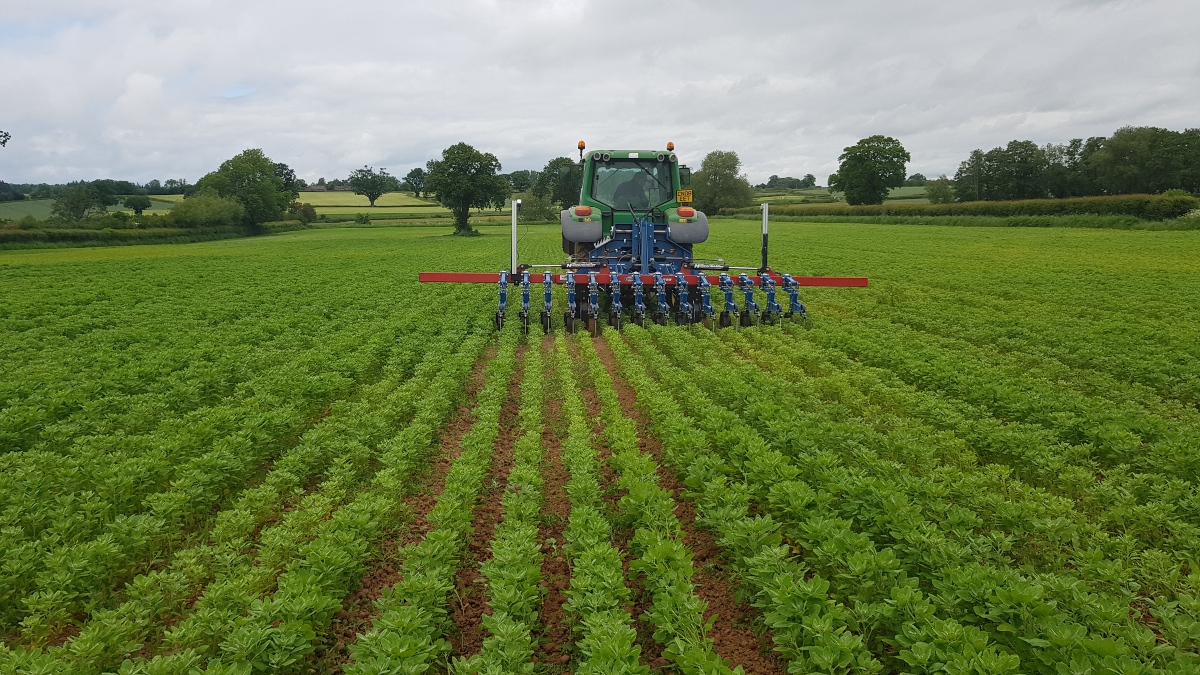
As sugar beet growers struggle to continue growing the crop, one grower in Herefordshire has invested in an alternative, mechanical, solution for weed control to help him keep beet in the rotation. CPM visited him to find out more.
It’s essential for us to have equipment which can cope with a variety of soil types and situations.
By Charlotte Cunningham
Proudly pointing to the photo of three generations of Watkins’ on the office wall, Gareth Watkins explains that sugar beet was the raison d’être of Watkins Contracting based at Gillow Farm, near Hereford.
At that moment Monty the spaniel dashes past, proudly carrying a stray beet in his mouth. “He’s a big fan of sugar beet,” laughs Gareth as he begins to explain how the business’ latest mechanical investment is helping them to continue growing the crop.
“Watkins Contracting is now a partnership between my father and I, but dates back to 1952 when my grandfather purchased a small piece of kit which loosened sugar beet. This then allowed the crop to be picked by hand.
“With this, he started doing bits and pieces for other local farms and effectively, this is what kickstarted the contracting business as it’s become known today.”
As well as farming over 800ha themselves, the Watkins’ now provide a variety of contracting services across the West, including Herefordshire, Worcestershire, Gloucestershire, and Monmouthshire – as well as travelling further afield for specialist jobs.
And though sugar beet clearly has a sentimental value on farm, it’s not been without its challenges of late, as any grower would agree with, he adds.
“We’re currently growing 1000t of sugar beet for British Sugar. Logistically it’s quite tricky as the nearest factory is in Newark, but we feel it’s important to keep a foot in the door with them and stay growing British sugar for British produce.
“What’s more, it’s still a very important and valuable break crop for us, and we’re also supplying markets like digestors who specifically want sugar beet. But you’ve got to be kitted up right for it and ready to spend money on it to get the best harvest.”
Despite the importance of the crop, Gareth says that the loss of key chemicals in the crop protection armoury – and the increasing cost of those that are available – triggered the requirement for an alternative method of controlling weeds within crops. “We’ve always had a hoe of some kind on farm,” he explains. “But we realised we needed something more accurate and efficient that could come a key part of our operation as we look to take a more ‘hybrid’ approach to crop production.”
He began scouting show stands, looking for an inter-row hoe which would fit the bill. “We looked at a number of options, probably over three years, having fairly in-depth discussions with manufacturers to really understand what was available and if it would be worth the investment. Machinery like this isn’t cheap, so it had to be right.”
These discussions identified that not all options had the flexibility to alter row widths – something which was a must-have for Gareth. “We also planned to use it in maize, so we also wanted to be able to put grass seeds/other crops down between the maize.
“Covering such a vast area and different customer requirements, it’s essential to have equipment which can cope with a variety of soil types and situations.”
Something that did tick every box, however, was Opico’s Hatzenbichler inter-row cultivator. “This immediately stood out for us and coupled with the prospect of excellent service, which we’d previously had from the local dealership (Frank Sutton) who supplied this kit, we knew it was the right bit of kit for us.”
Walking out into the yard, the 12-row, 6m inter-row cultivator sits mounted nicely on the rear of a tractor. And though it only arrived last season, Gareth says he’s so far been left very impressed with the accuracy.
Looking to the nuts and bolts, how exactly does it work?
While Gareth is using the kit for predominantly sugar beet and maize, Opico’s inter-row cultivator can also work on combinable crops and is designed to hoe between rows of growing crops to cut off weeds just below the surface.
It does this via vibro-tines with duck foot shares. Parallelogram mounting frames for the hoe carriers maintain pre-set working angles and pressure while allowing accurate ground contour following, explains Nick Rider, the Opico territory manager who helped get the kit on farm.
“Different numbers of shares are fitted to the hoe carriers depending on row widths and crop types,” he explains.
The steel flange wheel is also an important component in the design, adds Nick. “Moving the hoe shares sideways to follow plant rows creates powerful lateral forces and if side forces exceed grip from the tractor’s rear wheels, then the tractor could be moved sideways leaving the hoe position unchanged, resulting in damage to the crop.
“To prevent this, the headstock has a pair of large diameter flanged steel wheels which anchor the guidance headstock in line behind the tractor wheels. Thereby withstanding the side forces for perfect row following.
“This is particularly the case with wider working widths, or when the hoe shares are working deep.”
A neat feature, and one which Gareth believes sets it apart from competitors, is the camera-controlled guidance system. “We drill sugar beet at 50cm row widths via a Väderstad Tempo 12-row drill and this is ultimately the reason we run a 12-row hoe – so everything is the exact same width. As good as we can drill with GPS, if doesn’t work in the same width, you’ll inevitably end up taking rows out.
“The benefit of the camera system, however, is that we can work even closer to the crop to really maximise our weed control.”
Integrated within the headstock for exact movement control, Nick claims that the Tillet and Hague designed camera guidance system is the most accurate on the market. “Camera guided machines can be operated much closer to the plant rows and hence provide improved weed control, but there are three distinct advantages with this particular system. Firstly, it’s able to take a feed from two or more cameras – therefore meaning a higher level of accuracy. This is particularly beneficial at row ends and any areas where the drill has missed/overlapped.
“Not only does the system boast unrivalled accuracy, but the software is also able to derive a speed measurement from the cameras, known as visual odometry. This means that it’s not dependent on a GPS or radar feed.
“From our perspective, the service from Tillet and Hague is also hugely advantageous. They’re specialists in the field and are based in the UK, meaning they’re able to provide quick and effective backup to operators when they need it.”
Looking at the headstock itself, Nick explains that the machine features an integrated hydraulic ram to provide up to 250mm of side-shift in either direction, allowing accurate compensation for deviations caused by side-slopes, as well as errors due to drilling or driving accuracy.
“A potentiometer monitors movement to ensure precise positioning. Oil is sent to either left or right by the camera controller, ensuring the hoe shares run as close to the crop rows as possible without damaging the crop. As you would expect, parallel side shift rails are greased and bushed.
“Three options of headstock are available from lightweight 450kg to heavyweight 1300kg for cultivators over 12m.”
There are also several optional extras available, including the Kult finger weeders. “These can be attached to the hoe carrier and are used to weed in between the plants. Rubber fingers grip and pull out the weed from the side and can reach the weeds where the hoe can’t,” he adds.
“For maximum effect, finger weeders should be used as the weeds emerge. They have a working depth of between 2-4cm and are suitable for rows of 25cm upwards. There are different sizes of rubber fingers to choose from, depending on row width.”
A tined harrow can be fitted to weed along the row and level soil. And to bring an extra level of precision, there’s also the option of ISOBUS controlled sprayer-style GPS section control, points out Nick.
“With individual hydraulic rams on each parallelogram linkage, the Muller ISOBUS controller is able to lift individual row units as they reach previously cultivated ground.
“This is a particular benefit when working in fields with angled headlands – the system is able to detect when the hoe shares are reaching the end of the run and automatically lift them out of work to avoid hooking out plants on the cross-drilled headland bouts.”
Not only has the performance been good, but Gareth says the backup service has also been as great as he’d expected. “Because it arrived fairly late in the spring, it literally went straight to work on sugar beet rows. But we had brilliant support from the Opico team, who came out with us a number of times and helped us work through different feet options, for example, and how many legs we ran down the rows.
“Tillet and Hague were also fantastic and helped with educating the drivers on how exactly the system works and how to set it up for different crops.”
Reflecting on last year and looking ahead to this season, Gareth says he’s already got repeat customers lined up, as well as growing interest from new ones. “Traditional hoeing has tended to be a very steady job which understandably causes concern for those thinking about going down this route.
“However, due to the nature of the machine, it needs to be put on a conventional tractor which helps boost output. What’s more, because of the camera system you can work far more accurately and quickly than previously possible with this kind of equipment.
“You do have to keep an eye on speed, and if you’re not careful there’s risk of burying the crop so one thing we might look at this year is crop guards, which run either side of the hoes and stops the soil getting moved too far. These are available as an optional extra.
“But overall, it’s a fantastic bit of kit which will really help us, and our customers, to keep growing sugar beet.”
Novel usage and new opportunities
Being the only contractors in the area to have such equipment in their fleet, Gareth says the investment has opened doors to new and novel contracting opportunities. “We’ve had a lot of interest, particularly from organic growers.
“We didn’t have a huge number of organic customers prior to this, but we’ve picked up a lot more since the machine arrived. Sugar beet, in particular, is an incredibly hard crop to grow organically, so we found these farmers were wanting us to hoe their crops multiple times early on to help them keep on top of weed burdens and effectively maximise control.”
As well as this, last year presented Gareth with the opportunity to use the cultivator in quinoa. “That came about through a local fruit farmer who wanted to put a block of land into cereal production for three years.
“In the first year, he chose to grow organic quinoa. We went and drilled it with our 4m combi drill and then followed up with the inter-row cultivator. Being slightly narrower, to make it work we blocked off every other row spacing and weren’t sure how well it was going to work.
“In the end, we only ran one leg down but put a wider foot on it and the results were great.”
Farm Facts
Gillow Farm, Saint Owens Cross, Hereford
- Farm arable area: 800ha plus contracting.
- Soil type: Sandy loam
- Mainline tractors: John Deere 6250R; 6230R; 6195R; 6175R; 6155R x 2; Valtra T230
- Combine: New Holland CR8070; CX 7.80; CX 8050; Claas Lexion 630
- Cultivation equipment: Lemken Juwel 6f plough; Pöttinger Servo 5f plough; Lemken Karat 4m; Spaldings Flatlift; Heva 8.2m rolls
- Drills: Lemken 4m combi; Amazone 3m Centaya and combi disc; Väderstad Tempo 12-row x 2; Moore Unidrill