A switch in its cultivation strategy is helping a Warwicks farm business overcome its considerable blackgrass problem. CPM finds out.
If we could sell blackgrass we’d make a fortune.
By Rob Jones
The economics of farming generally ensures most arable enterprises operate within tight margins. Where the problem of resistant blackgrass exists, it presents a plethera of other challenges on prudent use of proven cultivation practises.
Farm manager Jamie Orpwood of Faccenda Farms near Milton Keynes was well aware of the problems that he faced when he took on the farm a couple of years ago, but relished the challenge.
The farm comprises mostly Hanslope clay soils which support a predominantly cereals-based rotation, including winter wheat, oilseed rape and spring/winter barley. Some permanent pasture supports a small suckler beef herd and red and fallow deer. The farm also follows ELS and HLS environmental schemes.
All cereals are grown for feed and the five-year yield average for winter wheat is 9.6t/ha and barley and oilseed it’s 8.6t/ha and 4.0t/ha respectively.
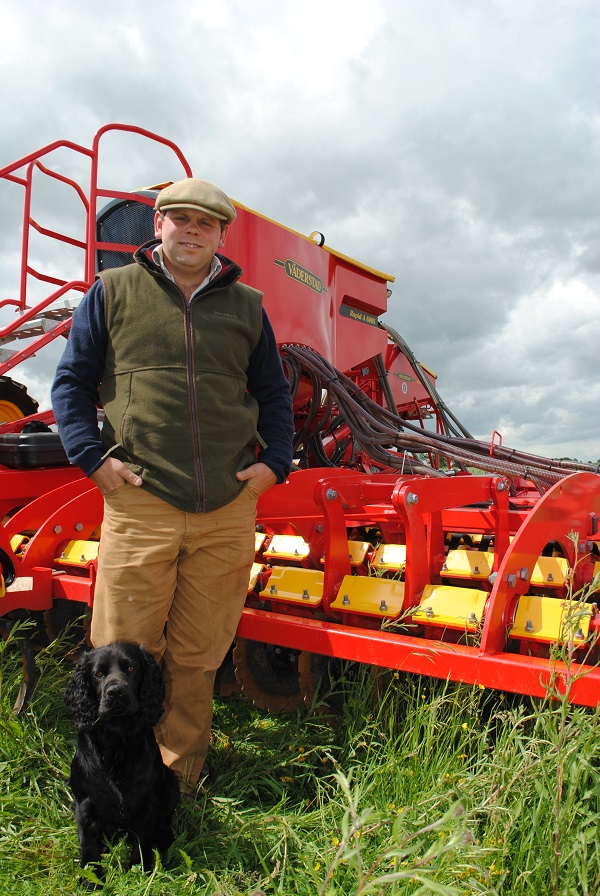
Jamie Orpwood’s approach to blackgrass has included introducing spring cropping and utilising cultural control options more effectively.
“If we could sell blackgrass we’d make a fortune,” says Jamie. “Herbicide options that we still have in the armoury have become less effective, while the weed seed-bank continues to rise.”
His approach to the problem has been to introduce spring cropping, utilise cultural control options more effectively, and to rely less heavily on a dwindling herbicide armoury.
“Blackgrass can take the whole crop out in a worst-case scenario and so in some situations we’re now growing back-to-back spring crops. Over the next 10 years the whole farm will have been double spring block-cropped,” he explains. “We’re also stretching the rotation out as much as possible so that we can introduce more effective cultural control, but at the same time keeping as much of the farm down to wheat and OSR because that’s where our profitability comes from.”
The previous management strategy was based on deep-tine cultivations followed by stacking pre-emergence herbicides and a full post emergence programme. Early drilling was also perceived to be the best approach to maximising yields. With the prudent use of glyphosate and an extended cultivation period – by delaying drilling for up to three weeks – Jamie has already seen a dramatic reduction in blackgrass across the farm.
Last year, the farm’s main cereal drill was up for replacement and a number of options were demonstrated including a 3m pneumatic Sky EasyDrill and a 6m Väderstad Rapid cultivator drill.
“We had a 4m Rapid on my last farm as well as a KRM Solo and a Kuhn drill,” he says. “I liked the Rapid best because of the seed placement accuracy even at speeds of up to 12km/h. The advantage of the other drills is that they’re lighter than the Rapid so they’re more suited potentially to later drilling, but a heavier drill gives better consolidation and on our land where slugs are a problem in OSR, this is a major advantage.”
Impressed by seed placement and the work load of the Rapid plus its ability to produce a seedbed, a new 6m RDA plus BioDrill arrived on the farm in time for autumn drilling last year.
“The Rapid is excellent at consolidating the seedbed after the seed has been placed evenly across the whole working width of the machine,” says Jamie. “Good seed placement is the key, so the Rapid’s ability to alter seed depth on the move ensures that seed is always placed where there’s moisture. The BioDrill is to be used for applying slug pellets and Avadex (triallate).
“The new drill is far more refined than the previous model,” he says. “The fan has been moved from the drawbar and is now integrated as part of the tank, which improves drill access and visibility. Redesigned steps provide access to both sides of the drill from the front.”
Even the calibration action has been thought about he says, so it’s now much easier and therefore faster to attach the bag. “We also like the remote iPad which means the operator can leave the cab but still have remote access to the functions. Sealed bearings reduce maintenance and downtime.”
Machinery purchasing decisions are made jointly with drill operator Barry Davies.
“It’s the drilling speed without compromising seed depth that puts the Rapid above all others,” he says. “I’d never used one before and so going from an old style cultivation drill originally and then to the Sky EasyDrill and finally the Rapid has been a massive but very positive change. The Rapid is easy to operate considering its level of sophistication. It works best in a well consolidated seedbed, but a forward speed of 18km/h isn’t a problem for it.
“Adjustments to maintain seed depth are easier compared with other drills,” continues Barry. “On the Rapid there’s a central ram which adjusts the whole section in one go. On some drills it can take at least 20mins to set up and then you’d have to go and try it, compared to only a few minutes with the Rapid which is then ready to go.”
The farm still employs Simba kit and a Cousins V form predominantly, but Jamie is looking to replace all his cultivation kit with Väderstad machines in line with the company’s replacement policy timescale.
To establish OSR behind barley, the stubbles are cultivated after harvest with a Cousins V Form deep tined cultivator to help incorporate chicken litter before consolidating with a Väderstad roll. The land is left to green up before spraying off with glyphosate and then drilling. Time from combining to drilling is normally about three weeks and the aim is to drill up to 70ha/day.
Cultivations prior to drilling winter wheat include a Simba SL straight after harvest followed by a Simba Cultipress or Väderstad RexiusTwin two days later. Two applications of glyphosate maximise the weed control prior to drilling 50-60ha/day with a Rapid at a speed of 16-18km/h. Rolling after drilling helps to conserve moisture and ensure good seed-to-soil contact.
The 5.5m RexiusTwin weighs 8.5t and is pulled by a 290hp New Holland tractor so the weight of 1.5t/m ensures good consolidation. Raptor tines at the front help incorporate even the trashiest of fields. By comparison Jamie says the Cultipress leaves the ground ‘fluffy’ after cultivation and is a playground for slugs and cabbage stem beetle.
“Our 4.5m RexiusTwin doesn’t wear out and it’s built to last. It replaces a 4.6m Simba Cultipress which was bought in 2007,” he says. “The RexiusTwin leaves a much finer and well consolidated seedbed. Its high horsepower requirement will be from a New Holland T7260.”