Hands-free farming has come a step closer with a ground-breaking research initiative underway at Harper Adams University. CPM visits to find out what it aims to achieve and reports on two new precision agronomy services.
My remit is very much about proving the technology.
By Jane Brooks and Lucy de la Pasture
In a world first, researchers at Harper Adams University plan to grow a hectare of spring barley using robots, agricultural machinery and drones all controlled from a laptop base-station. People are forbidden, however – once the area is fenced off, no one will be allowed to set foot in the field.
According to project manager Kit Franklin the plan is to sow, grow and harvest the crop using readily available machinery, autonomous control systems and open-source technology. Equipment preparations are well underway and all the systems have undergone vigorous lab and field testing.
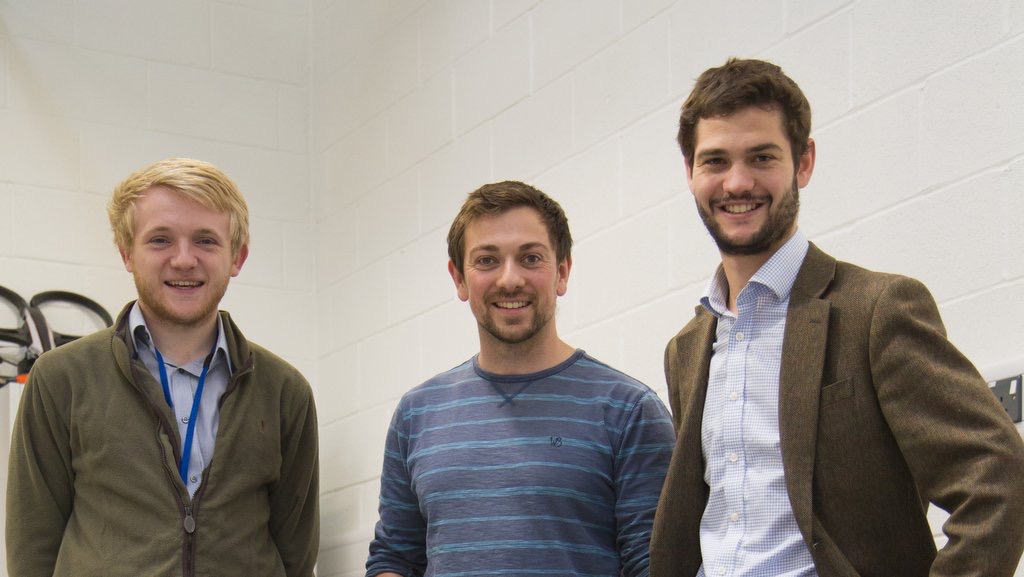
Martin Abell (left) from Precision Decisions has been assisting Harper Adams robotics researcher Jonathan Gill and Kit Franklin (right).
The single hectare plot has been chosen – it was sub soiled last autumn to get rid of old tractor track ruts and fencing is well underway. There’s just the small matter of applying the technology to the actual equipment for the task in hand, starting with a 40hp Iseki tractor.
“I’ve worked in this field since studying as an undergraduate, initially coming across agrobotics through Professor Simon Blackwell, here at Harper Adams,” explains Kit Franklin. “We had prototype robots trundling around but we wanted to put them to work in the field.
“People have experimented by automating parts of the process with many research projects going on across the world, but they’re snap shots. So far no one’s done anything like this over a complete arable crop cycle, which was the big driver for us. We aim to prove the technology by undertaking our own field-scale automation project here at Harper Adams, which is a world first.”
The project launched in Oct 2016 with early testing of the automation system on an electric all-terrain vehicle. They’re now on the next step, which is incorporating the system onto the 40hp Iseki tractor that’ll be used for drilling and spraying the crop.
“The tractor’s currently in the workshop having wires soldered and connected before undergoing various tests,” adds Kit Franklin. “We tested our systems on previous vehicles, so we know they work, but it doesn’t give us much time to get going as we plan to sow the barley towards the end of March or early April.
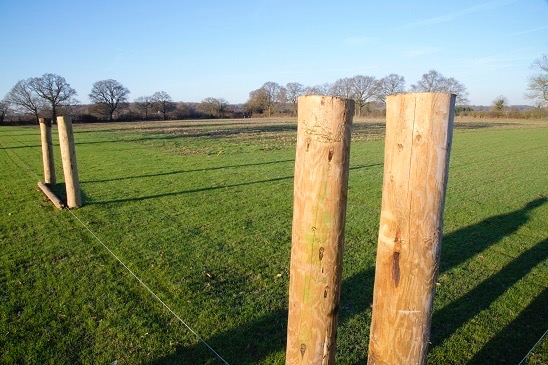
Once the fencing is finished, people will be forbidden and the machines will take over.
“The machines will be controlled via a laptop, using a system essentially adapted from drone technology. It’s similar to autosteer in that the tractor is programmed from the laptop to follow a pre-determined path. There’s no artificial intelligence in the machine, no decision making – it follows a pre-set course.”
A front-mounted sensor will monitor the route and stop the tractor if there’s anything in the way. “Agrobotics is a term that’s commonly used, but what we’re doing is more automation than robotics,” he continues.
“Our software comes from the open-source community so people all around the world are doing bits of coding and adding to it and the hardware is also developed from an open-source background.
“We’re not breaking new ground by writing really clever new bits of new code but using existing technology. I think in other places people are too caught up in developing from scratch rather than adapting what’s already out there.”
The project has received a great deal of support from within the agricultural industry. Iseki have provided the tractor and Linak have loaned the use of the actuators. Numerous other companies have either sponsored the project or come up with very competitive prices for items when they’re needed.
Precision Decisions of Shipton, York have been a strong presence in the agricultural technology market for a number of years, helping farmers integrate precision agronomy and new technologies into their businesses. Managing director Clive Blacker explains why he decided to get involved in the project.
“There’s huge enthusiasm for the project from the robotics team at Harper Adams. Kit Franklin and Jonathan Gill are two very bright lads working in the unmanned aerial vehicle (UAV) and robotics sector developing some of these prototypes. They’re the main driving force behind the project and our involvement is from the perspective of industry knowledge and staffing requirements.
“A lot of development is still needed to get the technology right. The business-scaling case is something we’ll be trying to understand as the project evolves. I think it’ll be a sharp but long-term learning curve to properly understand the scalability of autonomous field-based systems. But we’ll gain an insight into the production capabilities of this type of system, so we can be realistic with the figures when we’re looking at development opportunities.”
He believes two potential areas that may provide the biggest benefits are in reducing compaction and lowering cultivation costs. “There may be a lot of synergies and benefits by going with smaller machines. But the million-dollar question is obviously how many do you need and is it cost effective?”
Clive Blacker also explained that the project is purely an autonomous robotics evaluation and given the time limitations they may not able to give the cropping side the attention to detail they would like. “We did some basic hand scouting before being banished from the field, in terms of digging some soil pits and doing some penetrometer tests.”
The team will be using a vineyard drill, which fits the size of tractor and in common with larger drills will allow fertiliser placement with the seed. Remote-sensing drones will be used to monitor the crop, as well as N-sensor technology, so variable nitrogen rates could be applied.
“Along the way we intend to be as precise as possible – we have a very clever 6m sprayer with section control, but that’s a side issue. The key is whether we can do the process,” adds Kit Franklin. “I hope that it opens people’s eyes and awareness, and that they start talking about doing it for real.”
Although by no any means a commercial product, the hardware and electronics on the Iseki costs around £10,000 with the tractor itself in the region of £15,000. That makes the cost of a robotic system, including multiple small units, not really much different to buying a single, big horse power tractor, he points out.
“We originally planned to use a rice combine as they’re small, have tracks and are easy to control. But we’ve ended up with a Sampo trials combine that’s the size we wanted but not quite what we first imagined using. It’s on wheels not tracks and a little longer than we had planned, which makes our confined space a bit more of an issue compared with an Asian combine, but it should be fine.
“Obviously the work we’re doing is on one machine at the moment. But rolling forward, the whole idea is to have lots more machines of this size of 40hp or so out in the field working collaboratively and not crossing each other’s paths.”
Looking at future applications for the system, Kit Franklin believes there are parts of the world that would adapt to it far easier than we would here in the UK. “In terms of scale, our tractors are big – in other parts of the world they’re still farming with tractors that are 50hp.
“I was recently in India where it’s completely normal to farm with tractors around 50hp and they’re farming a huge area. Turkey is similar although their average tractor is about 65hp, but again lots of small tractors farm a very large national acreage.
“In these parts of the world using robotic small tractors isn’t that big a step. Also, places like Japan are facing huge problems with an aging farming population and no young people interested in farming. Just because these markets use small tractors doesn’t mean they’re opposed to technology. Actually, they’re possibly more receptive than we are and have a better infrastructure – they’re on 4G mobile communications all over the country in India, for example.”
One issue is safety, but Kit Franklin points out that in Australia, companies such as Rio Tinto operate driverless mining trucks in what is essentially a safe environment where they’re segregated on their own. The same thing could be done with tractors.
“In terms of the UK, I think that this kind of autonomous farming is the way of the future. It takes one man to drive a 200hp tractor and you could put him in charge of four autonomous tractors that do less damage and use less energy.”
Clive Blacker is already looking to the future. “I’d like to think that once we’ve proved the concept and fine-tuned the vehicles then perhaps we could look into a longer term project. Then we could really investigate commercialising it.
“In agriculture, we’ve continually battled to reduce our costs through scale by increasing the size of the horsepower of the equipment so we get more productivity from less labour. But equally that has a knock-on effect with machine accuracy because it reduces the precision we can actually apply.
“I honestly don’t think we’ve really started to precision farm at all properly yet. I believe opportunities are going to come to us at such a pace in the future that we really haven’t quantified them yet.”
Momentum builds for the digital drive
Sensors, software and computer modelling have been huge steps forward for agricultural processes, such as in matching fertiliser applications to crop needs. They’ve also enabled progress in agricultural research, particularly in areas such as plant health and growth.
Much of the data isn’t freely shared, however, as access to the results of big-data analysis by large corporations, as well as within the scientific community, is often restricted. But larger UK farmers, that have the available resources to gather the data, are more willing to exchange what they collect.
And the potential in agriculture is vast – huge amounts of data can be generated during crop growth. In the past, the cost of capturing data often outweighed the benefits. But technological innovations have led to a more favourable cost/benefit ratio, particularly when it comes to areas such as agronomy. Algorithms to interpret the data are also being refined, leading to better application of fertiliser, for example.
Adjusting to the jargon
Open source, broadly speaking, is shared software with the original source code being made freely available to anyone by the authors of the program. This allows the software to be redistributed, modified or enhanced by anyone with the knowledge to do so.
Source code is the list of commands in a piece of software that computer programmers can manipulate to improve, change or fix the way a program works.
Big data refers to the ability to examine and extract information from multiple sources. This has been made possible in recent years by more affordable technology developments and greater computing capability. Data storage and communication systems such as mobile phones and remote sensing have also enabled more data gathering to take place.
Farming focus for new drone package
Drone-assisted precision agriculture firm Drone AG has unveiled a new system that promises weather-proof agricultural data collection with support from “powerful” cloud-based farm management software.
The Storm Agri Pro is a robust rain and wind-resilient enterprise-level quadcopter that carries the latest sensors for agricultural remote sensing activities, claims the company. Data processing will be handled by software partner, Aerobotics, through its cloud-based platform, AeroView.
“While the data collected by drone systems can be extremely useful when assessing plant health and identifying weed growth, for example, we’ve experienced issues with the process of turning the raw data into useable on-farm information,” notes Hugh Wrangham of Drone AG.
“AeroView provides an intuitive and easy-to-use platform with analytics which simplify the process end-to-end and gives our clients the information they need to make better decisions on the ground.”
Built by Drone AG’s parent company in the UK, the hardware benefits from high-end components from leading drone manufacturer DJI. The UAVs can cover large areas quickly, says the company, even in adverse weather conditions, and feature dual batteries for up to 30mins flight time. Sensor options include Parrot’s Sequoia multi-spectral sensor, developed specifically for calibrated analysis of crop health and cropping defects.
“The drone system is designed to be versatile and robust, but also modular and easy to upgrade,” notes Hugh Wrangham.
Over the past two years, Aerobotics has worked with hundreds of farmers across South Africa and Australia to improve their yields and reduce costs, claims the company’s James Paterson. “We’ve designed our system to provide what we believe is the most user friendly platform currently on the market, packed with ground-breaking data analytics.”
Advanced data quality, ground-truthing, data interpretation and export capabilities retain the precision of the high-resolution information captured by the UAV and make it available for farm use, such as with variable-rate applications. This is supported by the AeroView platform that allows you to import and create field boundaries, upload UAV data, analyse it, add prescription rates and export field maps, all with just a few clicks.
Processing takes less than 24 hours, delivering results back to the grower that can be ground-truthed using a tablet or smartphone in the field or annotated with GPS precision. Data can be exported in formats directly compatible with precision agriculture machinery.
The drone systems are supplied in a package that includes a day’s training on safe and lawful flying, as well as how to use the systems to gather aerial data autonomously and subsequently analyse results in AeroView.
Prices start at £7200, including training and one month’s software and support. The enterprise software and support package costs £150/month, with 100ha of data processing included as standard and additional processing charged at £1/ha.
Omnia stimulates the mind
To Latin scholars, the name given to new precision farming system, Omnia, immediately conveys the ambition of those behind it. Omnia promises to be ‘all things’. But the big question is whether it delivers on its promise where so many systems haven’t succeeded in joining the dots of precision techniques to make sense of the bigger picture.
Hutchinsons’ agronomist and Nuffield scholar, Ben Taylor-Davies, describes himself as a bit of a maverick. He has a reputation for saying what he thinks and that doesn’t necessarily mean towing the company line. So when he says Omnia has impressed him, then the reasoning behind his statement is likely to have been well thought through.
“Precision farming is good for creating pretty pictures but as an agronomist, I need to be able to turn this into meaningful advice and if I’m not in agreement with the model, then I need to be able to over-ride the output,” he says.
The way Omnia has been designed allows for this. Different layers of information can be inputted, which may have been generated by other precision systems, such as soil or yield maps. They can even be built from using tacit knowledge of the farm, such as areas in fields where slugs are problematic or rabbits habitually graze, and manually inputted into the system.
This autumn, Ben Taylor-Davies convinced Andrew Troughton to put Omnia through its paces on his farm near Tewkesbury in Glos. Tredington Court is on heavy clay soil in an arable rotation of mainly winter wheat and oilseed rape, with spring beans and spring barley recently introduced to help with blackgrass management.
“We’ve been operating reduced tillage practices for the past 7-8 years in an effort to improve soil structure. The recent introduction of a new drill with the capacity to vary seed rate, raised the question of how to best utilise it – which is where Omnia comes in,” explains Andrew Troughton.
“We had historic yield maps from GPS systems on the combine as well as our own knowledge of the farm, so with Omnia we could use this and soil mapping to input a background for the system to generate a plan for variable-rate drilling,” adds Ben Taylor-Davies.
The farm started to produce yield map data in 2014, which revealed some areas of fields were very high yielding and some very poor, but like many farms the mapping data wasn’t really utilised for more than identifying possible problem areas.
For a farm business that’s new to precision technology, like Andrew Troughton’s, it’s best to concentrate on one area to see how it goes and identify a benefit before using more widely, suggests Oliver Wood, Hutchinsons’ Omnia technical manager.
“When RDS in the cab is a new experience, it’s useful to get a feel for it so that the technology isn’t overwhelming. Varying seed rates is the most important place to begin when looking at precision farming for the first time,” he adds.
At Tredington Court, Revelation winter wheat was drilled in the third week of Oct, after three stale seedbeds to help reduce blackgrass populations. In the past, a seed rate of 185-200 kg/ha would have been standard on the farm but using the Omnia system a much larger range of seed rates was planted this year.
“The lowest seed rates were 170 kg/ha, rising to 300 kg/ha in some areas so there was a much bigger variation. We’ve used more seed but hope to have more plants established and a better crop as a result,” says Andrew Troughton.
But the thing Ben Taylor-Davies most likes about his Omnia experience is that it makes him think.
“Omnia is about agronomy. It makes you consider the whole field and all the factors that may affect seed rate on this farm. The system filters all these factors, just as an agronomist’s brain would do every time they make a decision, but instead of an overall average solution, Omnia enables lots of different calculations to take place at the same time in producing a recommendation – enabling precision at the point of application.
“Most of all, I like the fact that I can still modify the recommendation produced by the system so that if I don’t agree with the recommendation or there are other factors to consider that aren’t already built into the layers of information Omnia is using, such as soil temperature or poor seedbed conditions, I can tweak the output.”