A group of UK arable farmers visited the BASF facilities in Germany and a couple of arable farms nearby to gain a different perspective on the industry. CPM accompanied them.
We plant nearly every day of the year.
By Tom Allen-Stevens
When you arrive at the centre of operations for the Renner vegetables business, near Mannheim, south of Frankfurt and just west of the Rhine, you wonder whether you’ve stepped into a busy European bus terminus. The place is teeming with Eastern European workers filing off coaches and registering at the reception, and fork-lifts weaving to and fro with crates of freshly packed leeks.
Just 15mins down the road lies the more peaceful BASF Rehhütte farm estate at Limburgerhof, with 480ha of what may be considered a more standard arable cropping mix of winter wheat, rye, corn, sugar beet and oilseed rape run by two farm staff. The two farming businesses share much the same soils – generally loamy sand ranging to clayey loams typical of the alluvial deposits around the Rhine. So what’s taken the two farms in such different cropping directions?
Farming practice
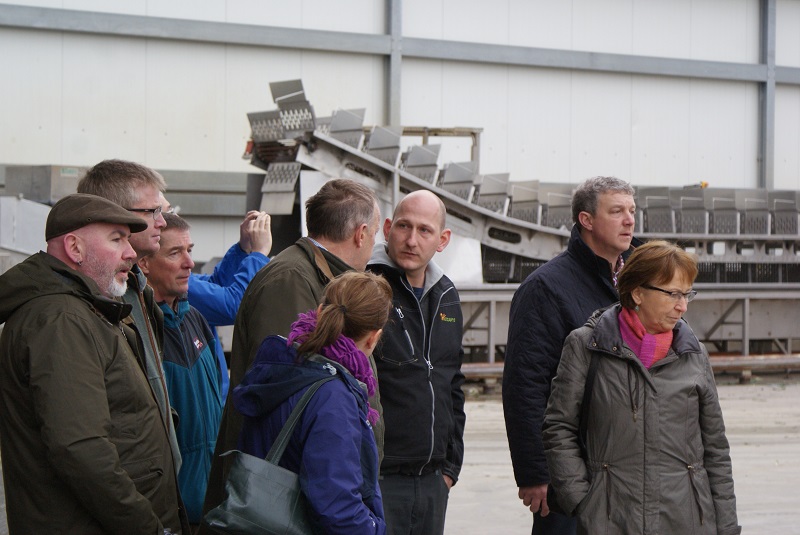
The tour of the Renner vegetable business was an opportunity to get an insight into the challenges facing a German farming business.
The visit to the farms is part of a study tour, arranged by BASF and undertaken by five arable farmers from around Grantham in Lincs. Having spent the first day looking round the BASF research and manufacturing facilities at Limburgerhof (see panel on pxx), it’s now time to see how farming is put into practice nearby.
And it’s clear that at Renner, the 1000ha of land the business has within a 30km radius are farmed to their maximum cropping potential. Onions, sweetcorn, carrots, radish, asparagus, celery and potatoes join the leeks currently being washed, packed and wrapped.
“We plant nearly every day of the year – Nov and Dec are the only months there isn’t a crop going in the ground,” explains arable operations manager Stefan Ossen. “This means we double crop, so we effectively grow 2000ha of vegetables.”
But average rainfall in the area is 450-480mm a year, and this year was just 300mm. “Every field is irrigated – 80% of this are pipes laid in the ground,” he reveals.
The soil’s lifeblood
It’s clear that water is the lifeblood that releases the potential of this soil, and with the best land in the area achieving up to €2000/yr (£1576) rental value, it gives you an idea of the returns growers can expect. “20,000ha in the area can be irrigated – it’s a problem when we all need water at the same time, so farmers work together to even out demand.”
There’s a regional cooperative that takes 80% of the produce, with the remaining 20% exported mainly to Russia, England, the Netherlands and Italy. This is planted, cared for and harvested using a fleet of 50-60 Fendt tractors (Stefan Ossen isn’t entirely sure of the exact number the business owns).
“The Fendts are comfortable and easy to operate, which is important on a large unit with many staff. But only our most skilled workers operate the big machines,” he says.
There are 80 full-time staff, with 800 seasonal workers coming mainly from Romania and Poland. They live on site in a “village” of purpose-built cabins, each accommodating two people. “It’s very important to provide a high standard of living accommodation – we have an 80% return rate of seasonal workers,” points out Stefan Ossen.
As well as harvesting, planting and helping on the packing lines, there’s a fair degree of hand-weeding they carry out. “We can’t afford any pesticide residues, so it’s often easier to weed by hand. We employ a third-party contractor to take and analyse the produce daily.”
It’s a remarkably different set-up at the Rehhütte farm estate. Dirk Wendel, the farm manager, has just one other full time member of staff. “We’re employed by BASF, but don’t carry out any research work here. It’s run as a commercial farm unit, and we set ourselves challenging economical and ecological objectives.”
One of the challenges is actually getting to the fields themselves – the farm is scattered over 32km from Limburgerhof to Frankenthal, north of Mannheim. “Every machine has to be big to take the volumes we need to transport,” says Dirk Wendel. There’s a 9t Amazone ZG-TS Profis spreader and 4000-litre self-propelled Pantera sprayer, supported by a 12,000-litre bowser.
But it’s water that’s the limiting factor for the farm, and 2015 was a dry year. “The oilseed rape performed well, but the wheat was very variable – the good land achieved 10t/ha, but we only managed 5.5t/ha from the lighter soils.”
He aims for a quality milling sample. In Germany, there are two main grades: A-wheat at 13.5% protein and B-wheat at 12.5%. There’s also E-grade wheat at 14.5% protein, with premiums currently around €10/t (£7.90/t) for A-wheat and €20/t (£15.80/t) for E-wheat.
Late application
“We start in March with a blanket nitrogen dressing of 30-60kgN/ha, going later with less if the crop is looking forward. There are then two further dressings put on with the N-Sensor at an average of 60kgN/ha. Then we’ll aim for a late application at booting, but it’s a big problem to get that right, especially if it turns dry.”
The wheat receives only one or two applications of fungicide. “Two years ago, we needed a third spray because of yellow rust, but in dry years, often just one application will do, although with corn in the rotation, we have to watch for fusarium.”
He chooses varieties with a good disease score and then, if disease is seen early on, the T1 spray is brought forward to GS30. “But that’s rare,” says Dirk Wendel. “Equally, if it’s a low disease year you can go a little later than GS39 with the T2 spray.”
And his choice of product at T2? He smiles: “Always Adexar (epoxiconazole+ fluxapyroxad). That’s not because I’m a BASF employee, but because it’s genuinely the best.”
The main emphasis in OSR is to build a good taproot in the winter, aiming for a hardy plant to weather the winter. “It gets an azole for phoma in the autumn and usually another in the spring with some growth regulation. One year in three we’ll get a problem with sclerotinia, which is why we’ve extended our rotation, and we also make a fungicide application at flowering.”
He holds off applying fertiliser to the OSR until the end of April, and then uses the N-Sensor to determine the rate. “Our average yield is above 4t/ha, although we achieved 6t/ha two years ago,” he says.
“You only need 140-160kgN/ha for rye, and that’s split two or three times and applied with the N-Sensor. The main disease is brown rust, that usually comes in after GS39, which is when you’d usually apply a fungicide.”
Biological boost for OSR dressing
A combined chemical and biological seed treatment for OSR could come to the market as soon as two years from now, according to Dr Annette Schuster, of the seed technology team at BASF. A new seed solutions technology and biologicals centre is due to open at BASF’s research facilities at Limburgerhof later this year.
“We’re in the process of submitting a dossier on OSR treatments – both fungicide and insecticide – that combine biological with chemical solutions,” she reveals. “It’s a very exciting prospect – we know they work, but we’re not sure what the regulatory journey will be like.”
It’ll be a new development for BASF’s Functional Crop Care division, that took a major step forward into biological solutions with the purchase of British company Becker Underwood in 2013. A number of inoculants are already on the market, while in 2015, BASF launched Xanthion, an in-furrow fungicide for corn that combines pyraclostrobin and the bacteria Bacillus subtilis.
“Against disease, biologicals are useful because they have an effect on a broad range of fungi. They’re not as effective as chemistry, and shouldn’t be seen as a replacement. But combined with chemical solutions, they can add efficacy and help resistance management.”
The company is now putting a significant resource into this area of novel pesticide solutions. BASF is the largest chemical company in the world with a turnover of €74bn. Although crop protection makes up just 7% of that, it takes 27% of the R&D budget – or around €500M. “If you add biotech, that’s more like a third of the budget,” says Annette Schuster.
However, bringing a new product to market costs around €225M and takes a good 10 years. “We start with pre-screening some 140,000 compounds and take these forward to 1000-2000 that may reach the greenhouse,” she explains.
At Limburgerhof there’s an impressive 12,250m² under glass across the 40ha site, with 1700 staff developing new products. Much of the initial screening work is now automated with robots, that can sift through 70-80,000 active ingredients per year. But it’s the final registration that proves the biggest hurdle of the process, says Annette Schuster.
“Environmental studies take one third of the development cost. A dossier submitted for registration may be thousands of pages long, but the efficacy part is just 20-30 pages.”
Once a product goes into production, that’s when BASF’s facility at Ludwigshafen rolls into play. This is a vast chemical works, spanning an area of 10km² just west of Mannheim on the Rhine. There are 213km of railtracks and a staggering 2800km of above-ground pipelines ferrying product and raw ingredients around the site.
Regulation shows its hand when it comes to packaging the products. For 140 crop protection products formulated on the site, there are 1100 different packing materials and 17,100 different product labels to manage. Packaged product is then taken to the site’s logistics centre and carted out worldwide at the rate of one million pallets/yr.