Rhizoctonia remains one of the most important potato diseases and liquid seed tuber treatments are now increasingly important in control strategies. CPM visits two Cornish producers who’ve found that getting the most out of them is all about the application.
“We tend to treat early and it’s particularly important this year as the seed is quite lively after a stressful growing season.”
By Rob Jones
With only one powder seed tuber treatment remaining for ‘just in time’ application at planting to control seed-borne Rhizoctonia solani, many are converting to pre-planting liquid treatment.
Options like RhiNo (flutolanil) and Maxim (fludioxanil) – soon to be joined by Honesty (fluxapyroxad) – all offer the chance to take a job off the planter and onto a roller table instead. When applied by the latest equipment, coverage is second to none for protection against black scurf and, in the case of RhiNo, control of stem canker caused by rhizoctonia infection, claim Certis Belchim.
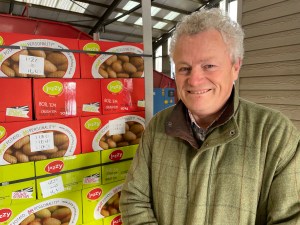
Seed health is critical and if you don’t start the growing season correctly, then it won’t finish right, says Philip Pryor.
One potato grower who’s seen an advantage from moving to liquid seed treatment is Philip Pryor, who runs FG Pryor & Son near Truro in Cornwall with his wife Denise and son Warwick.
The farm grows about 500ha of potatoes each year, with the bulk heading to the fresh market through a diverse range of customers, including local restaurants, wholesalers, and supermarkets.
Planting typically starts pre-Christmas under fleece, on ground rented to the west of its base at Perranwell Station. It then continues eastwards to finish nearer home in the middle of May.
The farm’s major variety is salad variety Jazzy, which it’s been growing since 2010, and the business has helped nurture markets at home and in Europe in partnership with the Meijer seed potato company. It also grows chipping varieties for local bag trade and a small area of hand-planted, hand-harvested earlies for niche wholesalers.
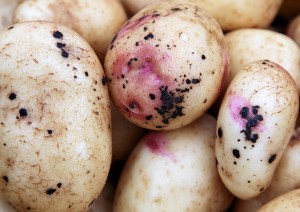
Customers buy with their eyes so black scurf is a big no-no in salad potato production.
The business has 8500t of cold storage and some additional ambient storage space for chippers, says Philip. “We pride ourselves on offering our customers a 12-month service and we are fortunate enough to be able to do that here in Cornwall.”
Seed production is an important part of the system and Philip grows Jazzy seed under license for Meijer Seed Potatoes, which he then uses for the farm’s own fresh market production. “This seed is acclimatised to the local area, which gives an advantage in the following season and helps to reduce the farm’s carbon footprint,” he says.
“Seed health is critical and if you don’t start the growing season correctly, then it won’t finish right,” says Philip. “A lot of our own seed is grown on virgin land. Because of where we are and the air that comes off the Atlantic Ocean, aphid pressure is usually a lot lower than other parts of the country. The only thing it brings with it is a bit of blight risk.”
There may also be a potential threat on the seed itself from R. solani, which can also be a soil-borne threat, and that is an area where Philip doesn’t take any risks in his seed or ware crops.
Allowing the disease into the system through infected seed creates more inoculum in the soil, which in turn increases the potential for poor emergence, stem and stolon canker and loss of marketable yield.
Customers buy with their eyes, he says, so black scurf is a big no-no in salad potato production. “Anything that isn’t what they perceive as perfect becomes a reject. That’s a real challenge because the cost of producing a reject is the same as the good stuff, so reducing that waste is a target,” explains Philip.
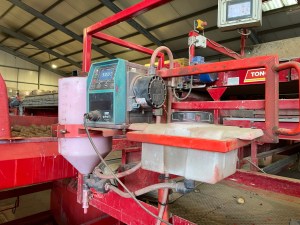
A direct injection system feeds a Team Sprayer CTC2 hooded canopy with twin rotating nozzles, enabling all seed to be accurately treated in-house at Pryor & Sons.
The unpredictability of how a season might play out is a significant risk factor in the management of rhizoctonia. If early planted crops spend a long time in cold soil conditions the potential impact of the disease increases, which can be particularly significant in salad crops where the aim is to produce many tubers of a similar size.
“It’s the perfect scenario and sometimes you can see it on the stems and get some stolon pruning. Last year we didn’t get any as we didn’t get any cold weather after planting, but now we are in a terrifically wet period and it could be a risk,” says Philip.
With no control over what happens post-planting, it’s all about ensuring the seed it put into the best conditions possible for rapid emergence, he explains. So once land is fit to travel, it’s ploughed, ridged, bed-tilled and destoned in quick succession.
Nutrition is becoming increasingly important, with an early compound fertiliser applied at planting alongside humates, allowing nitrogen rates to be cut by 10% in recent seasons.
According to Philip, a seed tuber treatment is the icing on the cake and there’s been a switch to liquid treatments applied with specialist application equipment. It was also an opportunity to take a job off the planter, which was a complex operation including in-furrow application of Amistar (azoxystrobin).
Philip says there was some initial apprehension about liquid tuber treatments, as back in the late 1990s there had been some crop emergence issues with Gambit (fenpiclonil) and the reputation stuck even though there have been no issues since then with the latest products.
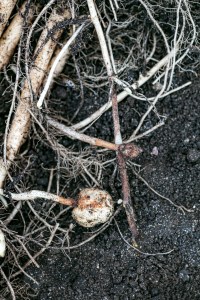
Stolon pruning caused by rhizoctonia stem canker can prove disastrous to salad crops which require a high number of even sized tubers.
“It’s vital the crop is treated when it’s still dormant and it’s dried off before going back into cold storage. We have had some blind tubers, but following this process minimises that risk. That’s why we tend to treat early, and it’s particularly important this year as the seed is quite lively after a stressful growing season,” he explains.
Ahead of switching to liquids, Philip invested in treatment equipment – with a Team Sprayers CTC2 canopy with twin rotating-nozzle applicator enabling all seed to be accurately treated in-house. This makes good use of the firm’s large workforce, which is maintained throughout the winter to treat about 2500-3000t of seed each year.
“Although it’s another process to oversee, if you’re treating any reasonable volume of seed, it makes sense to have control of the operation yourself and ensure it’s done right,” says Philip.
“The roller table and applicator cost about £10,000, which equates to a load of salad potatoes. The amount of work the machine does each seasons means it’s a minimal investment and gives crops the best possible start.”
Another Cornish potato business that has benefitted from investing in seed treatment kit is AR & SA White, based near Bodmin. Shaun White runs the business alongside his brothers Mark and Kevin, growing just above 280ha of cereals and 200ha of pre-pack potatoes for supermarkets.
Maris Peer is their main variety aimed at the early market, with the other being Lucera for Tesco’s Finest range. This year the farm is also growing a small area for Burt’s Crisps in Plymouth for the first time.
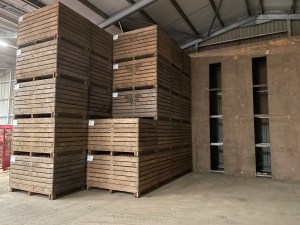
Shaun White likes to treat early and then get seed dried for 24 hours on a drying wall before going back into store, allowing at least 90 days between treatment and planting.
Shaun says certified input stocks are bought in at the start of a production cycle then multiplied up in-house to acclimatise the seed to Cornish conditions over field generations. Growing much of their own seed gives them the chance to identify minor issues and adjust management to ensure they don’t turn into major ones, he says.
“It takes the unknowns out of buying a lot of seed in. If we identify any issues in our farm-saved seed crops, we can change management to reduce risk of it affecting the crop,” explains Shaun.
The farm employs in-house agronomist Seth Pascoe, who walks every crop weekly, identifying problems early and taking crops out of seed production if deemed high-risk.
Seth also advises cereal growers in the area who rent their land out for potatoes and is mindful of the need for a rotation-wide, integrated approach to potato disease and pest problems.
“You need to keep on top of volunteers and weed hosts, which helps reduce the risk of developing soil-borne problems, such as PCN and rhizoctonia. It’s an approach Seth applies across the board,” comments Shaun.
Planting typically commences in early March and Shaun’s team throw everything at seedbed preparation to ensure they’re planting into optimal conditions. Winter ploughing is avoided as the land sits too wet ahead of spring, so the plough is never far ahead of the bed preparation and planting rigs. The plough stops when significant rain is forecast, as soils can cap and cause problems right through the season.
“It isn’t necessarily about the number of passes but doing them at the right time. We try to be as patient as possible and wait for the right conditions before starting,” he explains.
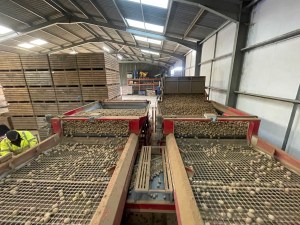
Most seed crops are graded into the right size fractions before store loading at the White’s farm – with some whole crop placed in store, then split graded in December and January before treating seed fractions with a fungicide.
Most seed crops are graded into the right size fractions before store loading – with some whole crop placed in store, then split graded in December and January before treating seed fractions with a fungicide.
Shaun says they like to treat early, the get it dried for 24 hours on a drying wall before loading back into store, allowing at least 90 days between treatment and planting. The farm also has plenums in its cold store, with the positive ventilation keeping air moving through boxes and ensuring there’s no free moisture to aid disease development.
Treatment was initially done over a 2ft roller table with a single nozzle treating 8-10t/hour. It’s now split over two 4ft roller tables, which were incorporated into its newer twin Tong grading line installed in 2016.
Both have rotating twin arm, twin nozzle applicators with custom-made stainless steel hoods, and the two lines and applicators mean two seed sizes requiring different rates can be treated at once. This has doubled output to about 20t/hour, he says, with the chemical delivered via a pair of Team Storemaster spray units.
The key driver for switching to liquid treatments was to optimise coverage of tubers, explains Shaun. Logistics at planting has been simplified too, particularly for the planter operator.
Integrating the treatment tables into his grading line, which has treated up to 1500t of seed each year for the past seven years, has proven to be a cost-effective investment. “Today it would work out about £1-2/t of seed, which isn’t a great deal, and if it has resulted in a crop or two being marketable rather than unmarketable, then it has been worth it,” believes Shaun.
Asked if he would recommend others to take control of their seed treatment by investing in a roller table, he says that would depend on the needs of the business. “As a salad producer, we’re handling large quantities of seed and want to ensure it’s done right. Farms handling a smaller tonnage might be better getting it treated at source, with a lot of seed houses now offering that service,” he concludes.
Keeping application accurate
Harry Raley, technical specialist at Certis Belchim, advises that application kit requires regular servicing and calibration to extract maximum value from seed tuber treatments.
With that in mind, the company has compiled a useful guide to applying liquid seed treatments over a roller table and advise that equipment should be serviced and cleaned at least once a year before each treatment period. It should also be cleaned with Jet 5 (peroxyacetic acid) between seed lots – essential if there is a known disease problem – to avoid transmission onto clean stocks.
Harry also urges regular calibration to ensure the correct dose is applied, helping to maximise efficacy of products. This requires an operator to time how long it takes to fill a one tonne box then adjust pump settings and nozzle choice to match the desired output, he says.
“Our step-by-step guide can help PA12 qualified operators through this process. It includes a calibration chart for single and twin nozzle set ups, and both conventional and peristaltic pumps.
“Once calibrated, it’s important to maintain an even flow of seed as the nozzle applies the product at a constant rate,” explains Harry. “Check tubers regularly under a light to see they are fully covered so you can identify any problems early.
“Products like RhiNo contain a surfactant, which helps spread the spray solution over the surface of the tuber, but that will only take it so far. Re-drying the seed post-treatment is also critical to prevent any disease issues arising when placed back in store, ready for planting,” he concludes.
For more info on best use of liquid seed tuber treatments for rhizoctonia control, go here.
This article was taken from the latest issue of CPM. For more articles like this, subscribe here.