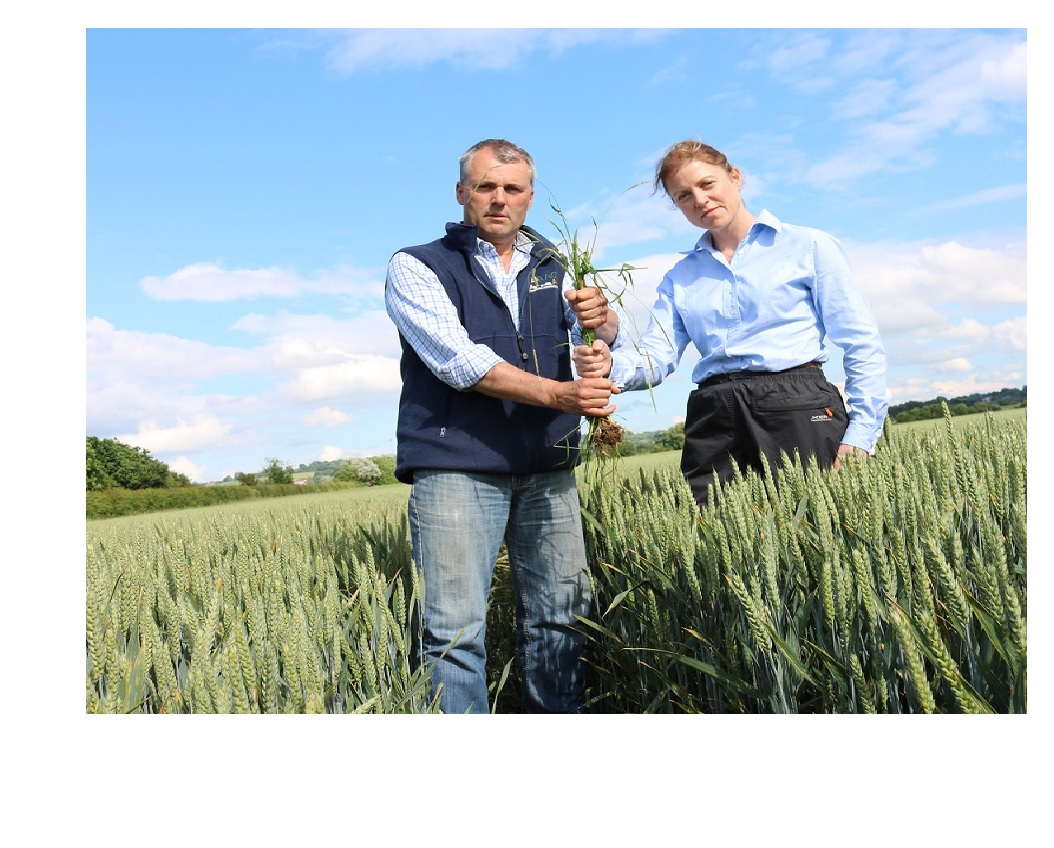
A zero-tolerance approach, meticulously costed and perfected through on-farm trials, has helped Lincs grower Andrew Ward get a firm grip on blackgrass. CPM visited to help pull some of the last few plants that remain.
Everything we do, every decision we make is driven by blackgrass. I eat, sleep and dream it.
By Tom Allen-Stevens
As you’re driven past the fields of immaculate spring barley and winter wheat at Glebe Farm, Leadenham, Lincs, looking earnestly for a blackgrass head or two to pull, an element of doubt begins to creep in. Has Andrew Ward been making a big fuss over nothing, or are you looking at the successful outcome of his zero-tolerance approach to blackgrass?
The well publicised piles of pulled blackgrass, the photos of sprayed-out patches and numerous reports of what he’s done to get this far suggest it’s the latter explanation that’s probably nearer the truth. “Everything we do, every decision we make is driven by blackgrass, whether that’s cultivation, rotation, choice of seed or chemistry. I eat, sleep and dream it,” says Andrew Ward.
Indeed, it was probably one of these dreams that resulted in his determination to take on what he sees as arable farming’s biggest threat, and beat it. “Every May, all I saw was the blackgrass as it appeared above our crops. Then we went in with the combine and the yield dipped to below half the field average as it met a bad patch. It was about four years ago I woke up one day and realised the only way to stop it was not to allow a single blackgrass head to go to seed.”
The farm covers around 650ha, with soil type ranging from heavy clay to sand over limestone on the Heath, above Leadenham. Spring barley (Odyssey and Explorer being the varieties grown) is now the farm’s biggest crop in the rotation, as a direct result of blackgrass. There’s also around 200ha of Vistive HOLL oilseed rape, 130ha of winter wheat (Evolution, Skyfall, Revelation and Reflection) and 42ha of sugar beet. Grass/flower margins and areas under environmental stewardship cover the rest of the acreage.
It’s a rotational shift, from 50-55% winter wheat to just 20% of the cropped area that’s made a massive difference to the farm’s ability to tackle blackgrass, says Andrew Ward. Wheat has been taken out of the rotation altogether on the very heavy soils, unsuitable for sugar beet, where two spring barleys now follow a crop of OSR.
Spring barley
“So many farmers say you can’t grow spring barley on heavy clays, but that’s because they haven’t tried it. Those that have and failed should take a good look at their cultivation strategy and soil management – I believe you can grow any crop on any soil if you put your mind to it,” he says. On the lighter loams where blackgrass is a problem, sugar beet alternates with OSR around the spring barley. Only on the heathland and fields where the grassweed is less of an issue does the wheat slot in.
“The secret to our blackgrass management is to create resilient soils, put them in a condition that will be easy to work with and leave us in charge and not the weather. So no matter what crop is planned, we go straight in behind the combine with the Simba Solo and cultivate the land when it’s dry. It’s then left for blackgrass to flush, that we spray off with glyphosate.”
The wheat is never drilled before 20 Oct. “If the weather isn’t right, we just switch to spring barley. It’s important not to force a crop in because successful blackgrass management needs a competitive crop and you don’t get that with mauling wheat in.
“I think many farmers are hung up on getting a good winter wheat crop in, but why re-crop bad blackgrass fields with wheat in the hope you’ll have a clean crop? All that achieves is a bigger problem to sort out in future.”
The cultivation routine ensures the Simba Freeflow can get on to the heavy soil to drill spring barley relatively early in the spring, says Andrew Ward. “Because the land is worked early, it goes into winter in a better condition – heavy land has a memory and will let you get on if it’s treated right.”
The approach to cultivations is taken carefully, and on-farm trials are frequently used to test the favoured strategy. “We’re trying some direct drilling, but just don’t get the same result. We’ve also tried cover crops, but the trial plots

Andrew Ward has resolved not to allow a single blackgrass head in his cereal crops go to seed.
had real problems. It’s not a ‘no’ – we need to do more work before we know how they fit in.
“But I never wanted to be the average Jo Bloggs farmer who did things the way they’d always been done. I’ve always had a drive to do something more.”
It started in 2001, when the farm shifted away from ploughing. A trip to Hungary opened his eyes to the Simba Solo. “Following harvest that year, we ploughed some land and tried the Solo on the rest. It was a success, and the next year we got rid of the plough and haven’t looked back.
“At the time, the agronomist was horrified – the prospect of establishing sugar beet without the plough really was radical, but the difference it made to cultivation costs was staggering.”
And it’s Andrew Ward’s keen grasp of costs that drives many of the business decisions he makes. “It stems from a spreadsheet-based system that Bill Basford of ADAS introduced me to. We were trying to work out how to move from a steel-tracked crawler tractor to a modern rubber-tracked Challenger. The spreadsheet was a brilliant way to allocate the costs, so I’ve modified and developed it and still use it today as a tool to plan with.”
Every machine is costed out carefully and every pass it takes through each crop is allocated meticulously, from fuel use to share of insurance and office overheads. These are figures that are constantly referenced and never too far from Andrew Ward’s side – many are quoted from memory.
“Tightly monitoring costs is not something that’s easy to do. I’m lucky that I have very capable farm staff who are involved in the business, know as much about the costs as I do, and appreciate the value it brings to the farm operations.” This includes the main arable operator Ian Stubbs and Andrew Ward’s son in law Eoin Gallagher.
Out of control
But blackgrass was one aspect of the business that he could feel was slipping out of control. “By 2010, we realised Atlantis (iodosulfuron+ mesosulfuron) was only taking out half of the blackgrass it should be controlling. It clearly
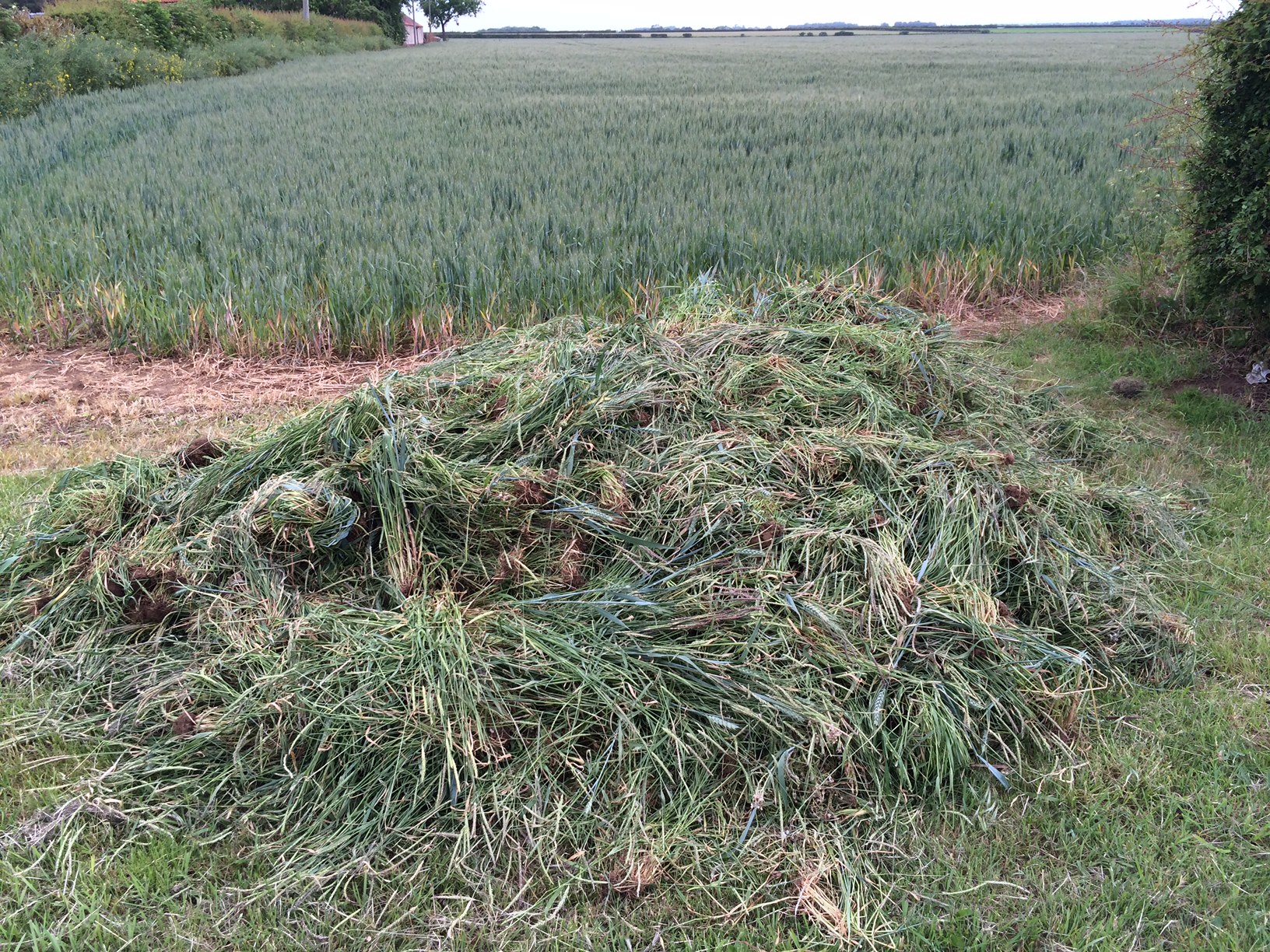
Pulled blackgrass is heaped on the field edge and disposed of.
wasn’t application error – the chemistry simply wasn’t working.” The grassweed was also knocking serious holes in the farm’s five-year average wheat yield of 10.2t/ha.
“I’d seen what others had managed to achieve in reducing blackgrass on heavy land, especially in Agrii’s blackgrass trials at Stow Longa, however. So in 2012, we took the decision to pursue a zero-tolerance approach, that didn’t rely on chemical control – we’d use every means available to prevent any blackgrass seeding into the crop.”
It started with 40ha of wheat that was cut wholecrop for a local anaerobic digester. In addition, 31ha were sprayed off with glyphosate. “Over the years since then we’ve reduced the amount we’ve had to spray off – 38ha were taken out in 2013, 10ha in 2014, 3ha last year, while we’ve only sprayed off 2ha before harvest this season.”
Every acre that isn’t sprayed off is hand-rogued. A local labour provider supplies a nine-strong team of Latvians and Lithuanians who pass through the crop and pull the blackgrass.
“It’s so important this is done right, and it’s a time-consuming job managing them. Every day they come, we meet at 7:00 and I spend time getting them started and making sure they know what they’re doing and revisit them a few times in the day. It’s a God-awful job, so you have to look after them and keep them in the right frame of mind,” notes Andrew Ward.
The team stays in a line and covers one 32m tramline at a time. “It’s important they’re not too far apart in the field – there was one team that wouldn’t stay in line and kept missing plants, so I had to let them go.” All blackgrass plants are removed to the side of the field from where they’re taken away and disposed of. While some of the crop is trampled down in the process, most comes back up, so damage is negligible, he adds.
The team costs around £750/day and work rate depends on burden – this year 4ha was cleared in as little as two hours, while the worst 6ha took 14 hours to cover. But unsurprisingly, this has all been costed out and, argues Andrew Ward, works out at remarkably good value for money.
“The average cost is £54/ha, although there may be one or two fields that may need a repeat pass. It varies from the best field at £38.50/ha to the worst at £186/ha. On top of that, there’s the cost of the pre-emergence herbicide at £60/ha and on average, 2.5 applications of glyphosate between crops at £20/ha. That’s a total herbicide bill of £80/ha, including application costs.
“What you save is Avadex (tri-allate) at £42/ha, including application, and Atlantis at £41/ha. So the total cost where we’re hand-rogueing is £134/ha, while continuing with chemicals alone would cost us £163/ha. What’s more, my blackgrass control bill comes down each year, along with the blackgrass populations, but how many growers with blackgrass can say the same about their herbicide bill?” points out Andrew Ward.
How to be an on-farm innovator – Andrew Ward’s top tips
- Keep an open and enquiring mind. Don’t accept everything you’re told as gospel, especially if you’re blankly told a particular new practice you’re considering won’t work.
- Do your own farm trials. It’s crucial to set aside an area on your own farm where you can try something out and learn how something new might fit with your own farming system.
- Learn from others. Take advantage of farmer groups, events, open days and get togethers to find out how others are getting on, being wary to keep point (1) top of mind. There are plenty of opportunities available, and it’s worth looking for like-minded growers – positive people who have a similar outlook and view on farming practices as yourself, with whom you share ideas.
- Know your costs. This is essential, and don’t use ‘industry standards’ as there’s no such thing. You cannot start to know the potential of a new practice or idea until you’ve fully costed what you’re doing at present and made reasonable projections on the difference it could make.
- Involve your staff. Bring them with you through every step of the journey so they understand what you’re aiming to achieve and encourage the free flow of ideas and suggestions through regular staff meetings. Someone who feels part of the farm, rather than just working for it, will be more self-motivated and less likely to cut corners.
- Put your head above the parapet. Never be afraid to speak out on something you believe in, to share your ideas, or promote your experiences. This includes the media – never turn down an opportunity to feature in articles, speak on the radio and TV because this is the best way to promote agriculture to the public. If you’re seen to interact with others, you generally get more useful information back than you share.
7. Cultivate contacts and nurture networks. Forming close links with manufacturers and suppliers can offer opportunities to be at the forefront of best practise and new technology. They are always looking for farmers to be involved in their R&D programmes.
A dogged determination to hit a defined target
Knowing what blackgrass costs his business and having those figures to hand are what stand out about Andrew Ward, reckons BASF East Midlands agronomy manager Ruth Stanley.
“To know those costs so well is unusual, but it gives Andrew a solid basis on which to form his plans. The other impressive aspect is that he’s really taken the bull by the horns – he’s set out a bold, zero-tolerance plan and he’s stuck to it doggedly. You only have to look at his crops to see that it’s succeeding,” she notes.
There’s a determination to succeed, too. “Andrew’s someone who clearly takes pride in what he does. He sticks to his guns and he’s not afraid to put his head above the parapet – in fact he welcomes it. It’s that mixture of pride and determination that’s truly progressive.”
Any bold, progressive plan carried out on farm needs a solid foundation, points out Ruth Stanley. “The real strength here is knowing your costs and using that as the basis on which to build a plan. You then need the determination and strength of character to make that plan succeed.
“But most of all, to effect change, you have to be prepared to do something different – try things out on farm and learn from the mistakes to develop a system that works.”
And Ruth Stanley has first-hand experience of this on her own 400ha farm at Harby, Leics, where for the past three years she’s run a series of blackgrass control trials for BASF. “Initially we were looking just at chemical control techniques, aiming to identify the best regimes. We found one that delivered 95% control on our highly resistant blackgrass. But it came with a heavy price tag.”
So the trials are now focused on combining chemical with cultural control techniques. “The aim is to make the chemistry work harder,” she explains.
“The big wins we’re finding are ploughing, which reduces the seedbank, and late drilling, including spring drilling, followed up with a robust chemical programme.”
That’s built around flufenacet, which has good activity on grassweeds, partnered with pendimethalin for its long-lasting residual activity, she continues. “But we’re not afraid to spray off areas where control has failed – the focus in the trials this year was barley, and one area had 302 blackgrass plants/m², for example. The seed return would have been 604,000 seeds/m² – even in a farm trial you can’t afford to let that happen.”
On-farm innovation
Farmers are constantly innovating to improve their businesses, which is why BASF is committed to investing 10% of its sales revenues into R&D to deliver new technologies for farming. BASF’s new innovations include pioneering agricultural chemistry, as well as Innovations Beyond Crop Protection like biologicals, bacteria, soil and water management and renewable technologies. Our future is firmly focused on delivering towards farming’s future.’