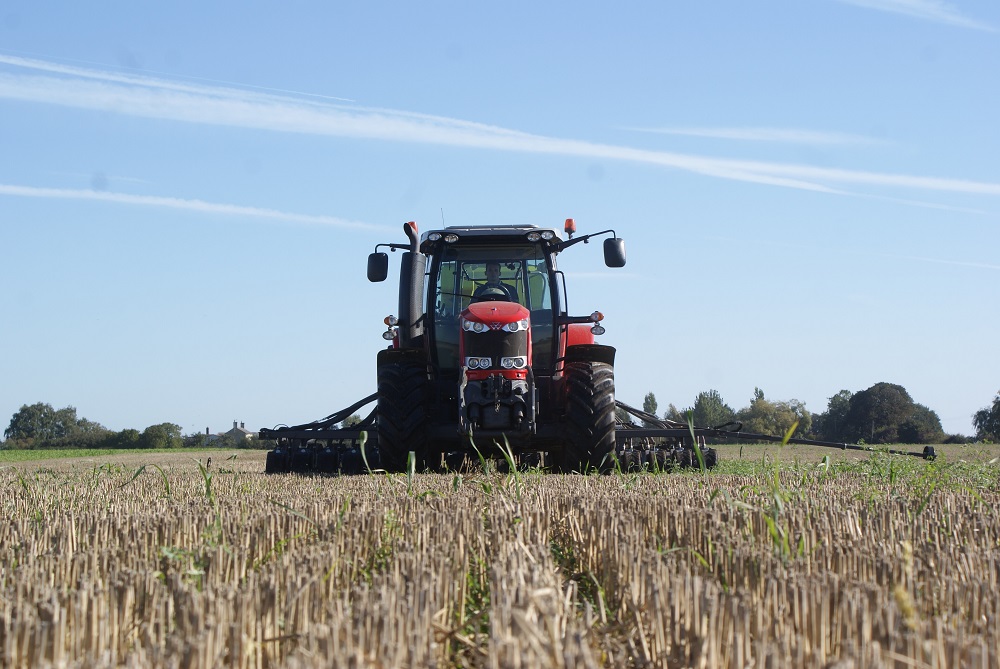
Retrofitting older tractors with the latest technology has it advantages, but it comes down to evaluating the technology on offer and determining if or where they fit into an operation. CPM looks at a few of the options.
There’s less overlap, compaction and I know my valuable input is going in the right place.
By Jane Brooks
There are numerous retrofit guidance systems on the market, from simple light bars through to full autosteer applications. If the technology works reasonably well on older equipment, in some circumstances it might actually be more economical to retrofit than to buy new.
Entry level steering
Andrew Williams of AS Communications is uniquely positioned to talk about Trimble steering systems because his father’s own 1985 David Brown 1394 tractor is fitted with a Trimble CFX-750 display which is running with an EZ-Pilot assisted steer system.
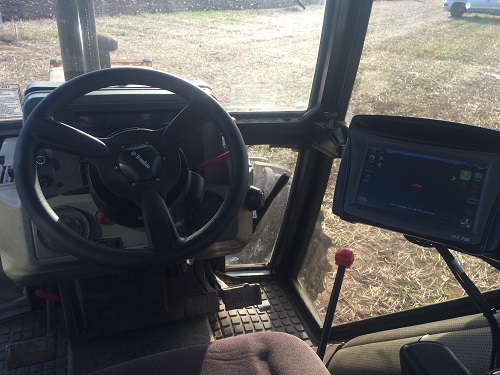
Trimble’s EZ-Steer entry-level steering system uses a friction wheel and motor to turn the steering wheel.
“I’ve been using it on an RTK signal for just over a year and it’s highly accurate. We’re grassland farmers so don’t really need RTK, it’s a luxury and I do work for a firm that supplies them. I have field boundary maps and I let the system steer me when I’m in the field, I find there’s less overlap, compaction and certainly when I’m spreading fertiliser I know my valuable input is going in the right place,” he says.
“It took me about a day to fit it, but normally we would get our engineers to fit the system for a customer. We can fit steering systems and screens to practically any tractor, it can then work from a prescription map using the generic shape file format to apply variably if required with a compatible machine.”
A CFX-750 and EZ-Pilot system with the steering would cost roughly £7300 + VAT including fitting with two years’ warranty and support.
Trimble’s EZ-Steer entry level steering system uses a friction wheel and motor to turn the steering wheel. Taking its guidance from any Trimble display, this system costs from £4300 + VAT including display and installation.
The assisted steering and automated system compatible CFX-750 is a mid-sized 20.3cm full colour touchscreen display, with a built-in LED lightbar, two video camera inputs and integrated GPS/GNSS receivers.
Field-IQ system compatible, the CFX-750 has USB and wireless data-transfer capability.
Chris Limb, Sales and technical support engineer at LH Agro UK says they have RTK customers achieving the same levels of performance with electric steering wheel systems equipped the wheel-angle sensors as steer-ready tractors working in the same conditions.
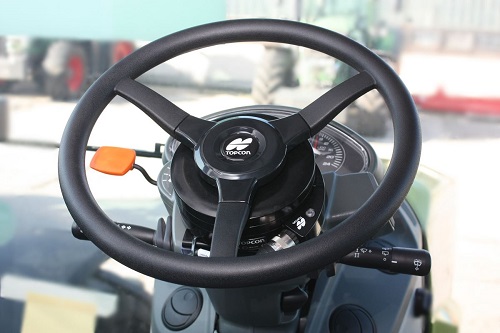
The Topcon model AES-35 includes a high-torque electric motor, which can work in conjunction with an optional wheel-angle sensor.
“At least 95% of sales are Topcon products, with all steering products being Topcon. We also have a name for application control systems as well as specialising in supply of farmer-owned RTK base stations,” he says.
“We use survey-grade Topcon receivers in the bases, adding our own choice of radios or modems to transmit the data depending on the customer’s requirements. I would say that three quarters of the steering kits we sell are subject to RTK correction, which is an extraordinarily high amount.”
The Topcon model AES-35 is a brand new electric steering system for non-steer-ready tractors. Key features include a high torque electric motor, which can work in conjunction with an optional wheel-angle sensor, offering hydraulic performance with electric convenience, he says, as well as being fully weatherproof.
“When you add a wheel-angle sensor, the steering controller knows exactly the angle of the wheels and will turn the electric steering wheel to the point it needs to correct the vehicle error without going any further,” continues Chris Limb.
“Vehicles that can have poor weight distribution, or which suffer loss of traction at the steering axle, such as combines, self-propelled sprayers, or tractors which have front-mounted implements that are taking weight from the front wheels would all benefit from the addition of a wheel-angle sensor,” he explains.
“The AES-35 is powerful enough to be put on just about anything with a steering column and a steering wheel, basically the only vehicle that really excludes us is a skid-steer crawler.
“If the steering is hydraulically power-assisted then we’ve a range of hydraulic valves with oil flows enabling us to do anything from a compact tractor in an orchard to a pivot-steer prairie tractor, which requires a lot more oil.”
Chris Limb also points out that a steering system is a computer and is software driven. Within its lifetime there’ll be software upgrades available with new features, compatibilities, and services.
“The upgrades can be significant in file size and time and may be essential, especially when it comes to satellite reception and connectivity. Equally they may contain a few small tweaks for certain niche markets and have little benefit for many so it’s always worth discussing the benefits with the supplier or manufacturer first, before upgrading.”
Second-hand control units
David King of David King Electronics is based at Heath End, Stratford on Avon, specialising in component-level repairs and provides technical assistance on most types of agricultural electronics.
They also service tractor and combine instrumentation and monitors, controls for implements, and new electronic equipment provided by German company Müller Elektronik either as retrofit or new supply to equipment manufacturers.
The range extends from simple counters, sprayer controls, entry level GPS Guidance and auto-steering, right through to ISOBUS-compliant controllers for precision farming applications.
“We’re currently selling quite a few second-hand control units, but find that the autosteering market isn’t as buoyant as it used to be, probably because most new tractors are autosteer ready these days,” he says.
The entry-level Müller Elektronic Track-Guide II terminal is a popular product, he continues and has a 14cm colour screen, which can be used for basic lightbar guidance and section control. Red lights on the screen indicate areas already covered so the operator can manually apply section shutoff to a sprayer, for example.
It can also be upgraded to ISOBUS control to enable its use as an implement control terminal, as well as other upgrades to allow auto-section control and variable rate applications.
App based systems
Monmouthshire based Patchwork has introduced its Blackbox Air app, which is Bluetooth GPS combined with a state of the art Android App that retains the existing look and feel of the BlackBox.
BlackBox Air uses tilt correction, GLONASS and GPS with EGNOS to obtain a true ground position even on rolling ground. Operators can use a Patchwork-supplied Android tablet or their own and download the Air app from the Google Play store.
An Apple and iPad-based app is Agricision’s onTrak tractor GPS system. Due to its unique design, the onTrak system requires no wires or installation, says the company. A bonnet-mounted waterproof lightbar/GPS receiver provides the guidance and Agricision claims it’s easier to use than a small in-cab terminal.
Another interesting app to anyone using farmyard manure is Rothamsted Research’s recently updated ‘The Farm Crap App Pro’, which is an app for farmers to help with nutrient management planning.
Available free on Apple and Android devices, the app allows the user to map their fields, create full nutrient management plans and take complete account of manure and slurry applications depending on season, soil and crop type, and application machine.
The connected approach to crop control
The historical role of the agronomist is to provide technical crop protection advice to their farmer clients, but this role may be changing.
Numerous legislative challenges are currently regarded by many as putting the continued use of several important and well used agrochemicals under threat. What’s more, chemical resistance, evident from the proliferation of blackgrass across many parts of the UK, has led to massive changes in farming practices.
This is leading to a changing role for on farm agronomy, according to Agrovista. As well as giving advice on chemical applications, today’s agronomist needs to be able to use all the precision tools that are available to sample, analyse, map and advise on the best and most economical use of arable land.
Plantsystems is Agrovista’s integrated precision technology and agronomy brand and the company is currently undertaking a long-term trial on wheat grown at Manor Farm, Ramsey, Cambs to evaluate the latest technology.
Lewis McKerrow, head of precision farming at Agrovista, explains that they are looking at two strategies. “Improvement” is where higher inputs on areas of fields known to perform well will hopefully lead to higher outputs. Secondly “Optimisation” indicates where there is a possibility that too many inputs are being used on poorer ground that may not be able to utilise them, so that lowering those inputs could actually maintain output and cut costs.
A trailed Veris MSP3 has been used to test soil organic matter, soil conductivity and pH. Fields have been mapped using the Isaria sensor and drone technology, with field slope, curve and soil type assessed and curve maps produced.
All this information has been combined with historic yield maps to produce variable rate sowing prescriptions, which have been applied to the land together with targeted variable rate nitrogen applications.
“It’s about reducing the cost per tonne of growing the crop,” explains Lewis McKerrow. “When we overlaid the historical yield map with the curve maps it was apparent plants growing on ridges across the field had lower yields than those at the bottom of the ridge, due to the movement of nutrients down the slope.
“It’s in these low yield areas that we may need to reduce nitrogen rates to improve margins by reducing inputs. The maps also indicated areas of the field with potential for water runoff – another reason to reduce nitrogen in that area.”
Conversely, in areas where the historic yield maps showed high yields, applying more nitrogen may increase yields further, he continues. In this way, the Optimise approach should reduce input costs, whereas the Improve strategy, although increasing input costs, should improve yields in the high-yielding areas.
Another tool that’s being used during the trial is an Isaria crop sensor to enable real time variable rate nitrogen spreading. Developed by the Fritzmeier Group in Germany, the Isaria can be fitted on to the front hydraulics of a tractor in a matter of minutes. An in-cab terminal connects to most spreader/sprayer controllers and the sensor communicates with the terminal via Bluetooth.
The sensor is about 1m above the crop, completes up to 2000 measurements per second and will operate in daylight or at night. It measures crop biomass reflectivity to determine nitrogen requirement in real time, irrespective of any previous field performance history.
This year, the sensor’s being used in ‘absolute’ wheat mode – an automatic mode that feeds the crop to a pre-set yield target. Additional crop sensing and scouting is also carried out using a drone together with the use of soil moisture probes.
There’s also a requirement for software to analyse the data produced, and Agrovista has worked with Muddy Boots to develop its software’s advanced field mapping and data-capture capabilities.
This more holistic approach to agronomy doesn’t come without a cost. Lewis McKerrow says that annually, based on a 200ha farm it would cost about £31.20/ha to purchase the technology. Or to put it another way, an additional yield of 0.24t/ha using the Improve strategy would be needed or a 10% reduction in N, P and K on the poorer ground in the Optimise strategy.
Precision Costs (/ha)
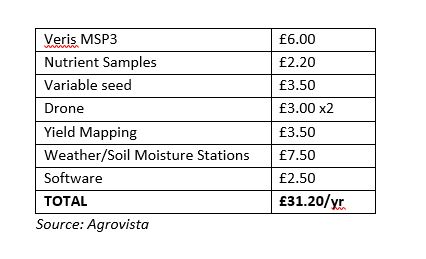