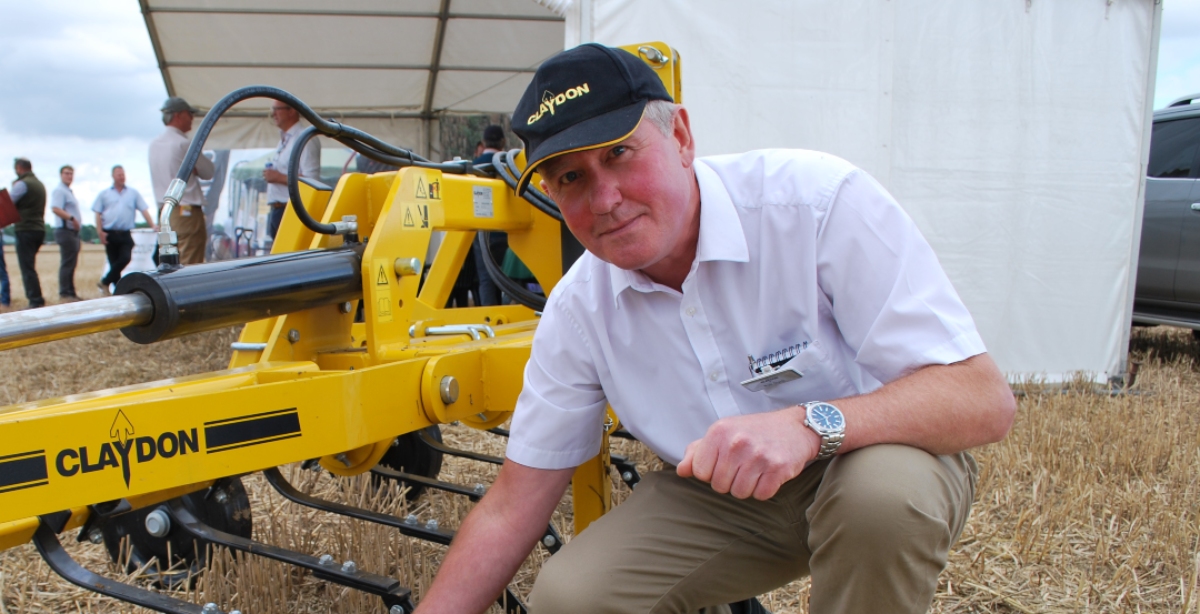
Soil management can’t possibly change fast enough to counter basic payment cuts. But farmers, advisers and machinery makers are increasingly determined to have a go, Charles Abel reports.
Natural biology and rooting are what structure soils, which metal can give a bit of help with, but it really is a case of prevention being better than cure.
By Charles Abel
Soil management is stuck in a rut on too many farms, with a lack of expertise and real barriers to better systems slowing a transition that most now agree is essential.
Economics, efficiency, government regulations and end-user requirements all point in one direction. But achieving meaningful changes to soil management on-farm is far harder, experts agree, with even the best eager for external expertise to move forwards.
With support payments fast dwindling the heat is on to strip costs out of establishment systems and enhance crop productivity – with soil health the buzzword. Achieving it will be no mean feat – putting off-farm expertise at a premium.
The good news is that the expertise already exists. But it requires big changes in thinking, something many farms haven’t begun to consider yet. “We are finding through AHDB Benchmarking activities that farmers are investing in equipment to reduce soil movement, but not seeing a reduction in costs but are seeing a reduction in yield. This highlights the need to develop the farms soil management plan beyond the equipment,” says Harry Henderson, national AHDB Cereals & Oilseeds Knowledge Exchange manager.
Getting to grips with the fundamentals is key, agrees Lincolnshire-based independent soil management guru Philip Wright, who pinpoints numerous opportunities for improvement.
It all ties in with a drive to use the best expertise to apply constant pressure to operational costs, says Velcourt’s James Taylor, who manages FarmCare’s Down Ampney farming business, which hosted the Tillage Live event in September.
“Our goal is to move as little soil as possible and put on as few inputs as possible,” he comments. But that can’t be at the cost of good establishment. “We won’t skimp on establishment – if it needs the plough we’ll plough, if we can use direct drilling, we’ll direct drill.
“The real focus is on the nitty-gritty of operational costs, looking at labour costs, diesel costs, travel times, not just the capital cost of new tillage equipment.” Those are all crucial when looking at new equipment, not just the capital cost. “Squeezing operational costs can soon save £10/ha,” he says.
“There’s no silver bullet for correcting soils overnight or indeed slashing establishment cost in just one season” adds Kieran Walsh of Velcourt Agronomy Services. “Get the agronomy right and the soils in good order and the numbers will follow. We all know that, so it’s about keeping the discipline, doing the right thing at the right time, it is a key responsibility.
“Be willing to try new things, think outside the box and find solutions not problems. When trying anything new, ask to see the independent data sets and measure these new ideas. But with such a multitude of people telling you how to do it, many may not actually be right. There’s a lot of newly-minted experts out there, so question everything they tell you”
Patrick Levinge, head of Velcourt Agronomy Services agrees. “People’s understanding of what you can do with the soil is changing. Farming used to spend all its time inverting the soil. We do that much less now, and it is better. But it’s taken several generations to realise. It’s not a quick process.”
The LEAF/FWAG-backed UK Soil Carbon Code, supported the Environment Agency, could help further focus attention. But the need to increase soil productivity to maintain a level playing field in the face of declining support payments, is the main driver. “Even the best need help to make the changes, because they’re big changes.”
Slash tyre pressures
Soil management guru Mr Wright urges more farms to make time to check soils, and to empower operators to do the same, to query cultivations if they don’t feel right. “Let them be your eyes and ears, get them to dig holes too, and say if the tractor doesn’t feel right, if a compromise might be worthwhile.”
He accepts that many farms face real challenges coping with time pressures across big crop areas, hitting attention to detail. “It isn’t always easy to find time to check soils, but it can make such a difference.”
He has witnessed a surge of interest in improving soil management. “A number of my larger clients have adopted a country-wide approach to lower tyre pressures, for example, and consciously doing less, in terms of wheelings and cultivations. But it’s a long term thing and seasonality can still over-ride changes being made.”
Drilling tractor tyre pressure is a wonderful case in point. Combine yield meters may show average output across a field, but utterly miss the impact of compaction in the zone around the drilling tractor tyre’s footprint, he notes.
Three years of in-field studies suggest massively reduced tyre pressures could bring hefty yield responses, purely because soil compaction is reduced.
Get the agronomy right and the soils right and the numbers will follow.
His work looked at a chalky soil on the Lincs Wolds and a heavier Fenland clay loam. Dropping the drilling tractor tyre pressure to 1.0bar (14.5psi) sounds radical. Taking it down to 0.7bar and 0.5bar extreme. But with advice from the tyre supplier, to ensure all equipment settings meet their recommendations, it can be done with confidence, says Mr Wright.
What was the outcome? Where wheat was un-trafficked it yielded 100%. By contrast wheat from a zone affected by a 1.0bar tyre yielded just 60% – a visible yield impact. Dropping tyre pressures even lower, to 0.7bar, lifted yield to 70% of the un-trafficked area. Dropping to 0.5bar, a tall order, lifted yield to 94% of the un-trafficked area.
It sounds extreme, raising fears of over-heated tyre walls, bead slippage and the like. But for a tractor pulling a 3m cultivator drill the yield impact across a whole field is substantial. The tyre footprint could create an affected zone 1.5m wide for each pass, meaning half the field suffers soil damage. Even with a 6m drill the yield impact will be significant.
Clearly, the tyres fitted need to be suitable for such low pressures. But options are widely available and could be worth specifying when purchasing a tractor. “Get the tyre manufacturer to come out to the farm, with their kit, including weigh cells, to define the right operating parameters, so any potential equipment failures are covered. I’d never recommend doing it without the tyre manufacturer’s support. It’s something they will do.”
Whole-system approach
Manufacturers are well placed to help farmers identify suitable equipment and get the best from it, says Rob Dunk of Claydon. But it all needs to start with a soil pit.
“It’s the acid test. When did you last dig a soil pit? Spade holes are vital to see and smell what’s happening in the soil, to check worm numbers, they’ve got to be the start, before we look at any demos. It’s not a trick question. We genuinely need to know what the issues are, and what needs doing.”
He has been struck by how many people are now prepared to pay to seek better soils advice. “Farmers paying to get in front of key speakers at Groundswell proves the point. They can see establishment costs need to come down, it’s economics, over and above any benefits for carbon, the environment, soil run-off and the like.”
But inertia, nervousness and brand snobbery can all get in the way. “It often needs a stepwise change from what’s been done for generations, by father, grandfather and great-grandfather. It/s not easy, which is why it’s good to be able to see things in action, and ideally locally.”
Claydon has its own 400ha farm where kit has been developed, but also places great store by local demos too, so farmers can see equipment working in conditions relevant to them.
Its new TerraBlade inter-row hoe is now on 100 farms, including Velcourt’s Stamford operation, where it complements a 6m Horsch drill. Like Claydon’s own drill seed is placed in 12-15cm bands at 30cm centres, leaving a 15cm band between ideally suited to mechanical weeding using the hoe.
“It’s just part of a whole system to learn and change, starting with the combine leaving 6in high stubble, a straw rake to chit weeds and volunteers, and an inter-roe hoe to help in the establishing crop. It needs to be a whole system approach.”
Groups have the edge
“Farmers like any business, follow what makes sense financially,” says Alex Wade, AHDB SE Cereals & Oilseeds Knowledge Exchange Manager. “Where Monitor Farm groups get together and use benchmarking to look at costs, on local soils, in a local climate, with neighbours they know, they get answers to their ‘so what’ questions – it shows the real benefits.”
Moving soil is a big cost, with many farms still spending too much on it, says Philip Dolbear, a former HSBC senior agriculture manager and now AHDB SW Cereals & Oilseeds Knowledge Exchange Manager. Investing in new kit is a big step, but unless it is matched by a real understanding of how to manage soils in a new system, it can fail to deliver desired benefits.
“Regenerative farming, min-till, low-till – they’re buzz words that create peer pressure to make changes, but there needs to be real understanding to bring the desired benefits.”
That expertise does exist. Soils, together with RB209 nutrient work, are the AHDB’s second biggest arable budget item. “The principles and protocols are all there, the research has been done,” says Mr Henderson. “It’s more about putting that expertise into practice in a farm-specific way, which more farmers are certainly looking to do, judging by attendance at our webinars, specialist events and Monitor Farm activities.”
But many are yet to get involved. Mr Wade points to the anxiety of stepping away from the tried-and-tested. “It’s an old saying, but a true one, that too many farmers, and too many tractor drivers, simply enjoy cultivating.”
Many farms have yet to develop a suitable alternative to the hamster wheel of more mechanisation, more inputs and more crop headaches that led to the industry-wide move to adopt integrated farming techniques. “For too long generous support payments allowed farmers to spend their way out of trouble, but that’s really coming to an end now.”
Costs are under fresh scrutiny, but a lack of confidence in new approaches to soil management can hamper progress. Working with neighbours to improve that expertise can help a lot.
“It is something we need to get across to more farmers, the level of expertise we have, which could really help, even on smaller farms, of say 200 acres,” says Mr Henderson. “They could actually be ok, even with the support cuts, if they can adjust their systems over the next few years. But the changes need to start now, not when the 2024 farm accounts start showing the impact of support cuts.
Cover crop loosening
Another area of interest is soil-loosening through cover crops. “Cover crop rooting can reveal where there’s a problem in the soil – if you get a spade out and have a look,” says soils expert Philip Wright.
“All you need is a spade and 10 minutes! Even tillage radish can hit a problem, which will be very obvious if you just have a look.”
Using a sward-lifting machine, set at the right depth, is a great example of synergy between roots and metal, helping the cover crop do what it is meant to do, pushing roots further down the profile, he comments.
“Natural biology and rooting are what structure soils, which metal can give a bit of help with, but it really is a case of prevention being better than cure,” he advises. So check soils, and check regularly. “It’s frustrating that more people aren’t digging soil holes, but it’s also pleasing that so many are doing so now.”
“So, if the money is there, take heart that there is time to evolve your system, and maybe take a bit of a yield hit now, while there is some leeway, so when support payments have gone you’re in a better place,” Mr Wright concludes.
CPM Feedback
Tell us what you think. Write to editor@cpm-magazine.co.uk