The transition from traditional to minimum tillage has been a journey for one Somerset farmer but working with nature has played a huge role in its success. CPM paid a visit to Manor Farm to find out why the latest kit purchase has proven to be particularly beneficial.
I’ve always believed that establishment is 90% of growing a crop.
By Charlotte Cunningham
It’s barely past breakfast time, and already a hive of busy bees are working away on the flowering bean crops at Manor Farm, near Taunton, Somerset.
The 283ha farm is home to Richard Payne, whose family has farmed there since the mid-eighties. Pouring a coffee, Richard points towards the open door at the end of the farmhouse kitchen. “Can you hear that? The bird life we have on this farm now is absolutely fantastic,” he says as he sits down and begins to explain why working with nature – rather than against it – has become a fundamental principle of the arable operations.
“My father moved from Herefordshire to the South West in 1981, before purchasing this farm in 1985 – it was the first farm to come up in the Taunton Vale in its entirety since the war. I left the army in 1986, before coming back to the farm full-time in 1989, and I’ve been here ever since.”
At that time, Manor Farm was operating as a traditional mixed farm. “We had a 100-cow suckler herd and used to finish all the stock too, meaning we’d have up to 300 cattle on the farm at any one time. About 25% of the farm was put to grassland and maize, and the rest was arable.”
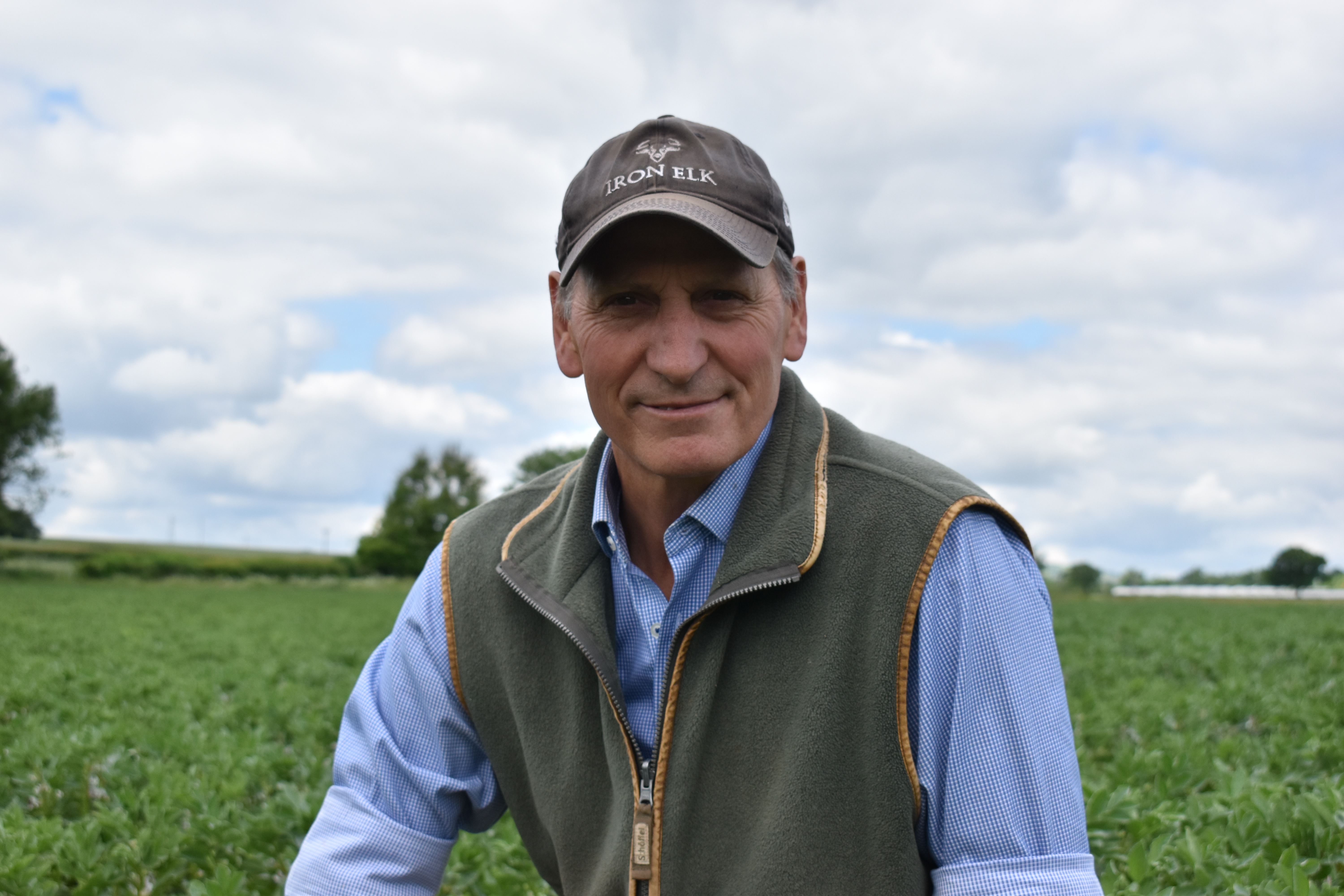
The transition from plough to minimum tillage has been a journey, says Richard Payne.
This remained the way until 2003, when the herd was dispersed and sold – two years after Foot-and-Mouth. “I had grown really tired of all of the risk associated with cattle – TB, BSE, Foot-and-Mouth. The market was also in the doldrums a bit, and so I had a moment where I just thought, what am I doing?”
From that point on, the farm has run purely as an arable enterprise. Today, a typical rotation includes first and second wheats, winter oilseed rape, and winter and spring beans grown for feed markets. “Where we can, we slip in some barley if we need to, and we do rent some ground out for maize, just to get in another break crop.”
The farm has not ploughed commercially for more than 30 years and has been operating as minimum tillage since then. Over this time, a plethora of different kit has been purchased and trialled on farm – the latest, a Sumo DTS (Deep Tillage Seeder) is showing great promise. But it has been a journey to get to this point, explains Richard.
“I’ve always believed that establishment is 90% of growing a crop – how we do it is the one thing that’s in our control. If you don’t start right, you can’t make a silk purse out of a sow’s ear.
“I’m also not a great chemical farmer – I don’t like high intensity chemical farming. I believe it’s wrong and we’re doing ourselves a disservice because I think chemistry will either lose efficacy, or public opinion and legislation will remove a lot of the options available to us as the moment. And so therefore, I try and farm with nature a lot more than I used to.”
When the move away from more traditional tillage began, the first thing Richard bought was a Simba Freeflow drill and he was using this while he still had the plough.
“Being someone who gets his head turned by new bits of flashy machinery, we then went down the route of using a Simba 2B disc harrow and a following press. However, we’ve got quite a few small fields here and found we were ending up with too many headlands.
“Then we bought one of the very first Väderstad Carrier disc cultivators in the country – we’ve still got it going, it’s a 1999 model,” he laughs.
“We then swapped the Freeflow drill for a 3m Väderstad Rapid box drill, before changing to a Horsch Sprinter in 2013.”
On the cultivation side of things, a Sumo Trio one-pass stubble machine has been the primary cultivator for the past 10 years. “But over time, I’ve found that to be as destructive as the plough because it’s high intensity, deep, min-till,” explains Richard.
“The main problem we have with it though is that if we get a lot of rain in September, it takes us longer to get back on the ground – and wet autumns are becoming much more frequent.”
He’s also tried his hand at direct drilling. “We’ve done a few experiments where we’ve direct drilled when the soil conditions have been right, and you can see the soil gets a bit darker – a bit more organic matter – and greater worm counts. However, with a silty clay loam soil type, which tends to slump a little, a bit of something was needed to prevent soil from running together.”
A changing weed outlook has also influenced his machinery choice. “Like many farmers in the country, we’ve started getting blackgrass issues so we’ve been trying to delay drilling,” says Richard.
But the challenge with delayed drilling, in combination with wetter autumns, is the headlands and corners started to get compacted, he explains, which is where the Sumo DTS offers potential.
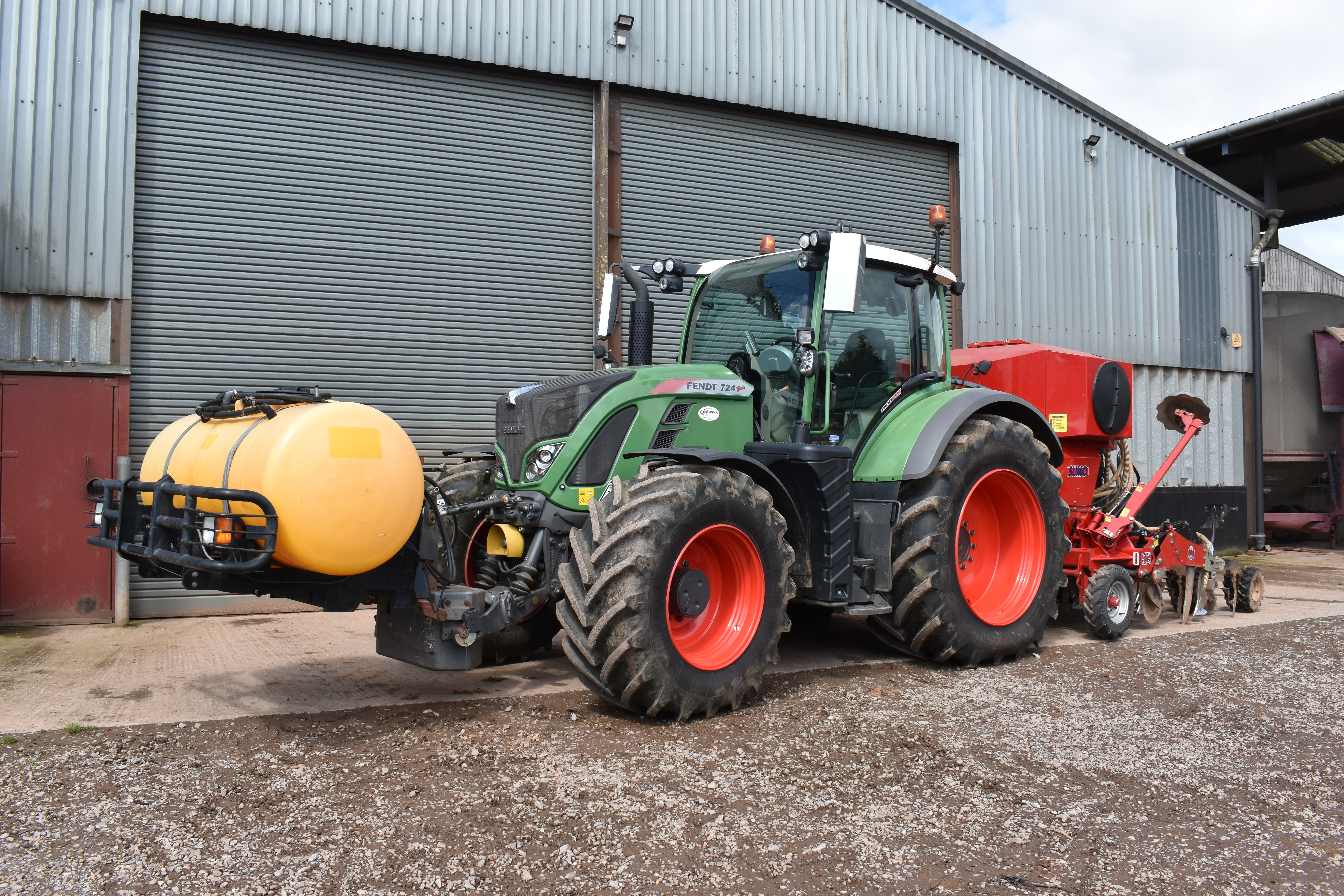
Manor Farm invested in a second-hand 3m Sumo DTS this year.
Richard first spotted the machine through trials carried out as part of the Agrii iFarm network. “We were an iFarm for four years and ran establishment trials every year. In these, we’d normally have our Horsch, a DTS, a Mzuri, sometimes a Claydon and a Sky drill, run on a 24m drilling plot to assess the results.
“I always liked the way the DTS went,” he muses. “You could get a reasonable forward speed, it was quite easy to pull and depth control – once you’ve sussed how deep you put the seed – was straightforward too. So while I wasn’t really on the lookout for another bit of kit, I’d always had my eye on the DTS, as it were.
“I then spoke to a good farming friend who had one, and he told me that it’s his go-to drill for break crops, which I thought was quite a nice strapline for it because you can get that depth for OSR and beans but you’re not wasting all that energy cultivating ground you don’t need to in between the rows.”
This year, Richard says he took the plunge and purchased a second-hand 3m Sumo DTS from a local contractor who was ceasing operations.
Looking to the nuts and bolts, how does the DTS work? Marketed as a ‘versatile drilling system’, the DTS strip-till seeding is a conservation agriculture system that uses a minimum tillage approach that improves root development and soil carrying capacity, explains Mark Curtis, general manager at Sumo. “It combines the soil drying and warming benefits of conventional tillage with the soil-protecting advantages of no-till by disturbing only the portion of the soil into which the seed is placed.”
Alongside the savings in fuel, labour and machinery, using the DTS is also claimed to reduce seed and fertiliser rates due to precise strip placement.
When it comes to design, the DTS comprises a straight disc which cuts trash and initiates the rip line for the ensuing leg. “This is followed by a straight ripping shank which loosens to depth and creates an environment conducive to easy root development,” says Mark. “A tungsten tipped, depth adjustable twin row – or optional single chute – seed placement coulter capable of handling a wide variety of seeds then follows.
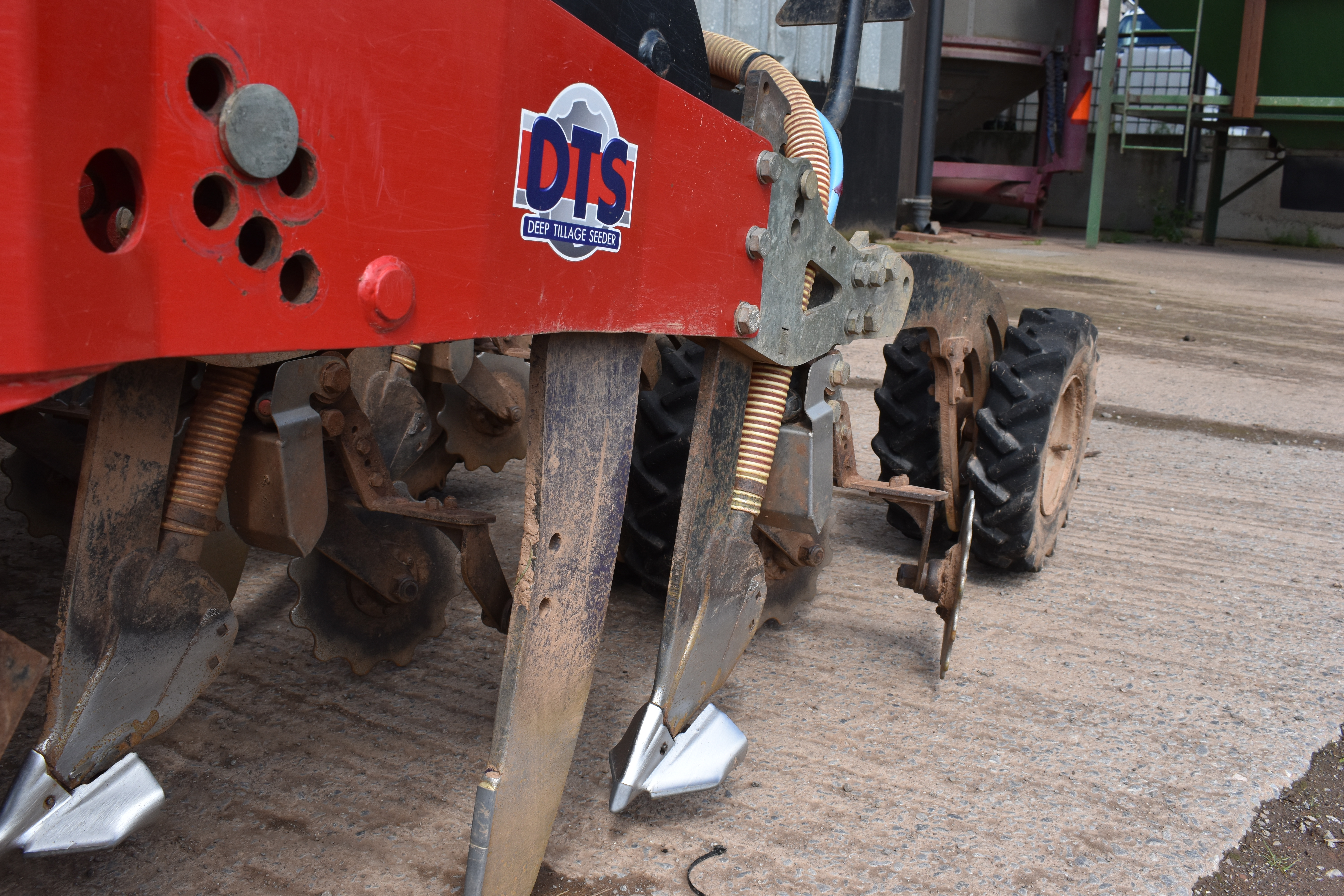
The DTS comprises a straight disc which cuts trash and initiates the rip line for the ensuing leg.
“Covering discs follow and these simply re-direct soil over the seed before the final press wheels just firm it over the seed.”
The DTS coulters are set to spacings of 333mm, and each coulter is independently mounted to ensure good contour following ability and seed-to-soil contact across difficult terrain.
As well as this, the DTS comes with simple calibration and metering, satellite speed monitoring, 120mm seed row spacing – with grain/fertiliser options also available, adds Mark.
Being based in the UK is also a benefit to customers, he says. “Being a British manufacturer, 99% of our machines are manufactured in-house, meaning we’re in a good position to continue to supply the UK agricultural market with little disruption. Not to mention having full control over quality.”
As the DTS is such a new addition to the fleet at Manor Farm, Richard has only drilled 6ha of Lynx beans and some chicory with it to date, but so far says he’s pleased with its performance and sees potential for the future. “We’ve tested the DTS in our worst field this year – it’s poorly drained and we don’t tend to put a winter crop in as the plants just rot off.
“So, in a bid to work with nature, we decided we’d just spring crop it instead. Prior to this, it had grown wheat and linseed, both zero tilled, so we decided to go straight in with the DTS and I think it could possibly be one of our best crops of beans.
“I love it because you get a bit of a cosy feeling that you’re doing two things at once – you can bust compaction and give a route for your roots. I can see this being a really important bit of kit for the areas where we have localised compaction. What’s more, the coulters follow the terrain a bit better than our other drill too. It’s also incredibly easy and simple to set up and calibrate.”
This focus on elevating compaction spans beyond just drill choice, explains Richard. “Our whole fleet runs on Michelin tyres so we can let the pressures right down, for example.”
Looking at the bigger picture, this latest purchase plays an important role in the overall strategy to enhance both farm and business sustainability, he believes. “Over the past three or four years, we’ve also had sheep back on the farm which we rotate around the land to go slightly regen, bring diversity to cropping, and to feed the soil a bit more.”
He also avoids using any insecticides where possible, though this decision is made pragmatically, depending on the season.
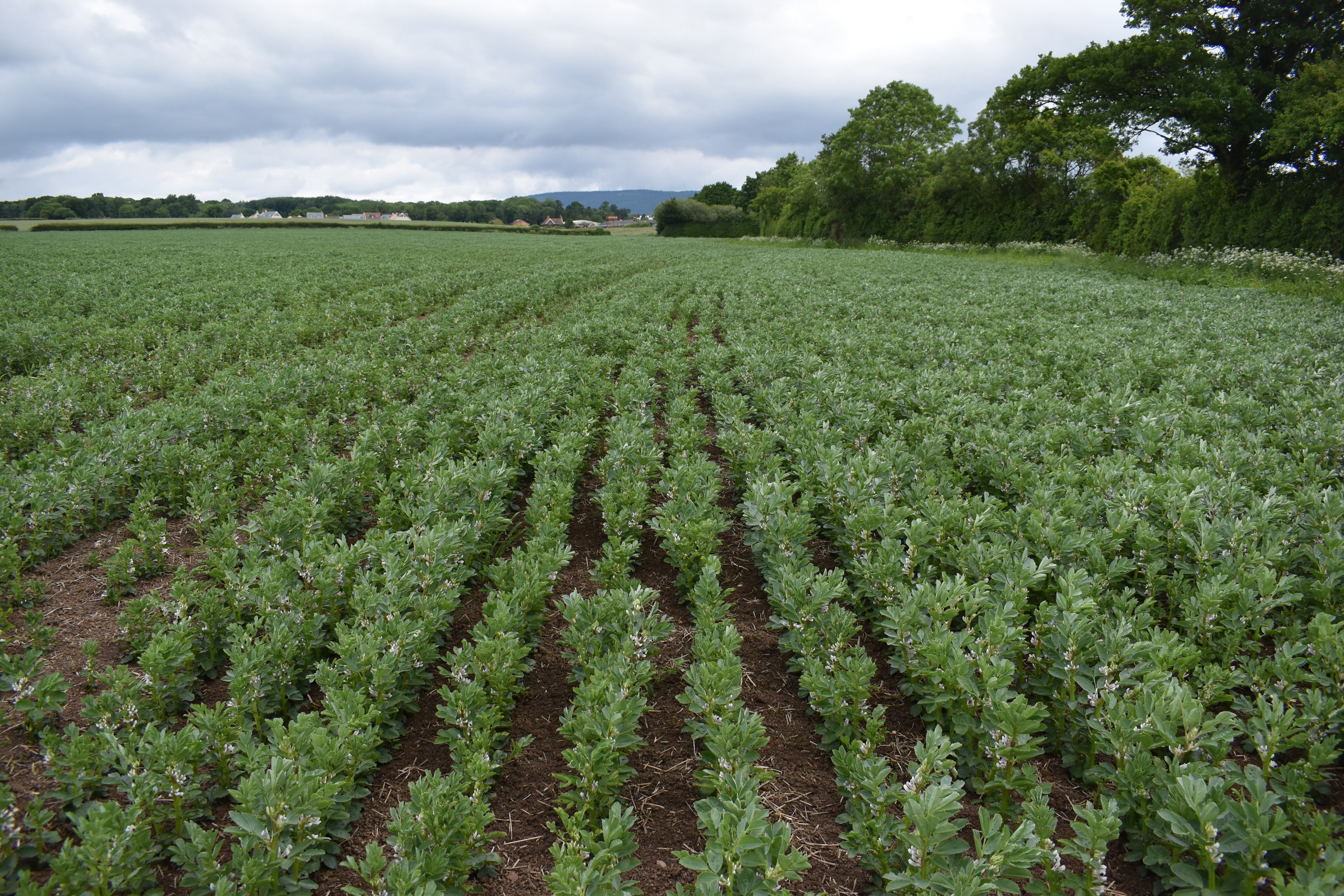
The worst field on the farm looks to have
produced the best crop of beans this year, after drilling with the DTS.
As well as benefiting the environment, the way Richard establishes crops has a strong business case too. “With pressure on input costs, the challenge now is doing the same with less resource. I also believe that the biggest stumbling block for innovation in farming is cash flow.
“If we look at diesel costs alone, last year we bought diesel for cultivations and harvest at 44p/litre. This year, we’re looking at £1.18/litre. Fertiliser is the same. So I’m just trying to look at all the options – whether that’s with machinery, cover cropping, or even bringing livestock back on to the farm – to help us be more financially efficient, all round. Essentially it’s about maintaining a margin, but with less risk.”
With one son to potentially succeed him, Richard says there are still discussions as to the future of Manor Farm, but in terms of both his short- and longer-term goals, it’s simply just to keep going. “We’ve diversified over the years, both in terms of how we do things on the farm, and also bringing in additional income streams via business units made from converted old cattle buildings. Apart from that, it’s all about just getting a fair reward for an honest day’s work.”
Put to the test
As a previous Agrii iFarm, and just coming to the end of a stint as an AHDB Monitor Farm, Richard says these opportunities have been brilliant for facilitating knowledge exchange from other farmers and as such, he has personally experimented with trialling different products and practices.
Among these are some experiments with foliar nitrogen. “The DTS features a front-loaded liquid fertiliser tank, presenting an opportunity to trial something new in light of high granular fertiliser prices,” explains Richard. “We’ve cut our fertiliser right back from 220kgN/ha to 160kgN/ha. Instead of relying on granular, we’ve bought an IBC of Efficie-N28-t and then, where we’ve got anything with potential, we’ve put on 20 l/ha of the foliar nitrogen – essentially, this has been our OSR and our best looking first and second wheats. With the liquid route, we can essentially design our own fertiliser.
“We did some trials last year and couldn’t really draw many conclusions, but the one thing we did note is that when using Liqui-Safe – a urease and nitrification inhibitor – with fertiliser we got the best results by putting 220kg on in one go. I think this is because we had quite a dry spring, and the Liqui-Safe kept it there. We saw significant differences in the crops where this approach had been used.”
He’s also been looking at the potential of biostimulants. “Rather unscientifically, what we’ve done this year is buy an IBC of AminoA and then at T0-T2 we applied 1 l/ha to the cereals at each timing. It’s marketed as giving drought tolerance, so we’re looking forward to seeing the results this year.
“We’ve also given the crops 1 l/ha of molasses every time we’ve gone through with the sprayer, the cheapest grade you can buy, and we’re putting it on because everyone talks about the importance of sugar and getting it into the plants.”
He’s running some more measurable trials on this too this year, applying molasses with fertiliser side-by-side, with the results set to be analysed at harvest.
“I’ve got stacks of IBCs sat in the yard now and, in the future, I’m quite keen on making a few of our potions,” laughs Richard. “Especially now we can put them down the spout with the DTS, it’s really quite exciting.”
Farm facts
Manor Farm, Heathfield, Somerset
- Farm area: 283ha
- Soil type: Silty clay loam
- Cropping: First and second wheats, winter oilseed rape, winter and spring beans. Some ground rented out for maize.
- Cultivation equipment: 6.5m Väderstad Carrier disc cultivator; 3m Sumo Trio one-pass stubble cultivator.
- Drills: Horsch Sprinter; 3m Sumo DTS.
This article was taken from the latest issue of CPM. For more articles like this, subscribe here.