The right handler can bring a multitude of benefits on farm. CPM rounds up some of the most recent launches.
It offers a zero-emissions load handling solution with no compromise in performance or productivity.
By Charlotte Cunningham
Perhaps one of the most underrated bits of kit on farm is a materials handler, but it’s fair to say that few would argue that they’re one of the most essential.
That said, upgrading your current model might not be top of the priority list, however, innovative features in the market are boosting efficiency – bringing with them cost and time-saving benefits.
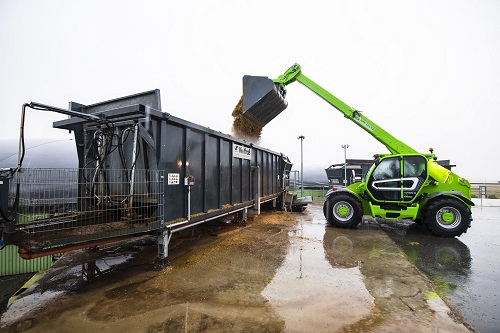
Merlo has added to its heavy-duty offerings with the introduction of the new TF65.9TCS170-HF telehandler.
CPM has picked out some of the most interesting new material handlers, including a new ‘emission-friendly’ option for those who are looking to future-proof their investments.
JCB
As the industry moves more and more towards creating ‘environmentally-friendly’ kit, JCB has announced the launch of its first ever electric Loadall model – the 525-60E.
Designed to deliver the same performance as the conventional diesel-powered machine, JCB says 525-60E offers a zero-emissions load handling solution for use in agriculture and commercial horticulture.
“The launch of the JCB 525-60E Loadall takes equipment electrification further into agricultural markets, with no compromise in performance or productivity,” says Tim Burnhope, JCB chief innovation officer.
So how does this all-electric innovation work?
The 525-60E uses two electric motors, one for the driveline and the second to power the hydraulic system. The 17kW traction motor drives through a permanent four-wheel drive dropbox, to JCB drive/steer axles, he explains.
“The 22kW hydraulic system motor powers a fixed displacement gear pump, delivering a maximum 80 l/min of flow. Flow is proportional to joystick position and the lift end is controlled by an electro-hydraulic valve block, with hydraulic regeneration on boom lower and retract.”
According to JCB, the electric motors are 85% efficient, which compares well with the 45% efficiency of a diesel engine. “Extensive analysis of customer duty cycles, through JCB’s LiveLink telematics system and on-site studies, tests and evaluation, has allowed our engineers to optimise the machine’s battery to meet customer requirements,” adds Tim. “The 96V Lithium-ion battery, is capable of providing full-shift operation.”
The traction drive motor utilises regenerative braking, instead of a traditional braking system, topping up the battery in the process. The hydraulic system also regenerates flow while lowering the boom, reducing the power requirement, and extending operating hours. The brake regen function automatically turns off when the battery is fully charged.
The machine has the same on-board charger as other JCB E-Tech products, capable of recharging the battery in eight hours using a standard 240V, 16A electrical supply, notes Tim. “An optional JCB Universal Charger can be used for a rapid top-up during breaks, in as little as 35 minutes.”
According to JCB, a secondary benefit of electric operation is a significant reduction in noise levels, making the Loadall an attractive machine for operators behind the wheel, as well as for use in situations when working close to other people, such as in vegetable grading sheds and glasshouses. “The 525-60E delivers an in-cab noise level of just 66.7dB, while the external level is 92.2dB,” explains Tim. “A white noise reversing alarm is available as an option, to warn site workers of machine movement.”
External dimensions are unchanged from the diesel model and the 525-60E offers the same 3.7m outside turn radius. Maximum lift capacity is 2500kg, with a 2000kg maximum load at the full 6m lift height.
Also new from JCB is a range of Loadall telescopic handlers featuring more powerful Euro Stage V emissions-compliant engines – and offering the DualTech Variable Transmission on additional models.
The transmission, which combines hydrostatic drive for low speeds and powershift mechanical direct drive at faster speeds is no longer reserved for the top-specification Series III Loadalls – making it accessible to more farmers and contractors, says managing director, John Smith. “It can now also be specified for Agri Super versions, as well as the smallest full-size Loadall – the 532-60 – for the first time.”
“DualTech VT has been successful and popular in our top-spec agricultural Loadall and now we’re making it more accessible to a wider range of farm businesses by adding it to the Agri Super equipment package and to our 3.2t, 6m 532-60 introduced in early 2020.”
Merlo
Merlo has also added to its heavy-duty offerings with the introduction of the new TF65.9TCS170-HF telehandler.
According to the firm, the TF65.9TCS170-HF has been developed specifically with demanding applications in mind – making it a great option for agricultural use, says general manager, Shaun Groom. “Offering a maximum lift capacity of 6.5t and a maximum lift height of 8.80m this new heavy-duty handler offers improved performance.”
Looking at the nuts and bolts, Merlo’s latest launch is fitted with a four-cylinder, 4.5 litre FPT turbo diesel engine, producing a maximum of 170hp. “The Stage V engine is equipped with both Diesel Particulate Filter technology and a Selective Catalytic Reduction system, and users can be sure of having sufficient power for all on-farm tasks.”
The hydrostatic transmission is fitted as standard along with the Eco Power Drive TOP electronic transmission control. “This feature allows the operator to select to automatic engine response while using the hydraulic functions, giving efficient – and the right amount – of power for all actions,” explains Shaun. “Furthermore, it’s possible to activate the Eco and Speed Control functions in order to maximise ease of use and overall performance all while minimising fuel consumption. A maximum transport speed of 40 km/h is standard.”
The TF65.9 is also equipped with the brand-new Adaptive Stability Control System, he adds. “This system comes as standard with an in cab 25.6cm LCD colour screen that displays the load dynamic and capacity chart, which is updated in real time. The information from the load being lifted, attachment in use and the machine stability index.
“This feature also allows the adjustment of the reaction and speed of hydraulic functions, setting and defining of possible load capacities for each attachment, as well as recording and storing the load cycle data.”
A new load sensing and flow sharing hydraulic system HF (High Flow) is fitted as standard. “Utilising a high capacity 160 l/min variable displacement this heavy-duty hydraulic pump offers responsive and high output hydraulic for the most demanding of tasks,” adds Shaun.
Additionally, the new model can be specified with the MCVTronic CVT transmission. “This Merlo designed and built feature increases the torque at the wheels at low speeds, for maximum pushing power, whilst optimising efficiency at higher speeds such as those used for transport.”
The Merlo designed and manufactured cab is a modular-type construction with a roomy overall internal width of 1010mm, making it one of the largest on the market, claims Shaun. “Operator comfort is further enhanced with the patented CS cab suspension fitted as standard. The Merlo pioneered hydro-pneumatic cab suspension system maximises comfort for the operator by reducing vibration, shock loads and fatigue, helping maintain operator safety.”
Claas
Last autumn saw Claas announce a new addition to its Torion range – the Torion 738 T Sinus, Claas’ first telescopic wheel loader.
According to Claas product manager? Steffan Kurtz, a key benefit of the Torion 738 T Sinus is the central telescopic boom, which boasts a bucket pivot-point height of 4.96 m. “A maximum payload of 2300kg in pallet fork mode on level ground is accommodated, even in articulated position with the boom fully extended. The maximum tipping load articulated is 3800 kg and the maximum loading and stacking height with loading forks is 4.8m – with a full reach of 2.69m.”
Ample hydraulic power for lifting and stacking tasks is available, thanks to the hydraulic capacity of 93 l/min, while large oil consumers can be accommodated with an optional additional high-flow pump, providing a further 28 l/min for external implements such as sweepers and mulchers, adds Steffan. “The maximum operating pressure is 230 bar. A double-acting control circuit can be fitted as additional equipment at the rear, while at the front, a maximum of two control circuits can be optionally fitted for external implements. The hydraulics also feature free flow return and an oil overflow line on the implement carrier.”
A neat feature is the optional Smart Loading package, targeted at repetitive loading tasks carried out over long periods. “This provides features for greater user convenience, and significantly reduces operator stress. Functions include the programmable lift height and lowering depth limit, automatic bucket return, dynamic load limit, and display of telescopic boom and implement carrier operation on the 23cm touchscreen terminal located on the right A-pillar,” he explains.
“A feature unique in the marketplace is automatic retraction of the telescopic boom in combination with automatic bucket return and transition to the lowest lowering depth limit point. The boom and implement carrier are moved to their stored positions with a single movement of the joystick. The optional end-of-travel damping for the lifting and lowering kinematics can also be set individually on the terminal.”
New Holland
New Holland recently announced upgrades to its D Series wheel loader range with improvements focused on enhancing driver experience and delivering benefits in Total Cost of Ownership and reliability – which the firm says is key to customers’ operations and businesses.
According to Alain de Nanteuil, New Holland light equipment Europe leader, the range is already really popular with forage-harvesting contractors and biogas plant owners. “Our machines push and climb fast for up to 17 hours a day when clamping silage, for example.
“They are equally ideally suited to biomass digester loading, and the improvements we’ve made only increase their versatility and functionality.”
The two major improvements are focused on fuel usage and maintenance costs which, together, New Holland claim can deliver over £17,000 in savings during the machine’s lifetime. “The Total Cost of Ownership and the reliability of a machine is something that is really important to our customers and we feel we’ve made some real developments in this area,” says Alain. “So, the first innovation is the new ‘Smart Work’ mode which helps to deliver up to 10% fuel savings.
“The other improvement is the extension of service intervals from 500 to 1000 hours, which has the potential to slash maintenance costs by up to 20%.”
User experience has been improved through the new touch-screen, which features ‘quick access’ buttons, as well as self-levelling mode for easier fork handling, says Alain. “The 20cm colour display now features a touch screen for a more user-friendly operation.
“The new configurable quick-access buttons also allow operators to use the screen without interrupting operations.
The self-levelling mode makes fork handling easy, he notes, ensuring they remain parallel with the ground, and the payload scale is designed to accurately monitor the quantity of material loaded. The tyre pressure-monitoring system ensures tyres are always operating at the optimal pressure, reducing fuel usage and tyre wear, he adds.
“The visibility has been enhanced by the one-piece windshield and the rear-view camera can be further improved by the optional Enhanced Lighting Pack. With 43,000 Lumen, it turns night into day for safe and efficient night-time operation.”