The concept of small autonomous robots taking over from heavy costly machines has taken its first few steps into reality and its first foray into the field. CPM travels to Portsmouth to meet the Small Robots.
The agricultural industry is so entrenched in its practice it’s absolutely right for disruption.
By Tom Allen-Stevens
Here’s the story so far: Tom, Dick and Harry want to get into farming but do so in quite a different way. Tom scouts the fields, feeding information back to Wilma, who joins the team as the brains of the operation. She instructs Dick, who controls weeds and protects the crop, and Harry who plants the seed.
Then Rachael appears, kind of standing in for the role Tom was going to take, and the only one of the team that makes it onto a farm. Rachael steals the limelight, capturing national media attention and even attending a convention in China. Dick and Harry have yet to make an appearance, though, and there’s talk of morphing them into one.
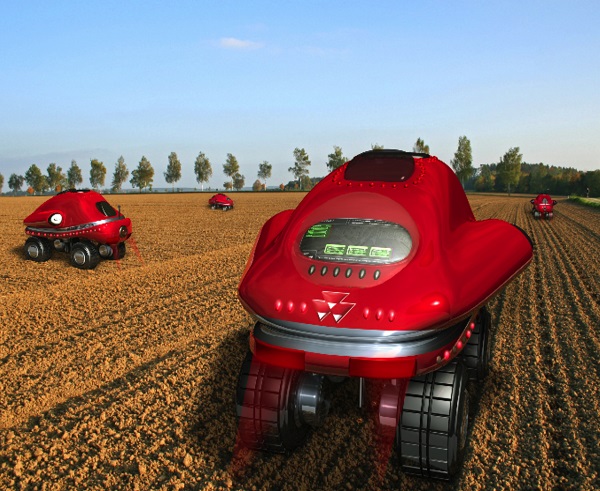
Simon Blackmore’s concept of unmanned ground vehicles, including this crop-scouting robot, was the original inspiration for the Small Robot Company.
It sounds like a bizarre plot line from The Archers, but these are in fact The Small Robots, and they could have a bigger influence on how farming operations are carried out than Harry Ferguson’s hydraulic three-point hitch or Jethro Tull’s seed drill.
The original concept comes from Professor Simon Blackmore of Harper Adams University. The current way crops are grown is flawed, he argues because:
- It is high cost
- Around 90% of the chemistry applied never reaches its target
- It has resulted in large machines that damage the soil.
Crops are routinely blanket sprayed, he points out, while often it’s just one drop of chemical on a target weed that’s needed. “Where inputs are targeted intelligently, you can easily save 99% of chemical applied. What’s more, if active ingredients are applied to only a small target area, there could be a raft of chemistry, currently not allowed, that could get approval for use.”
But it’s the move over the past 50-60 years towards ever-larger machines that’s the most damaging and needless, he says. “90% of energy used in farming operations goes into repairing damage caused by cultivations and trafficking that didn’t need to happen in the first place. The annual cost of compaction in England and Wales is estimated at £0.4 billion.
“It’s because every kilonewton of force needed to drag metal through the soil takes 2kN of downwards force to create the traction, and that’s killing the soil.”
Simon’s concept is one where small autonomous robots, rather than large manned machines, carry out the field operations to a point of precision that’s not just sub-field but specific to each crop plant. This simultaneously solves the labour-shortage problem, particularly for the horticulture sector.
Now a new UK start-up has taken the concept on. The Small Robot Company launched in Nov last year and has already gathered £1M worth of funding. This will help develop prototypes, the data management and artificial intelligence systems that will bring a new way of farming into the field, with a projected launch date for a commercial service of autumn 2021.
“What appealed to me about the concept is that it’s a very disruptive innovation, using the technology in a way I’d never considered before,” says co-founder Ben Scott-Robinson.
Ben’s background is that he’s worked on the digital transformation of the Ordnance Survey maps, and has been involved in shaping the technology behind the autonomous vehicles soon to become commonplace on roads. “I heard Simon first on Farming Today and was inspired by the talk he gave at the Oxford Farming Conference. The attraction here is that the agricultural industry is so entrenched in its practice it’s absolutely right for disruption.”
But he was keen to develop Simon’s initial concept. “It revolves around robots doing a specific task, controlled by a farmer. I couldn’t see why you shouldn’t develop a system with more autonomy where increasingly the robots would learn to make their own decisions. Also, I didn’t want to take field robots simply in a direction where you’re automating an existing task, such as picking strawberries – all you’re doing is automating the process, but everything else stays the same, which means you’re limiting the opportunity.”
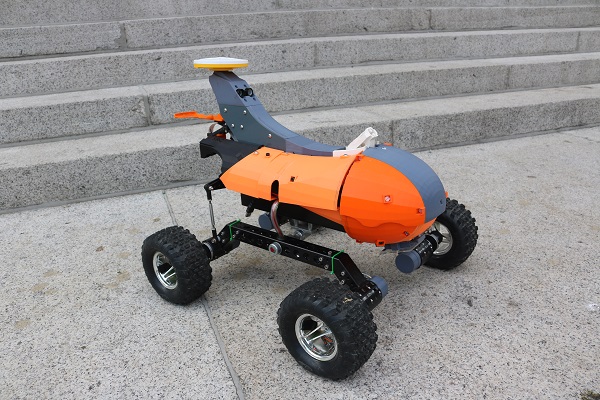
Rachael is the first prototype of Tom, the crop-scouting robot.
Ben met Sam Watson-Jones, a fourth-generation farmer who had recently taken over the reins on the family’s arable and beef business in Shrops. “On our farm, gross revenues generated from each ha of cereal production are the same as they were 25 years ago, but the costs incurred to generate those revenues have gone up significantly,” he points out.
“When you discuss this with someone who works in a different industry and knows nothing about the finances of farming, they almost fall off their chairs. But as farmers we just accept that we are operating a business model which is fundamentally broken.”
Aghast at the precarious state of farming, Sam felt as strongly as Ben that things had to change. Another step they agreed on was to focus on wheat, partly because it’s the crop Sam is most familiar with, but it also has most potential for scalability and there’s a greater commercial imperative, explains Ben.
“Virtually all robotic systems currently in development are working in glasshouses, polytunnels or field vegetable crops. Wheat is the most widely grown crop, however, and once we’ve introduced the system, it’s easily transferable into other combinable crops, including corn, soya and rice.”
The first step was to discuss their initial ideas with farmers, and they set about conducting around 70 interviews – so-called “Aga sessions” – to draw out how it should develop. “What became clear is that farmers are equally keen for the way in which they grow crops to progress, and they want to be involved in taking things forward, in shaping and evolving new solutions,” continues Ben.
“But they’re not keen in making large capital investments in a new and unproven technology. Upskilling of farm staff to manage maintenance and technical hitches, and the potential for downtime would be huge barriers to uptake. And that’s when we came up with the idea of Farming as a Service (FaaS).” (see below).
Although it sounds like a neat system, it’s still just a concept – not only is the technology nowhere near ready for commercial roll-out, most of it doesn’t exist. Turning it into reality will take investment. “Our initial start-up funding has been used to develop a prototype Tom robot and bring a team together,” says Ben. With eight in the team to date, it’s been awarded a sizeable sum from Innovate UK to develop Wilma and the artificial intelligence (AI) and data management structure that will form the foundation of this new way of farming.
And this is where Joe Allnutt comes in, with the enviable title head of robot “awesomeness” at Small Robot. Joe worked with Ben on digitising OS, running the tech labs to develop hardware as well as AI systems to manage the data. They have also partnered with Cosmonio, a UK-based start-up that specialises in developing AI systems that automate the process of extracting visual information from images using self-learning algorithms.
Before data can be processed and machines can begin to learn, there are some fundamental aspects to address, however, explains Joe. “With any autonomous system that relies on geopositioning, you need to know not only precisely where your vehicle is in terms of longitude and latitude, but what direction it’s facing. That means you need to equip your robot with a whole host of monitoring devices, and there’s also a staggering amount of data that must be managed.”
The first prototype Tom is curiously named Rachael (see below). “We’re taking all the names of prototypes from the classic sci-fi thriller Blade Runner,” explains Ben. It’s taken over a year to build and bring her into operation, but she’s already taken her first exploratory journeys through wheat crops. Night or day, whatever the weather or field conditions, she can scout the crop, travelling around 0.5m/s (1.8km/h), and can cover 10ha/day, he claims.
A key issue to overcome is the machine learning itself, which is where the public funding is being directed. The concept being developed here is that the system teaches itself as it develops. It starts by distinguishing a crop from a weed, then gets better at identifying different plants at different growth stages – the more images it sees, the better it becomes.
“You have to accept that a robot sees things differently from a human,” notes Joe. “The experience of other AI pioneers is that you can train the system to perfection to recognise a particular crop – even better and quicker than a human. Then you move it to the same crop in the next-door field and the robot is completely lost, simply because the soil type is slightly different, and it throws the algorithms completely.
“But then that’s also a positive – AI will define ways to identify diseases, and even crop stress in different ways to a human brain, that could offer us greater insight into plant physiology.”
So what’s the biggest challenge? “There are multiple challenges, and it’s the breadth of the task we face that concerns me most,” says Ben. “But there have been two Eureka moments in this project so far – the first was when we spoke to farmers and from this came the FaaS idea.
“The second was when we planned the roadmap for the project, and broke down every single component into its individual challenges. There may be many problems, but they’re all solvable – the technology and the knowledge exist, and the drive is there to do it. The challenge for us is applying that thinking to farming and taking farmers along with us.”
As far as the technology itself is concerned, what’s surprised him is the level of work that’s already taking place in this space. “We’ve been contacting PhD students who we know are working in robotics, for example, to ask if they’d like to help. They go to check with their course tutor, and the next thing we know, the head of department at that university is keen to join us, offering the full resources of its robotics facilities. There’s currently very little commercial application of the technology here in the UK, especially in agriculture, but plenty of research.”
Work is now underway to develop Harry, spurred on by a £50,000 Horizontal Innovation award from the Institution of Engineering and Technology (IET) and the High Value Manufacturing Catapult (HVMC), sponsored by Innovate UK. This will look to develop the company’s precision drilling and planting robot, from concept through to in-field prototype, and in particular his “punch-planting mechanism”.
“It’ll be a completely different way to plant a crop, and we’re working with the Manufacturing Technology Centre,” says Ben. This is one of seven centres that make up the HVMC. He reveals there are plans to possibly combine Dick and Harry into one multipurpose bot that will have a maximum 1t payload. But as for the planting mechanism itself, he’s keeping tight-lipped on detail.
This is one area where there could be problems, he notes. “We have been working with intellectual property lawyers. We also recognise we’re not the only ones working in robotics and AI, and there are a lot of big players in the industry, who are looking at this area with interest. But for the most part, industry is hanging on to its big machines and going smart, with very little innovation going small and smart, as we are – it’s very difficult to innovate at pace in a big company.”
Experience in other industries has shown that interconnected systems of many small interventions together can have a massive impact, according to Kevin Burrowes, head of clients and markets at PwC. “Small companies are often the ones that change industries. Disruption is driven by agility and an alternative outlook – it’s not about avoiding the downside, but mapping the opportunity.”
He reckons Small Robots has a significantly different approach to larger, established players which automate or extend existing systems. “Digitisation, enabled by robotics, unlocks the potential for exponential improvements in the farmer’s ability to collect, process and act on data. Every industry is subject to disruption and digital transformation and agriculture is no exception.”
It’s why Small Robots is going direct to farmers to develop the system and is looking to be as inclusive as possible. “Success for us will be to have a system that’s working 5% of the UK wheat production by 2025. That’ll only come through working with farmers to develop the system and the concept,” says Ben.
“We’re looking to start with a core group of 20 farmers, but keen for anyone who’s interested to get in touch – whether you want to invest or just interested to see how it works. We’ve a long way to go and there’ll be many conversations along the way that’ll help us get there.”
Farming as a service (FaaS) – a new way to grow crops
The idea of FaaS is that you don’t actually buy a robot, but contract in the service, paying a rate per ha. The Small Robot Company owns and administers a nationwide fleet of robots, ensuring they’re all running effectively and carrying out any maintenance, upgrades or replacements required. It revolves around three basic units:
- Tom, the scouting robot – “chatty and curious”. He lives in a ‘kennel’ on your farm, where he charges, uploads and downloads data, and is probably the only resident robot. His task is to constantly monitor crops and fields on a plant-by-plant basis, covering fields at least once every two weeks. He knows exactly where every plant is and its growth stage so can identify weeds and monitors for stress, disease, pests, etc. He works autonomously, although he can be directed if required. It’s information from Tom that determines exactly what Dick and Harry do.
- Dick, the feeding and weeding robot – “ruthless and efficient”. He micro-sprays each plant with fertilisers or chemicals, delivering just the right product and amount to ensure it thrives. He has three ways to deal with weeds –micro-spray a tiny amount of chemical on the weed, burn it with lasers, or crush it as it comes out of the ground. He’s delivered to the farm periodically to carry out the work.
- Harry, the drilling and planting robot – “measured and precise”. He places individual seeds in the ground and accurately records exactly where he’s put them. He’s designed to cause minimum disturbance and compaction and bring the edges and corners of your fields back into full production. Like Dick, he’s delivered to the farm when needed. Any seeds or field areas where germination fails are not a problem – he’ll simply pop out and precisely replant the seed.
The key to FaaS is the artificial intelligence that drives it, and that’s down to Wilma – “smart and incisive”. Wilma isn’t a physical robot as such, nor does she reside in any one computer. She’s a data storage and management system that sits in the ‘cloud’ – a collective structure of networked computers and devices driven by data. She draws all the information from Tom, combines it with weather data, crop and field history, plugs into pathogen-monitoring services, and the like, and delivers direction to Dick and Harry.
The bits that make up a bot
Although Rachael may look like a radio-controlled buggy, every component has been developed from scratch, or adapted from a parallel technology. She was born in Southampton in the Makers Space – basically a big garage for start-ups developing similar prototypes – and shared her space with Alan the Dalek.
“She has a titanium substructure, on four independent wheels but this articulates fully, so she can navigate all kinds of terrain – she could even climb steps,” explains Joe.
The motors that drive the wheels have been specially sourced. “They need to be relatively slow but high torque compared with most roving robots. Each one has encoders to tell us precisely what the wheels are doing – part of the positioning information comes from monitoring wheel movement.” The wheels don’t actually steer, but she slews, like a tank.
The battery pack lasts for around two hours. “Battery technology is something that’s developing constantly but we’re currently using a lithium-ion polymer pack that gives good power, although you have to be careful how it’s treated. One aspect we need to address is how it will autonomously change batteries. Likewise, once we come to develop Dick and Harry, we must address how we replenish the seed and fertiliser, etc, they’re applying.”
The GPS antenna sits proud towards Rachael’s rear and delivers accuracy to within 2cm, but there’s also a compass and accelerometer that deliver precise positioning and direction. “These are very sensitive instruments so we have to keep them away from metalwork, and especially the wheel motors, due to interference,” explains Joe.
Rachael has just two cameras, currently – one that faces down and one forward. Hi-resolution imagery in a full spectrum is what defines her primary role in terms of the data she gathers, but Joe’s cautious about loading her with too many cameras. “You can mount as many cameras as you like, but you’re limited by how much data you can physically transfer – we need to refine exactly which sort of imagery gives us the best information about the crop and the field. We’re also working on a camera that will give a view from higher up.”
One component that’s taken a leap forward recently is LIDAR. “This is what tells Rachael what’s in her vicinity and is essential for autonomous navigation and object avoidance. The technology’s developing fast and you can now get a 360° camera that gives you a 3-D point cloud. A crowd-funded unit has just come onto the market costing £250 with the same capability as one that previously cost £10,000.”
The orange outer body that houses all the components was made on a 3-D printer. Take off this housing and underneath lies the electronic gadgetry that does the basic processing and local data storage. “Her brain is a Raspberry Pi 3 model B, running Ubuntu,” explains Joe. “It’s remarkably capable but costs just £30. There’s another microprocessor that counts the clicks of the wheels to help with positioning.”
So is he worried that Rachael will be stolen if she’s running unsupervised in open arable fields? “Firstly, we’ll know precisely where she is and what she sees – if she’s approached, she can cry for help. But what is there to steal? Her value is the data she generates, which is part of the cloud-based system, and in the wizardry under the hood. If you break her down into components, you’d probably have something worth little more than £100 to potential thieves. I’d be more worried that a curious deer might tip her over,” says Joe.
Become part of the robot revolution
The Small Robot Company is actively looking for farmers to get involved with the project. “We need funding to develop the system, but we also need fields in which to test it, and input from farmers is crucial,” notes Ben.
There are a number of ways to get involved:
- Crowd-funding. There’s currently a bid to raise £50,000 on crowd-funding platform lndiegogo, with almost half of this target raised to date, which will go mainly towards developing the prototype Harry. You can pay anything from £5, simply to join the small robot community, up to £5000, which would be an investment in your first tranche of FaaS, once this is rolled out as a commercial service.
- Become a test site. Rachel needs as much practice in as many situations as possible to develop and refine the AI and machine-learning algorithms, as well as test the hardware itself. Once prototype Harry and Dick have been built, these will also need test sites.
- Become an equity investor. The Small Robots has a current estimated value of around £4-5M, and Ben and Sam are keen for farmers, more than anyone, to invest and share in the success of the project going forward.
- Join the project steering group. There’s already a consultant agronomist on the team, but Small Robots aims to set up a core group of around 20 committed farmers who’ll help develop the system and steer the project as it progresses towards commercialisation.