Better known for its min-till drills, Horsch is a relatively recent newcomer to the direct-seeder sector. CPM visited a south Herts farm to discover how an early adopter has fared with its Avatar model.
One of the reasons we were especially impressed by the Avatar was its relatively low power requirement.
By Martin Rickatson
Few farms are blessed with consistent soil types, simple rotations and low grassweed burdens – and far fewer than that benefit from predictable weather. And as units become larger and these challenges consequently become greater, the ability of a single drill to work successfully in all situations tends to diminish.
That’s the issue that has faced south Herts farmers JS Hunter and Sons as their enterprise has expanded. When CPM last visited in 2012, the family had grown its farmed area from 760ha to 1040ha, through the addition of rented, share-farmed and contract-farmed land in the locality. Since then, further agreements have seen that figure grow to 1600ha, producing wheat, barley, oats, oilseed rape and beans.
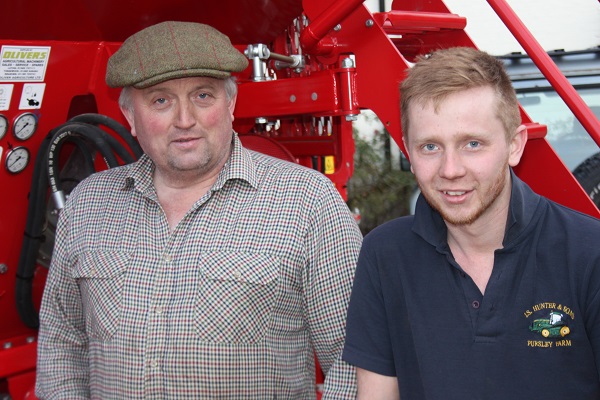
Jimmy and Hugh Hunter believe they’ll be able to gradually increase their direct drilled area, but for now they’ve retained other options.
To handle the greater area efficiently, the business has moved from 24m to 36m tramlines and added a second (used) combine to its fleet to speed harvest and try to ensure crops can be cut in ideal conditions without the need for drying, going from a Claas Lexion 600 with 10.5m header to a similar-sized Lexion 770 and used 750 models. In addition, the Hunters have switched from tractor/trailer grain haulage to a chaser bin and a brace of 32t capacity eight-wheeler trucks for road transport.
Despite all of this, the labour force has remained static, with brothers John and Jimmy Hunter having seen their father take more of a back seat and their one member of staff retire, but a son from each side of the family, Hamish and Hugh respectively, join the business. However, while the wider spread of land has helped to produce economies of scale, it has also brought with it the challenge of greater soil variability and the need, where possible, to seek out more efficient methods of crop establishment.
“We were already running a largely min-till system, using an 8m Väderstad Rapid and, for some suitable fields, a Kverneland TS tine drill where possible, but with the plough retained for some circumstances,” explains Jimmy.
“But we’re always keen to try new ideas, and wanted to reduce costs further where possible by adopting direct drilling where the land and crop type suits it. We also wanted to speed up the whole crop establishment process, particularly at harvest when OSR drilling has to be carried out alongside wheat cutting – previously we’d been using a cultivator-mounted seeder. And at the same time, we wanted to further minimise soil disturbance, as we have some challenging blackgrass issues.”
As a result, the family began to consider the idea of direct drilling for at least part of its area and some of its cropping. A small number of drills were trialled on demonstration, with judgement reserved until the following harvest, but some were dismissed due to their available working widths, grain-only format and power requirement.
“We were looking for an 8m drill to cover the ground, wanted a model that would give us the option to also put down some seedbed fertiliser and slug pellets through the same system. We also wanted one that was compact and handled well, not just for manoeuvrability in the field – our average field size is only around 8ha – but also in transport, as we need to move quickly on busy roads,” notes Jimmy.
“The drill would need to be versatile enough to work in high trash conditions, as we now have crops such as maize for anaerobic digestion in our rotation. We also have one farm where pick-your-own strawberries are grown, and the drill needs to work into the residue at the end of the season.”
A number of machines were trialled over the 2016-17 season, in crops including OSR and barley, but while establishment was generally pleasing, some failed to deliver the expected results at harvest, recalls Jimmy.
“Based on a number of factors, including the availability of a 8m model, a fertiliser option and the drill’s on-road handling, plus good results from the demonstration-drilled crops, we decided on the Horsch Avatar SD demonstrated by Oliver Agriculture, the dealer with which we already work for our combines and handlers.”
When it comes to min-till drills, Horsch has traditionally preferred to provide choice rather than nail its colours to a particular mast, with the Pronto for those who favour a disc coulter and the Sprinter for those who would rather place seed down the back of a tine. But in 2015, when it re-entered the direct drill sector for the first time since Michael Horsch launched his business 35 years ago with the Seed Exactor, it chose a single-disc set-up for its new Avatar SD.
Some of the components of Horsch’s Pronto DC min-till drills mirror those used in the Avatar SD, including the seed tank and metering equipment, and the design concept uses a similarly compact format. Seed capacity is 5000 litres on the 8m model, split 60:40 seed to fertiliser. The drill is built around a coulter frame claimed to be sufficiently strong to eliminate sideways movement, and thus ensure sowing depth is maintained on uneven soils. The Avatar SD’s single disc coulters are arranged over two rows to minimise the power required to pull the drill, with a 16.7cm row spacing and a clearance of 33.4cm per row to help handle high trash conditions.
Set at a 7° angle, each disc is paired with a rubber-coated gauge wheel alongside to control the seeding depth. An angled, steel press wheel, running alongside, then reconsolidates the soil over the seed slot. A more heavy-duty version on the Pronto’s rubber suspension system is used to maintain the set pressure on the coulters, with a maximum figure of 200kg. In 8m format the drill weighs 9900 kg, and additional weight can be added for hard ground.
The Avatar SD is supplied as standard with mechanical half-width shut-off, while electric half-width shut-off controlled via the ISOBUS terminal, or automatically using Horsch’s SectionControl activation, is optional. Control and monitoring of the machine are carried out via a standard ISOBUS terminal, or through an ISOBUS tractor screen.
“One of the reasons we were especially impressed by the Avatar was its relatively low power requirement, which Horsch reckons is due to the staggered coulter layout,” says Hugh, who operates the drill much of the time.
“Although we have a 370hp John Deere 8370RT crawler, and have occasionally used this with the drill, usually it’s operated behind our 290hp John Deere 7290R wheeled tractor, and although we have some heavy ground and some banks, it copes well.”
The new drill has slotted into a system now based around three drills according to land and crop type. The bulk of the farm’s wheat drilling remains the responsibility of a Väderstad Rapid, upgraded this year to a new 8m Jumbo model, while the 6m Kverneland TS tine drill has been retained for bean sowing. Meanwhile, the area of direct drilling undertaken by the Avatar is being gradually increased, with its current roles largely as an OSR drill in the summer and for spring barley establishment.
“Essentially we’re trying to slowly grow the area on which we use the drill, and that depends largely on ensuring the soil structure and drainage are suited to its use,” says Hugh.
“If you don’t have well-drained soils I think it’s difficult to get good results from any direct drill. We’ve tried sowing in wetter conditions, but results aren’t good. A relatively dry soil surface is best.
“That said, it’ll work well in a wide range of circumstances beyond untouched land – where we drill OSR directly after baled straw – including after the incorporation of digestate. Because we now have two local AD plants we make use of this as a pre-drilling fertiliser, applied through a 24m umbilical system and incorporated with a Sumo Mixidisc. We’ve also used it on ground which has been moved to a greater extent, where our Grégoire Besson Discordon has been used to loosen more compacted land and/or incorporate chopped straw to minimise slug issues, followed by a pass with the rolls.”
With slot closing in tough soils often being an issue with direct drills, the Hunters have trialled four different press-wheel types with the Avatar to try to find the best option to suit their largely heavy soil types.
“We’ve had good results using a steel type with four sections and an open centre,” reports Hugh. “It presses sufficiently to fill the slot with soil and flexes just enough to ensure it doesn’t bung up in damp conditions. Only in very wet going have we had any issues. We try not to roll post-drilling unless there have been slot-closing issues, as we find it only encourages weed establishment.
“Disc performance has also been good, with the units slicing well into post-crop stubbles including wheat, maize and the strawberry plants. With the drill weighing around 10t when loaded with seed, it’s weighted well for ground penetration.”
While he’s very happy with the performance and design of the drill, Hugh says there are a few areas where design could be improved.
“In particular, the depth adjustment could be made simpler. It has to be carried out on each individual disc, which takes two of us around an hour. A gang arrangement would be simpler.
“But calibration takes only around ten minutes, and seed filling is easy. We considered a seed bag crane to simplify loading, but didn’t think the cost could be justified. I don’t think it would actually make our system much easier. We often have two drills working at once in different fields, with a third person running between them with a telehandler and trailer, and that works well for us.”
The drill’s tramlining kit isn’t used, with the farm’s Challenger RoGator RG655B sprayer making its own path through crops using RTK GPS. The split seed/fertiliser hopper, though, gets full use through the OSR drilling season, with all of the crop being planted with 75kgN/ha as DAP, while the 200-litre capacity microgranular applicator simultaneously places slug pellets.
“I don’t think it’ll be a drill we’ll ever use for all crops on our ground – the depth required for beans, for example, will require too much power to achieve sufficient speed at this width,” notes Hugh.
“But it’s now our only method of establishing OSR, speeding up the job and enabling us to get back to the wheat harvest, and we’re increasingly trialling establishment using the Avatar in a number of other situations. That’s not to say we don’t or won’t reintroduce the plough and drill with the Rapid if we’re having real difficulties with blackgrass and need to reset things, but I can see us gradually increasing the area on which we use the drill each year.”
Farm facts
JS Hunter and Sons, Shenley, Herts
- Farmed area: 1600ha (of which 292ha owned and remainder contract or share-farmed or tenanted)
- Soils: Mainly clay over gravel, plus some lighter land
- Cropping: Winter wheat, winter oats, winter oilseed rape, winter beans
- Staff: Jimmy and John Hunter plus two sons Hugh and Hamish
- Mainline tractors: John Deere 8370RT, 7290R, 6215R, 6930, 6430, 7810, 7710, 4955
- Handlers: JCB Loadall 531-70 and 530-70
- Combines: Claas Lexion 770 and 750 (both with 10.5m headers)
- Drills: 8m Horsch Avatar, 8m Väderstad Rapid System Disc, 6m Kverneland TS tine drill
- Cultivation: 9f Grégoire Besson semi-mounted plough, 6f Kverneland mounted plough, 4.2m Grégoire Besson Discordon, TWB 9-leg subsoiler c/w Opico Variocast seeder, 12.3m rolls, Brock Underburst subsoiler
- Sprayer: AGCO Challenger RoGator RG655C 36m self-propelled
- Spreader: Amazone ZA-M