When does the alternative become the normal? Is it when something replaces the old to the point of majority or when the newer version is standardised? In this first of two articles from the West Country Farming & Machinery Show, CPM learns about the possibilities of alternative fertilisers.
“Those three components, which we currently consider waste, are turned into something both valuable and good for the environment.”
By Melanie Jenkins
It’s late February and farmers in the South West have flocked to the inaugural West Country Farming and Machinery Show, held just outside Exeter. Although this part of the country is often associated with predominantly livestock rather than arable farms, it faces a lot of similar challenges to those across the rest of the UK.
One such challenge surrounds artificial fertilisers, its cost, carbon emissions and continued availability. But organic manures also have their own challenges, often to do with their environmental impact.
A lot of focus in recent years has been about stopping nutrients from artificial fertilisers getting into water once they’re applied to agricultural land, says Tim Stevens of Wessex Water. “But the focus is shifting increasingly to addressing the source and trying to avoid the overload of nutrients – in the form of nitrogen and phosphorus – in the first place.
“At the same time, we’ve got a challenge with the expense of inorganic fertilisers and the amount of fossil fuels used to create or extract them,” he says. “And there’s also a food security issue as these nutrients are crucial for food production, but when relying on imported goods this becomes a challenge.”
The annual UK phosphorous surplus – the difference between all that’s applied to agricultural land and all that’s taken off in harvested crops, milk or meat – is about 80,000t. “Every year the UK is accumulating this much elemental phosphorous, mainly in our soils, but this will leak into water.
“So the challenge is that the nutrients we’ve got are often in the wrong form, be it animal manures, biosolids or food waste,” he says. “So how can we recover and recycle these?”
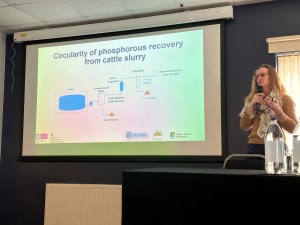
Dr Marie Kirby has been part of a team at Harper Adams researching removing phosphorous from slurries to create alternative fertilisers.
A research group at Harper Adams University has been exploring valorisation pathways for a range of agricultural by-products, so that instead of them being waste, they’re put to further use. Some of this work has been on manures and anaerobic digestion, explains the institution’s Dr Marie Kirby.
“The aim is to bring new revenue streams on to farm, to help farmers minimise their carbon footprint and reduce the potentially negative environmental impacts,” she says.
One interesting use for slurries being explored is the extraction of components that can be used to make biodegradable plastics, says Marie. “We’ve also been looking at biomethane, biocarbon dioxide and biohydrogen use.”
But one particular project, funded by Innovate UK and Defra, aims to make it easier to comply with legislation on slurry applications by stripping out the phosphorous and introducing it into artificial fertiliser that could be sold to other grassland or arable farms, she says. “We generate as much P in slurry and manures as this country requires, so we don’t actually have to import it in artificial fertiliser.”
A system, by Elentec, which has been fitted at Harper Adams’ dairy farm is removing P from slurry to make a secondary fertiliser and the project next aims to make the technology scalable. “The slurry is put through a separator to remove some of the solid fraction. We then introduce electrocoagulation, whereby an electrical current is applied to slurry which depolarises the ions of dissolved metals in the effluent. These depolarised ions then link with the P which becomes bigger and are then dropped out of suspension, she explains. “This then generates both a P-rich fraction – which is separated off – and a P-free fraction.”
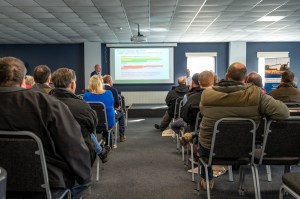
Farmers in the South West flocked to the inaugural West Country Farming and Machinery Show seminars.
From this point, if the P-rich fraction has a high availability of the nutrient, it could be used as a source of P for artificial fertiliser and could reduce the reliance on imported P from other countries, she says. “The P-free fraction, which is still rich in N, can then be spread on the farmer’s fields.
“There are no chemicals involved and it has a relatively low energy requirement. Plus, the system is modular, so it can be fitted for a 50-head herd or a 2000-head herd,” explains Marie. The system is fully automated and runs off a smartphone and it fits within a very small footprint, she explains. “We want technologies that are robust and don’t take up a lot of time.”
For dairy farmers, the conservative estimate is a 15% reduction in volume of slurry just from the separation of solids, explains Marie. “We see a further 35% reduction in the amount of slurry you would then have to spread.”
“We’re seeing around 98% of the total P recovered through the P-rich fraction and about 89% of the phosphates. For those in zones where there are limits on how much slurry can be applied due to the P index, then this helps with compliance and still allows for the application of sufficient levels of N.”
The current trials are looking at the bioavailability of the P and so far, it does appear to be bioavailable compared with a standard TSP fertiliser control. And there seems to be no negative effects to the slurry, says Marie. Field trials are about to start imminently, and the next stage is to engage stakeholders and roll the system out to other herds as demonstrators.
It’s not just slurry that poses potential as an alternative fertiliser, CCm Technologies is using carbon dioxide and biological waste materials to either capture CO2 emissions or convert them into fertilisers and plastics.
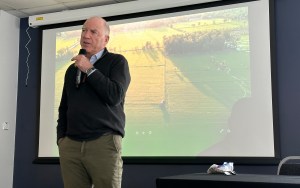
Synthetic fertilisers produced by CCm can be customisable to include the desired nutrient content, depending on a farmer’s requirements, says Pawel Kisielewski.
Quoting figures published in Nature magazine recently, one of the firm’s founders, Pawel Kisielewski, points out that the global impact of fertilisers has been quantified to account for over 5% of total greenhouse gas emissions. About two thirds of this figure are in-field emissions, while the remaining third is from manufacturing fertiliser.
“The critical point from a policy point of view is that the emissions from manures and synthetic fertilisers is 2.6Gt (gigatonnes) and put into context, that’s more than global aviation and shipping combined.”
Pawel and his business partner, Peter Hammond, founded CCm in 2011 and Peter developed a method for capturing CO2 and using it profitably as a pelleted fertiliser. “We’re able to produce fertiliser with a zero-carbon footprint or even be potentially climate positive,” says Pawel. “It’s relatively straightforward mixing and blending technology that has around three inputs; fibrous materials from any sustainable source – grass, straw, woodchip or digestate cake – ammonium, recovered from food waste and cardon dioxide from exhaust streams.
“Those three components, which we currently consider waste, are turned into something both valuable and good for the environment,” he explains.
Synthetic fertilisers produced by CCm can be customisable to include the desired nutrient content depending on a farmer’s requirements. It has a slower release time than current inorganic fertilisers and the aim is for the price point to match or be slightly better than them, adds Pawel.
The firm has conducted eight years of field trials, worked with a number of universities and has been working with PepsiCo to grow potatoes in Scotland using CCm produced fertilisers. Pawel also hopes to be able to work with water companies to extract P and ammonia from discharge being put into rivers and groundwater – but this requires regulatory approval.
The firm’s fertiliser is also placing both organic matter and carbon in the form of calcium carbonate into the soil, says Pawel. “So it’s putting it back where it started from and closing the cycle.”
It’s not just waste products that can be a source of fertiliser, naturally produced flora has been used in this capacity for centuries.
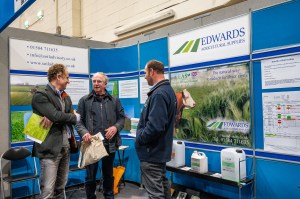
Edwards Agricultural Supplies has a blend of seaweed and humic acid which makes a rich potash and carbon seaweed liquid fertiliser.
David Edwards of Edwards Agricultural Supplies, and long-time farmer, diversified 30 years ago to become an agent selling seaweeds and soil advice. “If we go back in time, our ancestors fed this country by using cover crops and green manures, and seaweed was widely used but now a lot of people have never heard of it.”
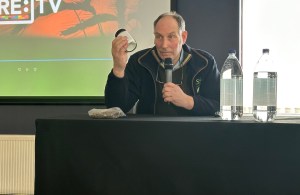
According to David Edwards, just 100g of a bacterial blend can supply enough continual N for one acre for nine months.
The company blends seaweed and humic acid together to make a rich potash and carbon seaweed liquid fertiliser. “Applying seaweed to plants means there’s no build-up of phosphates as the seaweed helps plants mine P from the soil, so there’s no surplus to what a plant requires,” explains David.
As well as seaweed, David advocates the use of bacteria as a soil conditioner. A blend of eight naturally occurring soil borne bacteria can help to colonise roots and provide pathways for plants to access soil nutrients, he explains. “Just 100g of this bacterial blend can supply enough continual N for one acre for nine months by capturing N from the air. And because N is captured from the air as the plants require it, there’s no waste.
“Natural fertilisers are what the government wants, what customers are looking for and we see them as probably the only way forward into the future.”
Mastering methane
New Holland’s T7 methane tractor has been in production since 2021 and for any farmers with a slurry tank, the methane could be harnessed at source to directly fuel the tractor.
If anyone stood and watched a lagoon for a few minutes, they’d see the biogas boil coming off it, says Dr Chris Mann of Bennamann. “It’s really toxic and that’s going on for 24 hours a day, seven days a week. So the fuel is there, it’s just about capturing what’s already on farm and converting it into something.”
But the methane produced from a typical dairy slurry is more than a methane tractor could possibly use, he says. So the firm’s gas capturing system actually processes all emissions, supplies it back to the farmer in a useable form at a fixed cost and then sells the rest to the market, with profits shared with the farmer at a fixed ratio. “We supply the compressed methane at 45p/kg which is the equivalent of 35p/l of diesel, for five years. For a typical 150-head herd, this is worth between £25,000 and £40,000 in savings.”
The system can store a month’s worth of methane on farm, says Chris. “So when there’s a period without much sun, we can power a generator to produce electricity, providing power to the grid or charging electric vehicles.”
Converting a slurry’s methane to an alternative fuel is also worth about 3000t of global warming potentials (GWP), he explains. “This accounts for about two-thirds of a farm’s carbon footprint. And as methane is probably going to be responsible for nearly 50% of global warming over the next 20 years, it’s vital we start capturing it. The only thing that leaves our system is carbon, hydrogen and oxygen, all the other nutrients are locked into the slurry.”
The T7 tractor is powered by a liquefied form of methane and according to the firm, if the biomethane is supplied by animal, crop or food waste, it’s possible for farms to achieve a carbon negative footprint. Because the methane is liquefied, more can be stored than a compressed gas, meaning that the tractor operates just like a standard diesel tractor, delivering the same power, torque and fuel for a day’s work.
Kevin Hoare has been using Bennamann’s methane capturing system alongside the T7 for the past 12 months, at Trenance Farm in Cornwall. “There are no downsides to it. We’ve got the fuel on farm and we fill it up with a gas tube no differently to a diesel, and the tractor runs just as well. The only difference is the farm’s carbon footprint.”
The farm typically produces 60-100kg of methane from 100 cows, which is enough to power a fleet of 60 vehicles for six months, says Chris. The methane storing system is also portable, allowing it to be exported from farm. And to supply this to a wider pool of consumers, Bennamann has started setting up supply systems with fuel stations in Cornwall.
When the farm had its carbon footprint assessed in 2020, it was producing around 800t of CO₂ equivalent, but when it was tested again in early 2023, this had fallen to 172kg, both because of the methane capture and due to efforts towards carbon sequestration, explains Kate Hoare. “I think the total emissions from the methane that we can save on our farm is nearly 700t, which is a huge amount.”
According to Chris, the farm running the T7 for one year using its own slurry, is the same as taking 700 cars off the road. “The next biggest challenge the tractor manufacturers is where to get the gas, which is where our storage system comes in.”
This article was taken from the latest issue of CPM. For more articles like this, subscribe here.
Sign up for Crop Production Magazine’s FREE e-newsletter here.