The flagship of Grimme’s potato harvester fleet, the Varitron 470 Platinum boasts a range of features. CPM visits one in Sussex to get an insight into what these do and to find out if the machine meets expectations.
It doesn’t take long to hoover up a field with this Varitron.
By Tom Allen-Stevens
The weather is ideal and ground conditions near-perfect for harvesting the Gemson salad potatoes, destined for the salad, pre-pack market. But the Grimme Varitron 470 harvester has come to a halt in the 4.5ha field at Donnington near Chichester, Sussex, farmed by Greenseed.
Arable foreman James Silvester doesn’t seem too fussed, however. “There seems to be a problem at the grader that’s holding things up,” he explains. “No one likes hanging around at harvest time, especially after last year. But it doesn’t take long to hoover up a field with this Varitron, so the wait won’t be much of a worry.”
Greenseed grows over 1600ha of seed, salad and new potatoes across East Anglia, Sussex, Northumberland and the Scottish Borders. The operation based at Chichester comprises 320ha of salad potatoes and 80ha of seed, with a cold storage facility of 15,000t.
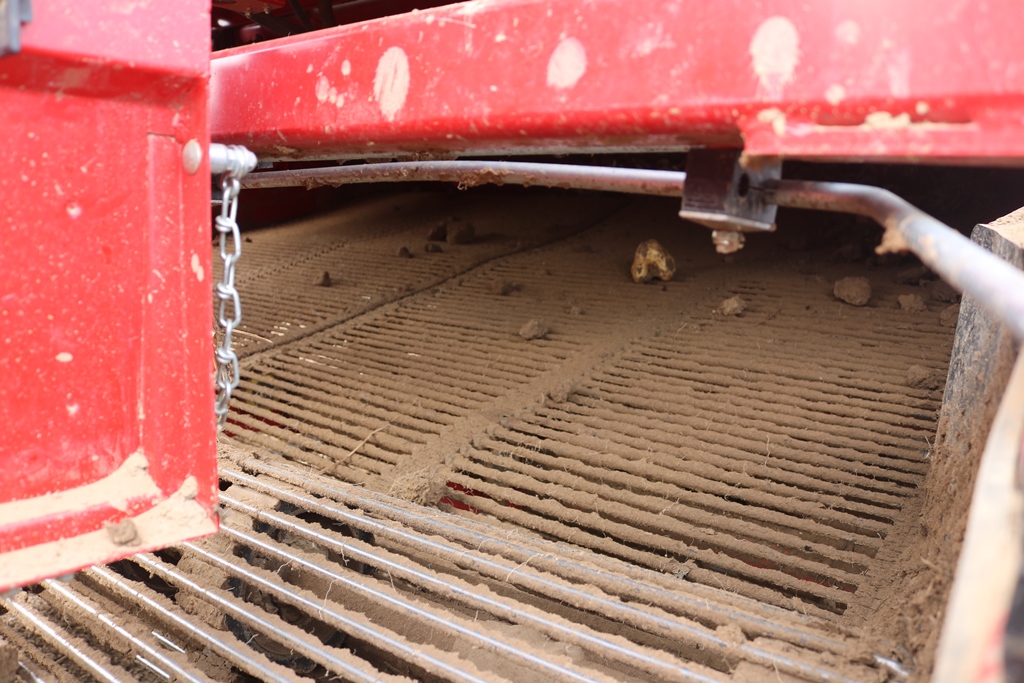
There’s a gentle shallow intake over the webs with less roll back and a massive sieving area.
It’s from there the trailer eventually arrives and the Varitron growls back into life and quickly empties its 7t bunker, continuing its run along the four rows of silty clay loam. Farm manager Matt Carr joins the team in the field and explains that the potatoes dropping gently off the elevator are destined for the high-value end of the pre-pack market.
“It’s all about quality,” he says. “Everything we harvest is less than 45mm in diameter and we look for a perfect skin finish. That can be a challenge off these soils, but we’ve found the harvester makes such a difference.”
The business purchased two Grimme Varitron 470 Platinum harvesters for this season, and had previously been running both in the same field. One has now gone to Greenseed’s Cambridge farm while the other finishes off the last of the pre-pack crop in Sussex.
“We had a pair of Grimme Tectron four-rows last year, and felt that was a step on. But the Varitron is a game-changer – there’s a large web area with a shallow run and less bottlenecks. It’s gentle on the crop from the share to the elevator, which maintains our premium quality,” notes Matt.
It’s not just the crop that the business is keen to look after, as James explains. “From a soil condition point of view, a self-propelled harvester does a much better job. The difference is the bunker which adds flexibility to unloading and leads to less travelling in the field. Of course the Varitron’s a larger machine, but the weight distribution on its Terra tracs is much better than a tractor and trailed harvester.”
The business moved over to self-propelled harvesters several years ago, although still runs a trailed GT 170 two-row with picking table for tramlines and odd runs in fields to maintain consistency at the grader. “Harvest is a 24-hour operation for us, which previously meant a team of ten operators on four trailed two-rows. We now have the two Varitrons running 24 hours and the GT during the day with half the team we needed before. But our throughput has increased while it’s getting harder to find the skilled labour.”
The crop itself was topped prior to desiccation with Spotlight (carfentrazone), leaving 100-150mm of haulm. “Preparing a salad crop for harvest when it’s still trying to grow is always a challenge, so we have the front topper, but rarely use it on the pre-pack crop,” says James.
In the harvester it’s the Double-MultiSep unit that does most of the haulm separation. This set-up has two sets of 8mm spiral segmented rollers (eight in total), alternating with rubber rollers at the front while steel rollers at the back minimise losses. “It took a while to set up the speed on the independent hydraulic drives to the exact specification we wanted, but we had plenty of technical support from Grimme to get it right,” says James.
“What we like is the gentle shallow intake over the webs – there’s less roll back and it’s a massive sieving area, which all helps for a cleaner, less damaged crop. We were dubious about the Optibag to start with, thinking we’d lose a lot of crop through the slots, but it’s worked out well and reduces the loose soil that comes through.”
By now Greenseed operator Chris Newell has reached the headland, skilfully bringing the lengthy machine round and lining up for the next four rows. “It’s a bit less nimble than the Tectron, but surprisingly manoeuvrable, and once you get your head round it, it’s a doddle to drive,” he reports.
As the trailer draws alongside, the camera switches to the elevator and Chris makes some minor adjustments before unloading. “The elevator flows better than on the Tectron and bends in three places, which is useful. The reversing bunker is genius – we had a fault with it early on which made you realise just how handy it is not having to unload every last potato.”
The harvester’s been moving along at about 5-6km/h, but Chris crosses a footpath into a heavier part of the field and slows up to around 1.2km/h. “This is as slow as I’d want to go, but the web speed adjusts automatically, which gives you one less thing to worry about.
“That’s just as well, because in this field there are places where you need to adapt the share height. The Share Delta Control does a decent job lifting four rows at a time, but it’s good to be able to adjust individual shares it as you don’t always plant rows in pairs,” he notes.
The produce coming into the bunker in this heavier part of the field is bringing with it more soil, but Chris is still happy with the result. “The Varitron does a much better job than the Tectron ever did – it has a better cleaning capacity with longer webs. All-in-all it’s a better machine and I’d take it any day over any other.”
So maybe that has more to do with the new Comfort Cab, standard across the new Platinum range of harvesters? Chris smiles – “I’m happy to sit in here all day,” he says.
Features bring flexibility and optimum output
From the front to the back, everything about the Grimme Varitron 470 Platinum is geared towards optimum harvesting throughput while being gentle to the crop, says Grimme specialist Ed Hodson. He picks out a few features that ensure the harvest operation goes smoothly.
“Starting at the front, the topper is easily removable and has a road transport trailer. Moving to the intake, this is set at a slight angle over the four rows to funnel the crop onto the first main web,” he explains.
One aspect Ed’s keen to point out is the web itself. The crop passes along a sieving area of up to an impressive 18.1m² before it reaches the MultiSep unit. “Although the machine must be narrow enough to meet maximum road-width legislation, there’s full width separation. Hydraulic drive to the web and all rollers on the MultiSep allows for infinite adjustment, while the rollers themselves can be tailored according to how aggressive you need the separation.”
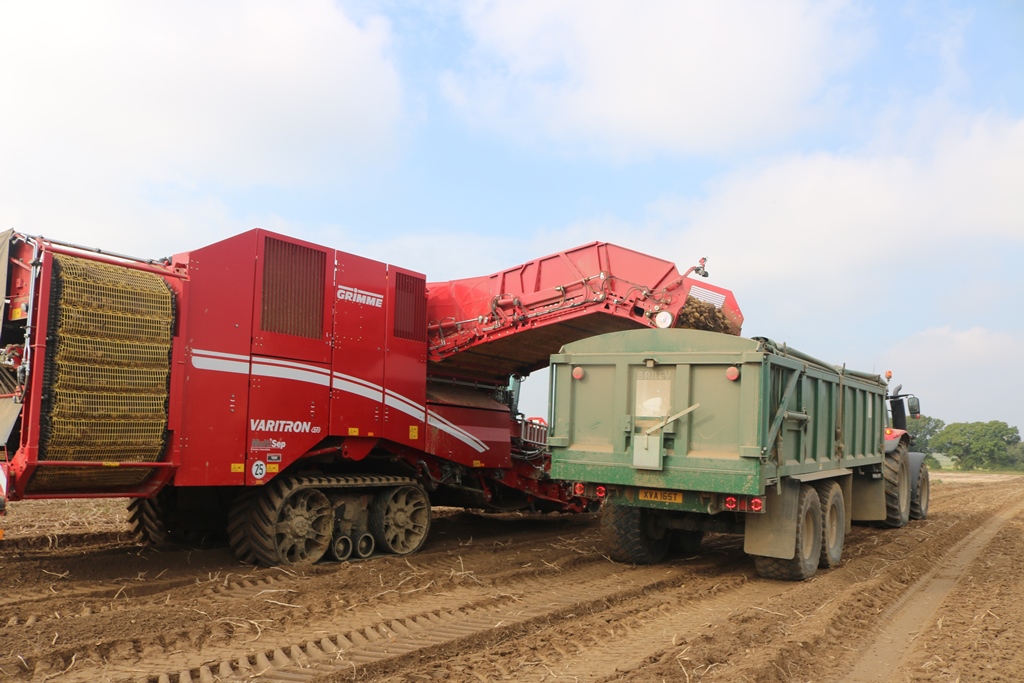
The unloading elevator itself has a 600mm extension and is set in three sections.
Optibag is an option for the ring elevator at the back. The crop is held in a mesh, rather than a solid sheet, allowing further soil separation. The pockets are made up of individual sheets clipped to the frame, so replacing one is a relatively simple operation, notes Ed.
“A key feature on the Varitron 470 is the generous 7t bunker, which allows you to travel 390m in a 50t crop before you need the unloading trailer. The belt advances automatically when filling and a unique feature allows it to reverse, that gives the operator some flexibility when unloading.”
The unloading elevator itself has an extension of around 600mm long. Set in three sections, it gives the operator plenty of control over unloading into the trailer to minimise drop height, notes Ed. “It takes just 40secs to unload the 7t bunker.”
Grimme’s Platinum range of harvesters come with a Stage V compliant Mercedes-Benz engine with the Varitron 470 delivering 460hp. “That’s about 10hp more than some other harvesters, but it’s displacing some three litres less, which reduces fuel consumption by around 30 l/ha with no loss of performance.”
The Varitron 470 Platinum is the flagship of the Grimme fleet and Ed believes it’s suited to the upper end of mid-sized growers with upwards of 200ha of potatoes to harvest.
“It delivers 67% more capacity than a two-row harvester but you’re not paying two thirds more for it. That also means you can reduce manpower and increase timeliness at harvest. Moving from a trailed to a self-propelled system frees up tractors and the bunker offers the big advantage of less downtime,” he adds.
All Grimme self-propelled harvesters now benefit from extended two-year warranties, introduced last year. This can then be further extended to up to five years for those who opt for the Protect warranty package. “This Full-Service package includes an annual inspection and routine maintenance, so you can fix your costs,” notes Ed.
Fingertip control of smart technology
Grimme has picked up a string of DLG medals for the innovations the company’s added over the years and these are delivered to the operator via the Ergodrive joystick control unit.
Introduced across the sugar beet harvesters and then brought into the Varitrons, the joystick has five buttons to control ram functions, such as share height, or topper lift and lower. Field in and out can be assigned to the buttons, or the unloading elevator. Two scroll dials are included in the joystick, with a further four to the right-hand side to adjust the speed of the intake web, MultiSep or ring elevator, for example.
Lifting depth is handled by Terra-Control, which earned Grimme a DLG silver medal when it was unveiled at Agritechnica in 2005. The system uses special hydraulic cylinders, guided by the diablo as it runs over the ridge, to set the depth of the share. A strip of sensor tape inside the ram monitors the diablo position as it moves up and down and passes this information through to the control panel.
There are three functions that can be set – depth control, ridge pressure and depth sensitivity. Depth control can be set according to field conditions, so additional pressure can be applied to the potato ridge to improve flow without affecting digging depth.
Particularly useful on a four-row machine is Share Delta Control. While the diablos move independently, they set the height of the shares on a plane. Share Delta Control allows one side to be adjusted individually to keep the share level and prevent crop damage.
Visual Protect is another innovation that won Grimme a DLG silver medal in 2007 and prioritises which of the machine’s eight cameras feed the displays in the cab. If there’s a problem building, detected through monitoring pressure to the hydraulic drives, an alarm sounds and one of the monitors switches to the camera where the potential blockage is, so the operator can take the appropriate action. When unloading, the monitor also automatically switches to put the elevator in view.
Speedtronic is a feature aimed at minimising problems associated with uneven crop flow. The hydraulic drive to the main webs maintains a constant speed, irrespective of forward speed. But if the crop intake becomes lighter and the operator steps up the forward speed, the speed of main intake web self-adjusts to match, allowing for a more constant speed of crop throughput. Likewise the intake adjusts if the harvester comes across a thick patch and the forward speed drops. The drive to the webs can also be reversed to easily clean out any blockages.
One recent development and constantly evolving is MyGrimme, the company’s web portal for its telematics. This free service transfers all manner of data direct from the machine to the Cloud, which can then be viewed from the farm office or mobile phone for monitoring harvest. It also allows remote access by technicians to diagnose a problem, and there a geo-fencing feature so if your harvester passes outside a certain radius from your farm, it sends you an alert.
Machinery Masterclass
Technology is advancing fast, and the capabilities of equipment found on farm far outstrips what was available just five years ago. For growers who embrace the change, the potential to cut cost, refine production systems and boost output is immense. But how can you make an informed choice about whether an innovation will deliver the refinements you seek if you’ve not operated it before?
This is where Machinery Masterclass comes in. In this article, sponsored by Grimme, CPM has worked with the manufacturer to get a true user experience and an insight into the technology advances it has introduced. We hope this will bring you a ‘try before you buy’ feel for specific features found on this item of machinery and help you remain at the forefront of progression in crop production.