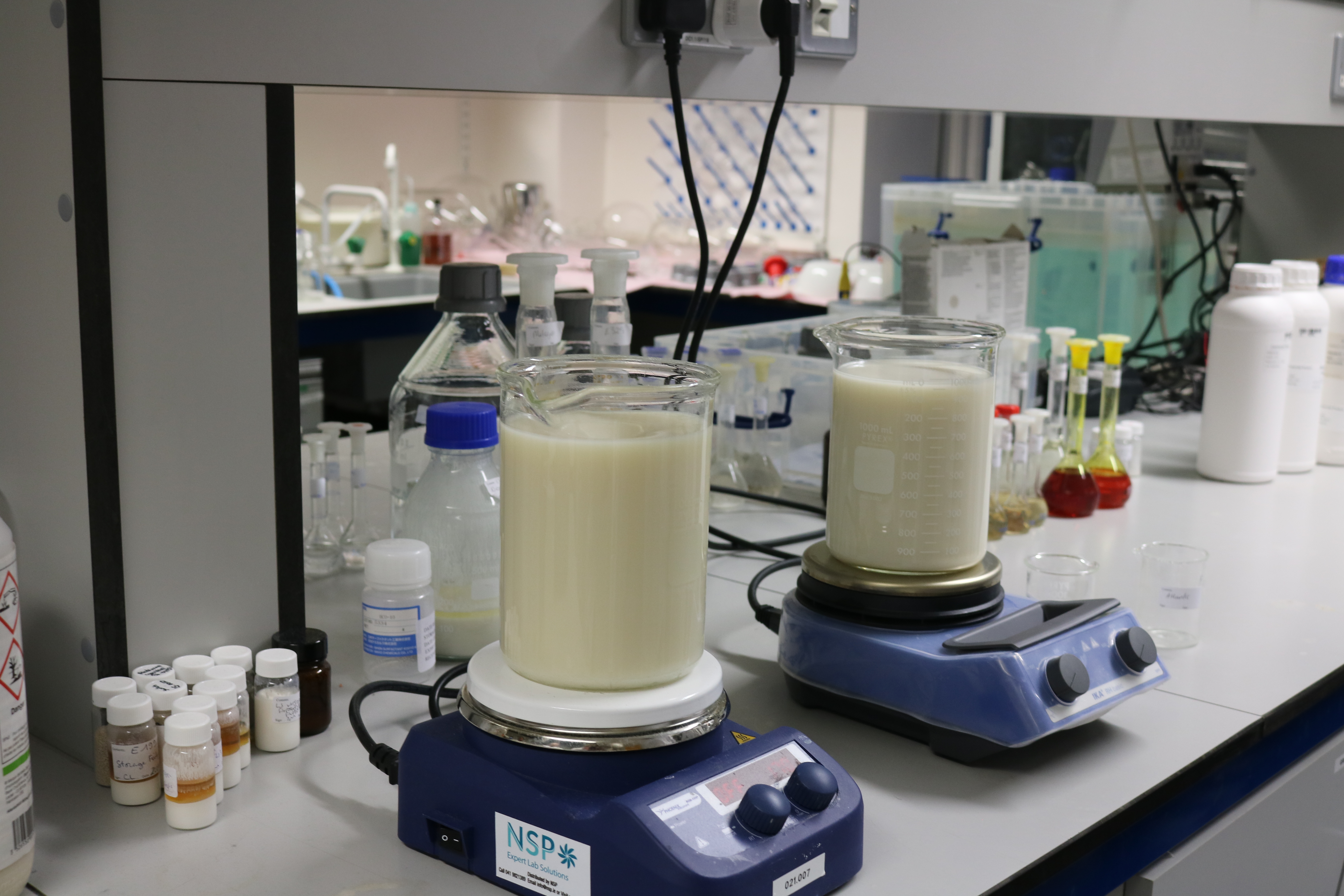
There’s a team of scientists in Dublin focused on pulling apart some of farming’s biggest-selling pesticides, identifying the components and manufacturing replicas. CPM takes an exclusive tour of the labs.
Talented chemists put an immense amount of work into developing the most remarkable innovations – so complex, they believe they can’t be unravelled. Well that’s the challenge
By Tom Allen-Stevens
Two beakers of clear water stand on the lab bench, with magnetic stirrers whirring up a vortex in each. There are two small pots of what looks like identical granules, and each is poured into the whirling water.
The familiar smell of pesticide solvent fills the room. The granules quickly dissolve, and you really can’t tell the difference between the white, cloudy solutions that result. But one is Atlantis (mesosulfuron+ iodosulfuron), manufactured by one of the largest agchem giants in the industry, with well over 100,000 employees. This product is one of the stars in its portfolio of herbicide innovations, revered and relied on by tens of thousands of growers the world over.
The other is Niantic, manufactured for Life Scientific, an off-patent crop protection manufacturer, based at University College Dublin, with a workforce of less than 50, that created this product to be the very same as Atlantis. It’s claimed to be identical, and has at the very least been proven to be comparable. Because this team of scientists spent several years pulling apart the components of Atlantis, replicating them, and putting together a product designed to be identical.
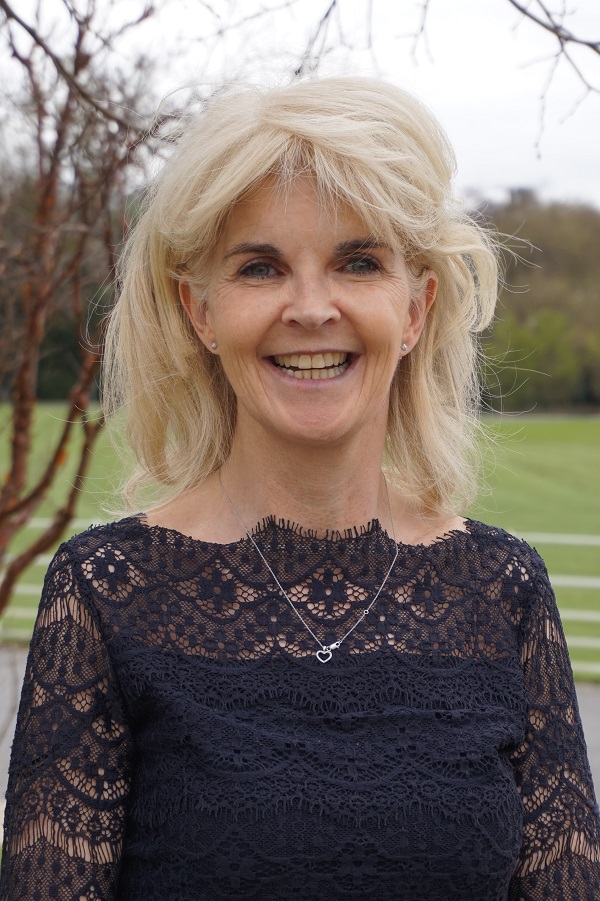
Having worked for a generic company, Nicola Mitchell was determined to set up something driven more by science.
The process is called reverse engineering. It’s totally legal, and with the right approvals, the resulting product can be sold commercially and used, just like the original, as soon as the patent on the original expires. For Atlantis and its sister product Pacifica, that happened on 18 Nov 2017, and barely a week later Niantic and Cintac were launched.
Both are now available for use by UK farmers, and because they’re officially comparable to existing products, they already have approval and don’t need to undergo further regulatory field trials. This sets these ‘cloned’ products aside from generic versions of an active ingredient that have to undergo further tests and additional regulatory field trials before gaining approval.
“The large multinational companies do a brilliant job bringing these products from concept to market,” notes Life Scientific CEO Nicola Mitchell. “They have very talented chemists who put an immense amount of work into developing the most remarkable innovations – so complex, they believe they can’t be unravelled – a bit like the Coca Cola recipe. Well that’s the challenge.”
For Dr Robert Williams, the company’s chief scientist, there’s a parallel with the computer industry. “IBM invented the home PC, and what Dell did was to clone the product and develop the mass market. When you already have a product of outstanding performance, to redevelop it makes no sense.”
Nicola started her career, based in Ireland, with the generic manufacturer Barclay. “It was 1988, I’d just completed my chemistry degree, and it was a very exciting time to be in a generic company as glyphosate was coming off patent. I could see there was huge potential for generics and that the future lay in regulation.
“But at the time the sector was very young – the industry was geared towards new molecules. Being part of a generic was almost a badge of dishonour, seen as counterfeit and poor quality. I was determined to set up something driven more by science.”
She left the company in 1995 and set out on her own, working first from home and then from a small lab within University College Dublin. “The first landmark achievement was gaining Good Laboratory Practice (GLP) in 1996 – this underpins regulation around transparency and robustness of data. Mine was the first lab in Ireland to get GLP.”
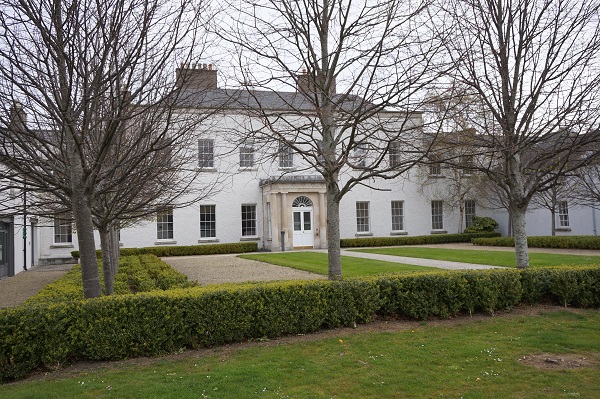
Where it all started: since 1996, Life Scientific’s labs have been located with the campus at University College Dublin.
The focus for the start-up was in reverse engineering (see below). The lab gradually grew, acquiring its own equipment and building a team of skilled analytical scientists tasked with cracking the chemistry of some of agriculture’s best known products.
“Lambda-cyhalothrin was the first big product we cracked,” Robert recalls. “The unique feature about it is that it’s a capsulated suspension, so we not only had to replicate the ai and the other elements of the formulation, but also the organic polymer coating of the capsules.”
A key aspect of the technology that the Syngenta scientists had perfected was the breakdown of this polymer – it had to preserve the chemistry during storage, but release the active at exactly the right time. “There was a component that gives it photostability, to prevent it breaking down in daylight, and eventually we cracked it – it was tooth whitener,” he reveals.
It’s the formulation that really sets apart a product made by a multinational, compared with a generic compound, he says. “Generics do comparatively little evaluation of tank-mix compatibility, rainfastness or how a droplet lands on and penetrates a leaf. So the way the product is put together and the materials used will always be of a lower standard.
“Multinationals put a vast amount of R&D into these areas. If you look at a product like prothioconazole, it’s critically important to its efficacy that it enters the waxy leaf cuticle correctly. We try to get into the minds of the chemists who have developed the formulations – we’ll never produce anything as innovative, but we can replicate them.”
And the analytical team is getting more experienced at identifying components. “A common practice to prevent copying is to include a tracer element. We discovered one manufacturer was using caffeine. That’s a fingerprint and helps us identify their involvement elsewhere. You also get to know the solvents used, right down to the individual source and supplier.”
But producing the clone is only half the story. “We then have to get the product approved and the natural reaction of regulators is to say ‘no’. We have to build a very convincing case to show our product is comparable and ensure the only conclusion they come to is to say ‘yes’.”
Across Europe, it’s currently the UK’s Chemicals Regulation Division (CRD) that carries out the bulk of approvals, and there’s now a team at Life Scientific dedicated to ensuring CRD and other agencies have all the evidence they require.
But this isn’t easy – as well as proving the chemistry is comparable, the team have to certify that it meets the high regulatory standards. Just as molecules can carry patent protection, so too can the studies carried out around them, and these also have to be picked apart, points out Nicola.
“Multinationals are fiercely defensive of this information – they build walls of data protection, and sometimes it’s like you’re fighting blind. What we do is pick our way through the reference lists, go back to the original studies and aim to work out which ones truly are proprietary.”
It’s this work that often exposes elements of a product that is claimed to be innovative and proprietary, but is actually based on previous work. If the team can show this, it strengthens their case to get the comparable product approved, notes Robert.
“Companies differ in their approach. Syngenta has some of the best formulations in the industry – the beauty is in their simplicity. There are other companies that use data protection to paper over cracks in science that is less innovative than perhaps they claim.”
Fiona Maguire is Life Scientific’s regulatory affairs manager and has the task of peering into these “cracks”. “We use reasoned and scientific arguments to question some of the data protection claims made by companies. There is an agenda to build walls and we need to find a way behind them,” she says.
Examples include ecotox studies included as part of the original dossier that may not have been necessary. “Multinationals will over-submit information in a dossier, partly to err on the safe side, but also to make it harder for generics to get competitor products approved.”
The process identifies additional field studies that do have to be carried out as part of the approval process, and the work’s commissioned. But more often than not, the regulatory team can cut this workload considerably. “With azoxystrobin, for example, there were 154 studies for which data protection was claimed. We managed to reduce this to just seven,” notes Fiona.
From 107 applications submitted in 2017, 33% were approved, just 12% refused while 55% are still pending, she reports. “It takes a couple of years on average – the process for mutual recognition is supposed to take just 120 days, but can take over 2000 days.”
Niantic and Cintac were two of the products that gained approval. “It did take a huge amount of work to optimise the formulations and make them the same as the Bayer products,” says Robert. “It was the most difficult one to crack, but put it in the spray tank and it’ll give you the same results. That’s because we’ve applied the same level of rigour to ensure the quality’s sustained.”
Bayer points out that its mesosulfuron products and components are made in Germany and that it manufactures no competitor products. As well as supporting and developing its herbicide portfolio, the company provides help to the industry through research on weed resistance and practical advice through commercial technical managers.
Field trials to demonstrate Niantic and Cintac are underway this year in the UK, but these are the first ones, so there’s no data available from previous years. There are plans for more R&D, though, looking specifically at brome and ryegrass control plus evaluation of different adjuvants.
But no matter how ingenious it is to unravel and copy the technology, is it right to ride on the coat-tails of someone else’s innovation? “Bayer has a new focus in this market in the form of new formulations. The patent expiry has driven the company to invest and develop new lines,” he notes.
And it’s a point picked up by Nicola. “What we’re doing may be disruptive, but it also encourages truth and greater transparency in the industry. What’s more it challenges the multinationals to stay ahead of the game and do what they’re good at, which is to innovate and drive the chemistry forward.”
Reverse engineering – breaking it down to build it back up
Dr Costin Camarasu has 30 years’ experience in mass spectrometry and is clearly a scientist who relishes a challenge. “It separates complex mixtures into its components so you can identify not only what these are, but also their molecular mass – it’s a very powerful tool.”
His colleague John McGrath is using a charged aerosol detector that helps identify larger polymers that can’t be distinguished in the mass spectrometer.
These are two of the tools that lie at the heart of reverse engineering, that deconstructs agrochemicals right down to a molecular or atomic level. Every component has to be analysed and identified, even the so-called ‘inert’ materials, notes Robert.
“These may have no role in the product, but they’re very important. No matter how good the source of your raw materials, impurities always get in. We have to ensure the same impurities at the same level are in our product, and that’s often how we identify and source a raw material.”
It’s the same for fillers, such as kaolin – products are analysed with an electron microscope not just for quantity of the material, but for particle size.
Once all the components are identified and sourced, they’re put back together and the product undergoes further tests to ensure it’s identical. This includes chromatography, that gives a very good fingerprint of a substance.
There’s also nuclear magnetic resonance (NMR), a bit like an MRI scanner, that jiggles the atoms so they give off a unique signature that can be picked up. It’s the NMR comparison that can clinch the acceptance by CRD that two products are comparable.
Finally there’s a series of physical tests to ensure it performs the same as the original product, both through the manufacturing process and once it’s added to the spray tank.
“We’ve built good working relationships with partner companies and work closely with them to ensure the quality of the raw materials are correct. The same goes for the manufacturer, which is based in the EU and has very tight quality control protocols that ensure compliance to our standards,” says Robert.
Chemically comparable – Life Scientific product line-up for 2018
• Azoxystar (azoxystrobin 250g/l SC)
• Basilico (mesotrione 100g/l SC)
• Cintac (mesosulfuron 30g/kg + iodosulfuron 10g/kg WG)
• Kipota (clodinafop 240g/l EC)
• Lambdastar (lambda-cyhalothrin 100g/l CS)
• Niantic (mesosulfuron 30g/kg + iodosulfuron 6g/kg WG)
• Firestorm (flufenacet 400g/l +diflufenican 100g/l SC)
• Fade (prosulfocarb 800g/l EC)
• Sumir (florasulam 50g/l SC)
Innovation Insight
CPM would like to thank Life Scientific for kindly sponsoring this article, and for providing privileged access to staff and material used to help put the article together.