Speed, weight and its distribution, tyre design and inflation pressure all have an influence on how efficiently tractor power is converted into usable work. CPM reports.
Slapping on too much ballast is among the most common errors.
By Peter Hill
There’s something magical about getting advanced tractor tyres to perform at their best.
As the slip percentage drops to the 10-15% optimum with the implement cultivating the soil as its designer intended and fuel consumption wanes towards optimum cost-efficiency, the operator can feel comfortable that the tractor’s maxing its capabilities while there’s also best care for the soil.
Achieving that nirvana takes a bit of planning, a bit of equipment preparation and at least a basic understanding of how advanced traction tyres work and what influences their performance.
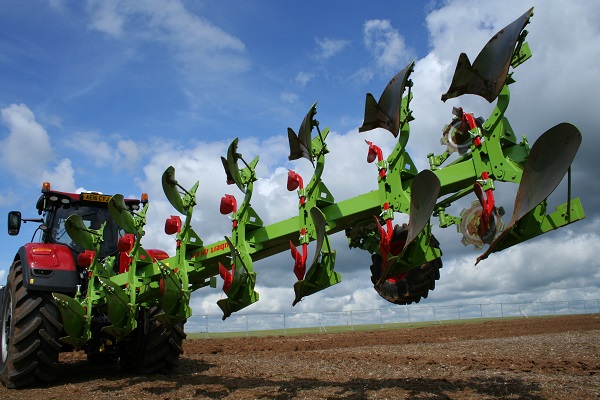
Calculating the most appropriate tyre pressures must take account of each tyre’s load-carrying capability at different speeds and with the load on the tyre measured in the worst case scenario – with implement raised, in the case of rear-mounted equipment.
The basics are these – it’s not so much the tyres as the air inside them that supports the weight of the tractor and that of any implement it carries, so there must be sufficient air within the tyre to support a given load in line with the manufacturer’s specifications.
But too much air stiffens the tyre carcase unnecessarily, reduces the contact patch area and generally makes the tyre less able to transmit power and torque.
With speed comes heat, generated by friction between the many and various components that form the finished tyre.
And while plenty of heat is needed in the tyre manufacturing process to fuse those components together, too much heat too frequently – when running under-inflated tyres for extended periods on the road, for example – can soon have them coming apart again!
Getting the balance right for different applications using different implements, and exploiting the extraordinary advances in traction tyre capabilities made over recent years brings the rewards of optimum performance in terms of productivity, cost-efficient fuel use and minimised impact of weight and wheel slip on soils.
This is the broad message that Stephen Mills, Fendt brand manager at Lincs machinery dealership Peacock and Binnington, aims to get across to participants in his driver clinics.
Slight variations in tyre inflation pressures can make a significant difference to the resulting contact patch of very supple tyres such as the new IF and VF designated designs, he points out, so it has to be worth making adjustments when tractors change from one task to another for a length of time.
“Over-inflation limits sidewall flexibility so you get a smaller footprint, resulting in less grip and greater soil compaction,” he explains. “Increased levels of tyre wear result from the lower traction, and you use more fuel because of the lower work rate.
“As a general rule of thumb, 20% over-inflation can result in a 30% loss of performance, and with the low inflation pressures we use today, 20% can be as little as 0.16 bar or 2.4psi.”
For starters, then, best get a good quality pressure gauge.
And then consider tractor weight management before tackling the tyres, Stephen advises, because getting overall weight and weight distribution right is just as valuable as managing tyre inflation pressures.
“Slapping on too much ballast, especially for higher speed operations that don’t really need it, is among the most common errors,” he points out.
Carrying insufficient weight and distributing ballast incorrectly also rank high in his list of wayward practices.
“All these scenarios result in fuel being wasted because the tractor is not being operated to its potential,” Stephen emphasises. “Soil damage through smearing or compaction are additional penalties.”
While the type of implement involved – whether it’s mounted, semi-mounted or trailed – clearly has an impact on the amount and distribution of weight carried by the tractor in addition to its own mass, the effect of working speed is less well appreciated.
“It’s true that power and weight go hand in hand – you generally need more weight to transmit more power as far as traction with draft implements is concerned,” says Stephen.
“But it’s also the case that greater speed mitigates the need for weight, so higher speed operations need less weight to achieve the same levels of traction.”
There’s a formula for calculating the impact of this effect and rule of thumb figures for tractor operating weight: multiply the tractor’s pto power in kilowatts by 650, then divide the result by the working speed in km/h.
Take a 240hp Fendt 724 Vario as an example; it delivers 158kW at the pto and has an unladen weight with a full tank of diesel of 8000kg.
When working at 6.5km/h, the formula above produces a target weight of 15,800kg and therefore a need for 7800kg of ballast to achieve optimum heavy draft traction.
When the working speed increases to 9.5km/h, the total operating weight drops to 10,810kg and the ballast requirement to 2810kg.
Working faster still – operating a compact disc cultivator on stubbles at 13km/h, for example, and the calculated figure falls to less than the tractor weighs, so any ballast is superfluous.
Having determined the appropriate weight of the tractor, the contribution of the implement to the load the tyres must support needs to be worked out.
The ideal method is to commit some time to hitching on the relevant equipment and running the outfit over a weighbridge – although some tyre manufacturers offer a service using portable weigh cells to gather this data.
The key thing here is to weigh each axle in the ‘worst case’ configuration; so that means with the implement up in the air in the case of rear-mounted equipment in order to measure the maximum weight the rear tyres will have to bear.
Conversely, placing the implement on the ground loads the front tyres to the most they will experience; and in both cases, remember to divide the results by two to get the weight per tyre before thumbing through the tyre manufacturer’s data table.
Exploring the columns for the tyre and size concerned, as well as the target operating speed, will reveal the recommended inflation pressure, which should be tweaked upwards a touch to counter the added loading and sidewall stress that comes from working across hilly ground.
No weighbridge or friendly tyre adviser to hand? Then resort to rule-of-thumb methods for a quick fix before the job can be done properly.
These include measuring the static laden radius, which is from hard surface to the top of the loaded tyre, and adjusting the inflation pressure until that measurement matches the figure in the tyre manufacturer’s data chart.
Alternatively, adjusting inflation pressure until a loaded tyre has three or four lugs in firm contact with a hard, smooth surface will also yield a broad-brush result.