Advances in power, road speed, suspension and tyre technology mean conventional wheeled tractors are replacing tracked models as some larger farms’ mainline machines. But one Bucks contractor believes the former don’t hold all the cards. CPM pays him a visit.
“This isn’t a machine for operating in a high gear at tickover.”
By Martin Rickatson
Reinforced rubber track technology unarguably revolutionised the tracked tractor principle. First came differentially-steered twin-track machines as an evolution of the conventional crawler. Then came a complete departure in crawler tractor steering – the development of the first tractor using four triangular track units on a chassis that articulated.
This development facilitated smoother headland turns, minimises trafficked ground and keeps each track in full ground contact when pulling hard.
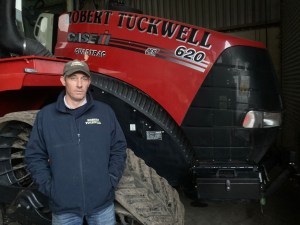
The need to operate wide tillage equipment at speed to achieve the desired finish was a key reason for his tractor policy change, says Daniel Tuckwell.
More recently, advances in tyre technology – such as, increased/very high flexion (IF/VF) carcase designs and variable pressure systems, plus higher tractor road speeds and the trend to shallower cultivations – have seen some larger farms move away from rubber-tracked crawlers towards conventional tractors in the 400-500hp bracket, to pull wide cultivation equipment at high speeds. But is this a trend set to spread?
Ask Buckinghamshire-based contractor Daniel Tuckwell, and he’ll suggest it’s not something that suits everyone. To maintain cultivation speed, improve work rates and enhance soil finishes on the heavy clay land using full and minimal tillage, he has switched his prime mover from the largest conventional wheeled tractor on the market to the largest articulated tracklayer.
Having done so, he reckons there’s little to challenge tracks for traction, both to pull deep-working implements and to operate shallower-working wide ones at the speed required for best effect and decent daily output.
“We run four 360hp conventional tractors for general work, backed by some smaller 180-250hp models,” explains Daniel, who runs Robert Tuckwell Contractors with his father Robert, who began the business out of a dairy and arable enterprise that’s now focused on beef and combinable cropping.
“Customers judge us on how our seedbeds and crops look and perform, especially as much of our cropping is milling wheat. We’re on mainly heavy clay, which isn’t kind when very wet or very dry. It needs effort in to get quality and quantity out, but I think the crops we produce look and perform better for the cultivations we do, particularly as we have maize in our rotation, and also often need to incorporate sewage cake and cattle muck.
“Because that means doing more than scratching the surface, we need power and traction to maintain cultivator momentum, achieve good daily outputs, and get jobs done when soils are in good condition.”
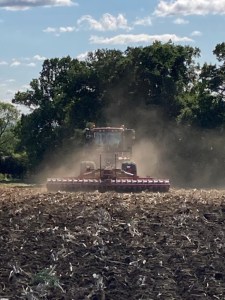
The Väderstad TopDown for shallow working or the Sumo Quatro for deeper loosening are both followed by a 10.5m Väderstad Rexius Twin press where necessary.
Väderstad TopDown and Sumo Trio one-pass cultivators and a Väderstad Rexius Twin press have been the business’s main primary and secondary soil implements, plus a nine-furrow semi-mounted Lemken where ploughing is required for restructuring or weed control. But expansion of contract services and whole farm contracting in recent years has meant more work in both autumn and spring, necessitating an upgrade to both the cultivation equipment and the top-end tractor.
“When our preferred big tractor maker Fendt introduced a 400-500hp range above the biggest ones we were running, in 2016 we purchased the largest 1050 model to boost cultivation output. It was equipped with a variable tyre pressure system and set up with help from tyre specialists.
“You need weight to pull weight, and they helped us find not only the best pressures, but also the ballast needed to maximise grip, resulting in a weighted tractor that totalled 24 tonnes so we could get full power transfer. It worked well in many situations, and when the tractor came due for renewal in 2019, we replaced it with another,” he says.
“But across more seasons we found its limitations. On maize ground, using full wings with 80mm points on our 5m TopDown to move all the soil at 9-10in deep, upon hitting compacted ground it would stop and spin. I’d have to disengage cruise control, back up and raise the cultivator, pre-work the soil, then drop back in.
“And on hard cereal land after a dry summer, we just couldn’t get the power to the ground with the 7km/hr. The 1050 often topped out at not fast enough to boil the soil and produce a good result. At some points on headlands or tramlines the tractor would just sit and spin, and I felt we’d reached the limits of what a wheeled machine could do for us.”
Having previously considered a tracked tractor to boost primary cultivation output, Daniel subsequently decided to arrange some demonstrations. His favoured high-hp tractor maker Fendt was by this point marketing twin-track crawlers, but a four-tracked articulated tractor was preferred over a differentially-steered twin-track for full power turns and full track-to-ground contact.
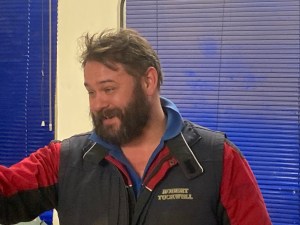
The tractor switch has helped cut fuel use, boost output and shorten some working days, says operator Scott Hosking.
“The expansion of our contracted land area and the wheeled tractor limit we’d found with our existing main machine meant I decided we’d reached the point we could justify one. From the outset, the Case IH Quadtrac was my preference, as it was the original machine of its type, so was well-proven. But John Deere had also entered the articulated four-track market, so we had the two choices.”
Demonstrations of the largest model in each maker’s range – the 9RX 9620 (691hp max) and the Quadtrac 620 (692hp max) – were subsequently organised, and Scott Hosking, who was to be the chosen tractor’s operator, compared the two alongside Dan.
“I’d operated mainly John Deere tractors for my previous employers,” says Scott. “But when I came here, I worked mainly with a Fendt 724, so it was a while since I’d driven a John Deere and I’d had no experience of Case IH machines.
“We used a Quadtrac demonstrator for a few days, and then tried the John Deere 9RX. The Deere impressed us both, and visibility to the rear was better, but we felt the Quadtrac had the edge in terms of refinement – the cab was better-finished and quieter with more forward vision, and the tractor was smoother at work when pulling hard.”
Both tractors were subsequently priced, with the Quadtrac proving significantly more competitive, partly due to the dealer being keen to work with the Tuckwells as a new customer. Consequently, the Quadtrac’s purchase was agreed in September 2021, with the Fendt 1050 part-exchanged.
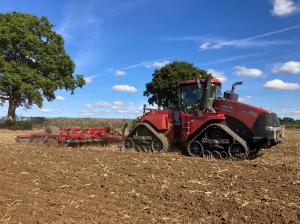
To match the new tractor’s capacity and help ensure one-pass seedbed creation across all soil types/conditions, the 3m trailed Sumo Trio was upgraded for a 5m trailed Quatro.
To match the new tractor’s capacity and help ensure one-pass seedbed creation across all soil types/conditions, the 3m trailed Sumo Trio was upgraded for a 5m trailed Quatro from the same maker, featuring an additional twin row of scalloped discs ahead of its loosening legs, which are followed by a further double row and a press. Other Quadtrac partners include a 9f Lemken plough and a 7m Kuhn power harrow.
“Where compaction at depth isn’t a particular issue and we want to ‘boil’ the top few inches and mix the trash, we use the TopDown, which produces a better finish. But if deeper loosening is necessary we’ll use the Quatro, following in both cases with a 10.5m Väderstad Rexius Twin press if needed,” explains Dan.
“The Quadtrac isn’t as fast and easy to move on the road as the 60km/hr tractor it replaced, but it does do 40km/hr, and as all our cultivation equipment is rated for towing at that speed – apart from the 30km/hr-rated Rexius – this isn’t an issue. We’ve always been careful to stick to those speeds for safety and machinery care reasons.
“It looks a big machine, but the Quadtrac is actually 10cm narrower than the 1050. That said, we’re slightly more restricted in running to and from jobs. As a rule we run tractors home at night, but that isn’t so simple with the Quadtrac. While we have some outlying areas, most of the 1200ha (3000ac) we currently farm is in a 15-mile radius, and we try to crop and work in blocks. We usually take a vehicle and fuel bowser, leaving the vehicle behind so the operator can return home if there’s more than a day’s work.”
This is reckoned to be more than compensated for by the Quadtrac’s greater output and the better work it produces, he says.
“With the additional power, footprint and grip we soon found we could achieve with ease the right forward speed to get the best finish from the TopDown and Quatro, even in last year’s dry and hard conditions.”
Scott keeps detailed tractor fuel use and performance records, and he and Dan reckon this analysis supports their conviction that the Quadtrac has brought about significant output and cost benefits.
“Using the 1050, typical fuel use with the TopDown was 88 litres/hr, working at 7.4km/hr at 15% wheelslip,” he says.
“With the Quadtrac, those figures are 8.8km/hr at 1.0% track slip and using 83 l/hr. At the depth we pull our TopDown, the fastest I pulled it with the 1050 is the slowest I have pulled it with the Quadtrac.
“With the 5m TopDown on our heaviest ground, the 1050 was covering 3.6ha/hr using 85 l/hr of diesel. With the Quadtrac we were using 122 l/hr of fuel but covering 5.2ha/hr. As a result, the Quadtrac was £2/ha cheaper to operate, and was also doing a better job, because it just walks through sticky corners and tough spots.
“There’s no need to stop and start and feather through, doing half a job with the implement to maintain momentum. It’s not just another 120hp, but how the power is put to the ground. Track slippage is no more than 2-6%, compared with up to 20% in tough going for the fully-weighted Fendt.
“Higher output also cuts long working days – on larger fields I can cover 80ha/day with the Rexius without doing silly hours.”
In its first year the Quadtrac completed 1,300 hours’ work, and Dan reckons that provided a fair analysis of its benefits and any drawbacks. The former considerably outweigh the latter, he believes.
“Since it arrived, we’ve reduced the annual workload on our frontline Fendt 936s from 17-1800 hours to 1500, because they’re not doing as much work supporting the main tractor, as it’s now more than on top of the job.
“In fact, I think we could do more with some implements, and as we’re taking on more land this autumn I’m considering replacing the 5m TopDown with a 6m, if our balance of light/heavy contract ground remains unchanged.”
With the business growing a significant area of maize for AD and for sale to dairy/beef farmers, plus stubble turnips and spring-sown combinable crops, the Quadtrac is busy both sides of Christmas.
“Spring crop land is mucked during February-March before cultivation,” explains Dan. “That presents additional traction issues, and is another reason we didn’t looked at a twin-track crawler or half-track machine. With the TopDown, for example, 11km/hr is the optimum speed to achieve a good mix at 250mm/10in deep. With the 1050 we were sometimes pulled back to 8km/hr, especially on old grass leys, but we now have the power and grip to maintain speed.”
Quadtrac models from the 525hp (max) Quadtrac 470 to the 613hp (max) Quadtrac 540 are available with an optional CVXDrive continuously-variable transmission, but the 620 (692hp) and 580 (647hp) models come in 16F/2R powershift form only. While he appreciates the benefits of a CVT, Dan says power was his first consideration. Scott agrees that the larger powershift model was the right choice.
“To operate the powershift for best efficiency, I select the best gear for the task and load the engine so the revs are pulled back as the tractor settles into work and just tap back a gear if hitting a really tough spot. This isn’t a machine for operating in a high gear at tickover – it prefers 1800rpm to the 1400rpm sweet spot of the 1050 – and in tough going powering through is the right technique rather than easing back.
“But I keep a close eye on fuel consumption, and the larger displacement of 15 litres versus 12.4 litres in the 1050 means it just doesn’t sweat. Working the 1050 the same way would see it needing more rpms and more fuel as it searched for grip, and I often found as a result that I’d end up operating the CVT manually.”
Beyond the in-field arguments, there are pluses and minuses on the road for both tyres and tracks, notes Dan. “The first 1050 we had wasn’t so bad, but with the second we were asking more of it, wearing out the tyres in 18 months. At £20,000 a set, that’s costly. Track wear on the Quadtrac has been ok, although after 1300 hours in its first year it doesn’t look like the midwheel rollers will do much more than another 12 months.
“But with regard to other components we’ve purchased a 5000-hour warranty with the tractor. The purchase prices of tractors today mean long warranties are essential.”
While its wheeled predecessor’s comfort was rated highly, despite being a tracked tractor the Quadtrac’s suspended cab means the ride is good, says Scott. “Sometimes you don’t notice that the implement has hit some tough going, because the tractor simply pulls through it, so it’s important to make sure the cultivator can cope with what the tractor can.”
Based on his first year’s Quadtrac ownership, Dan is now considering supplementing it with another. “We’ve got customers who’ve seen the cultivations and crops we produced with it this past year and have booked us for 2023 as a result. With more contract land and greater demand for services, I may add another Quadtrac to complement the 620.
“Leaving that tractor to do the primary tillage, the largest CVX model, the 540, is a possibility for top work and to operate our chaser bin. For jobs like those where traction and flotation are critical, I think the Quadtrac is ideal and the CVT will be the right transmission for those tasks.”
Farm facts – Robert Tuckwell Contractors, Little Horwood, Milton Keynes
Cropped area: 1258ha plus contract work
Cropping: Winter wheat (768ha), maize (490ha)
Livestock: 100 Belgian Blue cows plus followers
Tractors: Case IH Quadtrac 620, Fendt 936 x4, JCB Fastrac 4220 x4, Claas Arion 650 x3
Combine: 10.5m New Holland CR10.90
Cultivation equipment: 5m Väderstad TopDown, 5m Sumo Quatro, 10.5m Väderstad Carrier, 6.5m and 10.5m Väderstad Rexius presses, 2x 6f and 1x 9f Lemken ploughs
Drills: Kuhn Megant 6m tine drill, Väderstad Rapid 6m disc drill, Horsch 16-row maize drill
Sprayer: Amazone Pantera 36m self-propelled
This article was taken from the latest issue of CPM. For more articles like this, subscribe here.
Sign up for Crop Production Magazine’s FREE e-newsletter here.