Putting telescopic handler power to the ground has long been the preserve of two transmission types – gear-based powershift or oil-driven hydrostatic. JCB claims its DualTech VT system combines the best of both. CPM visits an early user.
Our operators work some very long hours from late spring through to late summer, and more than anything it has really improved their working conditions
By Martin Rickatson
Telehandler users tend to fall into two camps – those who prefer powershift transmissions for their tractive efficiency and low-noise travel at high speeds, and those who favour hydrostatic drive, with its low-speed controllability and smoothness of power transfer.
Combining the merits of the two has long challenged telehandler design engineers, but two years ago, at the launch of its DualTech VT transmission, JCB claimed it had done just that.
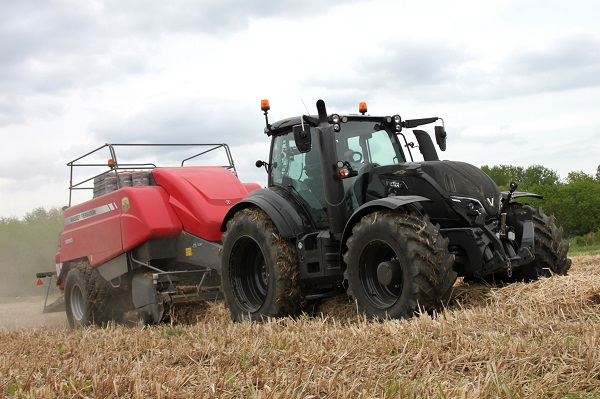
Agribale’s 12 big square balers package around 45,000 tonnes of material each year, ranging from straw to miscanthus.
Development of the new drive system began in 2010, under a team combining members of JCB’s Loadall and Transmissions businesses. The result of their work combines hydrostatic and powershift drive systems using established components in a single housing, and in 2016 the first Loadall models with DualTech VT became commercially available.
The transmission can now be specified on the firm’s top-spec 531-70, 535-95 536-60, 536-70, 541-70 and 560-80 Agri Pro Loadall handlers. In capacity and capability terms, the second and third numbers relate to the number of tonnes the machine can lift, and the fourth and fifth digits refer to maximum lift height in metres, a decimal point insertion being required in each case.
Providing infinitely variable working speeds up to 19km/h – a reduced maximum speed can be set – the hydrostatic drive module works in first gear for low-speed operation and controllability, being more quickly responsive and offering finer speed adjustment than is possible with a powershift. This, claims JCB, limits noise, makes for smooth power transfer, heightens response and maximises power efficiency. Precision inching from a standstill is possible using the brake pedal. In Flexi mode an electronic hand throttle can be used to select pre-set engine speeds or adjust them from 1500rpm in 100rpm increments, while engine speed can be set to optimise boom hydraulic performance, leaving the operator to focus on controlling steering and boom operation.
Beyond 19km/h, when auto-disengagement of 4wd also takes place, power transfer is automatically taken up by the powershift element of the transmission. Electronically modulated clutch packs auto-shift between gears two, three and four up to a top speed of 40km/h, while it’s possible to restrict auto-shifting within certain gear numbers if on field work and maximum speed isn’t desired.
With no torque converter required, direct drive in each gear maximises use of available torque for rapid acceleration, climbing ability and maintenance of speed on inclines, claims JCB. Automatic skip-shifting also takes place down to the lowest ratio after the machine has been slowed – for example, at a road junction – so it can then pull away again smoothly.
Power and Economy settings allow the handler to be operated as appropriate, with the latter restricting maximum engine speed to 1700rpm in working gears. This alters the engine’s power delivery characteristics and up-shifting earlier, to minimise fuel usage. JCB makes a claim for fuel consumption reductions of over 5% when using the Economy setting across an average agricultural telehandler duty cycle.
Flexi mode also builds on the Vari-Speed feature established on JCB’s fully-hydrostatic 525-60 compact Loadall, allowing engine speed to be set to deliver the required amount of oil from the 105-litre/min high-flow auxiliary hydraulics circuit and a low ground speed to be dialled in to operate a hydraulically driven attachment, such as a yard sweeper, at the required rate.
The machines also use JCB’s 140 l/min flow-on-demand piston pump hydraulics system, which features a regenerative circuit for the boom lower and retract cylinders, claimed to be unique. This allows the boom to lower significantly faster than usual but still under full control, says the firm. Side-by-side comparisons show an improvement in loading cycle times of up to 20%, or a 15% reduction in the amount of fuel consumed to move the same amount of material. There’s also a new high flow auxiliary hydraulics circuit that provides up to 110 l/min flow for attachments with hydraulic motors.
One of the first UK customers for a DualTech VT-equipped Loadall was Peterborough-based AgriBale, a specialist straw-baling contract business. Much of the business’ work is for the supply of power station fuel where AgriBale runs a fleet of 12 big square balers.
“We’re now running 12 Massey Ferguson/Hesston, consisting of ten 120cm x 130cm machines and two 120cm x 90cm models,” explains managing director Doug Price.
“We’ve been using JCBs for our handling needs for some time, for building stacks and loading lorries, and last year when looking for a couple of replacement machines we tried a demonstration model of the Loadall 535-95 Agri Pro with the DualTech VT transmission.
“Currently we run a pair of machines through the winter for moving straw and loading trucks, with a further handler hired in for our busier period. That begins long before the cereal harvest, as we also cut and bale a large amount of miscanthus each year. But the bulk of what we do is straw in the peak season.”
With the miscanthus – or elephant grass – being a perennial crop, harvested in the late spring to early summer period, pressure isn’t quite as severe as it might otherwise be to get ground cleared, as once there’s cereal straw to bale it becomes more urgent to get fields baled and bales removed as fast as possible to ensure customers can establish their next crop.
The various parts of the AgriBale team generally work as a single unit, and bales spend very little time in the field, which also ensures they pick up little extra moisture. The chasers follow up behind the balers as soon as they start work, and this means the business’ telehandlers are also kept on their toes forming stacks from the chaser loads as soon as they arrive at the stack site where they’re to be stored before later transportation to their final home. Out of harvest season, it’s loading lorries from these stacks that forms the main workload for the machines.
“We need handlers that can stack quickly and stack high, so the current models we run have a maximum lift height of 9.5m, enabling us to stack nine bales high where possible. Because we’re using chasers to clear the fields, it’s precision when stacking – and then unstacking again to load lorries – that’s most important to us, rather than work in the field. But it’s also important the machine is fuel-efficient between sites on the road, as we operate over quite a wide area.
“What especially appealed about the idea of trying a Loadall with the new DualTech VT transmission was the promise of something that would be more controllable when manoeuvring close to a stack, placing or removing bales from up at full height.
“We had the opportunity to have a DualTech Loadall for a few days on demonstration last year, and I was really pleased with the way it performed. One of the main benefits is that it’s possible to keep the machine still without using the footbrake, but still providing sufficient hydraulic power to quickly get the bale to full height.”
The demonstration resulted in an order being placed for a pair of Loadall 535-95 Agri Pro Loadall models, which joined the AgriBale fleet in time for harvest 2017. Since then, the two new handlers have each racked up a number of hours, says Doug Price, and to date the impression has been favourable.
“There are more long-term driver benefits to the transmission than perhaps we originally realised. When stacking and unstacking bales previously, our operators very quickly ended up with locked left-leg muscles during harvest. This comes from putting the throttle on with the right foot to extend the boom once at the stack, while at the same time holding the handler still by pressing hard on the brake with the left foot.
“With Flexi mode, the hydrostatic element of the transmission means that when you approach a stack with a bale, the machine can be brought to a standstill by removing your foot from the throttle and then using it for inching. You then don’t need to put plenty of throttle on to rapidly extend the boom sections as the engine speed has been already pre-set to the most efficient hydraulic performance.”
Among the other operating features of the Agri Pro models are a seat-mounted servo joystick with proportional roller switches for boom extend and retract, a transmission forward/reverse trigger switch on the joystick that complements the left-hand column-mounted power shuttle, and high-intensity LED lights claimed to provide 360° illumination. It’s these that Doug Price singles out for particular mention.
“They do an excellent job, and really turn night into day. We do end up stacking a lot of straw after dark, and decent lights really make a difference.
“The other upgrade we specified on these two new machines were bigger 500mm tyres, which we’ve found much better for traction and stability than the 435s fitted to our last machines.
But it’s the transmission that has made the most significant difference to his operation, he believes.
“Our operators work some very long hours from late spring through to late summer, and more than anything it has really improved their working conditions. That’s worth a lot.”
Farm facts
AgriBale, Elton, Peterborough, Cambs
- Partners: Doug Price, David Johnson, Corbetts (Malpas)
- Business: Buying straw in the swath for baling
- Services: Baling, chasing, selling straw and other crops for baling
- Primary markets: Power stations, livestock farms
- Tractors: 12x John Deere/JCB Fastrac/Valtra
- Balers: 12x Massey Ferguson/Hesston and New Holland big square models: 10x 120cm x 130cm machines and 2x 120cm x 90cm models
- Bale chasers: 6x Heath Superchasers
- Telehandlers: 2x JCB Loadall 535-95 Agri Pro DualTech VT plus another hired-in