The chance to buy his local main dealers demonstration model sprayer complete with a full range of options made a Lincs farm manager revise his intention to go for a second-hand self-propelled model. CPM reports.
I was so impressed with how well it rode the bumps and how easy everything was to operate.
By Jane Brooks
Having managed farming businesses in the Heckington area for the past ten years, Brain Hammond was seeking a new challenge. “Last year John Priestly, the managing director of Heckington-based Melbourne Holdings, invested in Westmoreland Farm. I was approached and asked if I’d look around and develop a business plan for the place, with a view to managing it.
“I took him up on his offer and have been at Westmoreland Farm since last Aug, so it’s still really early days. Just growing wheat, oilseed rape, a few peas and letting a field for growing carrots is barely a full time job. It’ll pay the bills and a wage but to build a business that’s going to move on you need crops that add value. My background is in potatoes, so I suggested setting up a potato-growing operation, which is what we’re doing.”
Initially the farm was 255ha, then a 30ha block of land was added, followed by a further 38ha. “Shortly afterwards, another 22ha came up on the other side of the river, which with a little bit of rented land has brought it more or less up to 400ha. This spring we’ll be growing around 63ha of potatoes and probably increase up to 80ha next year – this’ll be the 30th year I’ve been planting potatoes.”
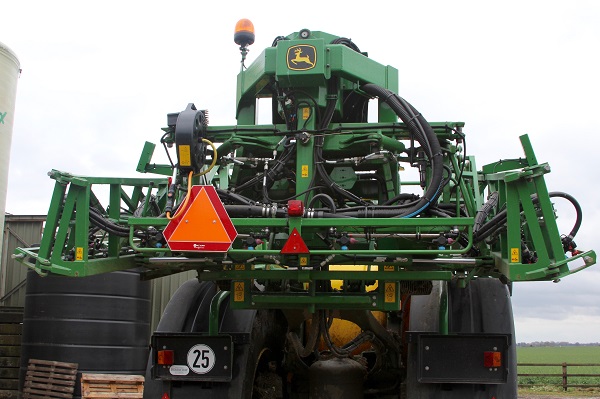
The booms are fitted with five jet nozzle clusters and the sprayer also has an in-cab nozzle-control system, allowing the operator to switch between two nozzles on the move.
Potato cyst nematode
The soil varies from light sandy loam through to heavy clay, but there are 100-120ha of light sandy loam suitable for potatoes, says Brian Hammond. “The potato cyst nematode (PCN) levels on the home farm are quite high, some of my neighbours stopped growing potatoes on similar land about 18-20 years ago.
“So I haven’t an infinite amount of land available but there’s a decent chunk of clean land to grow potatoes on and we can irrigate from our own supply, so we’re quite lucky in that respect.”
The other farm cropping will be 80ha of OSR, a further 78ha sugar beet and 40ha of combinable peas, which will be sold through Melbourne Holdings dried food ingredients business. There are 14ha rented out to Strawson Farming to grow carrots, which leaves less than half of the farm which will be in wheat this year.
The potatoes will be grown on various contracts with some salad potatoes in the mix. The sandy soil doesn’t lend itself to prepack, so a lot will go for chipping, he says. Potato planting started on 1 April with harvesting from the end of Aug. A Grimme harvester has been purchased, but they also need a grader and elevator.
The planned rotation is one in eight years for potatoes, one in three or four with sugar beet and OSR. Half the farm will be wheat and this year over half is in break crops, which is just the way it fell when the farm was taken over. “We went back to basics and ploughed the whole farm. At the moment, I intend to plough every year, I believe it’ll give better soil structure and better blackgrass control.
“Contractors Will Dean and James Burton of D & B Farming, will be combining, my view is we don’t have enough land to justify a decent combine and there’s a possibility we’ll be lifting spuds and combining on same day, so using a contractor allows us to do both.
“Our Agronomist is Nigel Mason from Frontier, he makes all the decisions but every now and then I question them and argue that we’re putting on too much, or too little. Nigel and the Omex rep Steve Ebbage, who does all the soil sampling and testing, both looked after the farm before I came so they have extensive knowledge of ground conditions here.”
All fertiliser and crop protection applications are liquid, and originally the plan was to buy a second hand self-propelled sprayer probably with a 24m boom. “But output wouldn’t be that fantastic and reliability could be an issue, particularly with the potatoes.
Demo sprayer
“Our local John Deere main dealers Doubleday rang me and said the demo John Deere R944i sprayer was in the area and he offered to bring it down. I had absolutely no intention whatsoever of buying the sprayer, but they brought it over on a wet afternoon, we put some water in it as you’re only allowed to spray water on a demo and I went onto a stubble field.
“I was so impressed with how well it rode the bumps and how easy everything was to operate. I thought I’ll probably have to spray all those potatoes I’m growing myself, so I’ll need something fairly decent to do the spraying.
“Also there was a keen deal on the table, so I secured the funds and we did a deal and brought the sprayer in Nov.”
Currently the sprayer is on a John Deere 6215R which is rated at 215hp, but boosts to 259hp, while a second 155hp (boosted to 202hp) John Deere 6155R is also available. Brain Hammond says either tractor will be used on the sprayer – both are still in their first season and were supplied by Doubleday and came complete with row crop wheels.
“The sprayer runs on BTK 620/70R/42 tyres, but possibly the best thing on the tractor are the Michelin MachXBib 650/85/R38 tyres. The salesman persuaded me to go for them, because I was going for wider tyres. I ran on very low pressure when I was ploughing in the wet and was getting fantastic grip although all my friends told me I’d a puncture, but of course they are meant to be like that.
Brian Hammond refers to the sprayer itself as a Christmas tree. “It has everything on it. But it was brought with an eye on future developments I expect to be here over the next ten years and the sprayer should last that long, too.”
A 4400-litre-tank model with a 36m steel boom, the R944i uses a Greenstar display and a SIM card RTK receiver mounted on the roof of the tractor. The nearest mast is about five miles away and is part of the system Doubleday has in the area.
The sprayer has automatic section switching and BoomTrac ultrasonic boom control, which uses ultrasonic sensors to measure boom height above the crop or soil. It then compensates for changes in the field or the target surface, automatically adjusting the boom to maintain the optimum spraying distance.
In use, the operator specifies the boom height for each nozzle type or chooses a different boom height depending on the application or field conditions.
It also has John Deere’s PowrSpray solution system, which features a pair of hydraulically driven centrifugal pumps. The first pump fills the sprayer at up to 1200 l/min, even with the tractor engine at idle, which reduces fuel use and noise whilst filling. The second 750 l/min-spraying pump has direct rate control for fast changes of application rate.
It adjusts between 0-8 bar at the nozzles in less than three seconds, to give high spraying accuracy. This is particularly important during headland entry and exit, where changing forward speeds and automatic section switching place heavy demands on rate-control systems.
Direct rate control also allows very accurate variable rate applications, where large changes in target rate may be required. Combined with ‘smart’ hydraulic control of the solution system, direct rate control allows spraying to be completed independent of the tractor engine rpm. At the moment, Brian Hammond isn’t using variable rate application, but doesn’t rule it out in the future.
“Auto rinsing is very good due to low residual volume, even though it does take a little time to go through its sequence. This is controlled from the cab and I generally do a double rinse in field. If I’m going to spray sugar beet I rinse two or three times more in the yard.
“I’ve just been spraying Omex nitrogen plus S – the OSR had it a fortnight ago. The last chemical I used before I went to spray the nitrogen was glyphosate, so there again I did a double rinse in the field and another rinse in the yard. Depending on what you’re using chemical-wise, a normal rinse in the field is good enough but in some circumstances you have to repeat it.”
SolutionCommand and AutoDilute enable in-cab operation of agitation, filling and rinsing the sprayer. Auto agitation intensity control decreases tank agitation as the solution tank level lowers. Conversely it has power agitation, which increases agitation for hard-to-mix products.
AutoPowr IVT or DirectDrive tractors with engine/transmission management can be operated in ‘ECO’ mode, and John Deere says the low engine revs significantly reduce fuel consumption during spray applications.
Brain Hammond’s tractor has AutoPowr IVT and he’s extremely impressed with the fuel consumption whilst spraying, “I sprayed a stubble field in the autumn and brought up the fuel per ha – it was phenomenally low at just 0.4 l/ha and I was spraying 40ha/hr.”
John Deere claims the low-profile tank and lowered centre of gravity provide better stability and keep the unit balanced in all spraying conditions. They also say the axle steering system provides excellent tracking on the headlands to minimise wheeling damage.
Brain Hammond is certainly impressed with its handling. “I find it stable and it’s incredible how well the sprayer rides the rougher patches and the axle steering is fantastic. It has triple-folding 36m steel booms, with three metres at a time automatic section control, which is excellent.
“I’m using fertiliser nozzles at the moment – John Deere’s own ultra-low drift, which are phenomenal – you could probably quite happily spray in hurricane conditions. The booms are fitted with five-jet nozzle clusters – I also have bubble jet nozzles on but will probably buy another set of smaller ultra-low drift. I’ve twin lines so I can generally switch nozzles in the cab.”
With just over 1000ha sprayed since the beginning of Nov, there have been no issues with the sprayer, he reports.
Looking to the future, Brain Hammond says the farm’s owners view it as a long-term investment. “Rarely in farming are you given an opportunity to make a business out of 400ha of land, which is what I’m doing. It’s a challenge, but I don’t do easy. The day after I accepted the job I went to the Cereals Event and told several people I’m going to be back farming – it was like going into a room and switching the lights back on. “
New European carbon-fibre spray-boom plant
Brian Hammond recently visited the John Deere factory and had an opportunity to see the new carbon-fibre spray booms, which were first seen last year on the new R4050i self-propelled sprayer. They’re the product of an exclusive partnership of King Agro with John Deere, who have opened a new dedicated production facility at Picassent, near Valencia in Spain.
Representing an investment of over €8 million by the company, the new plant will work alongside an existing factory at Campana in Argentina to manufacture booms for John Deere sprayers built in North and South America and at Horst in the Netherlands.
Up to 100 people will be employed at the 5500m² facility, as production ramps up over the next 18 months. The very latest technology will be used to produce up to a maximum of 1800 carbon fibre spray booms every year.
Manufacture of the booms starts with precision moulds, created using a five-axis, computer controlled CNC plotter. Carbon and Kevlar fabrics are cut to precise sizes and shapes using a CNC cutter before lamination in a controlled, dust-free environment.
Curing of the carbon composite components takes place under high temperatures and pressures of up to five atmospheres. Machining, painting and final assembly then finish off the booms, ready for installation on the sprayers.
Speaking at the opening of the new plant, King Agro president Guillermo Mariani said he believes carbon-fibre spray booms are just the beginning of a trend that’ll offer “innumerable advantages” linked to increased productivity, lower costs and reduced soil compaction.
The novel spray booms are six times stronger and more than five times lighter than traditional steel equivalents. Highly durable and resistant to the corrosion and fatigue that affect steel and especially aluminium spray booms, carbon fibre offers a long working life and lower operating costs.
The material’s light weight allows overall sprayer weight to be reduced, resulting not only in less soil compaction but also lower fuel consumption. In addition, the spray boom’s low inertia benefits ride performance, providing improved boom control for increased crop coverage and reduced spray drift.
Farm Facts
Westmoreland Farm, Melbourne Holdings, Howell Fen, Sleaford, Lincs.
- Farmed area: 400ha
- Cropping: Oilseed rape, sugar beet, peas, potatoes, winter wheat
- Agronomist: Nigel Mason, Frontier
- Soils: Light sandy loam through to heavy clay
- Elevation: 5m average
- Mainline tractors:John Deere 6215R, 6155
- Telehandler: JCB 530/70
- Drill: Lemkin 4m solitair combination
- Plough: Kverneland EO 6f Vari-width
- Cultivator: Väderstad Carrier
- Sprayer: JD R944i
- Staff: One full time; contractor plus gang labour; Harper Adams student in holiday time.