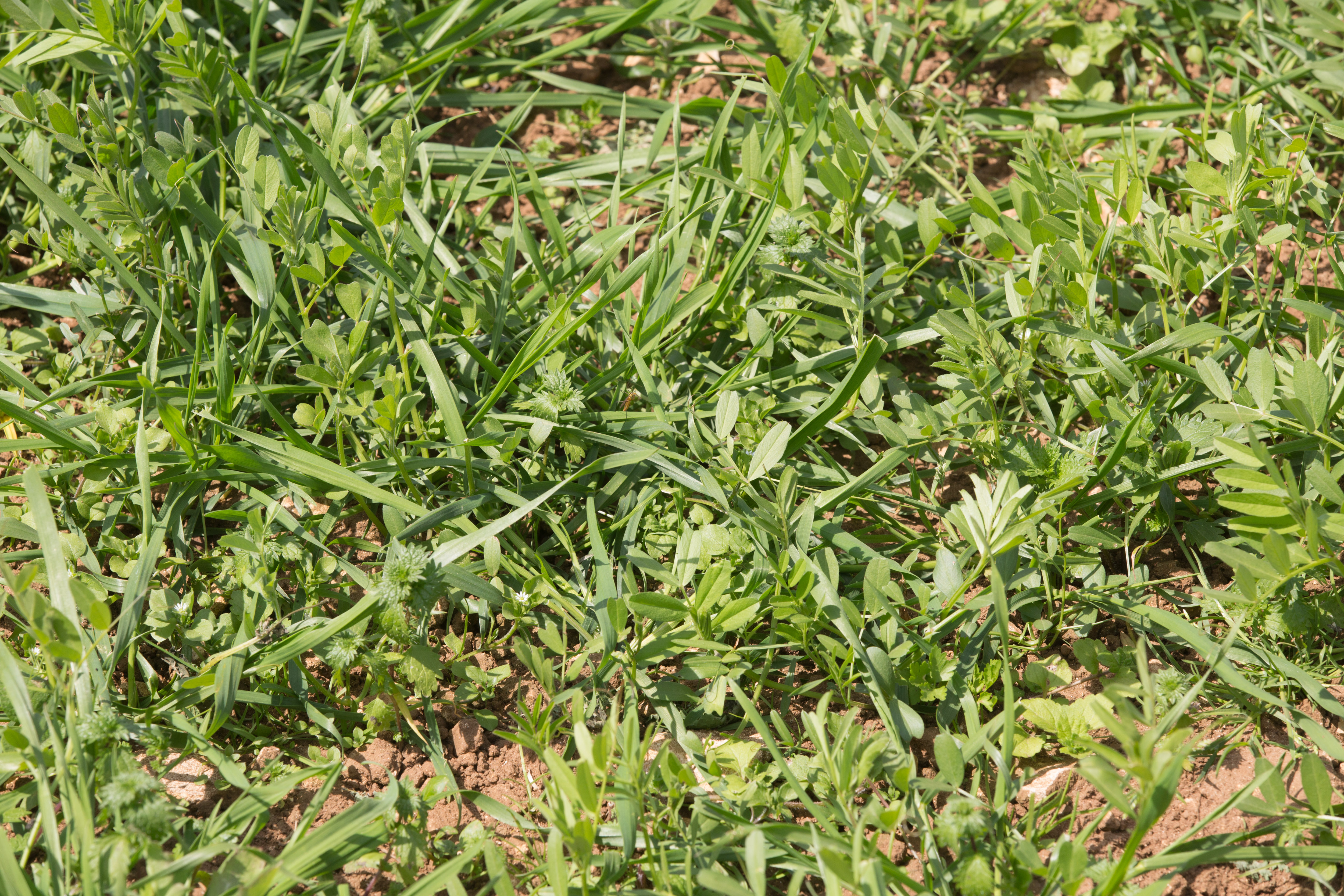
A focus on improving soil structure means crops are now established via minimum tillage, and cover crops are also grown for their soil structuring benefits.
With thousands of hectares to cover and land that can be described as heavy in terms of its soil type, achieving that balance between profitable and environmental farming doesn’t come without its challenges, explains Matthew. “One of our main challenges is not having the range of break crops on our heavy soils – it’s particularly difficult when we can’t grow as much oilseed rape as we used to because of cabbage stem flea beetle.
“We’ve also got quite a lot of blackgrass, which is why the range of cropping and stewardship is so important.”
Matthew sees weed control issues as the biggest hurdle to overcome. As part of the control strategy the estate has recently brought livestock into the system. The sheep graze herbal leys, which comprise of a mix of grasses, legumes and herbs, and cover crops over the winter. “The increased grass area, in rotation with arable, helps us in the challenge of reducing the competition from output-sapping and spray-resistant blackgrass weeds.
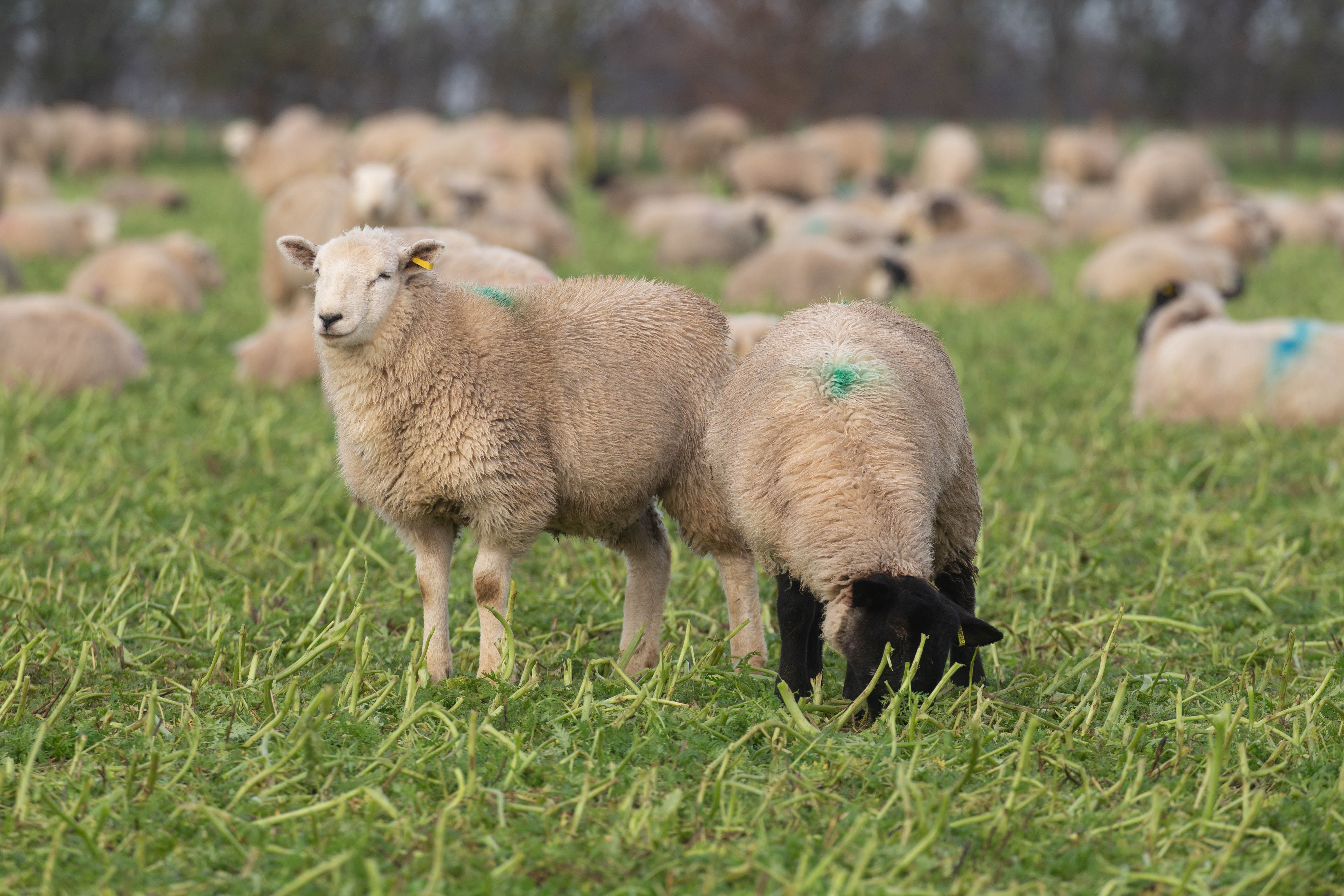
Livestock have recently been brought onto the land to help tackle weed issues.
“Our goal is to get to a point where we can drill more winter wheat, but slightly earlier. But first, we’ve got to get that blackgrass under control.”
With heavy land, timeliness is everything, explains Matthew, which has been one of the main drivers behind his latest investment. “Due to our blackgrass issues, we have perhaps more spring crops than many would which puts a bit more pressure on us at harvest. We’re also fairly high up in terms of altitude, so we do tend to be a week to 10 days later to harvest than other local growers. If it then comes wet at the end of August, the outlook often isn’t very good.
“With all this in mind, having combine capacity to make sure we can get crops off as quickly as possible when we’re ready to harvest is vital, to allow us enough time to get cultivations done and stale seedbeds ready for the next season’s cropping.”
Last year, Matthew set about to replace two existing combines. “The previous combines were excellent and the backup was second to none, but we just needed something with more capacity.”
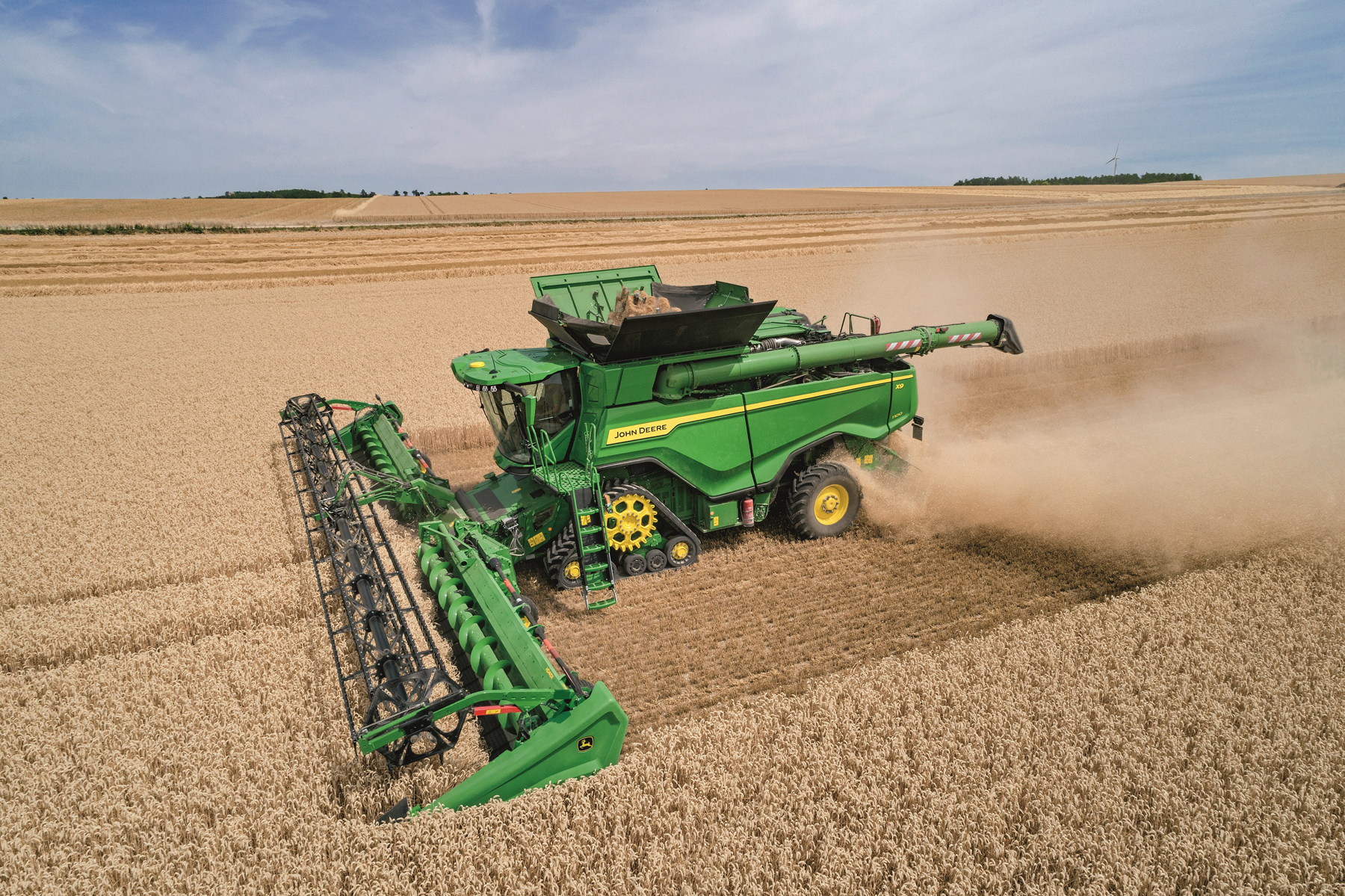
It’s the X9’s capacity which makes it stand out from the competition, with X9 1100 capable of harvesting wheat at 100t/hour at less than 1% grain loss.
He tried various different manufacturers and models on demo, but it was John Deere’s X9 that stood out. “It wasn’t power we were looking for. What put it above the rest was simply the fact that the X9 was one of highest capacity combines on the market.”
The demo model was the 1100 and Matthew said it went very well. “You could tell straight away that it was outperforming our existing combines and the capacity was there. It was a nice machine, a good quality sample came out of it, and it was good to drive.
“It’s performance in terms of cleaning and separation plays a large role in its abilities – these are essentially where you get output from.”
Impressed with what he’d seen, the next step was getting quotes from the dealer. “We worked through the options and from our perspective, the only real differences between the 1100 and the 1000 was engine horsepower and the tank capacity. As we’re not chopping as much straw anymore, instead we’re baling a lot behind the combine, we contemplated whether we really needed that extra power from the 1100. So, we actually ended up going with the two 1000 models in the end. It was a little bit cheaper, but it has still got the same internals as the 1100 so it was the best option for us.”
So, looking at its credentials, how exactly does the X9 stack up? A desire for maximum efficiency was the driver that led John Deere to develop and launch two new X-series models to add to its 2021 harvesting line up – predominantly aimed at large-scale farmers battling narrower harvesting windows.
According to Jack Wright, sales manager at the Farol dealership in Newark – which facilitated the deal with Matthew – the new X9 1000 and 1100 combines represent the “next level” of the firm’s harvesting performance.
The main feature of note is, of course, the X9’s capacity – with X9 1100 capable of harvesting wheat at 100t/hour at less than 1% grain loss, he adds. “The X9 series is able to automatically adjust to the conditions in front of it to ensure it’s always performing at optimum levels,” says Jack.
At the heart of the series, and responsible for this improved performance, is the feederhouse which is claimed to be the widest on the market. This is coupled with a new dual rotary separator – and what Deere claim to be the industry’s largest cleaning shoe – which work together to improve crop flow and increase harvesting capacity.
“As the crop moves from the feedhouse, it’s fed via a chevron-design feed accelerator into the X-Series Dual Separator (XDS) which was designed newly for this series of combines.”
The XDS system enables the crop to be handled through nine revolutions – facilitated by the largest active threshing and separation areas across the entirety of Deere’s fleet – which translates into low losses but high harvesting capacity, adds Jack.
“Via the largest active threshing and separation areas we’ve ever offered, crop in the XDS is handled through nine revolutions, resulting in low losses and increased harvesting capacity.”
The 3.51m long XDS rotors are based on a concept from the S-Series combines, with dedicated sections for threshing and separation. Alongside the traditional threshing elements, the separation area utilises a finger design to tease the last grains from the crop mat, in turn enhancing performance in conditions that are “less than ideal”, explains Jack.
The series has also adopted technology from other kit in the Deere fleet. HarvestMotion was first featured in the 9000 Series foragers and is essentially a belt system which is claimed to lower fuel consumption by 20%, provide almost a third more torque and to also lower engine rpm. Again, the inclusion of this in the X9 design is all centred around optimising efficiency at every point possible, he adds.
In terms of tank size, the X9 1000 grain tank holds 14,800 litres and the X9 1100 up to 16,200 litres of grain, with unloading rates of up to 186 litres/sec.
In comparison with the older S-Series combines, the cleaning shoe has a 36% greater cleaning area – coming in at 7m2 – as well as 45% more cleaning capacity as a result of a new fan system.
Powering all this performance is a new 13.6 litre six-cylinder engine, capable of delivering up to 700hp, which enables combines to run for 14 hours without needing to refuel – minimising downtime, he adds.
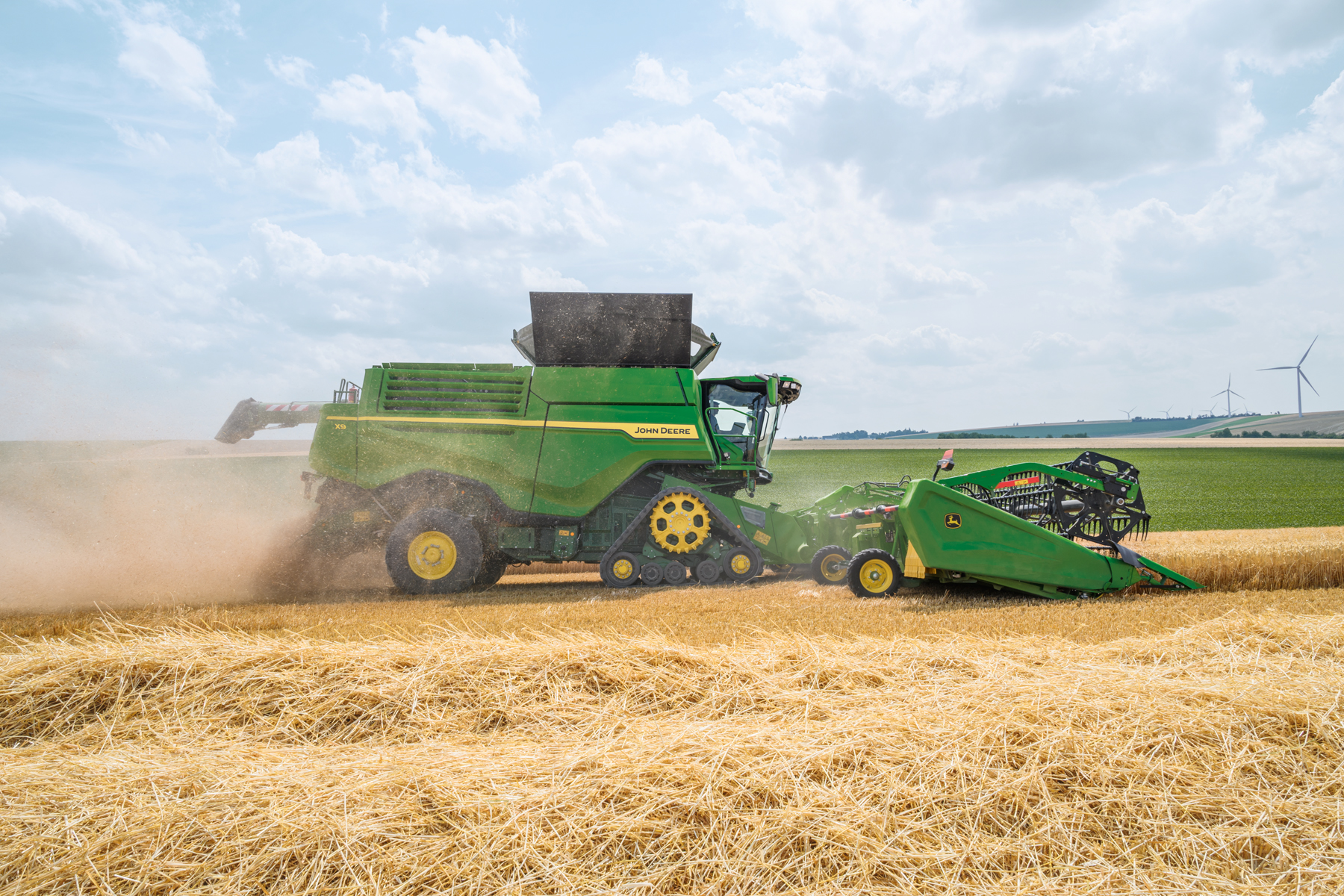
Powering the X9’s performance is a new 13.6 litre six-cylinder engine, capable of delivering up to 700hp, which enables combines to run for 14 hours without needing to refuel.
Looking at the transmission, the X9 features a new development here too. “The new ProDrive XL has a number of advantages over the standard ProDrive transmission,” explains Jack. “Namely, this comes via 30% more torque, which is useful in suboptimal conditions and on steeper ground, as well as engine speed management to 1700rpm to maximise efficiency on the road.”
Inside the cab the X9 also features a number of options including a seat fitted with a massage function, Apple CarPlay, and an updated LED lighting package. What’s more, as an optional extra operators can choose to kit their combine out with some of Deere’s on-board technology packages including Active Terrain Adjustment which automatically adjusts the combines sieve and chafer openings, controlling the cleaning fan speed and stabilising tailings levels to enhance grain quality.
The range of on-board technology is something that Matthew particularly likes. “The whole John Deere system works well for us, from the GPS to the OperationsCentre system which enables us to get the statistics from the combine while it’s still in the field – meaning we can see the yield in real-time, for example. Having access to this instant data enables us to make very quick decisions when necessary.”
Other tractors on the farm also run on the same system, which helps logistically with such a large operation, he adds.
To make it even better, Matthew says having the ability to switch one of the augers off in the tank would be really beneficial. “This would mean that when you’re unloading to a trailer, you could top it off much easier. But this is something quite simple, not a complete design change.”
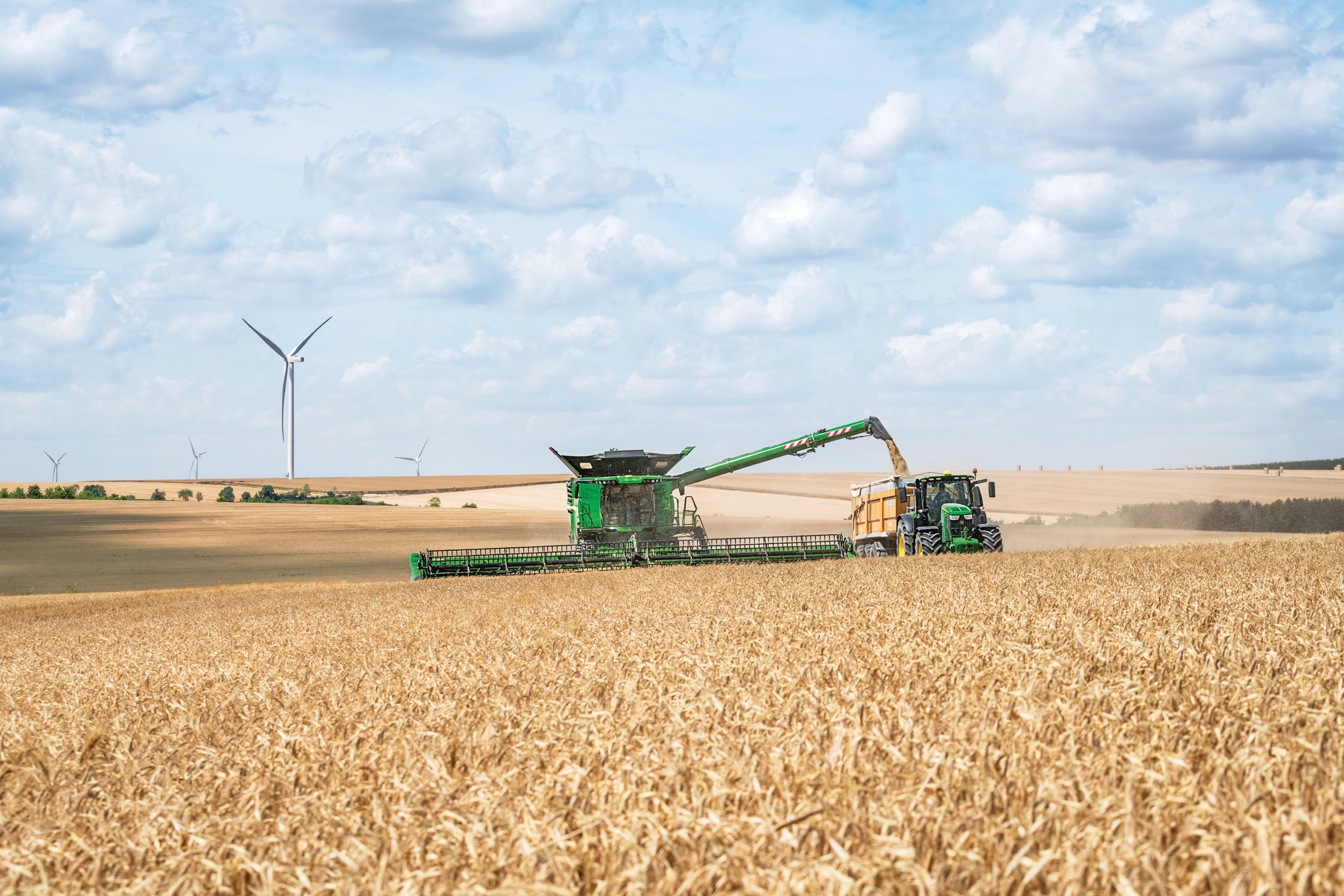
Matthew says the X9 stood out due to it’s increased capacity over anything else on the market.
Delays with delivery meant Matthew kept the demonstrator model for the rest of the season last year and has been using it alongside one of his original machines this season. The first of Buckminster’s own X9s arrived in early August, with the second due for delivery imminently.
And though it’s early days, Matthew says he’s impressed by its performance. “There has been a significant jump in output over the competition and we believe that if we’d been running our two X9’s over the entire season to date, we would easily have knocked a week off harvest.
“What we’ve actually found is that we’ve got so much more capacity with the X9 that it’s put a strain on everything else, like the handling system and storage,” he laughs.
The golden question is, of course, is it worth the price tag? “Yes. Particularly when you start to try and quantify the benefits to labour and fuel savings, for example. You have to remember, these machines come with a set price and then it’s up to the farmer and dealership to negotiate a figure everyone is happy with. We got quotes from a number of different manufacturers for different types of combines, but I’d say that what we paid for our X9’s is not far off the rest. All machinery is very expensive now, so you’ve got to make sure and be confident that whatever you go for is going to earn its keep, and for us, this will.”
This article was taken from the latest issue of CPM. For more articles like this, subscribe here.