A brand-new cab leads the features of the JCB Series III Loadall. CPM finds out what’s different and takes the machine for a drive at its launch at the company’s headquarters in Staffs.
It’s focused firmly on the agricultural operator.
By Tom Allen-Stevens and Nick Fone
With all the glitz and glamour you’d expect from a major new introduction to the agricultural machinery market, JCB has launched its Series III Loadall, boasting increased lift performance, improved safety and driver comfort.
Most significant among the new features, though, is the all-new Command Plus cab, designed primarily with agricultural operators and owner-drivers in mind, says JCB. The Uttoxeter-based manufacturer has lavished £8M and 50,000 manhours over five years on developing the new range, with a staggering £6M spent on the cab alone.
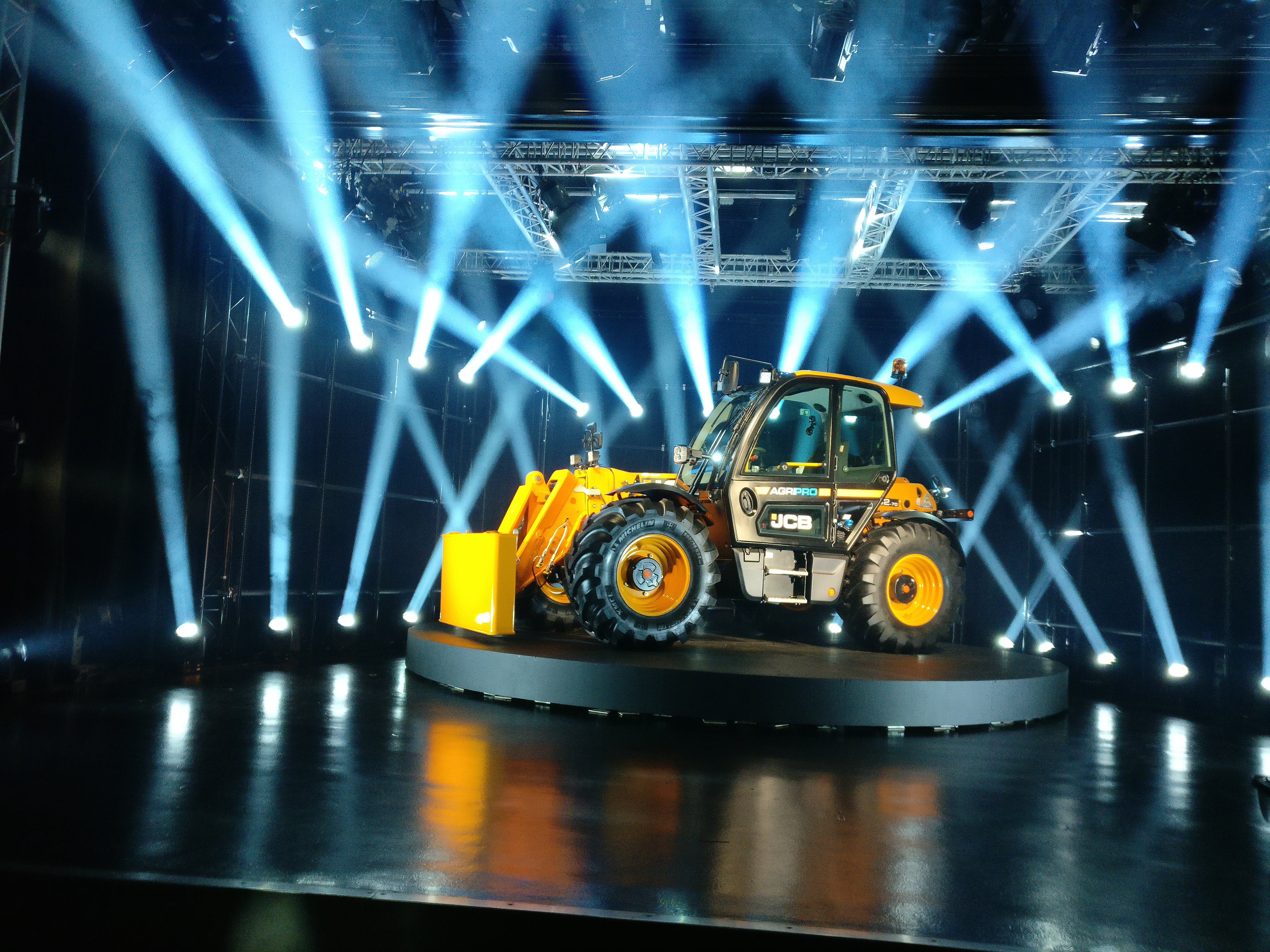
The Series III Loadall was launched with all the glitz and glamour you’d expect from a major new introduction.
The new Loadall may be a bid to reaffirm JCB’s leading position in the agricultural telehandler market. Introduced in 1977, it was the first telescopic materials handler seen on farms, and JCB’s first foray into the agricultural market. Since then, a third of the 240,000 machines that have rolled off the production line have found their way onto farms.
“Just over 40 years ago, the JCB Loadall telescopic handler introduced farmers to a revolution in mechanised materials handling,” says JCB chief innovation and growth officer Tim Burnhope.
“Through successive technical innovations in JCB engines, smart hydraulics and advanced transmissions, the Loadall has continued to deliver outstanding productivity, performance, durability and cost-efficiency.”
The Series III development represents the biggest R&D investment Loadall has enjoyed in its 42-year history. “It’s focused firmly on the agricultural operator, with the all-new Command Plus cab that’s quieter, wider and longer, with an improved driving position, controls that are easier to locate and use, and an instrument display that is larger and more informative,” continues Tim.
The new cab will be manufactured in a brand-new £50 million JCB Cab Systems factory being constructed near the company’s other manufacturing and assembly plants in Uttoxeter, Staffs.
Detailed engineering and ergonomics studies, and a programme of end-user consultation went into the new cab, says JCB, designed to meet the visibility, comfort, control and practical demands of discerning operators. The headline result is a cab that’s a full 50% quieter.
It’s 12% roomier, has a neater control layout and provides considerably more dedicated storage space. Visibility to the front wheels and beyond has been improved by the low-set dash panel and by 14% upwards to a raised bucket or fork by uninterrupted glazing that sweeps up and over the operator’s head. The aim has been to build on the Loadall telescopic handler’s all-round visibility – especially to the right side thanks to the low-set boom and compact engine cover – by focusing on the operator’s view forwards and upwards.
“A single-radius sheet of curved glass would have been the simplest solution,” notes Tim. “But this was rejected because it brought the windscreen too close to the driver’s face. So we opted for a more sophisticated solution – a multi-radius design that maintains a sense of spaciousness behind the wheel without distorting the view out, and provides a continuous field of vision from the low-set bottom edge of the glass to the top edge above the operator’s head.
“The Command Plus design brings a transformation in forwards and upwards visibility that we believe sets new standards for operator productivity, safety and driving ease – it’s a cab without compromise.”
So what else is new?
- An increased lift performance for all 6, 7 and 9.5m models in the telehandler line-up
- Optional Chassis Sway hydraulic levelling at the front axle for precision load placement
- In-cab and external pressure relief for attachment change-over
- Distinctive new colour scheme, ‘Loadall’ and ‘JCB’ branding but familiar overall appearance
There are four models in the new Series III range, with up to 200kg increased load capacity over their predecessors – the 6m lift 538-60, 7m 532-70 and 542-70, and the 9.5m high-lift 536-95. The heavy-lift, bulk handling 560-80 with 8m lift height and 6t lift capacity remain the same, and the 536-70 LP continues unchanged with its existing low profile cab for poultry shed and other low height applications.
There are Agri (including Agri Smart Power and Agri TorqueLock 4), Agri Plus, Agri Super and Agri Pro variants as before. These provide a choice of features and equipment levels, and options covering LED lighting packages, towing hitches and front-end implements from the JCB Agri range of attachments.
Power units are unchanged – the 4.4-litre and 4.8-litre JCB EcoMax engines serve up a choice of 55kW, 81kW, 93kW and 108kW (75hp, 109hp, 125hp and 145hp) outputs.
But there’s a new 40km/h TorqueLock 4 powershift transmission with four-speed torque converter lock-up for the 81kW (109hp) engine to provide more performance and better fuel economy when travelling and towing than the regular 30km/h four-speed transmission.
The six-speed JCB Torque Lock auto powershift and DualTech VT hydrostatic/powershift transmissions, which are both capable of 40km/h, continue unchanged.
So what’s changed from a driver’s point of view?
Swinging up into the new cab, the first thing you’ll notice is how much less cluttered it feels. There’s now a complete absence of rocker switches on the dash with virtually all machine functions handled by two of banks of rubberised buttons on the armrest. Backlit, the icons are logical and easy to fathom.
Just forward of these and off to one side from the joystick is a BMW-style twiddle-and-click dial that’s used to navigate through the new colour screen. While the introduction of computer controls on any machine will inevitably cause sighs and sharp intakes of breath (especially on a loader), JCB’s approach makes some sense.
By moving the plethora of dials, switches and buttons to the armrest and screen, it makes for a cleaner, less jumbled cockpit.
The main computer home screen shows engine rpm, speed, temperature, fuel and AdBlue levels just as you’d expect from a normal dash. But on top of that it gives you a read-out from an inclinometer to show how level the machine is. It also shows boom angle, which lights are on, what gear is selected, heater/AC settings and which steering mode you’re in. There’s no longer a rotary selector switch for 2WS, 4WS and crab, instead a shortcut button takes you straight to the right menu and the main dial is used to scroll between them.
Control-wise the heater and air-con panel is the only remaining switchgear left on the dash panel. (Set-and-forget climate control is now an option).
With good reason there’s been a fair bit of work put into the ventilation set-up. Being brutally honest the old arrangement was barely up to the job and the new system is a marked improvement.
It runs under positive pressure to keep dust and other undesirables out. Like any car-type set-up it’s now possible to switch between re-circulated and fresh air. Cleverly the diverter valve that does this job is linked to a door switch so that when the door is opened, it too opens. Then, when the door is shut it reverts to the re-circ position if required. This means that big downside of positively pressurised cabins – hard-to-slam doors – is avoided.
The ventilation ducting is sculpted around the steering column and along the side of the cab in a way that gives maximum blast to the glass. In combination with a more efficient heater matrix and 10% more airflow, it means defrost times have been cut by two thirds, according to JCB.
As a result of the re-arrangement in switchgear, it’s been possible to streamline the dash so that it now swoops lower than before, improving visibility down to the wheels and the attachment carriage when it’s in its lowest position.
Views skywards have been bettered too. By doing away with the cross-member that previously divided the front screen from the roof panel, there’s now an uninterrupted vista all the way through the lift arc, from right down low back to the highest point of the boom’s travel.
It’s all very well having acres of glass but it’s another thing keeping it clean. A twin-bladed wiper set-up clears the forward-facing glazing while a brace of opposed wipers sweep the roof leaving less than 10% of the glass unswept.
While this feeling of spaciousness is lovely, how does it benefit the bigger-boned operator?
Slight increases in width, height and length make for a 12% increase in volume, according to JCB, and access is improved thanks to a swing-up steering column borrowed from the firm’s loading shovels and Fastracs. On top of that, as an aid to hauling yourself into the throne, there are now more yellow-painted grab handles than your average tube train carriage.
Usually at a premium in telehandlers, there’s actually plenty of storage space on these latest Loadalls. Around behind the seat there’s a lift out bin for stilsons, string and the occasional springer spaniel. There are two cup-holders, a proper clamp-up phone holder and a pre-wired hands-free microphone that connects to mobiles via the Bluetooth stereo. There are twin USB ports and another pair of standard 12v sockets for charging.
Thanks to a whole raft of work done by the engineering team you might even be able to make yourself heard over the hands-free kit. By doing away with various holes in the cab structure and adding all sorts of sound-absorbing cladding both inside and outside, JCB claims to have reduced noise levels at the driver’s ear by 50%. That’s all good so long as you get out of the habit of driving around with the upper cab door latched open…