More automation is among tweaks manufacturers are rolling out across their combine harvesters. CPM rounds up developments set for next season.
This allows the operator to confidently push the combine closer to its performance limits.
By Martin Rickatson
Claas has extended its lines of Claas Tucano straw walker/hybrid combines to eight models, all with Mercedes-Benz Stage V engines and topped by a new 381hp 580 flagship. Adopted from the firm’s forage harvesters, Dynamic Power matches the engine power curve to the prevailing conditions, for example by reducing engine power when not chopping and boosting it when unloading. Full-load engine speed has been cut to 1900rpm, and idle speed to 850rpm.
Montana auto hillside-levelling compensates for side slope inclines of up to 16%, rising by 2% on the Tucano 560 and 430. Current tilt and cutting angle are displayed on the combines’ CEBIS terminal. Montana models are equipped with a two-speed manual transmission with automatic engine load adjustment and two drive ranges in each gear, automatically selected according to the load on the ground drive, with auto selection of the lower drive range when high traction is required.
Further new options include a new rear-wheel-drive axle said to provide up to 70% more tractive power, while a front axle diff lock remains optional. Hillside levelling is also available for the APS Hybrid Tucano 580, 570 and 560, as well as for the APS six-walker Tucano 450 and the APS five-walker Tucano 430.
New Tucano models also now feature the new touchscreen version of the Claas CEBIS terminal. While still also controllable via a control panel and armrest switches, it now allows, for example, drum speed adjustment by touching the relevant area on the screen graphic. The operator can also select specific machine control functions which can then be called up quickly when required via buttons on the CMotion multifunction controller.
Auto Crop Flow, the operator assistance system previously only available on Lexion combines, is now optional on Tucano models. This uses sensors to continuously monitor APS drum speed, residual grain separation, straw chopper speed and engine speed, and automatically alerts the operator to a potential blockage or overload. Claas claims this allows the operator to confidently push the combine closer to its performance limits under varied conditions, as well as aiding less experienced operators. Also carried across from Lexion models, Auto Slope continuously adjusts fan speed relative to combine angle, reducing it when working uphill and vice versa.
Meanwhile, Lexion 700 Hybrid and 600 walker combines are now available with a new 12in touchscreen version of the CEBIS Mobile terminal, which can be used to control the CEMOS Auto Cleaning, CEMOS Dialog, Auto Crop Flow and Cruise Pilot automatic operating functions. It can also be used to monitor the status of the 4-D cleaning system and to set-up and monitor results from the elevator grain quality camera.
The CEBIS Mobile screen also shows the status of Cruise Pilot, which automatically controls forward speed according to monitored parameters such as crop intake, throughput and engine load. The factor limiting combine performance under current conditions is displayed, and can then be altered using the touchscreen, which also allows selection of the required operating mode, from constant speed, constant throughput and constant throughput with minimal losses.
CEMOS Automatic, optional on all Lexion 700 and 600 models, is now said to be specified on over a quarter of all Lexion 700 combines sold in the UK and Ireland. It combines three modules: CEMOS Auto Cleaning fan and sieve adjustment, the new CEMOS Auto Threshing drum and concave adjustment introduced at Agritechnica, and CEMOS Auto Separation rotor speed and cover plate adjustment. Each can be specified separately or in combination to provide complete threshing/cleaning automation.
Those not requiring full automation can specify CEMOS Dialog, which, by monitoring and analysing settings and throughput, provides guidance steps to help improve combine performance. These can then be implemented by tapping the screen, or the operator can interrogate CEMOS Dialog on ways to improve specific aspects, such as grain quality, and then accept or reject the system’s suggestions.
Operators of new or existing combines without CEMOS Automatic or Dialog can now use a free-to-download CEMOS Advisor iOS/Android app for hints and suggestions to gain some of the same benefits. These can be saved in the app for future use. The app can also be used for grain loss estimation.
Case IH
For 2018-19, Case IH replaces the larger of its two Axial-Flow ranges, the 240 series, with new 250 models. Key upgrade is AFS Harvest Command, a three-level automation package said to help maximise performance by using multiple sensors for continuous monitoring and adjusting seven different settings from the data gathered.
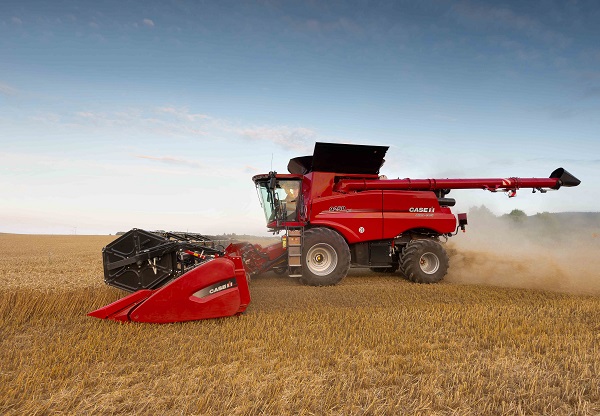
Key upgrade for Case IH Axial-Flow 250 series, which replaces the 240 range, is AFS Harvest Command, a three-level automation package.
Basic Harvest Command features Case IH’s existing Automatic Crop Settings (ACS) system, which adjusts operating items such as fan speed and concave clearance according to crop type selected. The operator is able to adjust desired outcome on the go, and save the settings for future use.
Next comes Harvest Command with Feedrate Control, which adjusts ground speed based on crop load to meet a desired outcome – performance to control losses, maximum throughput, or fixed throughput. The operator sets target maximum engine load and ground speed, and Feedrate Control operates up to those limits. The new system is said to more accurately control ground speed based on crop and ground drive load.
Full Harvest Command automation automatically makes threshing and cleaning system adjustments based on the same desired outcomes as Feedrate Control, but adds grain quality monitoring. This uses patented multi-spectral camera-based technology and sieve pressure sensing to provide further guidance to the machine’s automatic adjustment process by identifying broken grains via their exposed starch.
After setting chosen maximum target engine load and maximum ground speed, with full Harvest Command the combine can then be run in performance mode, operating at a speed to ensure an acceptable grain loss level from the rotor and cleaning system, or fixed throughput mode, where it maintains a target throughput by varying forward speed and adjusting settings to minimise losses. There are two further alternatives: maximum throughput mode, where it operates up to the speed or power limit set by the operator while adjusting settings to minimise rotor and cleaning system losses. There’s also grain quality mode, where it adjusts settings to maintain a targeted grain quality and impurity level at a set loss level.
Rotor vanes can now be either operator-actuated from the cab or set for automatic adjustment when AFS Harvest Command automation is engaged. The rear six vanes are linked and now include a greater range of adjustment. Meanwhile, new in-cab pre-sieve adjustment allows AFS Harvest Command automation or manual activation to automatically adjust all sieve settings according to loss sensor, grain camera and sieve pressure-sensor feedback. Pressure sensors provide sieve loading data to allow the system to gauge impending losses and make adjustments in advance, altering fan and sieve settings accordingly. They can also work together with an Auto Fan option to maintain an ideal fan setting and sieve pressure, says Case IH.
Drive-wise, a new two-range, shift-on-the-move hydrostatic transmission offers 18km/h and 40km/h maximum field/road speeds, although these maximums can be set lower according to preference. Differential lock engagement is now via a floor-mounted electrical button rather than a mechanical pedal, and braking moves from an external disc to internal oil-cooled brake, for reduced pedal pressure requirement and enhanced cooling.
Case IH has also added a number of options for the header/elevator end of the 250 series, including a new 6.1t lift capacity elevator alternative for large headers, a dual lateral tilt option, and an in-cab-controlled face plate fore-aft angle feature. Header height control function upgrades are said to improve responsiveness and flotation, and there are adjustable return-to-cut and resume lower rates. Header height sensitivity is automatically adjusted as forward speeds vary.
John Deere
John Deere says the new track system introduced for its 2019 model year combines provides a footprint that, when compared with the average of other systems on the market, offers 30% more contact area. Track design has been altered so significantly more is in contact with the ground, meaning that the 609mm (24in) track option for the S700 rotary and T-series walker combines has the same footprint as 762mm (30in) versions from other makers, claims Deere. There are 609mm and 762mm track options for the T-series five- and six-walker combines, plus an additional 914mm (36in) option for the S700 rotary machines. On five- and six-walker and rotary machines, transport width remains below 3.5m when 609mm tracks are specified, with that figure down at 3.29m for five-walker T combines.
With a 40km/h top speed on all models, John Deere claims ride comfort has been improved by an undercarriage incorporating five pivot points. The new tracks feature four rather than three steel cord layers, and the track profile has deeper lugs angled at 55°. The tracks can be replaced by wheels if required for field work or to enable easier resale of the combine, says Deere.
S700 rotary models now benefit from a new Interactive Combine Adjustment (ICA2) system said to make it easier for operators to consistently achieve maximum performance. After optimising machine settings such as grain quality, losses and sample cleanliness, ICA2 maintains the pre-selected levels as harvesting conditions change. A new, free, MyOperationsCentre app enables owners and managers to view and change combine settings remotely from a mobile phone, tablet or PC. The operator can then confirm the adjustments on the in-cab display.
Also new for S700 rotary combines is the 700FD flex draper header, claimed to improve combine performance by enhancing feeding ease. New seals are said to reduce OSR losses by up to 45%, and corrugated edges on both sides of the belt improve alignment and guidance. The optional top auger above the belt has an increased diameter of 45cm and the central feed drum now offers a second upper position for improved crop flow in OSR. The flexible knife can move up or down by 19cm across the full width of the cutterbar, to cut as close as 38mm to the ground. Up to four header height sensors aid ground contour following.
John Deere’s W- and T-Series walker machines now benefit from quick-change concaves. The firm suggests it takes only 15 mins to swap the universal concave suiting damp conditions for the small grain concave suited to drier situations, with a claimed potential output increase of up to 12% from, for example, changing to the small grain concave in tough conditions to enable more aggressive threshing.
All T-Series models are now equipped with a new separator grate, featuring new patented steel separation segments in place of the previous rear cast iron fingers. The distance between the rear beater drum and the grate below has been reduced, allowing greater separation aggression. Meanwhile, also new is a 360° LED light option, plus a central oil drain bank for cleaner and easier removal.
New Holland
New Holland’s CR Revelation combine models for 2019 feature its new IntelliSense automatic proactive setting system, claimed to help increase daily output, reduce grain loss and improve grain quality. By reducing the number of decisions the operator is required to take in targeting a certain outcome, it’s said to also enhance driver comfort and confidence.
IntelliSense allows the driver to choose from four strategies: limited losses, best grain quality, maximum capacity or fixed throughput. Based on data from the machine’s patented cleaning shoe sensors, the combine then continuously adapts the speed and vane angle of its two rotors, plus fan speed and the openings of the pre-sieve and upper and lower sieves, to automatically deliver the desired result. Automatic rotor vane adjustment is reckoned to improve the rotors’ power efficiency without impacting the threshing and separation settings, resulting in greater fuel savings and performance.
IntelliCruise, which automatically matches forward speed to crop load, now features automated ground speed functions and offers a choice of three harvesting strategies. Selecting ‘maximum capacity’ increases forward speed to reach maximum engine load, while ‘fixed throughput’ varies ground speed to maintain a pre-set load. Selecting ‘limited loss’ varies ground speed to maintain incoming crop flow, but if losses become excessive, throughput is reduced to address this. Three settings are available to adjust the IntelliCruise system’s boundaries and sensitivity: maximum engine load, maximum forward speed and feedrate sensitivity.
Further CR Revelation upgrades for 2019 include a new on-the-move two-range transmission, a bigger hydrostatic pump and integrated wet brakes. The two speed ranges comprise a 0-17km/h band for field work and a zero to maximum bracket for road travel. The transmission and hydrostatic pump are said to result in enhanced tractive effort, improved hill climbing and faster response. There is also a new footswitch-operated electrohydraulic diff-lock.
Meanwhile, New Holland has extended the CR Revelation range with a new CR7.80 entry-level model. Rated/maximum power outputs are 374/415hp from an FPT Cursor 9 Stage V engine, while further spec numbers include a 750-litre fuel tank, 9500-litre grain tank and 126 l/sec unloading rate. The existing CR7.90 now gets the same engine, gaining 11hp additional power for a 460hp maximum.
Deutz Fahr
Deutz-Fahr last year renewed key components its largest five- and six-walker models, with developments said to be aimed at boosting comfort and productivity. The C9300 series comes in two model sizes, with the C9305 and the C9306 using the same Stage IV Mercedes-Benz engines, but producing 340hp in the former and tweaked to turn out 395hp in the latter. New features include a redesigned cabin interior and controls, while within lies Deutz-Fahr’s established three-drum Maxicrop separator system. After this comes an increased separation surface thanks to longer straw-walkers, measuring 7.46m² on the C9305 and 8.90m² on the C9306.