Celebrating 25 years since it first set up, supplying machines to UK potato growers, Grimme UK now dominates the British root-crop harvesting market. CPM tracks some of the product developments that helped achieve this.
There’s always been an innovation infrastructure at Grimme UK that’s encouraged new ideas to come forward.
By Tom Allen-Stevens
When Grimme UK first started trading 25 years ago, there was little doubt it was going to be a successful business. But sealing that success and allowing the business to grow and dominate the root-harvesting sector in the UK have involved a series of innovations specifically tailored to the UK market.
“Grimme is a company with a 156-year history, and Grimme UK was the first daughter company set up by the German parent,” explains the company’s marketing manager Adam Johnson. “The root-harvesting market potential was huge and everyone recognised that the UK was an important player in the potato sector.”
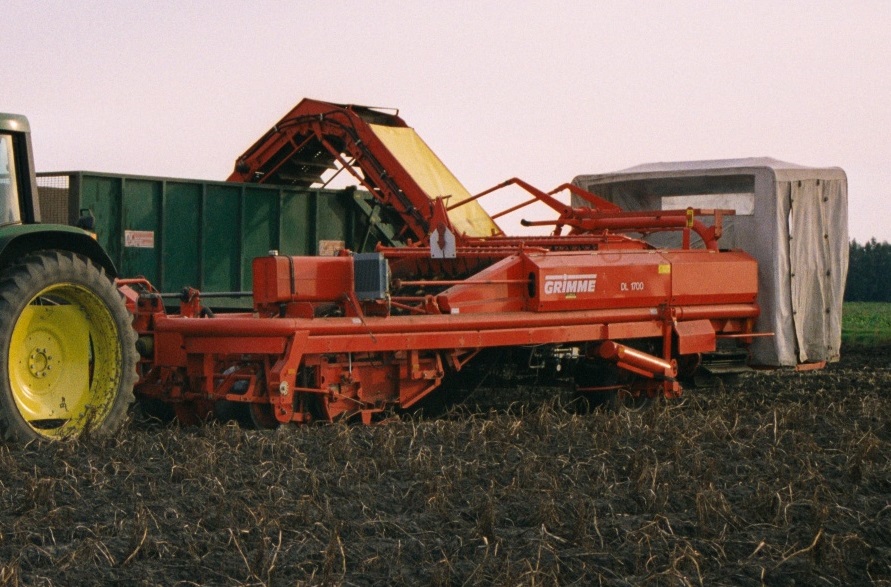
Key for the UK market was a trailed machine with a straight-through separation system.
Grimme kit was already well established, with over 50% of the UK potato crop at the time passing through the red-liveried machines. These were imported by Pearson, but the company was given notice in 1993 and seven staff members started the new operation from premises opened in Sleaford, Lincs, in Nov that year.
“We started with a clean sheet and built up a new dealer network throughout the UK,” recalls Barry Burrell, one of the seven. “A few of the dealers who’d been selling Grimme machinery joined us but most were new companies.”
The range of machines included the new Combistar destoner, that was launched at the 1993 Smithfield Show90. But it was Grimme’s potato harvesters that really defined what it offered to UK growers.
The leading model at the time was the Exel, that was renamed in 1994 as the Variant DL 1700. Most machines were fitted with the roller separation (RS) system, that became increasing popular during the 1990s, although other options and variations were available. UK growers were moving away from the web and pintle belts deemed too aggressive for the crop.
But it was other features that found favour with farmers, says Barry. “The new Variant machine was 1700mm wide, offering more sieving area than most of the competition, that was at 1500mm. It handled the wider row widths with better flow of the digging shares onto the main and second webs.
“Also at this time, Grimme introduced the hydraulic wheel-drive system, which revolutionised the traction of the harvesters in wet conditions – it was like four-wheel drive for your potato crop. It wasn’t long before the option was copied by other potato-harvester manufacturers.”
Key for the UK market was that this was the first trailed machine with a straight-through separation system. “There were fewer direction changes, which meant higher throughput with less damage to the crop,” says Barry. This focus on reducing damage was becoming a defining feature for UK harvesters that brought in more pre-pack crop than their continental counterparts.
In 1998, Grimme UK moved to its new purpose-built premises at Swineshead, with fully equipped workshop, parts store and showroom. “This was the point Grimme put its stake in the UK industry and decided it was here to stay – we’d cemented ourselves in the market place as an industry leader,” says Barry.
And innovation continued to drive product development with a CANBUS system introduced on harvesters in the same year – this did away with many of the levers and switches needed to make on-the-move changes, replaced by a digital control box and one wire connecting this to the harvester.
“There’s always been an innovation infrastructure at Grimme UK that’s encouraged new ideas to come forward – it’s part of the job to be trying new things in the field and discussing with customers how to make the harvesting job better,” he notes.
And it’s this that led to the introduction of the Multi-Sep. “It was late autumn 1999 when the separation system was modified to see if a rubber spiral segment roller was better at extraction of wet soil than the standard multi-bladed yellow star,” says Barry.
The first ever trial in the field was reputedly a star roller modified with a rubber mat wrapped around it. This allowed enough agitation to pull out the haulm and plenty of soil and clods, but the air pockets beneath the rubber ensured it was gentle on the crop. Grimme engineers designed the new rollers for testing.
“It was Barry White who exchanged two rows of stars for the new spiral rollers,” recalls Barry Burrell. “The first test was in the workshop and we used a wheelbarrow with wet soil off the wash pit, put through the machine. The difference between the standard stars and the new spirals was amazing in terms of how they removed the soil.
“The following day Barry White and myself took two spiral shafts to a customer’s harvester in N Yorks who carried out more test work. Because off the vast difference in the amount of soil which the new rollers were taking out, the decision was made to fit the new spiral system into all new GZ Multi-Sep machines as standard for the following year.”
In 2005, in-field testing put a new machine through its paces that was set to replace the GZ. “The new Grimme GT170M and GT170S machines were launched onto the UK market in 2006,” continues Barry.
“The M version consists of a main web leading onto a second web, then a single Multi-Sep separation system, or the second main web can be replaced with a second Multi-Sep. This gives the machine a tremendous advantage over other manufacturers’ as it offers double separation. The GTS machines are fitted with a short intake web leading onto the shorter main web, making it into a higher output harvester for the larger grower.”
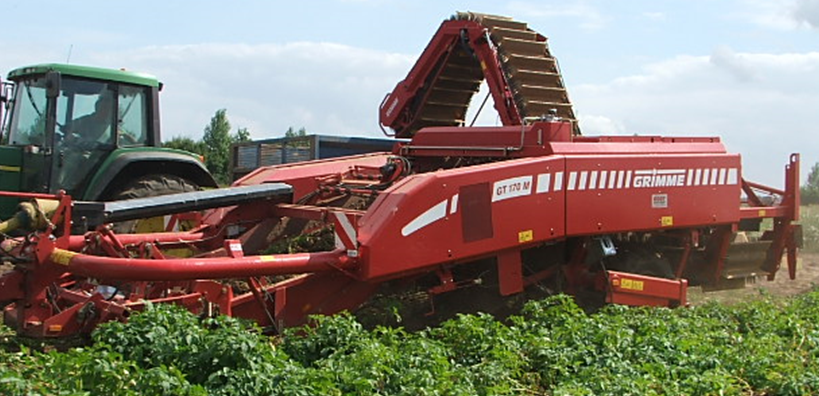
The GT Multi-Sep continues to be the UK number one trailed potato harvester, with around 85% of the market.
Sales took off and have continued strong ever since, with 90% of machines fitted with the double Multi-Sep separator. The GT Multi-Sep continues to be the UK number one trailed potato harvester, with around 85% of the market.
Earning Grimme a DLG silver medal at Agritechnica in 2005 and launched with the GT machines was Terra-Control. This system uses special hydraulic cylinders, guided by the diablo as it runs over the ridge, to set the depth of the share. “The hydraulic cylinders register every deviation of the ridge crest height and automatically adjust the height of the two swing frames,” explains Barry. “It means the digging depth and diablo pressure remain constant at all times and with every contour.”
Such innovations have also been included across Grimme’s range of self-propelled potato harvesters. The all-new SF 170 GT was introduced in early 2007, that were rebadged as Varitron. “These are available unmanned or manned, such as the Varitron 200 with no bunker, the Varitron 220 with 2t buffer bunker and the Varitron 270 with a 7t bunker.”
The new Platinum range brings in much of the technology, such as ErgoDrive, from Grimme’s sugar beet harvesters (see panel on pxx), topping out with the Varitron 470 Platinum, on Terra Tracs with a 7t bunker. “Fitted with Terra-Control and also Delta control, that allows you to adjust one side individually, it makes light work of lifting four rows. With the twin separation system, you also get a clean sample into the trailers,” says Barry.
Now, with a staff just short of 100 and new purpose-built training facilities recently added to its headquarters at Swineshead, the emphasis on innovation is as strong as ever, notes Adam.
The CleanLoader is a recent example. “During harvest between 3-20% of the crop in the trailer is trash, depending on the conditions. This means an increase in transport costs followed by an intense separation and disposal back at the farm yard.”
In very harsh conditions up to 100t of trash could be produced from a 10 ha field.“The CleanLoader allows you to clean the crop in the field, cutting down on transport and separation costs.”
Coming through are some “major leaps” in spring equipment technology. “These address the issues of reduced chemical use and greater care for the soil, as well as increased use of cover crops. We’re also developing machines with reduced labour costs, particularly in the field veg sector – with Brexit in mind, our customers are telling us this is a priority.”
This technology is also being developed with export opportunities from the Grimme factory in mind. “We’ve received a lot of interest from the US, where the industry faces the same pressure with labour shortage. We’ve come a long way from where we started 25 years ago as a daughter company focused on the UK market to be leading research in new harvesting technology for worldwide opportunities,” notes Adam.
Kit tailored to ensure the best start
Alongside the harvesting technology, the Grimme UK team has helped develop soil separation and bed-forming machines to suit the UK grower, as well as planting technology.
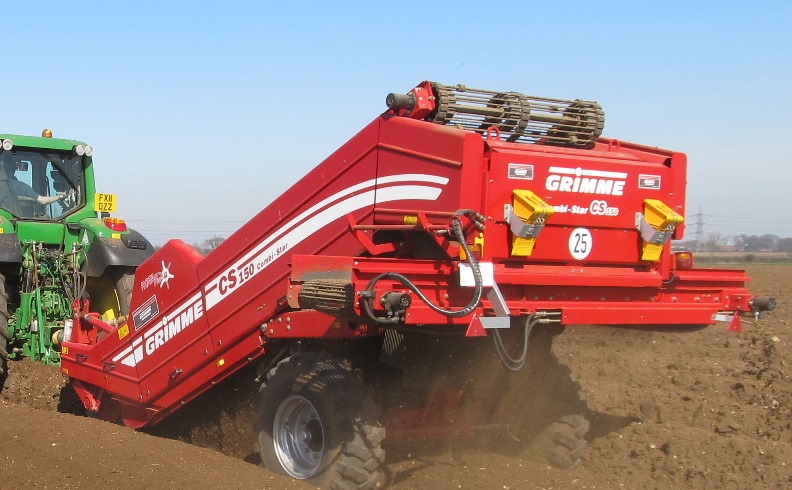
The Grimme Combistar destoner
Launched at the 1993 Smithfield Show, the new Grimme Combistar destoner was one of the first machines traded by Grimme UK. “The innovation here is the star roller,” says Barry.
“The machine is fitted with seven rows of adjustable stars that roll the soil to separate it, giving it far more sieving than on a conventional web destoner. It also has height adjustment the operator can make on the move. Spacers are fitted between each row, depending on soil type, so in heavy cloddy conditions this can be three to give extra separation.”
1997 saw the introduction of the new Grimme Combi-web separator, which consists of two webs, with the first having a cascade point to form a drop onto the main web. The following year, they were built as a three-web machine.
In 1999, a prototype three-bed stone and clod separator came for trial work in the UK. Designed for larger growers, it was lugged along by a 300hp Caterpillar Challenger tractor.
But only two commercial units were ever sold, notes Adam. “We always listen to our customers and look to develop machines that will suit their needs. Sometimes it doesn’t work out, but it’s worth having nine ideas that aren’t so good if the tenth one flies.”
The Shapeforma was another development introduced in this year. “Growers were looking to form deeper beds, up to 50cm,” notes Barry. “Mouldboards can achieve this in heavier soils, but the Shapeforma can pretty much shape any deep light soil into a sandcastle. It then holds its shape much better.”
In 2010, planter technology moved on with the introduction of Grimme’s GL42K belt planter. “Grimme built the GL42K as an alternative to the cup-feed machine which we’d been selling since 1994 with the VL20 planter,” he recalls.
“Seed size in the UK can be very variable, and small tubers can be very difficult to plant with any accuracy on cup-feed machines. But belt-feed planters will cope with any size of seed together in the same sample.”
The GB215 planter saw the introduction of a new chassis. “This has a longer hood which shapes the bed better – it was nicknamed the Kit Kat hood as a result. Another key feature of the Grimme belt planters is that they’re pivoted at the front, ensuring a constant drop height.”
2012 saw the introduction off the new GB330 three-row belt-feed planter. “UK growers had been looking for a new three-row planter for several years. It keeps many of the features from the GB215, but rather than fully mounted, this is built as a trailed planter.”
The three-row format suits salad and seed potato growers in particular. “Also, many growers on three rows also plant in two rows – with this planter a kit can be supplied to go from three to two rows, making it a very versatile machine.”
Technology sweetens the task for sugar beet growers
In Sept 2003, Grimme UK formed a new company, Root Systems to sell Grimme’s recently introduced sugar beet harvesting technology. Barry Burrell headed up the new team.
“Grimme was established in potato harvesting, but we really had to prove our value to sugar beet growers,” he says.
Again, a focus on innovations is how the company began to take market share. The Maxtron introduced tracks to harvesters that had usually run on tyres. Among other key features are the Oppel wheels which lift the beet more gently than walking shares with less soil intake, says Barry.
At over 15m long, the newer Rexor is a commanding presence in the field, although a steering and wheel configuration allow remarkable manoeuvrability. The roller table came across from Grimme’s potato technology, and this, plus just three turbines, ensure a gentler cleaning process as well as high throughput, he adds.
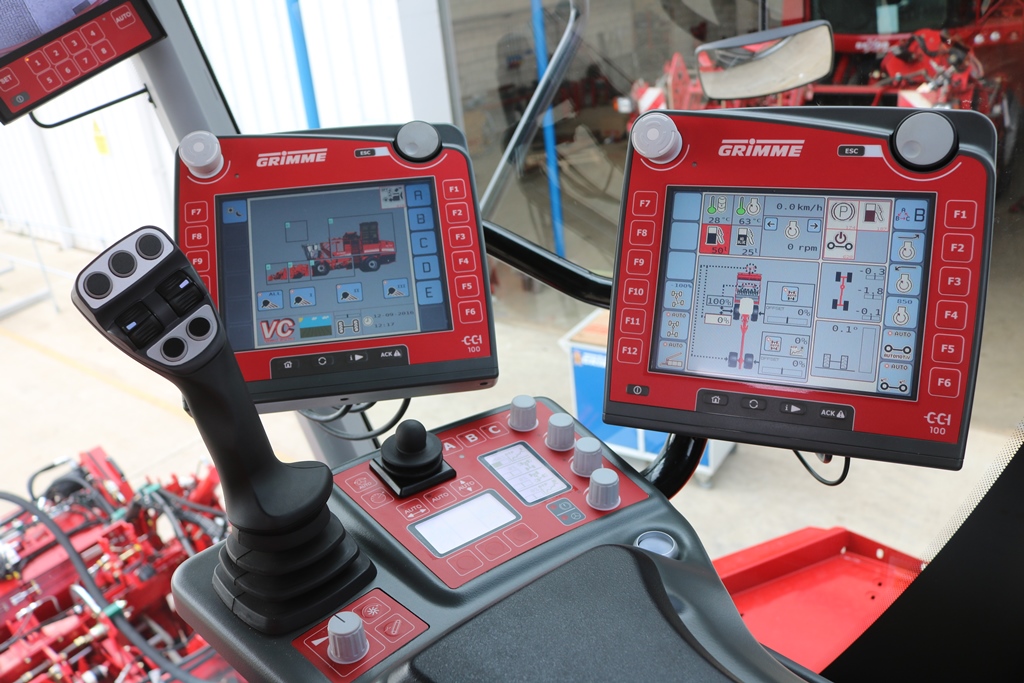
ErgoDrive brings all the functions of the machines to the joystick and terminals.
“Advances in the in-cab technology have really accelerated on the sugar beet side. ErgoDrive brings all the functions of the machines to the joystick and terminals.” Buttons to control ram functions, such as share height, and dials to adjust speed of the turbines, for example, are all programmable. Two terminals put a host of settings and readings for drive and harvest control into a standard format, while Visual Protect zeroes in a problem using up to eight on-board video cameras.
“ErgoDrive has proven so popular on sugar beet harvesters, we’ve now introduced it on the Varitron self-propelled potato harvesters,” notes Barry.
Innovation Insight
CPM would like to thank Grimme UK for kindly sponsoring this article, and for providing privileged access to staff and material used to help put the article together.