If the 2022 forage growing season has highlighted anything, it’s that forage cannot be undervalued, so optimising harvesting is as important as ever. CPM explores some of the latest machines and developments to hit the market.
By Melanie Jenkins
Whether farmers are producing forage for livestock, anaerobic digesters or a more specialised market, having the right machine for the job can help reduce losses and optimise crop quality. Below are some of the key releases for the 2022/23 season.
John Deere
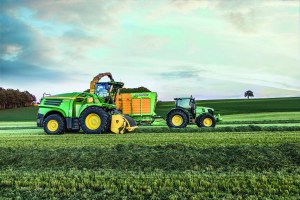
John Deere’s 9700 forge harvester now also gets the 18-litre JD18X engine.
John Deere is revising its 8000 and 9000 Series forage harvester portfolio for the model year 2023. The focus is primarily on the smaller models belonging to the 8000 Series, but the 9000 Series also receives important updates to further increase performance, announces the firm.
Looking at the changes to the 8000 Series, in addition to a facelift, the 8100, 8200 and 8300 models will receive additional horsepower. The 8100 forage harvester has a 9-litre engine and now delivers a maximum power of 431hp and replaces the current 8200. For 2023, the 8200 will receive a larger, 13.5-litre engine which will increase its output by 34hp to 465hp. The improvements to the 8000 Series is rounded off by the new 8300, which now has a maximum output of 505hp instead of the previous 490hp.
So what’s new in the 9000 Series? Joining its sister models in the series, the 9700 forage harvester now also gets the 18-litre JD18X engine, a move which aims to improve the harvester’s performance. The new engine also introduces HarvestMotion Plus, a concept which means the machine can operate in its sweet spot with less engine rpm, more power, a high torque increase, it doesn’t require AdBlue and has lower fuel consumption. As a result, the 9700 machine can deliver up to 825hp.
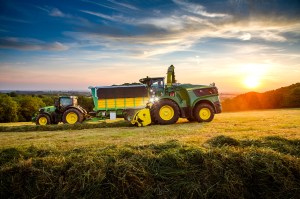
The 9000 Series are now equipped with a newly designed discharge chute, which is 20cm longer than the previous version.
Furthermore, all 9000 Series self-propelled forage harvesters are now equipped with a newly designed discharge chute, which is 20cm longer than the previous version and enables a higher throughput while providing a better overview during chopping.
John Deere has also developed a new high throughput grass pick-up with Kemper – the 30R. It has a working width of 2.7m and is equipped with a large 80cm diameter auger, with deep 20cm auger flights and six tine bars with 6.5mm tines pick up. The 30R features a chainless drive and heavy-duty wear parts that help reduce maintenance costs.
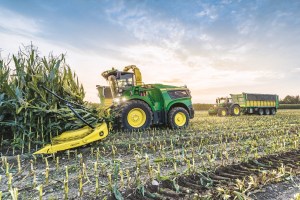
The new engine in the 9000 Series has HarvestMotion Plus so it can operate with a lower rpm and more power.
Recognising that operators work long hours during tight silaging windows, operator comfort is also addressed with a range of measures, one of which is AutoSetup. If the machine is equipped with a JDLink modem, data can be exchanged wirelessly and free of charge with the John Deere Operations Center. This allows workflows to be set up, planned and monitored in a single online portal.
Using this connectivity, it’s possible to send information to forage harvesters directly in the field and pre-planned work schedules will automatically appear on the Gen 4 display when the machine crosses the designated field boundary. This gives the driver direct access to the correct lanes, work settings and field boundaries.
Claas
Last year, Claas’ introduced a raft of new features to its Jaguar 900 series forage harvesters associated with the feeder unit, the corncracker, and the silage additive dosing system.
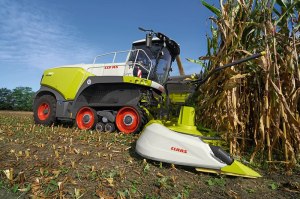
The biggest development for Claas’ Jaguar 900 series is the expansion of the options for the front-attachment drive.
The biggest development for the Jaguar 900 series is the expansion of the options for the front attachment drive. In addition to the all-mechanical drive and the variable drive for the ‘Pick Up’ grass and ‘Orbis’ maize headers, it’s now possible for customers to specify a twin hydraulic drive which offers particular benefits when working with the ‘Pick Up’.
If users select the twin hydraulic drive, the intake auger continues to be driven via the quick-release coupler and can adjust its speed in accordance with the length of cut. The pick-up reel, however, has an all-new hydraulic drive which allows it to be driven with variable speed adjustment independent of the intake auger. The principal objective of enabling the pick-up reel speed to be varied is to allow it to be adjusted automatically to the forager’s ground speed, so the faster the forward trajectory of the machine the quicker the pick-up reel moves.
Some of the key advantages of this functionality include efficient raking action at all ground speeds with low wear; if the ground velocity or the set length of cut is changed, the rotations of the auger and reel are adjusted automatically to the prevailing conditions. If necessary, the operator can adjust both speeds from the cab to suit the harvesting situation. It should therefore be possible to respond to changing harvesting conditions, either automatically or manually from the cab. As a result, it should be more accurate crop feeding and consistent crop flow overall, especially in variable conditions.
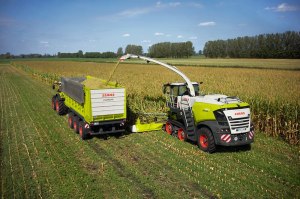
According to Claas, the design of the MCC Max is unique in the market and allows operation across a wide range of cut lengths.
Claas has also released a new wear-resistant coating for the Multi Crop Cracker Max, which the company claims will provide a fourfold increase in service life length. In field testing, MCC Max Cracker units – which include the BusaClad coating – have been able to process over 3100ha of maize, with some units now entering their fourth season.
According to Claas, the design of the MCC Max is unique in the market and allows operation across a wide range of cut lengths and processes the crop with cutting and shear forces as well as friction.
One of the challenges farmers and contractors are being increasingly faced with is being forced to rely on silage additives in grass crops with a high dry matter (DM) content. In order to simplify dosage preparation for the factory fitted silage additive system, Claas has developed a practical app. This helps the operator to find the appropriate dosage and the correct set-up dependent on the crop, yield, and the information provided by the silage additive manufacturer. The ultimate aim is to avoid both under and excess dosage of the additive.
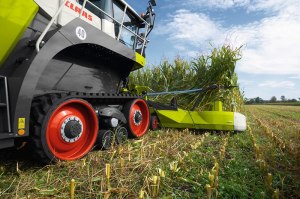
Both the Jaguar 800 and 900 now have a water injection system to help deal with very difficult harvesting conditions.
Both the Jaguar 800 and 900 now have a water injection system to help deal with very difficult harvesting conditions, such as grass with a very high sugar content or lucerne. Controlled via the CEBIS terminal, this system automatically injects water into the feeder unit, guide plate area, accelerator and discharge chute from its 375-litre tank whenever there is no crop flow. This should help to prevent a build-up of material in the crop flow and helps to keep the DM sensor or NIR sensor clean and accurate.
All Orbis maize front attachments are now equipped as standard with wear-resistant steel guide strips which were previously only available as an option. The ex-factory Premium Line range for Orbis maize front attachments has been enhanced with extended wear coatings on existing wear parts. In addition, other machine parts are protected against wear by new, replaceable wear parts.
Fendt
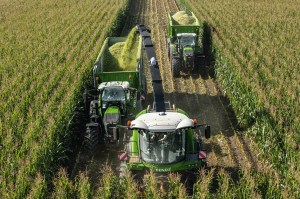
Fendt’s Katana 850 has an in-line six-cylinder engine from Liebherr, a displacement of 18 litres, and an output of 847hp/623 kW.
By launching it Katana 850, Fendt has entered the 800hp plus forage harvester market, 10 years after the delivery of the first foragers bearing the same name. The new model includes innovations such as the revised crop flow, a reversible fan and a new 12-row header to meet the requirements for high efficiency and output. Under the bonnet, it’s powered by an in-line six-cylinder engine from Liebherr, which has a displacement of 18 litres and an output of 847hp/623kW.
If the full power of the forage harvest isn’t required, it can be operated in fuel-efficient Eco Mode. This maintains the usual running speed of the chopping cylinder at reduced engine speed, making it possible to work fuel-efficiently in both full-load and partial-load operation.
The new model’s eco credentials are evident throughout the machine. As an option, the 850 – like the 650 – has a reversible fan with variable fan blade pitch technology. The pitch of the individual fan blades can be adjusted as required so that exact cooling capacity should always be achieved. But if the full cooling capacity is not required, the power saved at the fan is fed into the rest of the machine. The reversing function on the fan cleans the cooling package of debris and fine dust. The automatic control of this function is designed to relieve the driver of stress, allowing them to focus on the job at hand.
Optimised crop flow can have a significant impact on the machine’s throughput and chop quality. So when developing the machine, Fendt’s focus was on a uniform feed flow at high throughputs and, at the same time, minimal power requirements.
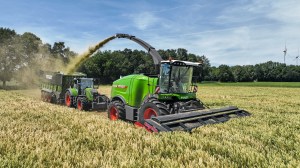
The six pre-compression rollers on the feed intake of the Katana 850 are designed to help ensure optimum pre-compression of the forage.
In addition, the Kemper 490plus header – with a 12-row working width – is available for the Katana. With this header, the full power of the machine should be fully utilised and harvesting time windows can be optimised.
A third skid and reduced set up times should improve ground following capabilities. The header is suspended on the pendulum frame of the Katana 850 and allows for variations of up to 14°.
There has been further attention to detail to the feed intake, with six pre-compression rollers designed to help ensure optimum pre-compression of the forage and to produce good chop quality with a consistent chop length. Metal and stone detectors on the first pre-compression rollers help to prevent damage to the chopping cylinder. Towards the rear of the intake, the crop volume is recorded via a sensor and this data can then be used for yield monitoring and documentation.
With a 720mm diameter chopping cylinder, the 850 has the largest on the market, claims the company. This large diameter with its high flywheel mass should mean smooth running and increased driver comfort. Optional chopping cylinders with 20, 28 or 40 knives are also available for the forage harvester – covering chop lengths of between 2.6-41.4mm.
The position of the knives allows a pulling cut and this should result in a good chop quality, according to the firm. The knives are fixed by means of a slotted hole which allows them to be repositioned once and also means the entire length of the knife can be utilised. According to Fendt, this should help to extend the life span of the individual knives which are kept razor sharp by the machine’s knife sharpening system, which continuously adjusts the sharpening stone for gentle grinding when in operation.
Fendt offers three different roller crackers with a diameter of 300mm. The standard R cracker has a sawtooth profile and is suitable for chop lengths of up to 20mm, whereas the optional RS cracker has a V spiral groove which has been developed for optimal processing of longer chop lengths. The speed difference of 30% or, optionally 40%, ensures thorough processing of the crop.
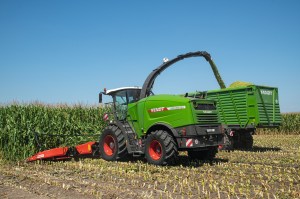
The discharge chute of the Katana 850 has been revised so that it can be precisely controlled when the crop is blown into the trailer to avoid losses.
The discharge chute has been revised so that it can be precisely controlled and centred so that when the crop is blown into the trailer, losses are avoided. The loading height of up to 6.2m is designed to allow for targeted transfer of the crop, even with large trailers and the Fendt filling assistant is available as an option for the 850.
If the discharge chute swivels, the discharge flap is automatically controlled with the result that trailers are filled more evenly. This aims to take pressure off the driver, providing time to focus on feeding crop into the machine and this is helped by the positioning of a camera directly next to the discharge flap, which allows the best view of the crop flow.
Optionally, Fendt also offers an interface for an NIR sensor. This allows farmers and contractors to measure the DM content of the crop, among other things and an ISOBUS interface enables the use of different sensors.
As with the older 650, the intelligent AWD system, BalancedGrip, is also available as an option for the new model. The 850 is available to order now and will be delivered for the 2023 season.
This article was taken from the latest issue of CPM. For more articles like this, subscribe here.