Manufacturers are continually looking to make improvements to their offering to help farmers and contractors improve efficiency. CPM breaks down and wraps up some of the latest baler and cultivators on the market.
The Optimer compensates for ground contours by adjusting the ground pressure across the machine’s five sections.
By Melanie Jenkins
For both farmers and contractors alike, the requirement for balers and cultivators to do the job well and efficiently is as important as ever. And with machinery accounting for a huge proportion of farm capital, it’s especially vital to have the kit that suits the task at hand.
Here’s a look at some of the latest launches from manufacturers.
Balers
New Holland
New Holland has extended its variable chamber round baler offering this year with the new Pro-Belt Series – launched at Scotgrass. Aimed at large-scale farmers and contractors doing over 7000 bales per year – the baler has achieved up to 30t per hour in field tests, according to Siôn Whittingham of New Holland.
“We felt we didn’t have a baler for this market, so we’re targeting it with this new baler. Basically, it’s been redesigned from start to finish. There’s very little that has been carried over from the Roll-Belt, but the duck-bill netting system has been.”
There are two model options, the 165 and the 190 and two options within these – the super feed which, is not a cutting machine, or the crop cutter. “There are two options to the crop cutter, so users can either have a 25-knife rota or a 13-knife rota. In the 25-knife model, users can select all 25 knives, 12 or 13 – all operated via the cab,” says Siôn.
On the old Roll-Belt, the knives were individually sprung protected but on the Pro-Belt they have hydraulic twin-accumulator protection. “If a large object goes into the baler, it’ll push the knives back a bit, but as knives are longer the chop quality will be maintained.”
This baler has an active drop floor which is sprung loaded. “If there’s a lump of material, the floor will drop to allow this to go through,” he says. “If it does block before or under the rotor, the floor can be dropped form the cab so you don’t have to get out of the cab to unblock the baler. If it drops more than 3.5mm, the baler will warn the operator to slow down.”
The Pro-Belt has a lot less connectors than previous models as there’s a hydraulic manifold on the baler and so two spools are required on the tractor. “One controls the rear tailgate and the other controls pick up, drop floor and knife selection,” explains Sion. “It’s all done through ISOBUS.”
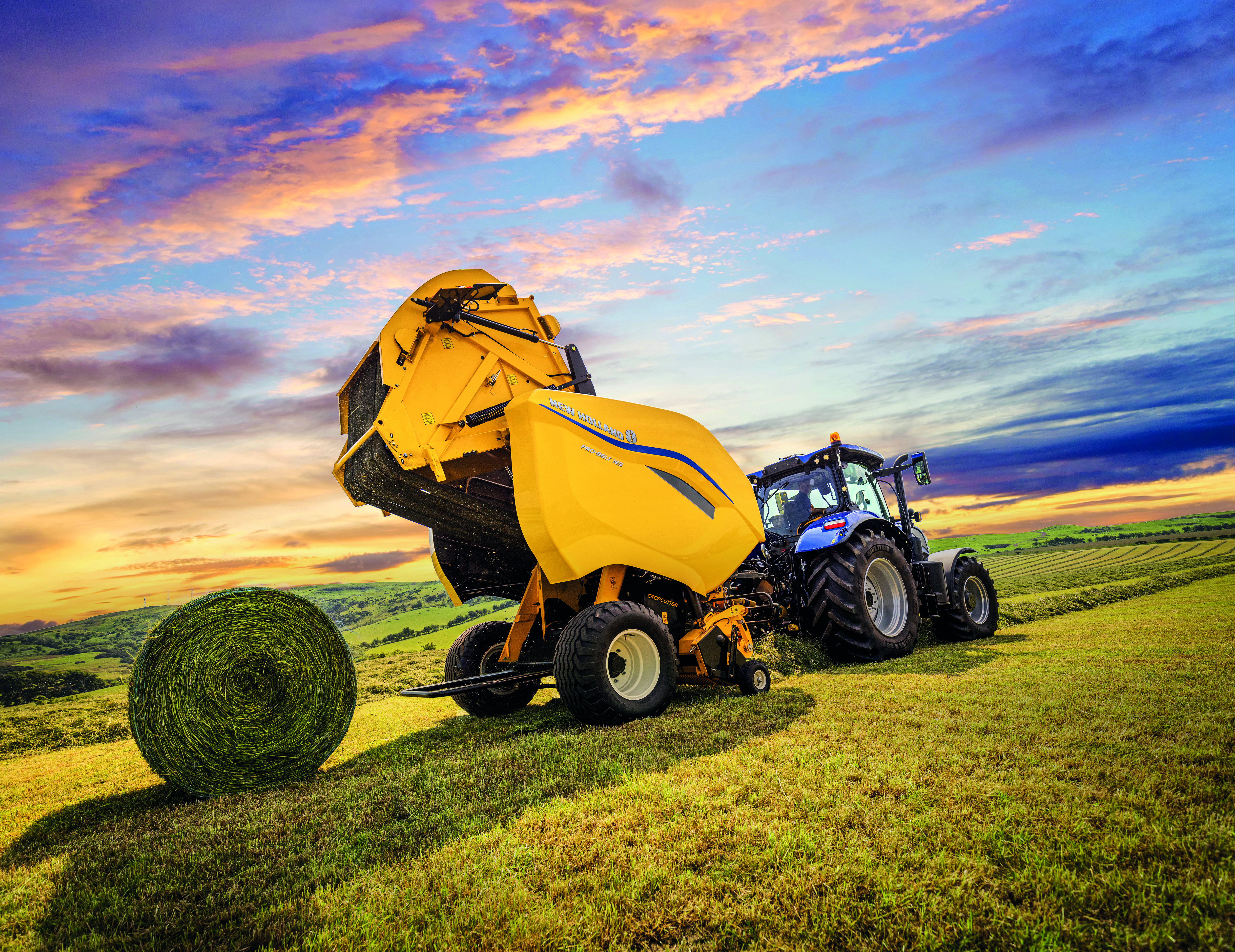
New Holland has extended its variable chamber round baler offering this year with the new Pro-Belt Series.
It has a thousand speed PTO into a twin-drive split gearbox. “We drive the left and right side of the baler, but historically we’ve only driven one side. On the left we drive the chamber and on the right the rotor and the pick-up.”
The pick-up reel is a five-tine bar cam steered system. We tried camless on field test units but they don’t really work for us,” explains Siôn. “We find cam steered better for sweeping all the crop up, so none is less lying on the ground.”
The baler has twin augers that feed into it and a top auger to compress materials into the rotor.
There’s no sledge formation for this baler, says Siôn. “On the Roll-Belt we had roll number four, five and six used to come in to help form the core of the bale but this chamber design is very different. We’ve done away with them so there’s fewer moving parts.”
With four moving belts, the Pro-Belt has five layers to make it strong and durable. There’s a dual drive system, so there are two drives for the belt. “This makes for better power transfer and less slippage, so you can continue baling under high pressures or on wet crops.”
Bale size is controlled from the cab; ranging from 0.9m up to 1.65m on the 165 model or up to 1.9m on the 192 version. Pressure can go up to a max of 160bar, so inner core size and pressure can be set and outer pressure as well.
Kuhn
Kuhn’s new VBP 3165 now features a twin-reel film binding system like that of the brand’s fixed chamber balers. This should enable the flexibility of a variable chamber baler to be coupled with the company’s improved Intelliwrap system that only uses a 750mm film wrap which Kuhn hopes will reduce costs and save time.
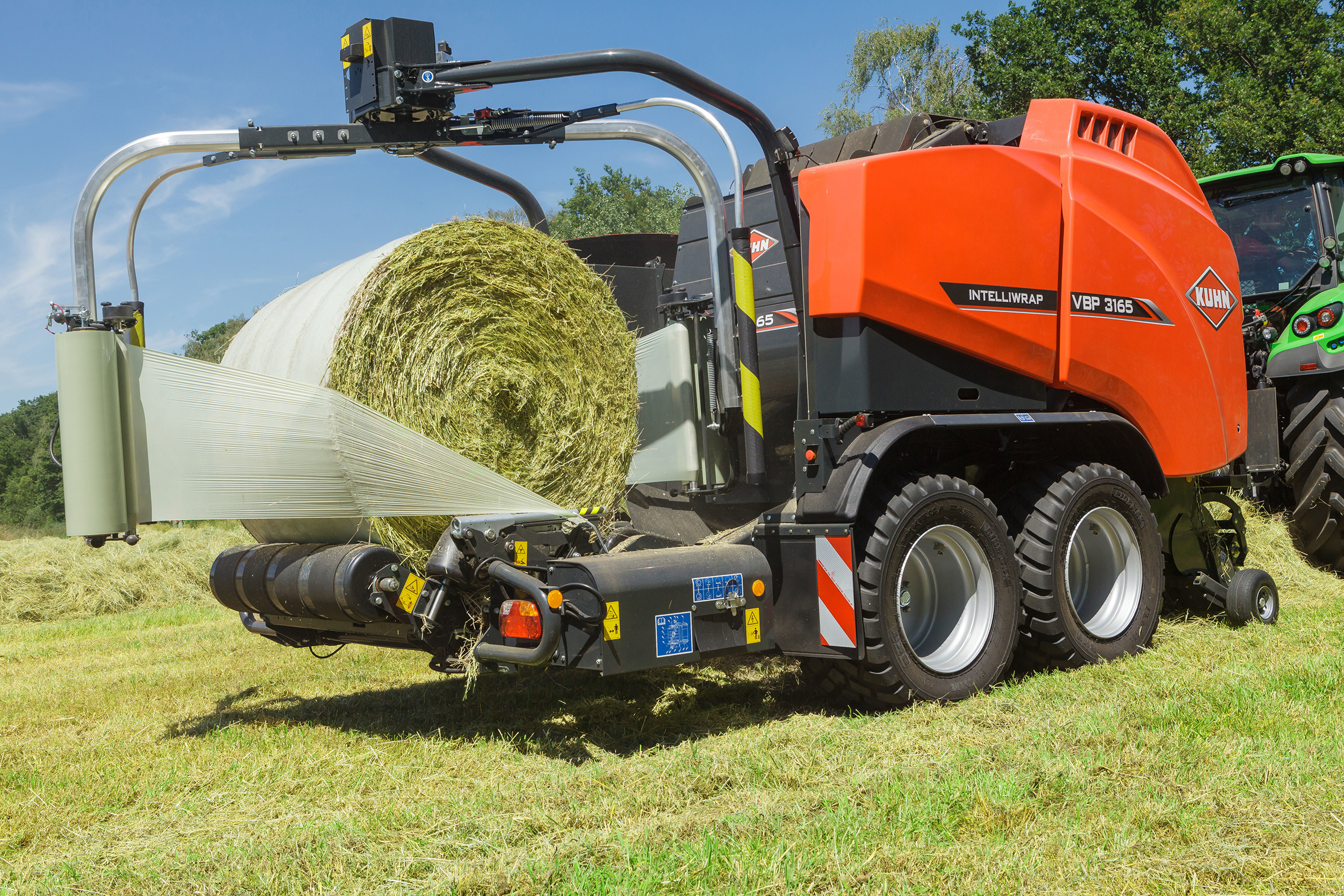
Kuhn’s new VBP 3165 now features a twin-reel film binding system like that of the brand’s fixed chamber balers.
Unlike some machines that use a 1.2 metre roll, the VBP 3165 uses two 750mm rolls. Kuhn’s patented duck-bill film applicator aims to optimise the use of film binding which should help to reduce the amount of film needed, saving operators up to 37% compared with a traditional wrapping system.
At 25kg, with a waist-height mounting point, the rolls should be easier to handle and change, claims the firm. “This will save contractors and farmers time in the field and make ordering easier. There is space on board to store 10 rolls of film, meaning the operator can carry more than sufficient for a day’s work,” explains Kuhn’s baler specialist, Thomas Ferrand.
Unlike a fixed chamber baler, the VBP 3165 can be used for different forages in a variety of conditions. This should be of particular use in wet conditions where the chamber can adjust to account for changes in weight and forage type. “This provides operators with an option to work in poorer conditions and still lock in the nutritional value to make best use of forage,” he adds.
The VBP 3165 creates a tighter, more compact bale with better protection around the circumference of the bale. This oxygen barrier helps improve bale quality resulting in a bale with a higher nutritional value. The shape of the bale has also been adjusted to make it easier to handle and store.
Kubota
Kubota’s new high capacity BF3500 fixed chamber baler has been developed for use in heavy silage conditions. It has an 18-roller bale chamber, with two rollers located in the base of the chamber to give additional support with heavy, wet silage bales.
A new 2.3m wide pick-up, designated XL+ has also been introduced. Other upgrades include an extra tine which has been added on either side, increasing the working width by 10cm; a new five-bar tine reel incorporates a cam track located at both ends, while each tine bar is supported on four bearings. Tine length has been increased by 10mm and the gap between the stripper plates has been reduced for improved performance in wet crops.
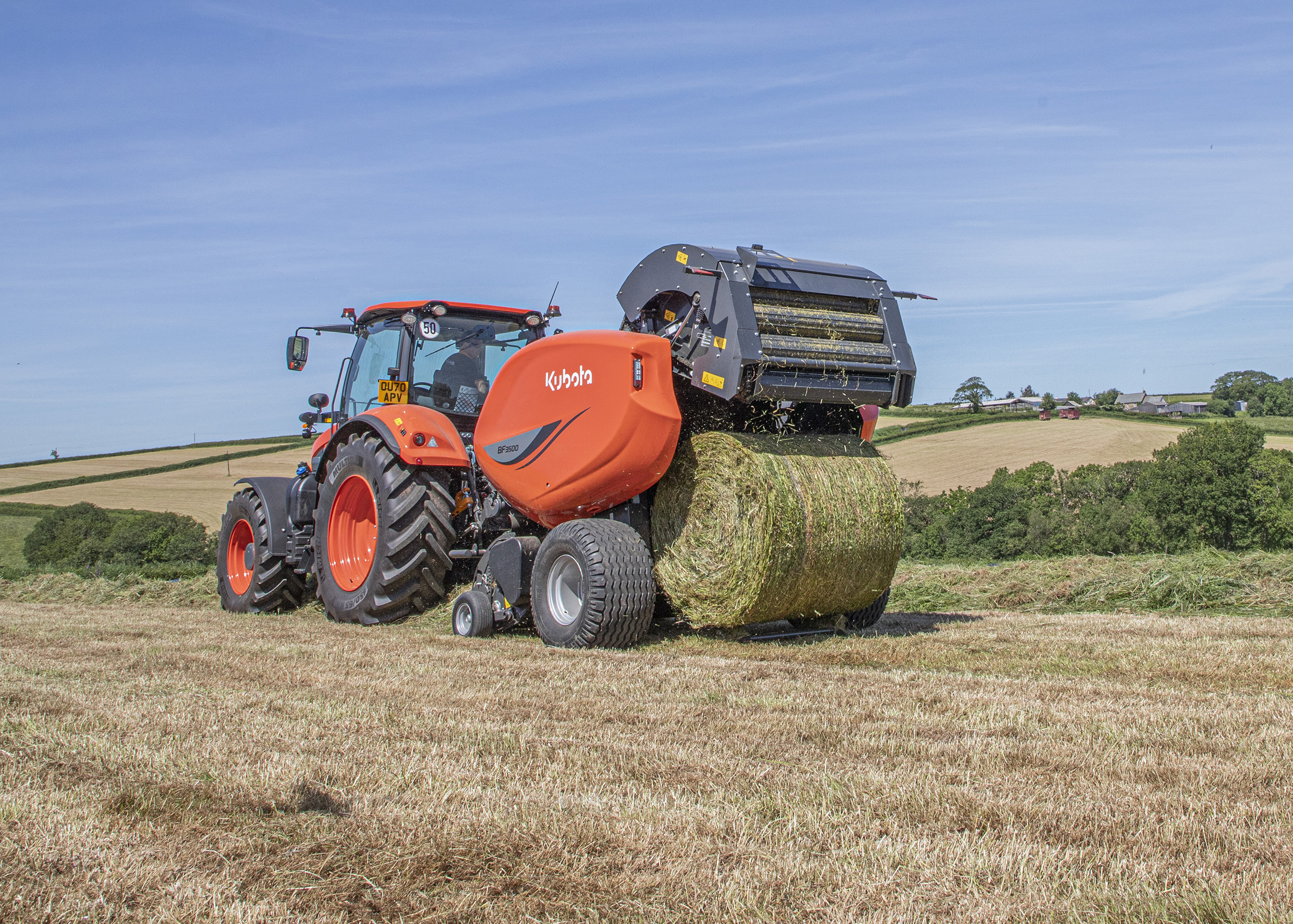
Kubota’s new high capacity BF3500 fixed chamber baler has been developed for use in heavy silage conditions.
Capacity has been increased with the introduction of a new larger diameter intake rotor, along with a revised drop floor system. The drop floor package uses a rounded profile under the rotor and operates with a parallelogram action – extending clearance under the front and rear of the chamber, when lowered.
Bales are tied using PowerBind net injection system, which should accurately place the tail of net directly into the bale chamber, without relying on traditional feed rollers or using gravity. The BF3500 incorporates heavy-duty bale chamber rollers and driveline components. This includes a split driveline, with the bale chamber and feed rotor featuring 3.18cm pitch drive chains. Chamber rollers all run on 50mm diameter bearings, with double-row roller bearings used on all main load points. Kubota’s BF3500 is also equipped with a 15-knife SuperCut pre-chopping system, plus automatic chain lubrication and auto-greasing.
Claas
Claas has reengineered its Quadrant square baler with a new HD pick-up with two cam tracks to increase output and durability. The design of the Quadrant Evolution should mean maximum torsional resistance and robustness.
The mechanically driven pick-up with five rows of tines and 18 double tines per row has also been tweaked to increase throughput and further improve raking quality. The extra row of tines allows the pick-up to rotate more slowly, while the speed of the Power Feeding System (PFS) roller has been increased.
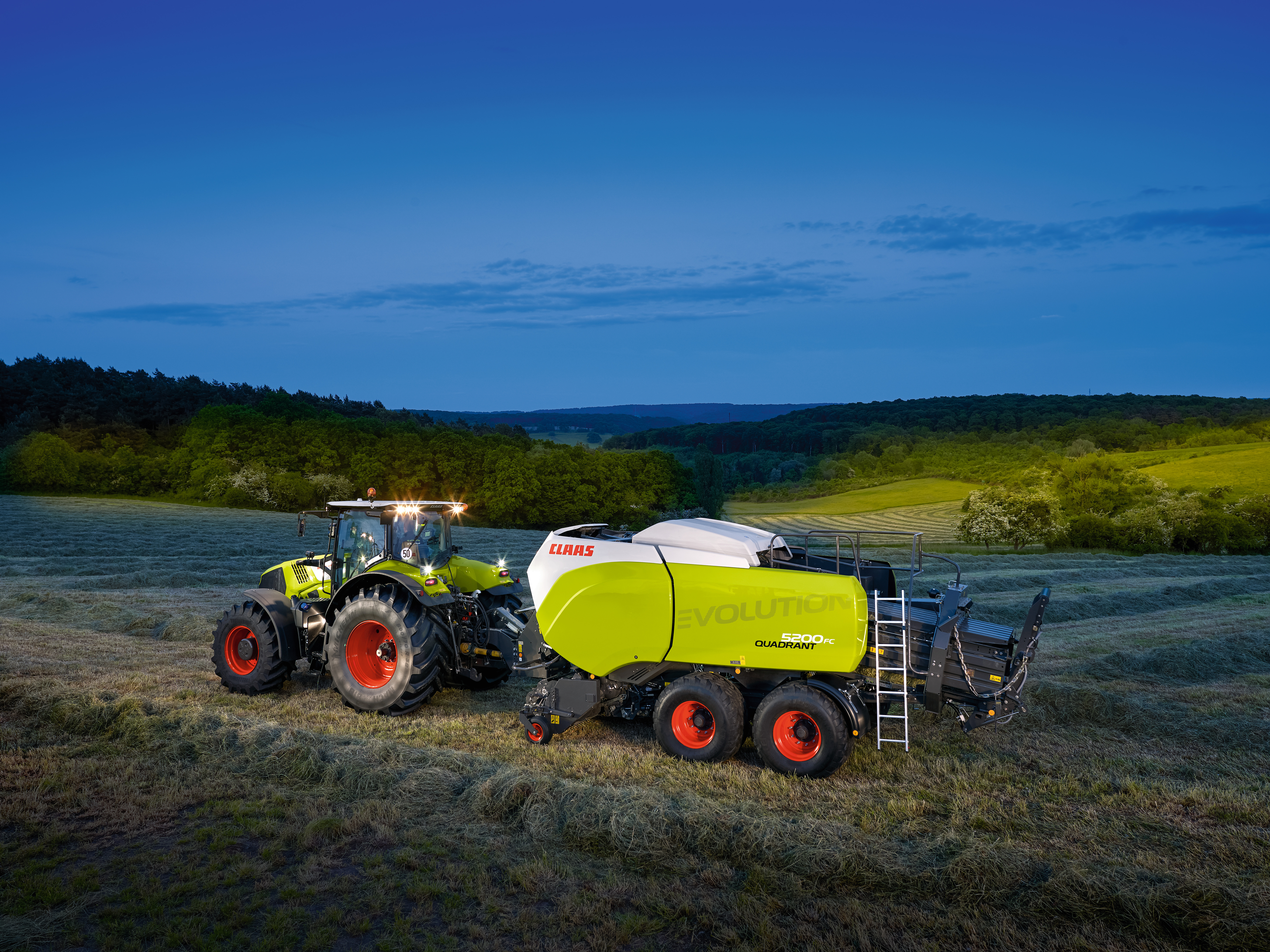
Claas has reengineered its Quadrant square baler with a new HD pick-up with two cam tracks to increase output and durability.
The feed roller has also been given extra paddles which can be removed when harvesting long-stalked crops. The spring mounted PFS feed roller compensates for uneven swaths. The overall objective of the innovations is to enhance raking performance and throughput while ensuring gentle, loss-free crop pick-up.
To handle the higher throughput volumes, the release torque on the friction clutch has been increased to 1600Nm and the diameter of the pick-up main drive shaft has been enlarged. Semi-automatic chain tensioning should ensure reliable pick-up drive and automatic lubrication and a 6.3-litre oil reservoir is available as standard.
The bale chamber’s top section now incorporates the header plate and the side panels have been redesigned and strengthened to produce a better bale shape and slightly higher bale density. Furthermore, factory-fitted side knives and deflectors are available to reduce material build-up in the ram guide area when baling straw, maize or sugarcane – further increasing operational safety and reducing the cleaning effort.
A new optional function allows the bale ramp to be opened and closed hydraulically from the cab. This function also enables the final bale to be ejected from the driver’s seat.
Cultivators
Claydon
Claydon has launched a new 9m straw harrow with working speeds of 15-25km/h which should enable it to create a micro-tilth in the top 30mm of soil, as well as to break up straw so that it decomposes rapidly.
The new 9m mounted version is aimed at bridging the gap between the 7.5m mounted and 12.5m trailed models, providing larger farms with greater flexibility and output, according to the company. It incorporates 75 double tines, each of which is attached to the frame by a unique fixing that enables it to pivot and absorb shock loads when working in stony conditions or turning.
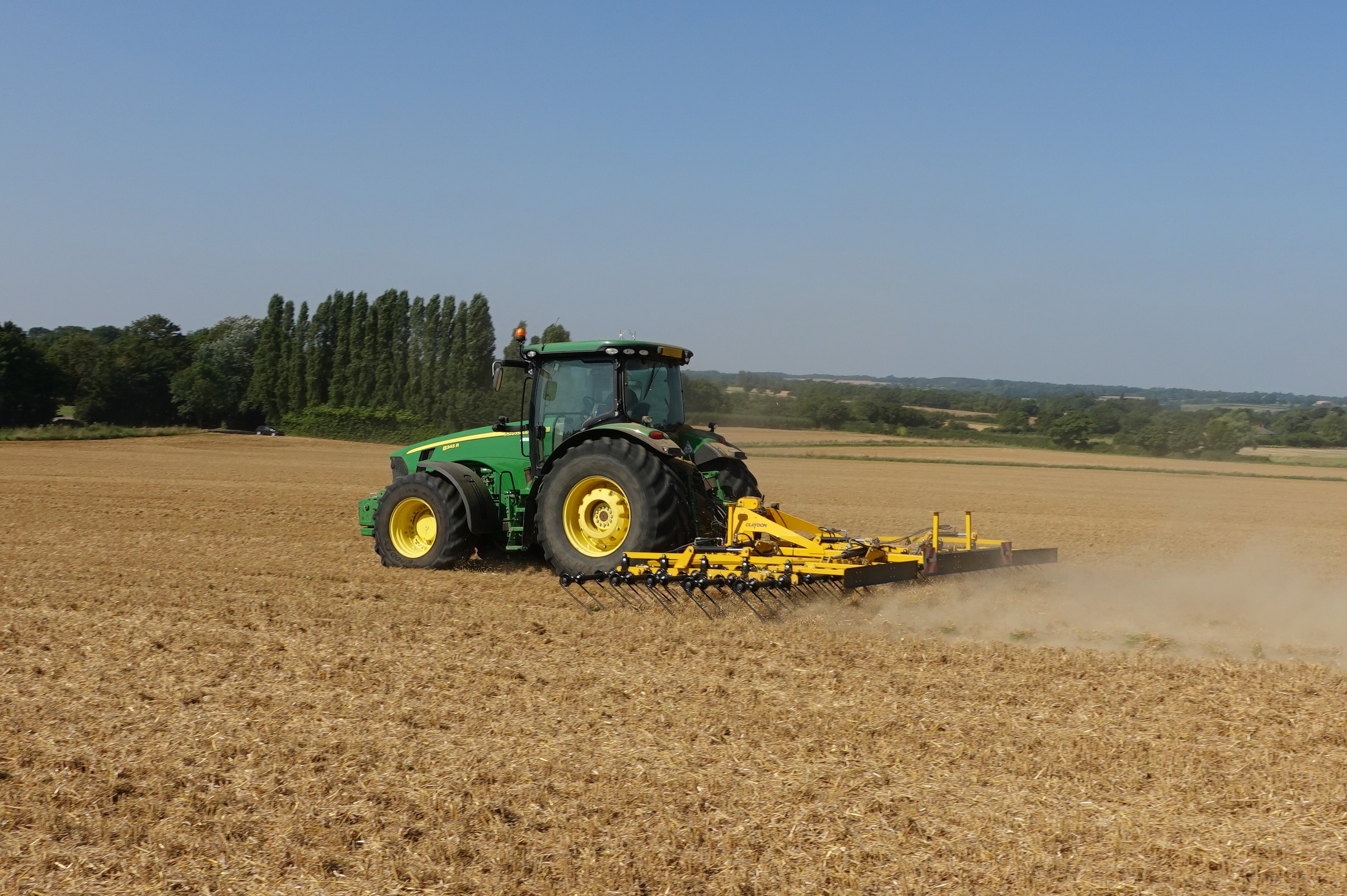
Claydon’s new 9m mounted version is aimed at bridging the gap between the 7.5m mounted and 12.5m trailed models.
The ‘wrap around’ design of the tines should enable high-speed turning on the headlands, which is designed to avoid leaving heaps of straw behind that interfere with subsequent operations or crop development. Tine angle is hydraulically adjustable from the tractor cab. Five rows of heavy-duty 14mm-diameter tines are standard, but 16mm tines are a cost option for very tough conditions.
Incorporating the same rugged design as other Claydon Straw Harrows, the 9m mounted version features a box section frame manufactured from high grade steel, while the wing pivot pins are greaseable and bushed to ensure a long service life. Twin hydraulic rams on each wing section enable them to fold vertically and remain level in work, so it should create a uniform tilth across the full width of the implement even when operating at speed.
The new model has minimum power requirement of 180hp and should achieve 12ha/h when operating at 20km/h. Weighing 1850kg and suitable for use on a Cat 3 linkage, it folds to 2.99m wide and 3.55m high for transport. Light boards and protection guards are standard.
Kuhn
Kuhn has announced a new 12m model has been added to its Optimer range. It’s the first 12m machine to feature the company’s Steady Control system which aims to maintain a uniform working depth, even at higher speeds and on undulating land, regardless of soil conditions.
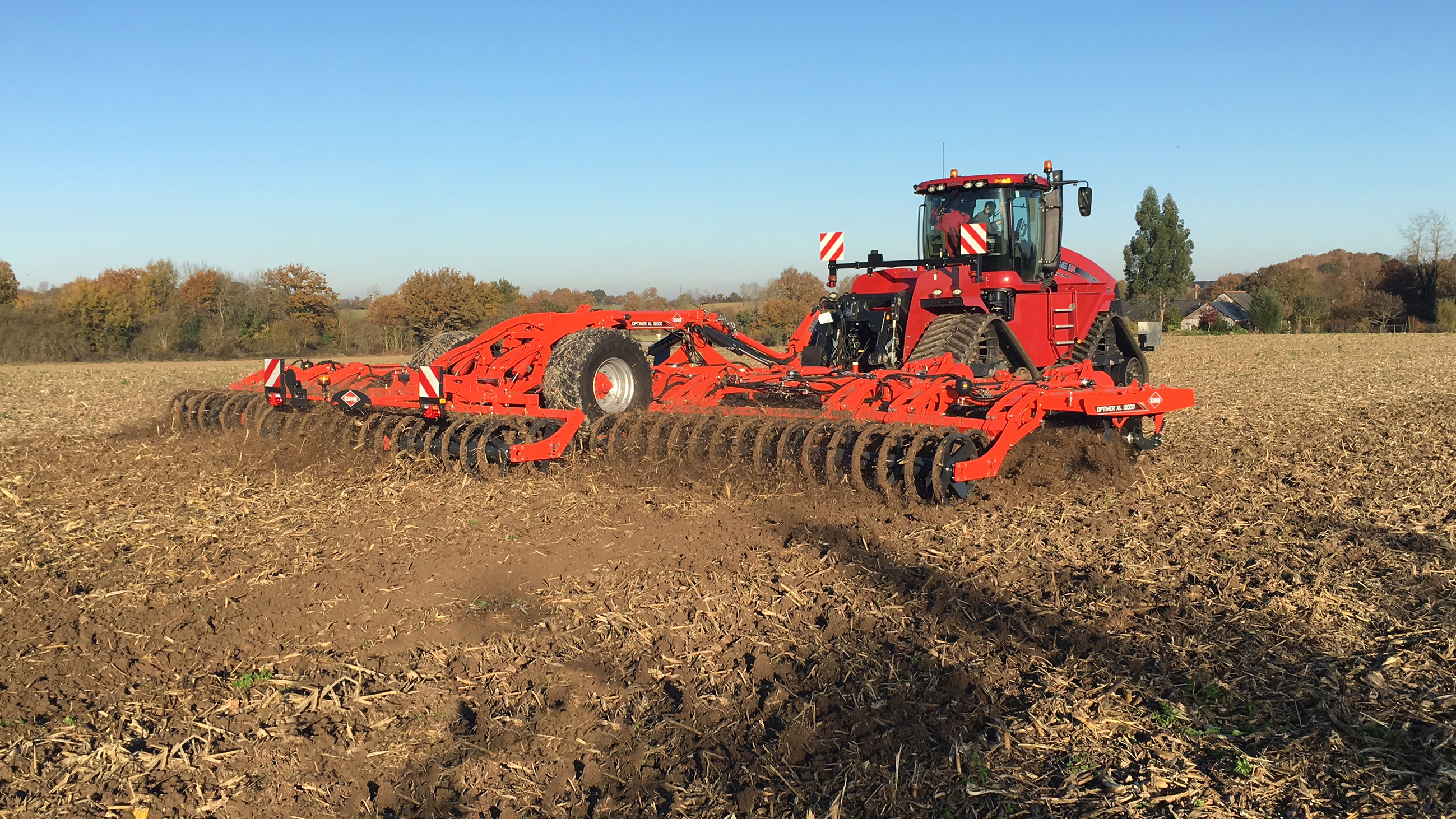
Kuhn’s Optimer XL is its first 12m machine to feature its Steady Control system which aims to maintain a uniform working depth.
“Steady Control exerts equal pressure across the full 12m width of the machine,” explains Kuhn’s Edd Fanshawe. “This means the discs all cut to an equal depth even when the ground is undulating because the Optimer compensates for ground contours by adjusting the ground pressure across the machine’s five sections.”
The 12m machine can also be run at up to 15 km/h whilst maintaining a consistent depth across the width.
The Optimer XL range is now available in mounted and trailed models in working widths of 3-12m wide. All models feature independent 620mm diameter discs which can work at depths of 5-15cm. When folded, the 12m model is just 3m wide and 4m high.
“All Optimer XL models are available with five different roller options. On the smaller width machines, a Kuhn SH 600 small seed drill with a 600-litre capacity hopper can be added. This enables stubble cultivation and cover crops or cereals to be sown in just one pass,” he concludes.
Väderstad
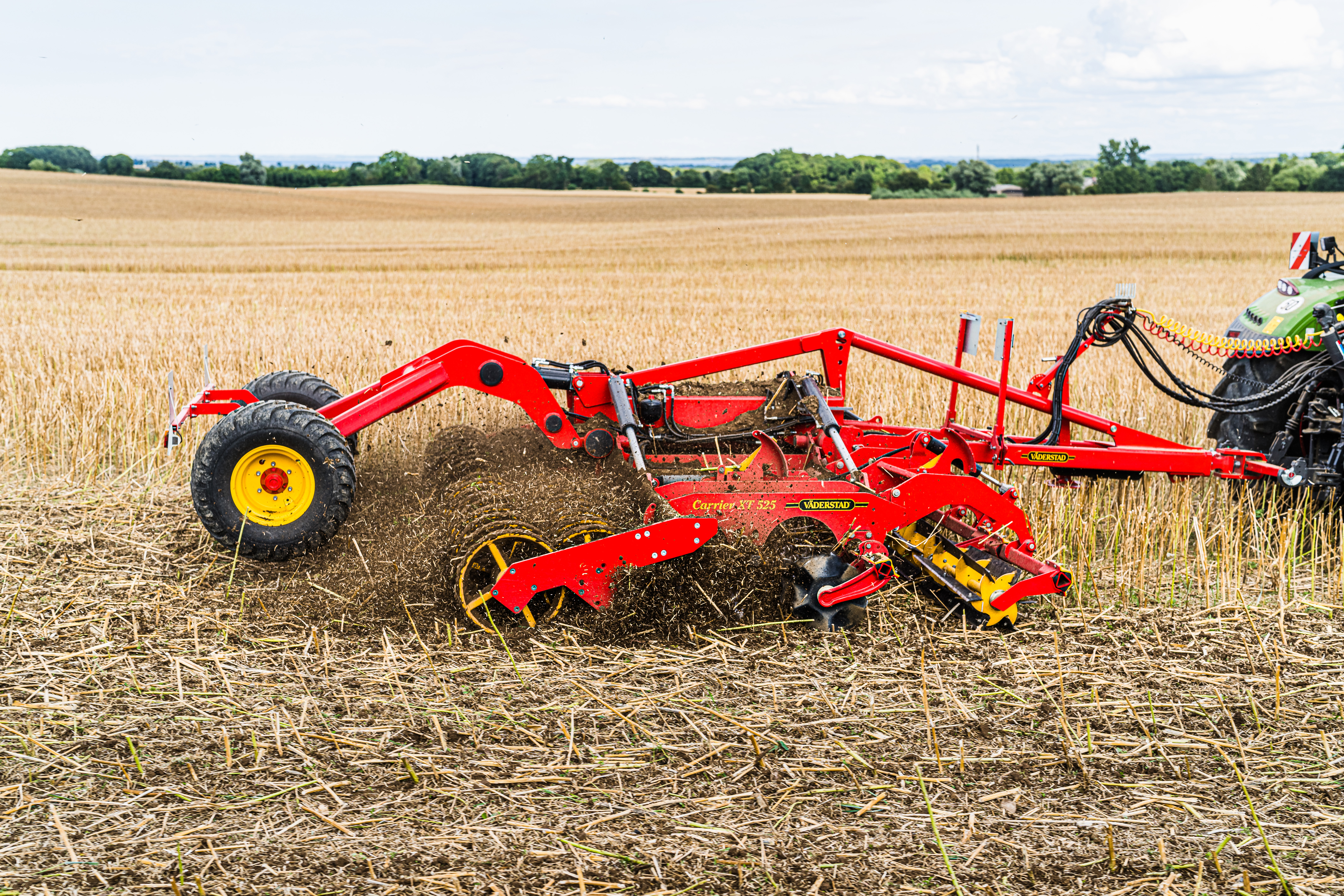
Väderstad’s Carrier XT disc cultivator is designed for high-speed primary tillage and seedbed preparation.
Väderstad has added Carrier XT to its portfolio of disc cultivators, used for high-speed primary tillage and seedbed preparation. Hydraulically rotating disc axles help to increase the disc angle towards the soil, so penetrability is maximised. This allows a full cut-out at a shallower working depth or reduced soil flow at deeper working depths. Both factors should contribute to lower diesel consumption.
The Carrier XT can either be fitted with the 450mm disc, 470mm TrueCut disc or the ultra-shallow CrossCutter Disc. Each disc is built from high-quality Swedish V-55 steel, ensuring a high wear resistance and long-lasting field performance.
The Carrier XT is available in three different working widths – 4.25m, 5.25m or 6.25m – and can either be delivered as trailed or mounted versions. All Carrier XT models can be equipped with a range of both single and double packer options.
This article was taken from the latest issue of CPM. For more articles like this, subscribe here.