With few alternative options, mechanical weed control is essential for organic growers. CPM finds out how one grower in Somerset has boosted his accuracy with GPS.
The true value of this kind of technology is now being realised.
By Charlotte Cunningham
When it comes to weed control in arable rotations, it’s often said that conventional growers can learn a lot from their organic neighbours. But that’s not to say organic farmers don’t face challenges too.
Farming over 180ha in the heart of the Brendon Hills, Somerset, grower Robert Herrod knows these difficulties all too well. “We made the transition to organic farming in 2006 as we felt it was the right thing to do for the land and the wider environment, but it does have many challenges, and for us the predominant issue is ensuring robust weed control.
“We rely on machinery to do the job and if it isn’t done as accurately as possible, it has the potential to wipe out an entire crop.”
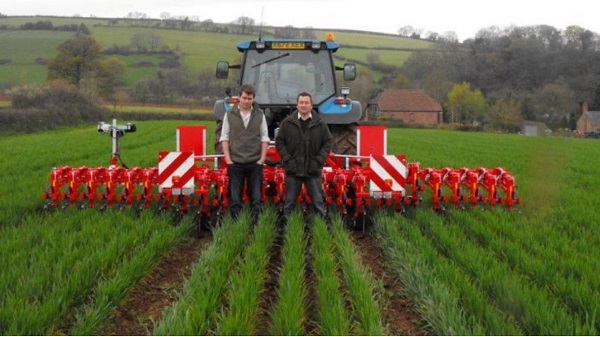
For organic grower, Robert Herrod (right), reliable weed control is the main challenge
Four years ago, Robert – alongside son, James – invested in an interrow camera-guided hoe to help improve accuracy. “Machinery is becoming more advanced and so the most effective way we’ve been able to deal with weed issues is by implementing a minimum tillage approach. This means no ploughing to bury weed burdens, but instead trying to kill them on top of the soil with cultivators.
“Once the crop has established, we then go in with grass harrows, followed by the interrow hoe, and finally the Weedsurfer which chops the heads off of any problem weeds sticking out of the top of the canopy, such as wild oats and charlock.”
However, while the purchase of the hoe proved to be a good move, there were still a few weed issues coming through in the established crop, spurring Robert on to do more and get more creative with his approach – which is where the farm’s journey with New Holland’s GPS system started.
In 2018, the farm began looking into the role GPS could potentially play in terms of squeezing that extra efficiency from the interrow hoe, and with promising results, started to experiment with New Holland’s IntelliSteer system, using an RTX range point signal with sub 15cm accuracy.
So how exactly does it work?
“IntelliSteer is a fully integrated New Holland designed and developed automatic steering system, which contributes to our Precision Land Management (PLM) strategy,” explains George Mills, area sales manager at New Holland.
“In a nutshell, it’s a guidance solution that offers complete machine direction control at the touch of a button and uses a single integrated display with the IntelliView IV for tractor functionality such as setting spool valve flow rates and configuring implements via ISOBUS implement control, as well as viewing guidance lines and coverage maps – while having the ability to transfer data via USB – which allows the operator total control of which information they view.”
The screen can be set up for separate users, for example, one driver may wish to view information in imperial measurements, while another may prefer metric, he adds. “This information can all be saved under that individual operator’s name. The screen is also dynamic to accept a camera input, so in the situation of interrow hoeing the operator can watch exactly what is going on at ground level.”
Looking to the technology behind the system, the T3 Terrain Compensation system uses sensors to calculate and correct the roll, pitch and yaw of the machine to help minimise skips and overlaps in areas with rolling terrain and rough ground, with the aim of improving efficiencies, accuracy, or yields – depending on which bit of kit it’s used with. “The 372 antenna receives RTX Range Point and RTX Centre Point signals and tracks global navigation satellite system (GLONASS) satellites to guide the vehicle,” explains George. “This antenna can easily be removed and transferred from tractor to tractor, or even to your combine or forager. The roof-mounted bracket also has the ability to lock the antenna in place to reduce the possibility of theft.”
Though two-way data transfer is still a major hurdle that the industry has to get over, New Holland has made this easier with the competitive line import feature on the IntelliSteer. “This allows the IntelliView IV display to import select John Deere and Trimble straight A/B guidance lines from their displays without the need for desktop software,” explains George. “Users of select John Deere and Trimble guidance systems can now seamlessly share their straight A/B lines with an IntelliSteer system by using this import feature, giving customers running mixed fleets additional flexibility.”
Another novel feature of the IntelliSteer system is Headland Turn Sequencing (HTS) II, which is available as an optional extra. “This system means you can easily record, and store all implement sequences and operations at the headland,” says George. “These can then be played back at the touch of a button. Now, it’s even easier to modify pre-recorded sequences, so when things change, your HTS sequence does as well. It’s simple but it’s a great way to improve repeatability and efficiency – as well as helping to reduce fatigue when working over extended periods.”
Available from the factory or as a retrofit package, the IntelliSteer system is available with integrated factory installed IntelliSteer auto guidance on T5, T6, T7, T8, T9, CX & CR Series combines and self-propelled forage harvesters.
For Glebe farm, the main benefit the system brings is the increased pass-to-pass reliability, explains George. “In Robert’s case, ensuring his interrow hoe is working as accurately as possible is critical for the performance – and effectively, profitability – of his cropping area and this is where the IntelliSteer system comes into its own.”
While the complexities associated with this kind of technology often deters growers from optimising it, getting to grips with exactly how it works has been very straight forward, adds Robert. “It’s an incredibly self-explanatory tool and if you do need any assistance, the support from New Holland is fantastic and available 24hrs a day.”
George agrees and says there’s been a noticeable uptake in this type of precision technology. “It’s no longer just the younger generation that are optimising precision tools – the true value of this kind of technology is now being realised across the board.”
But for those who are a little bit apprehensive about making the jump to this new way of farming, there is also the opportunity to start at a lower level and build up to running a high precision system, he adds. “We’ve taken a modular approach with the system meaning that growers can go in at entry level – using just basic GPS – and then when they’re ready to move on, or level up, they can then add on the self-steering functionality, for example.”
Having seen noticeable benefits from a weed control perspective, Robert has now expanded his use of the system across a number of operations. “We use poultry litter to top dress the crop, using a 16t spreader with rear spinning discs, and have used the GPS system alongside this to ensure an even spread. In fact, we use it when carrying out the majority of our cultivations – from rolling to drilling – and have found it just makes everything so much easier.”
As with any kind of technology, the more you put in, the more you get out, and this is a sentiment Robert echoes. “The more hectares we do with the system, the bigger the benefit will be – not only in terms of accuracy, but also time and fuel saving. For us, it’s all about optimising our productivity and this system is helping us do just that.”
The lowdown on PLM
According to New Holland, its PLM system is all about providing an open, connected, smart, supported solution to growers.
Boasting a full range of correction signals, the modular solution can be used on any machine for a wide range of precision farming techniques, from machinery guidance to crop management solutions, while advanced telematics systems enables users to synchronise in-field working between machines from the comfort of your office.
From a guidance perspective, New Holland offers a range of auto-guidance solutions to meet growers needs, from entry-level manual guidance, via assisted guidance right through to top of the range fully integrated auto-guidance which effectively manages the machine for you.
These solutions can be matched to a range of correction signals, from sub 20cm right down to sub 2.5cm absolute accuracy depending on the individual needs. New Holland offers solutions for its entire range of tractor, harvesting, and crop management equipment, including all implements.
Farm facts
Glebe Farm, Tolland, Somerset
- Arable area: 182ha
- Cropping: Winter wheat, winter oats.
- Soil type: Red sandy loam
- Mainline tractors: New Holland T7315, T6160, TS110
- Combine: Massey Ferguson Delta combine with a 9m header
- Cultivation equipment: Simba SL500 cultivator; Lemken 3m smaragd cultivator; Overum 5f plough; Amazone 6m power harrow combination drill; Opico 12m grass harrow; 6m Einbock Chopstar hoe; 6m CTM Weedsurfer.