Changing agronomic practices and the need to improve soil structure are driving a new wave of tyre development across the industry. CPM finds out how one leading manufacturer is responding.
Tyre development can no longer exist in a vacuum if manufacturers are to genuinely contribute to solving the problems growers face.
By Rob Jones
Value, longevity and reliability may be the traditional areas on which tyres are judged, and remain key buying criteria for growers. But the main focal point for engineers and new product development teams is now in improving the functionality of tyres to make them as relevant to future farming solutions as possible.
This is the view from Mitas UK managing director Jon Ward, who claims the rate of development in tyre and traction solutions for agriculture is now outstripping that of practically any other sector.
“So much has changed in the past few years with regard to machine size, power and road speed that modern agricultural tyres are almost unrecognisable in construction and performance terms from those of just 25 years ago,” he says.
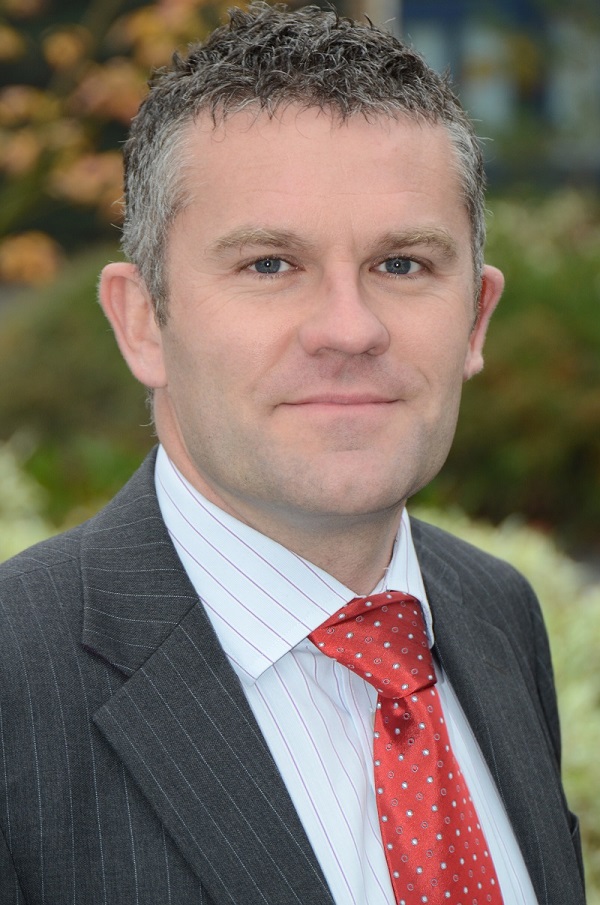
The challenge for Jon Ward is to build on the technology the tyre industry has developed to ensure more sustainable crop production in the future.
That may be just as well, because growers’ priorities are changing too, he continues. “Moving forward, the challenge is to build on the technology we’ve developed and look for ways this can contribute to more sustainable production in the future.”
Such areas could involve working with agronomists to understand how soil conditions affect blackgrass and nutrient utilisation or looking at modern rotations to find out how cultivation timings may be changing, he explains.
“There are a lot of reports how blackgrass favours wet conditions and this could well be made worse by deep compaction limiting the natural drainage.
“Equally, we’ve worked with soil specialists who tell us such soil structure creates poor conditions for fertiliser utilisation. Worse still, it can result in greater levels of greenhouse gases being released into the atmosphere.
“The simple truth is tyre development can no longer exist in a vacuum if manufacturers are to genuinely contribute to solving the problems growers face. Collaboration and integration of ideas is the way forward.”
Adam Hayward of Claas UK agrees – a large combine with a full grain tank can now tip the scales at 30t, he points out. But new generation harvesters will do much less damage to soil than those from 20 years ago. This is down to combining technical initiatives in tyre technology with modern harvester control systems, he believes.
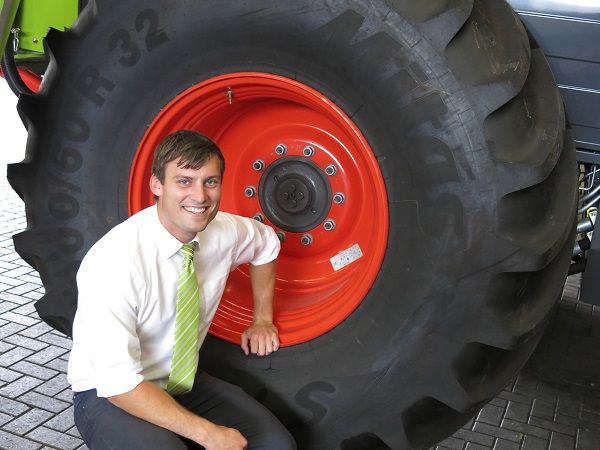
Despite a higher payload, new generation harvesters will do much less damage to soil than those from 20 years ago, reckons Adam Hayward.
“The significant increase in size of combines over the past 15 years has been a major development in terms of improving harvest efficiency, but it has put pressure on engineers and tyre manufacturers alike.”
Working with Claas, Mitas has now helped developed harvester-specific tyres designed specifically to keep combines rolling on days that would have previously been considered marginal.
According to Kirk Walker, technical manager for Mitas UK, the CHO (cyclical harvest operations) tyres resulting from the partnership give growers up to 20% more harvest days than a conventional tyre in a catchy year.
“The big advantage of these tyres is that they can be run at a much lower inflation pressure in the field than you would need normally.
“This is important because inflation pressure is directly related to ground pressure, so the lower it is the less compaction and damage you’ll cause in the field and that’s the real benefit of these tyres.”
For Adam Hayward, such intensive joint efforts promise even greater technical improvements for the future.
“We’re already seeing inflation pressures being safely reduced by between 0.6 and 1.1 bar which is around 35% less compared with tyres used just a few years ago, and that’s happened at the same time as the equipment has grown in size.
“Minimising soil damage is currently a great area of interest – the growing number of requests we get about whether our headers are compatible with controlled traffic systems is ample testament to this.” The interest goes further, he adds, with growers more aware of how reduced traction and road efficiency can affect fuel consumption and tyre wear
The concerns about increased equipment size damaging soils and the consequent losses in production are also fuelling the development of low flexion tyre technology for cultivation tractors, Kirk Walker points out.
“The fundamental difference with low flexion VF tyres is that the sidewalls can deform to a much larger degree than conventional tyres without causing structural damage to the carcase.
“This means you can reduce operating pressures significantly and achieve a much bigger footprint in the field to minimise soil damage and improve traction, but then you can use this set-up for roadwork without having to re-inflate.”
He reckons such technology is underutilised, however. “Very few growers actually adjust pressures between different jobs – I think most still set the best operating pressure for the road and then use this in the field without appreciating how much soil compaction this can cause and how much extra fuel it uses through reduced traction.
“The advantage with VF tyres is that it allows you to think the other way around and optimise the pressure for fieldwork knowing you can still use this on the road without problems.”
But some of the biggest developments in the future will come from thinking about tyres in a completely different way, believes Jon Ward.
Working with Fendt, Mitas has developed AirCell technology which is based on a rigid inner tyre that can be pressurised to 8bar. When some of this air is released it can inflate large agricultural tyres by +/- 1bar (from 0.8bar to 1.8bar) in less than 30 secs – more than ten times faster than current methods of inflation.
“The Mitas AirCell is located on the rim inside the tyre and occupies about 30% of the volume of the tyre.
“Tyres can be run at low pressure in the field with air from the AirCell being released on demand for rapid pressure increase in the agricultural tyre itself ahead of roadwork. It can then be lost quickly again via a specially developed valve.
“As the AirCell is constantly recharged, the inflation/deflation cycle can occur as often as the operator wishes.” Mitas AirCell will be available for the Fendt 900 Vario equipped with Mitas 710/75 R42 SFT starting next month, says Jon Ward.
But perhaps one of the most startling developments is the PneuTrac, a joint initiative from Mitas working with Gallileo Wheel. “We’ve talked about the concept of a tyre running on standard rims with the characteristics of a track for a couple of years but field testing has been so encouraging we’re now aiming for full commercial launch in the next couple of years.”
Initial testing has shown a 170% improvement in lateral stability for PneuTrac over a conventional tyre. “It can be run at roughly half the normal inflation pressure, giving it a footprint over 50% greater than a standard tyre of the same wheel size,” he reports.
Field testing has shown it’s possible to run PneuTrac at 0.5bar in the field, compared with 1bar on a standard tyre. There’s also an improvement in tractive force of 25% over a standard tyre and 15% more than a high flexion tyre.
“With PneuTrac, you choose the optimum pressure for field use safe in the knowledge that this will also be perfect for the road because of the design’s inherent rigidity. You have the added benefits of better handling and an improved ride and what’s more, it’ll run flat if you’re unlucky enough to need it.”
Softer tread from tyre switch
East Yorks grower Andrew Burrell reckons there’s a difference that’s immediately noticeable when you step up to VF tyre technology. He operates a 275hp New Holland T8030 as the main cultivation tractor at Boythorpe Farm near Driffield, and switched to Mitas VF600 70 R30s on the front and VF710 70 R42s on the back last year.
“You can see that there’s simply more tyre on the floor for a start. But the biggest difference is the reduced slippage when ploughing – there’s so much more grip than we had previously.
“Before we’d have to put more air in the tyres to do serious roadwork but we’ve completely done away with that now – even when using the tractor with a 16t grain trailer.”
Andrew admits he was previously aware of the potential damage the heavy equipment used on the farm was doing to the soil.
“I think it’s something you’re always aware of. We have around 400ha of arable land to prepare each year and use a Dowdeswell 6f reversible plough on all our second wheats and barley land plus a Cousins 3.8m cultivator on our first wheats.
“In previous years we’ve grown sugar beet, too, so you’re having to go in with big tackle at difficult times of the year and you can see the affect it has on the land. We’re definitely treading more gently on the land now while still using the same big kit.”