When it came to replacing their self-propelled sprayer, bigger, better and rather familiar proved the only choice for a Warwicks family business. CPM reports.
For us going with a RoGator again was the only choice.
By Jane Brooks
The Heath family have farmed on the heavy clay soils of Warwicks since 1944, trading as HG Heath and Sons. They currently farm 1400ha, of which 690ha are owned, 365ha rented and 365ha contract-farmed. A full agricultural contracting service as well as stubble-to-stubble contract farming is also part of the business mix.
“My grandfather Harold George Heath, has farmed in this area since 1944, initially renting ground, prior to purchasing the main farm in 1966,” explains Rob Heath, one of the partners. “He’s now 94 and still does a bit of hedge cutting.
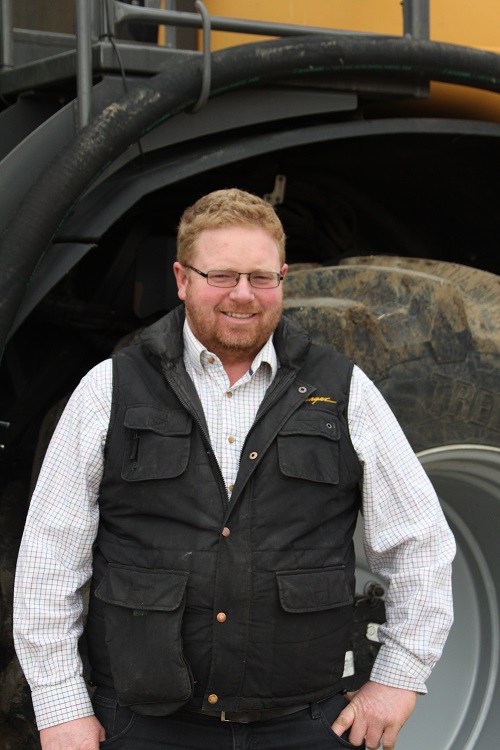
Chris Heath is the driving force behind the acquisition of the RoGator sprayer as well as being the operator of the machine.
His sons, Melvin – Rob’s father – and John, joined him in the business a number of years ago, and now it’s a partnership of nine family members, including Rob’s brother Chris who’s the main sprayer operator. There are also other family members working within the business.
“Over the years we’ve diversified. For example, John started Heath Engineering,” continues Rob Heath. John Heath designed and fabricated the Heath Bale Chaser in the early 1990s. These are still built at the farm and continue to be marketed by specialist company Big Bale North – a working relationship that’s lasted since the Heath SuperChaser was launched in 1995.
Heath Engineering also manufactures other agricultural accessories, such as loader attachments and mole drainers. This year they exhibited at the LAMMA show for the first time, where they received a Certificate of Merit in the farm machinery and equipment innovation category.
Another family business is Newbridge Straw products. The stand-alone enterprise produces and sells dust free straw bedding, mainly into the horse livery market. With recent investment of almost £1 million in shredding and bale packing equipment products, it was decided to follow the example of the bale chaser and hand product marketing to specialist companies such as Bedwrap and Nedz.
Around 1000t of home produced oilseed rape and wheat straw go for processing, with an additional 3500t of OSR straw brought in from other producers. A pelleting machine has also been added into the mix with an eye towards producing pelleted bedding in the future.
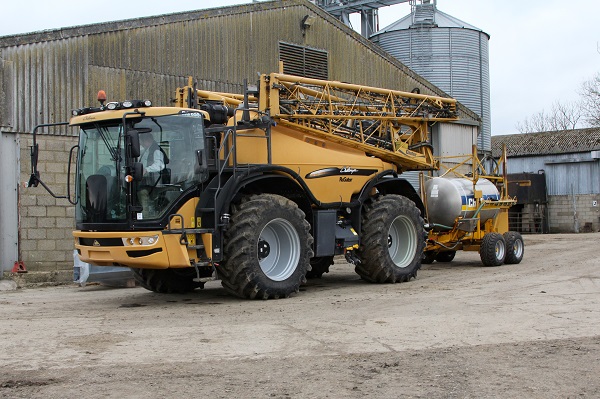
With ground to be sprayed up to seven miles away, being able to tow a 3000-litre spare water tank is a great benefit.
“We’re looking to the next generation and the big question, after seeing what’s going on with Brexit and everything else, is how do you protect a farming business,” says Rob Heath. “Diversification is one way and that side of the business is generating an income, so it supports our labour force in the winter and gives us a labour source in the summer.”
On the farm, there’s 100-head single-suckler herd with 200 followers mainly Simmental, on Aberdeen Angus and Belgium Blue Bulls. “Although we’re moving more towards Aberdeen Angus, because of the premium on the beef and their reputation for easy calving.” These calve in the autumn and spring and are just coming to the end of spring calving.
All the application options and spray plans are undertaken by Christine Furness of Central Independent Agronomy. “With nine partners, if we were all to try to make decisions on spraying and cropping it would be painful, so she makes the decisions for us,” comments Rob Heath.
The arable rotation is based on OSR, with a crop of 242ha. current cropping includes spring beans, spring barley, winter barley, winter beans, winter wheat, and 150ha of temporary grass leys. “Last year we harvested 4000t of milling wheat, 1000t of feed wheat, 2000t of barley, 600t of beans and 950-1000t of OSR,” he notes.
“Soyl is used for nutrient mapping, we also use Gatekeeper software, John Deere Greenstar as well as having our own Topcon RTK-based guidance position system, we share a signal mast with Forsyth Farming. We use a Topcon agi-4 gps receiver running with RTK radio and a fixed-base station.”
Chris Heath explains they use various cultivation techniques, but don’t plough unless it’s absolutely necessary. “Really we do a bit of everything when it comes to cultivations, it’s very broad spectrum – some direct drilling and a bit of min-till. We also have a Howard seven-leg Flatlift which we use a lot followed by the press, we also use a 6m Kuhn power harrow. Our nitrogen applications are done with a Kverneland GeoExact spreader.”
The business already had a Challenger RoGator 635B sprayer but this had reached the stage where they wanted a larger engine and needed greater tank capacity so the decision was taken to upgrade. “For us going with a RoGator again was the only choice, particularly as we were able to purchase a 2014 ex-demo RG655C with just 50 hours on the clock, through main agents Lister Wilder.”
The Rogator is equipped with 32m Chafer triple-fold booms on a 12, 24 and 32m pattern and a 6000-litre tank. The 242hp six-cylinder Agco tier 4f engine, which uses Adblue but doesn’t have ERG, is mid-mounted on the right-hand side of the machine. Road and field speeds are 50km/h and 30km/h respectively. The sprayer generally runs on Trelleborg TM1000 710/60/38 Ultraflex tyres, using Michelin 480/50s where necessary.
Rather than level indicators, RoGator sprayers use weight cells to measure tank volume. The Hypro centrifugal pump has a filling capacity of 800 l/min when the engine is running at 1250rpm. Opti-Ride double-wishbone suspension allows in-cab adjustment of the machine height to either 75cm or 1.2m, while the Opti-Track system allows pus- button in-cab track variation from 1.8m up to 2.25m.
There’s also automatic constant levelling and hydro-pneumatic damping, which automatically adapts the suspension to block the outer two cylinders when making high-speed turns. The Opti-Ride suspension has automatic individual wheel-height adjustment which enables the chassis to stay level while it’s being filled.
“Our average spraying speed is 14km/h,” says Chris Heath. “The RoGator has a Norac three-sensor system with three modes: Crop reads the height from the spray nozzle to the top of the canopy, Soil reads from the nozzle to the ground, while hybrid uses both measurements and creates a virtual crop canopy using historic crop height information. We use hybrid for OSR crops if they’re a bit patchy.”
On the headland, hedoesn’t usually lift the boom tips unless the ground’s undulating as the Norac tends to keep up round the end on level ground. “You need to be aware of the boom, but the turning circle’s excellent and it’s very well balanced from front to back and side to side,” he advises.
“We use TeeJet five-way twist-unit nozzles, which you have to switch externally, just a single line down the boom. But I tend to use Guardian twin airs, the nozzle has front and rear facing outlets. I use blues for 100 l/ha applications and browns for 200 l/ha. I generally use auto guidance for pre-emergence sprays and Roundup (glyphosate), although guidance is used all the time for auto-section control.”
Optiflow in-cab monitoring is something Chris Heath rates highly, particularly for activating cleaning operations without leaving the cab. He says the 500-litre clean-water tank makes it easy to clean out the tank and booms thoroughly between treatments. He also finds with 1.2m machine height clearance there are minimal losses on desiccated OSR.
“I enjoy driving the RoGator and wouldn’t want to use any other sprayer. With the exception of one or two software issues and a few sensors, it’s been relatively trouble free, but with a sprayer you’re mixing water, mud and electronics so it’s hardly surprising if you have the odd breakdown.”
That said, he can’t Lister Wilders’ support. “You can break down at 5:00 on a Saturday afternoon and they generally have an engineer available. The RoGator has just been to their Cirencester branch for a pre-season service, which included the annual sprayer test. We’ve done around 2600 hours spraying with it, most of which has been plain sailing.
“When it comes to folding the booms it’s not too bad overall, but as we have the triple-fold boom it does take a little while. We have the 76.2mm pipework on the boom. We put on whatever is needed, such as fungicides, insecticides, growth regulators, liquid nitrogen, liquid protein and Roundup – it’s really down to the agronomist’s advice. Although this year, blackgrass control has been good – we have just 130ha to spray this spring.”
In the cab, a Topcon C3000 terminal runs Agco software with the smaller C1000 screen in the armrest. Driving is via a foot pedal or hand throttle. “I generally tend to go with the foot peddle, programme the speed, then put it in auto control. As needed, I’ll take control back with the foot pedal particularly around telegraph poles.
Some of their ground is seven miles away and he can tow a 3000-litre spare water tank behind the RoGator. “This is a great benefit, especially when it comes to putting on liquid protein. It also saves anyone running out with a water bowser. On the road, two-wheel steer is generally good. It’s really a very comfortable machine – big but not really a problem.”
Precision networking
RTK (Real Time Kinematic) base-station networks are providing many farmers with cost-effective ways of accessing an incredibly accurate global positioning system (GPS) signal.
Information is accurate to within 25mm of a farmer’s actual location. This is because the signals from RTK base stations correct positioning errors caused by the Earth’s atmosphere.
Most RTK base stations are placed in a permanent position although portable base stations are available. They transmit information to the tractor or to another user terminal, which then accurately correct its own position and aligns it to the base station.
As the base stations are in a fixed place it’s possible to record GPS positions to enable repeated use of the same controlled traffic lines within fields.
RTK Base stations have a range of around 15km. This is because the same GPS satellites need to provide the information for both the base station and the tractor.
Many farmers and contractors may find the range of 15km unworkable and in recent years, many main dealers have installed their own networks of base stations supported by repeaters, which give wider coverage.
Additionally, wireless technology allows RTK correction through a mobile phone in areas where there’s a signal and this has been incorporated in several manufacturers’ guidance systems.
So currently the options available are to have one’s own base station, to have a portable base station, to use the mobile/network RTK (which needs a SIM card and is not available throughout the UK) or finally to subscribe to a third-party radio signal.
Farm Facts
H G Heath and Sons, New Bridges Farm, Blackwell, Shipston-on-Stour, Warwicks
- Farmed area: 1416ha
- Cropping: Winter wheat (242ha); oilseed rape (242ha); winter barley (180ha); winter beans (70ha); spring barley (37ha); spring beans (14ha); temporary grass leys (150ha)
- Agronomist: Christine Furness – Member of Central Independent Agronomy Group
- Soils: Heavy clay
- Elevation: 83m
- Mainline Tractors: 3x John Deere 6930; JD 7530; JD 8410; JD 6150R; CAT Challenger MT855c; Claas Challenger 75E; Valtra 141N; Renault 103; Renault 106; Massey Ferguson 8690; Fendt 724; JCB Fastrac 4220
- Telehandler: JCB 536-70; JCB 531-70; JCB535-95
- GPS: JD Greenstar, Topcon.
- Combine: Claas Lexion 580TerraTrac 9.1mheader; New Holland CR9080 9.1m header
- Loader: JCB 434S
- Drill: Väderstad Rapid 800S; Weaving 6m tine
- Cultivator: Väderstad Rexius Twin press 1030; Väderstad Topdown 600
- Plough: Dowdeswell 9f; Lemken 6f
- Sprayer: Challenger RoGator RG655C
- Fertiliser spreader: Kverneland GeoExact
- Muck spreader: 3x K-Two 1600 Evo
- Staff: 8 family members, 3 part-time family members, 2 full time farming employees, 4 full time workshop/farm employess, 6 seasonal